- 9-14 Min Read
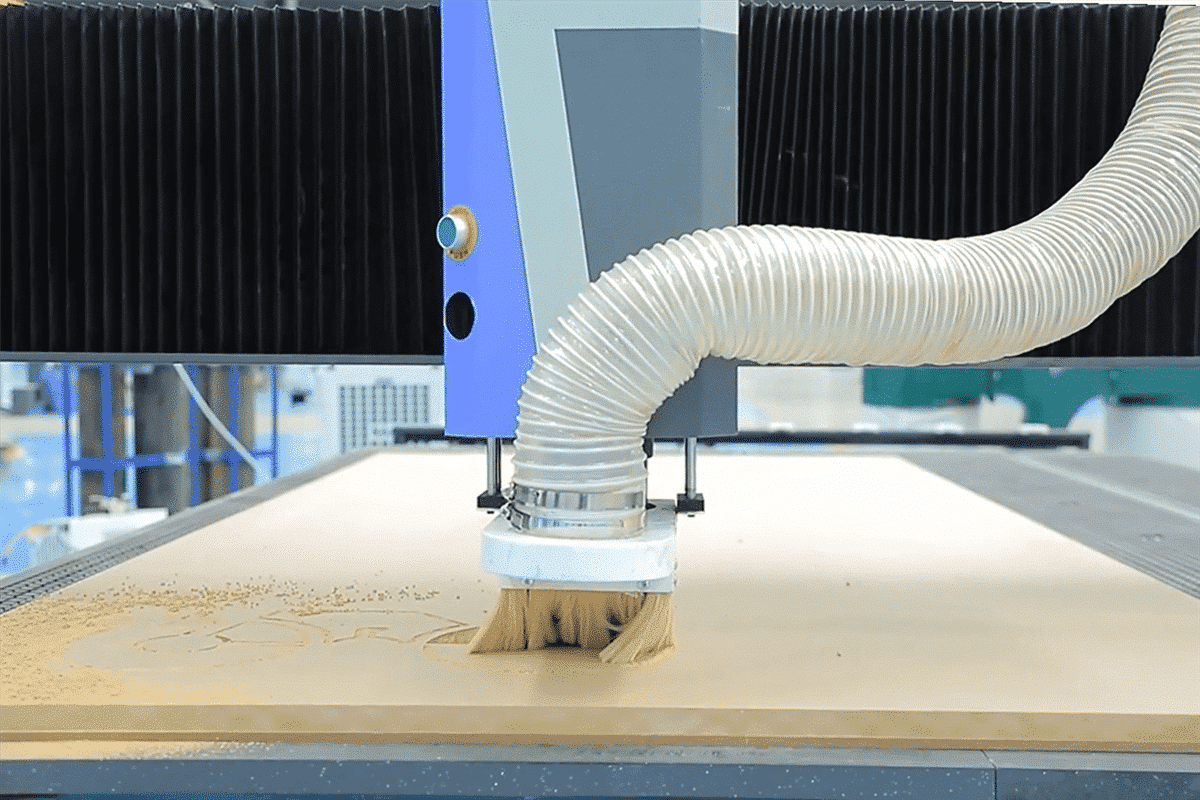
Cutting Medium Density Fiberboard (MDF) on a CNC router has become a staple process for professionals and hobbyists in woodworking, cabinetry, and custom fabrication. MDF’s consistent composition and smooth surface make it ideal for intricate designs, decorative panels, furniture, and more. However, its dense fiber structure, combined with resin binders, poses challenges, such as excessive dust production, rapid tool wear, and the risk of edge chipping. To achieve precise cuts and preserve the life of your tools, you should understand the best techniques for working with MDF and the correct procedures for machine operation.
This article delves into the key considerations for successfully cutting MDF on a CNC router, including choosing the right bits, optimizing feed and speed settings, and managing dust effectively. By mastering these aspects, you can enhance the quality of your projects, reduce downtime, and maximize the performance of your CNC router. Whether you’re a seasoned professional or a beginner, the strategies outlined here will help you achieve cleaner cuts, prolong tool life, and unlock the full potential of MDF in your projects.
Understanding MDF
Medium Density Fiberboard (MDF) is an engineered wood product created by breaking down wood fibers from hardwood or softwood and combining them with wax and resin binders. These components are compressed under high pressure and heat to form dense, uniform panels with a smooth surface. MDF is prized for its consistent texture and lack of natural defects such as knots or grain irregularities, making it a popular choice in the woodworking industry.
Advantages and Disadvantages of MDF
Advantages
- Uniformity and Consistency: Unlike natural wood, MDF does not have grain patterns, knots, or other imperfections, making it easy to work with and allowing for precise cuts and smooth finishes.
- Easy Machinability: MDF is highly versatile and can be easily cut, shaped, and routed without splitting, making it ideal for intricate designs and detailed machining on CNC routers.
- Smooth Surface: The smooth and even surface of MDF takes paint, veneers, and laminates exceptionally well, providing a high-quality, professional finish.
- Cost-Effective: MDF is generally more affordable than solid wood or plywood, making it a cost-effective solution for large-scale projects such as cabinetry, furniture, and interior trim.
- Wide Availability: MDF is widely available and comes in various sizes and thicknesses, offering flexibility for different project needs.
Disadvantages
- Moisture Sensitivity: MDF is prone to absorbing moisture, which can cause swelling, warping, or deterioration if not properly sealed or protected, making it unsuitable for outdoor use or high-humidity areas.
- Tool Wear: The density and resin content of MDF can be abrasive on cutting tools, leading to faster wear and requiring frequent tool maintenance or replacement.
- Dust Production: Cutting and sanding MDF generates a significant amount of fine dust that can pose respiratory health risks. Effective dust extraction and proper safety equipment are necessary when working with MDF.
The Importance of Cutting MDF Correctly
Cutting MDF correctly is beneficial for achieving precise, high-quality results while minimizing potential issues. MDF’s unique composition, which combines wood fibers and resin, allows for precise machining and smooth finishes, but it also presents challenges if not handled properly. Accurate cutting techniques prevent common issues such as edge chipping, rough surfaces, and splintering. Proper cutting ensures smooth edges and surfaces, reducing the need for excessive sanding or rework, which ultimately saves time and labor.
Additionally, cutting MDF correctly helps prolong the lifespan of cutting tools and equipment. The dense fibers and resin content can be abrasive, leading to faster tool wear if incorrect speeds, feeds, or blades are used. By optimizing the cutting parameters, you can minimize tool wear, reduce downtime for maintenance, and improve overall production efficiency. Effective dust management during the cutting process maintains a clean and safe working environment. Therefore, correct cutting practices not only ensure superior project outcomes but also contribute to tool longevity, worker safety, and operational efficiency.
Choosing the Right CNC Router Bits for MDF
Selecting the appropriate CNC router bits for cutting MDF is beneficial to achieving clean, precise cuts while minimizing tool wear and common issues like chipping and rough edges. Here are key considerations for choosing the best bits for MDF:
Types of Bits
- Up-Cut Bits: These bits are designed to pull chips upward, which helps clear debris quickly but may cause edge chipping on the top surface of the MDF.
- Down-Cut Bits: These bits push chips downward, resulting in a cleaner top edge and reduced chipping, but may lead to material buildup underneath.
- Compression Bits: Ideal for MDF, compression bits combine the benefits of both up-cut and down-cut bits by pulling fibers inward toward the center. This provides clean cuts on both the top and bottom surfaces, making them particularly useful for through-cuts.
Bit Materials and Coatings
- Carbide-Tipped or Solid Carbide Bits: Carbide is highly recommended for cutting MDF due to its durability and heat resistance, which helps withstand the abrasive nature of MDF’s resin and fibers.
- Coated Bits: Consider bits with specialized coatings, such as titanium or diamond-like carbon (DLC), to reduce friction, heat buildup, and extend tool life.
Bit Size and Flute Count
- Diameter: Larger diameter bits can provide smoother cuts and faster material removal but may require more powerful CNC routers. Smaller bits are suitable for fine details and tighter radii.
- Flute Count: Two-flute bits strike a balance between chip clearance and cutting surface quality, making them popular for MDF. Higher flute counts can produce finer finishes but may clog faster.
By choosing the right CNC router bits tailored to MDF’s characteristics, you can achieve precise cuts, prolong tool life, and reduce rework or surface defects, ensuring high-quality results for your projects.
Optimal CNC Router Settings for Cutting MDF
Achieving high-quality cuts on MDF with a CNC router requires careful adjustment of key machine settings. These settings impact the precision, cleanliness, and overall success of the cutting process, while also helping to reduce tool wear and minimize dust. Here are the optimal settings and considerations for cutting MDF on a CNC router:
Feed Rate Considerations
The feed rate, or the speed at which the cutting tool moves through the material. For MDF, typical feed rates range from 60 to 120 inches per minute (IPM), depending on the bit size, depth of cut, and spindle speed. Experimenting with feed rates and adjusting according to tool performance and cut quality is key.
Spindle Speed Recommendations
- High RPM Values: MDF is best cut using relatively high spindle speeds, usually in the range of 15,000 to 18,000 revolutions per minute (RPM). This helps achieve smooth and precise edges while reducing chipping.
- Matching with Feed Rate: Proper coordination of spindle speed and feed rate ensures that the bit cuts efficiently without overheating or causing burn marks.
Depth of Cut and Pass Strategies
- Shallow Depth Passes: To prevent overloading the bit and to achieve cleaner edges, it is advisable to use multiple shallow passes rather than attempting a single deep cut. A common practice is to cut at a depth that is approximately 1/3 to 1/2 the diameter of the bit per pass.
- Step-Down Strategy: Gradually reducing the cutting depth for each pass ensures greater control, minimizes tool wear, and produces more accurate results.
Cooling and Dust Extraction
- Cooling: Since MDF can produce heat quickly during cutting, ensure proper cooling of the bit to prevent premature wear and scorching.
- Dust Management: MDF generates a lot of fine dust. Utilize an effective dust extraction system and ensure proper ventilation in the workspace to maintain a clean and safe environment.
By fine-tuning these CNC router settings, you can maximize cutting precision, reduce tool wear, and produce clean, consistent results when working with MDF. Adjustments may vary depending on the specifics of your project, bit type, and CNC router capabilities, so monitoring and tweaking settings during initial cuts is recommended for optimal performance.
Toolpath Strategies for MDF Cutting
Proper toolpaths when cutting MDF ensure smooth cuts, reduce edge chipping, and improve efficiency. Here are some key toolpath strategies to consider:
Choosing the Right Toolpath Type
- Profile Cuts: Used for cutting along the perimeter or outer edge of a shape. When creating profile cuts, consider using a conventional (clockwise) or climb (counterclockwise) milling approach, depending on the desired edge quality. Climb milling often produces cleaner edges for MDF.
- Pocketing: For creating recesses or cutouts within the material, pocketing paths are effective. Use spiral or ramped entries into the material to reduce stress on the bit and minimize chipping.
- Contour and Slotting Paths: Contour paths are great for intricate designs, while slotting paths are used for creating narrow channels. For slots, multiple passes with incremental depths help prevent heat buildup and excessive tool wear.
Direction of Cut
- Climb Milling: This approach moves the cutter in the same direction as the tool’s rotation, resulting in smoother cuts and reduced chipping along MDF edges. It also minimizes dust being thrown onto the work surface.
- Conventional Milling: In this approach, the cutter moves against the direction of its rotation, creating a rougher cut surface. It may be useful in certain situations but typically leads to increased edge chipping when used with MDF.
Reducing Edge Chipping and Tear-Out
- Compression Bits: When cutting through the entire thickness of MDF, using compression bits helps reduce chipping by pulling the material fibers inward at the top and bottom edges simultaneously.
- Pre-Cutting Techniques: Consider performing a light scoring pass before the full-depth cut. This helps ensure a clean edge and reduces the risk of tearing during the main cut.
Toolpath Optimization for Speed and Quality
- Minimizing Toolpath Length: Optimize the toolpath to reduce unnecessary travel, which can save time and minimize tool wear.
- Lead-In and Lead-Out Paths: Use lead-in and lead-out paths to ensure smooth entry and exit of the cutting tool, reducing stress on the material at these critical points.
By carefully planning and implementing these toolpath strategies, you can achieve high-quality cuts, extend tool life, and ensure a smooth, efficient cutting process for MDF on a CNC router. Properly managed toolpaths reduce chipping, improve edge quality, and optimize your overall machining workflow.
Common Troubleshooting for Cutting MDF
Cutting MDF on a CNC router can present a range of challenges. Understanding how to troubleshoot these issues is beneficial for maintaining high-quality results and prolonging tool and machine life. Here are common problems that arise when cutting MDF and how to address them effectively:
Rough Edges or Chipping
The cut edges of MDF appear rough, frayed, or chipped. Here is the solution:
- Use a compression bit designed specifically to minimize chipping on the top and bottom surfaces of MDF.
- Adjust the feed rate and spindle speed to achieve a smoother cut.
- Try a climb milling approach to reduce splintering, especially when cutting intricate shapes.
- Consider using a light scoring pass along the intended cut path before making a full-depth cut.
Burn Marks on MDF
The edges or surfaces of the cut MDF show burn marks. Here is the solution:
- Reduce spindle speed or increase the feed rate to prevent the tool from lingering in one spot and generating heat.
- Ensure the cutting tool is sharp; dull bits create more friction and heat.
- Consider using a misting or air-cooling system to cool the bit and reduce heat buildup during cutting.
MDF Splitting or Cracking
The MDF splits or cracks during cutting. Here is the solution:
- Ensure that the MDF sheet is well-supported and secured to the worktable to minimize movement or vibrations.
- Use gradual depth passes rather than a single, deep cut to reduce stress on the material.
- Verify that the toolpath does not exert excessive lateral force on the MDF.
Inconsistent Cut Depths
The depth of cut varies across the material, leading to inconsistent results. Here is the solution:
- Check that the CNC router bed is level and properly calibrated.
- Ensure the MDF sheet is flat and securely clamped to prevent lifting during cutting.
- Inspect the CNC router spindle and tool holder for any play or looseness.
Poor Finish on Cut Surfaces
The cut surface appears rough or uneven. Here is the solution:
- Use higher flute-count bits for a smoother finish, but be mindful of potential dust clogging.
- Reduce feed rates slightly to allow for a more precise cut.
- Consider performing light sanding or using finishing tools after the cut for a refined surface.
By understanding the cause of these common issues and making the necessary adjustments, you can improve the performance and cutting quality of your CNC router when working with MDF. Regular maintenance of the CNC router and using the right tools for the job are key factors in achieving consistent results.
Finishing and Post-Processing After CNC Routing MDF
Once MDF has been cut using a CNC router, proper finishing and post-processing are necessary to enhance the appearance, durability, and usability of the final product. Post-processing steps ensure smoother surfaces, sealed edges, and a ready-to-use component that meets project requirements. Here’s how to effectively finish and process MDF after CNC routing:
Sanding the Edges and Surfaces
- Smooth Rough Edges: CNC routingcan leave sharp or rough edges on MDF. Start by sanding the cut edges with medium-grit sandpaper (e.g., 120-150 grit) and progress to finer grits (e.g., 220 grit) for a smooth finish.
- Surface Sanding: Lightly sand the flat surfaces to remove any tool marks, ensuring a uniform finish that is ready for painting or further treatment. Use an orbital sander for even coverage and to minimize swirl marks.
Sealing the Edges
- Importance of Sealing: MDF edges are highly absorbent and can swell or deteriorate when exposed to moisture. Sealing these edges is beneficial for preventing moisture absorption and creating a smooth, paintable surface.
- Edge Sealer Options: Apply a suitable edge sealer, such as water-based or oil-based sealants, wood fillers, PVA glue, or specialized MDF primers. Sand the edges again after the sealer dries for a smoother finish.
Painting or Laminating
- Painting: MDF can be painted using water-based latex paint, oil-based enamel, or spray paint. Apply multiple thin coats rather than one thick coat to avoid sagging or dripping. Sand lightly between coats for a smoother finish.
- Laminating: For a more durable and decorative finish, consider laminating MDF with wood veneers, melamine sheets, or plastic laminates. Ensure the MDF surface is clean and smooth for a strong adhesive bond.
Applying Protective Coatings
- Top Coats: For added protection and durability, especially for furniture or high-use items, apply a clear topcoat, such as polyurethane, lacquer, or varnish, over the painted surface. This helps resist scratches, moisture, and wear.
- Waxing: An alternative protective finish is applying furniture wax for a satin sheen and a smoother touch.
By carefully following these finishing and post-processing steps, you can achieve a high-quality, professional-looking MDF product that is both aesthetically appealing and durable for its intended use. Proper sealing, priming, and protective coatings are beneficial to extending the lifespan and maintaining the appearance of MDF components.
Summarize
Cutting MDF on a CNC router can be a rewarding process, yielding high-quality results for a wide range of woodworking and fabrication projects. By carefully selecting the right tools, optimizing your CNC router settings, and implementing effective cutting strategies, you can achieve precise cuts, minimize common issues, and prolong the life of your equipment. With the right approach, you can unlock the full potential of MDF, creating everything from intricate designs to robust furniture pieces. Continue reading the “CNC Router Safety Operation Guide” and you will get comprehensive guidance on the correct operation of the machine.
If you’re looking for high-quality CNC routers to optimize your MDF cutting projects, AccTek CNC is a trusted manufacturer that offers a range of reliable solutions. By choosing the AccTek CNC router, you can be confident that you’re investing in a product that will elevate your capabilities, maximize productivity, and deliver consistent results across a wide variety of applications. Whether you’re creating intricate designs or handling large-scale projects, AccTek CNC provides the perfect combination of quality, versatility, and performance to meet your needs.
Medium Density Fiberboard (MDF) is an engineered wood product created by breaking down wood fibers from hardwood or softwood and combining them with wax and resin binders. These components are compressed under high pressure and heat to form dense, uniform panels with a smooth surface. MDF is prized for its consistent texture and lack of natural defects such as knots or grain irregularities, making it a popular choice in the woodworking industry.