- 10-15 Min Read
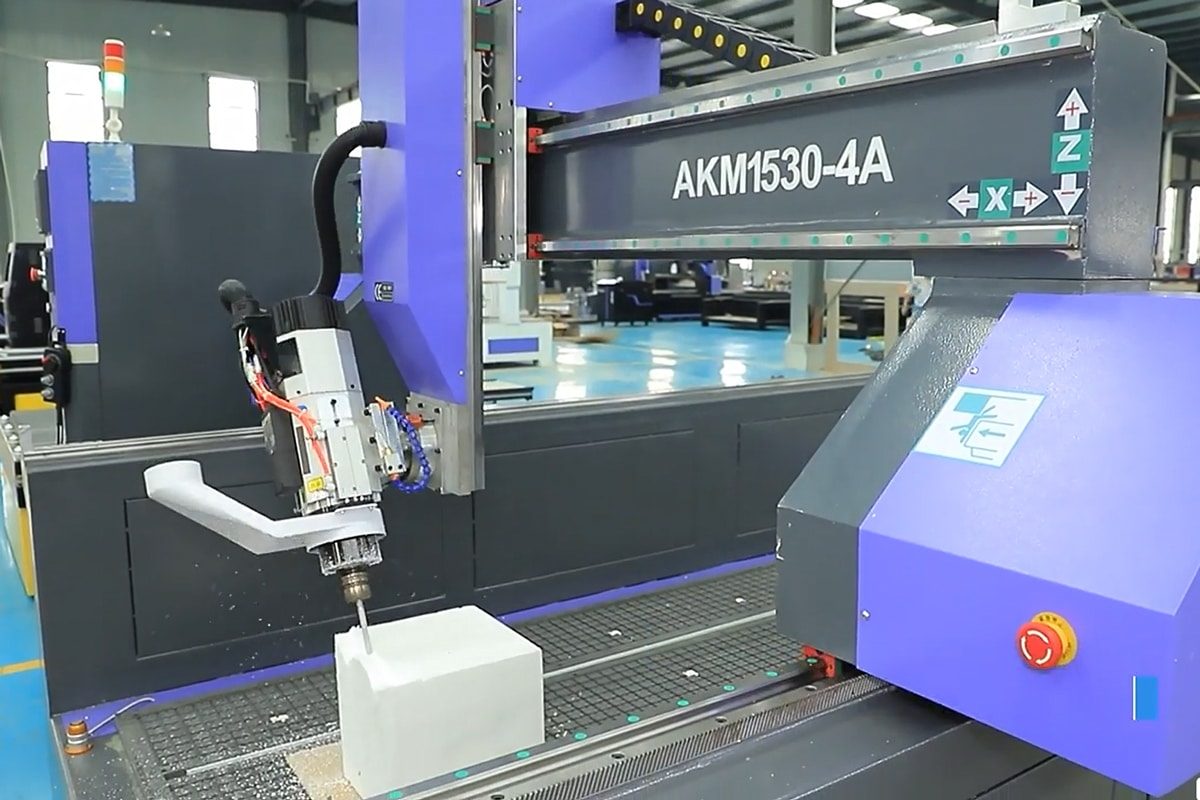
Foam is a versatile material whose lightweight nature, ease of shaping, and shock-absorbing properties make it ideal for a variety of applications. While CNC routers are commonly associated with wood, metal, and plastic cutting, they are also well-suited for foam processing when equipped with the right tools and settings. However, due to its soft and compressible nature, foam requires specific techniques, tools, and settings to ensure clean and accurate cuts without fraying or tearing.
In this guide, we will walk you through everything you need to know about cutting foam with a CNC router. From understanding different types of foam and selecting the right router bits to optimizing machine settings and overcoming common challenges, this comprehensive guide will help you achieve professional results. Whether you are a beginner or an experienced CNC user, mastering these techniques will enhance the quality and efficiency of your foam-cutting projects.
Understanding Foam as a Material
Foam is available in various densities, compositions, and structures, making it suitable for applications such as packaging, signage, modeling, and insulation. Different types of foam behave differently when cut, requiring specific router bits, feed rates, and cutting strategies to prevent tearing, fraying, or excessive compression. Therefore, choosing the correct foam type can ensure clean, precise results when CNC cutting.
Types of Foam Suitable for CNC Routing
- Expanded Polystyrene (EPS): A lightweight and cost-effective foam commonly used for insulation, packaging, and prototyping. It is easy to cut but can be prone to chipping and melting if not processed correctly.
- Extruded Polystyrene (XPS): A denser version of EPS that offers better structural integrity and smoother cuts. It is commonly used in architectural modeling and signage.
- Polyurethane Foam: Available in rigid and flexible forms, this foam is often used for upholstery, insulation, and mold-making. Flexible polyurethane foam requires careful cutting to avoid deformation.
- Polyethylene Foam: A durable and impact-resistant foam commonly used for protective packaging and case inserts. It is denser than EPS and requires sharp, well-suited bits for clean cuts.
- EVA Foam: A flexible and rubber-like foam used in padding, and sporting goods. It cuts well with CNC routers but may require specialized tools such as drag knives for intricate designs.
Properties That Affect CNC Cutting
- Density and Rigidity: Higher-density foams provide better edge definition and reduced tearing, but they may require stronger cutting forces.
- Thickness: Thicker foams may need multiple passes or specific cutting techniques to avoid excessive material compression.
- Compressibility and Flexibility: Softer foams tend to deform under pressure, requiring careful securing methods to maintain cutting accuracy.
- Heat Sensitivity: Some foams, like polystyrene, can melt if the cutting speed and spindle RPM are too high, leading to poor cut quality.
When setting up a CNC router for foam cutting, users need to be aware of these factors first. By selecting the right type of foam and adjusting machine parameters accordingly, you can achieve high-quality results while minimizing waste and production errors.
Choosing the Right CNC Router for Foam Cutting
While most CNC routers can cut foam, certain features and specifications enhance the cutting process, especially when working with different foam densities and thicknesses. The right machine should offer adequate cutting area, power, and compatibility with suitable cutting tools to ensure optimal performance.
Key CNC Router Specifications for Foam Cutting
- Spindle Power and Speed: Foam is a soft material, so high spindle power is not required. However, a CNC router with adjustable spindle speeds (typically between 10,000-24,000 RPM) is beneficial for fine-tuning cutting performance.
- Cutting Bed Size: The size of the cutting bed determines the maximum foam sheet dimensions that can be processed. For larger foam projects, such as insulation panels or signage, a large-format CNC router is preferable.
- Z-Axis Clearance: Since foam blocks and sheets can vary in thickness, a CNC router with an adjustable or deep Z-axis ensures greater flexibility for cutting thicker materials.
- Vacuum Table vs. Clamps: Foam is lightweight and can shift during cutting. A vacuum table is an effective way to hold it securely, preventing movement and ensuring consistent cuts. Alternatively, clamps or adhesive tapes can be used for smaller foam pieces.
- Dust Collection System: Foam cutting can produce fine particles and debris, which may accumulate on the cutting surface or affect machine components. A dust extraction system helps maintain a clean workspace and improves cut quality.
CNC Routers Types for Foam Cutting
- 3-Axis CNC Router: This is the most common and widely used type for foam cutting. It moves along three linear axes: X (left to right), Y (front to back), and Z (up and down). This type of CNC router is ideal for cutting 2D and simple 3D shapes such as foam sheets, packaging inserts, signage, and basic contouring. The 3-axis CNC router has the advantages of simple operation, cost-effectiveness, and being widely available.
- 4-Axis CNC Router: It adds an extra rotational axis (typically an A-axis), allowing the cutting tool to tilt and approach the workpiece from different angles. This provides greater flexibility when shaping foam, especially for projects requiring contouring, edge smoothing, and sculpting. The 4-axis CNC router is more efficient at cutting rounded and beveled edges, reducing the manual repositioning of foam blocks.
- 5-Axis CNC Router: It provides the highest level of precision and flexibility, moving in five directions (X, Y, Z, and two additional rotational axes). This allows the cutting tool to access the workpiece from multiple angles without repositioning. It is particularly beneficial for complex foam sculptures, intricate molds, and large 3D models in industries like film, aerospace, and automotive prototyping. The 5-axis CNC router is capable of producing highly detailed 3D foam parts, eliminating the need for manual repositioning and improving accuracy.
- Rotary Axis CNC Router: It includes a rotating fourth axis (A-axis) that allows cylindrical foam materials to be cut with precision. This type of CNC router reduces material waste by rotating the workpiece continuously and is used for creating foam columns, cylindrical sculptures, decorative elements, and pipe insulation.
Choosing the right CNC router depends on your specific project requirements, including material size, precision needs, and production volume. Investing in a machine with adjustable settings, proper holding mechanisms, and dust management ensures smooth, efficient foam cutting with minimal waste.
Tool Considerations for Foam Cutting
Foam has unique properties, such as being soft, flexible, and compressible, which require specialized tools to prevent tearing, fraying, or excessive heat buildup. The following considerations will help in choosing the most suitable tools for foam cutting.
Types of CNC Router Bits for Foam Cutting
Using the right router bit ensures smoother cuts, reduced material compression, and longer tool life. Below are the most commonly used bits for foam cutting:
- Single-Flute and O-Flute Router Bits: The O-flute design helps evacuate chips efficiently, preventing melting and excessive friction. Best suited for soft foam materials like expanded polystyrene (EPS) and polyethylene foam.
- Up-Cut and Down-Cut Spiral Bits: Up-cut bits pull material upwards, preventing clogging but may cause fraying on softer foams. Down-cut bits push material downward, resulting in cleaner top edges but requiring strong hold-down mechanisms to prevent lifting.
- Compression Bits: Combine up-cut and down-cut geometries to create clean edges on both sides of the material. They are useful for cutting foam sheets and laminated foam structures.
- Ball Nose Bits: Produces smooth surfaces when sculpting foam prototypes, signage, or molds. They are ideal for 3D carving and contour cutting in foam.
- Drag Knives and Oscillating Knife Tools: Offers precise, tear-free cuts with minimal dust production. Best suited for thin, flexible foams like EVA foam and soft polyethylene foams.
Bit Material and Coating
Choosing the right material and coating for CNC bits ensures durability and efficiency when cutting foam.
- Carbide Router Bits: More durable than high-speed steel (HSS), carbide bits maintain sharpness longer when cutting foam.
- Diamond-Coated Bits: Ideal for high-density foams, offering increased lifespan and smoother finishes.
- Titanium-Coated Bits: Reduce friction and heat buildup, preventing material melting.
Cutting Parameters for Foam
Foam requires careful tuning of cutting parameters to avoid material deformation and achieve optimal results.
- Spindle Speed (RPM): Generally set between 10,000–24,000 RPM, depending on foam type.
- Feed Rate: This should be adjusted based on foam density (higher feed rates for soft foams, slower for rigid foams).
- Depth per Pass: Soft foams can be cut in a single pass if the router bit is long enough. Dense foams should be cut in multiple passes to reduce resistance and avoid tool deflection.
- Chip Load: Ensuring the correct chip load prevents heat buildup, which can lead to foam melting.
Cooling and Dust Management Considerations
- Compressed Air Blower: Helps remove foam chips and prevents clogging.
- Vacuum System: Keeps the workspace clean by collecting foam particles.
- Foam-Specific Lubricants: Reduce friction in high-density foam cutting to minimize melting risks.
Choosing the right CNC router bits, materials, and cutting parameters ensures clean cuts, minimal waste, and high precision when working with foam. Whether using spiral bits, drag knives, or specialized coatings, proper tool selection and setup enhance both efficiency and final product quality.
Preparing the Foam for Cutting
Since the foam is lightweight and can be easily compressed or shifted during machining, securing it correctly and setting up the machine properly will ensure smooth cutting results. Below are the key steps to prepare foam for CNC cutting.
Selecting the Right Foam
Before cutting, choose a foam type that suits your application and CNC router capabilities. Consider the following factors:
- Foam Density: High-density foams (e.g., polyethylene and polyurethane) provide cleaner cuts, while low-density foams (e.g., expanded polystyrene) may require more careful handling to avoid fraying.
- Thickness: Ensure that your CNC router’s Z-axis clearance can accommodate the foam’s thickness.
- Flexibility: Soft foams may require special hold-down techniques to prevent shifting during cutting.
Securing the Foam on the Cutting Table
Since the foam is lightweight, it can easily move during the cutting process. Proper securing methods help maintain precision and avoid errors.
- Vacuum Table: A vacuum bed creates a strong suction force to hold foam securely in place without clamps. It is ideal for thin and flexible foams that may deform under mechanical pressure.
- Clamps and Fixtures: Mechanical clamps can be used for rigid and high-density foams. During the fixture process, make sure the clamp is outside the cutting area to prevent tool collision.
- Double-Sided Tape or Adhesive Spray: Suitable for thin foam sheets and small workpieces. Adhesive helps prevent movement while keeping the material flat.
- Sacrificial Board: Placing a sacrificial board under the foam prevents cutting through the machine bed.
Toolpath Setup and Software Configuration
Before running the CNC machine, proper toolpath programming is necessary to optimize the cutting process.
- Select the Right Cutting Tool: Choose the appropriate router bit or drag knife based on foam type.
- Adjust Cutting Speed and Feed Rate: Slow speeds prevent tearing, while high speeds may cause fraying. Fine-tune settings to match the foam’s properties.
- Optimize Depth per Pass: Cutting in multiple passes helps prevent excessive compression and ensures clean edges.
- Check Toolpath Simulation: Running a preview in CAM software ensures the path avoids errors or unnecessary material wastage.
Final Pre-Cut Inspection
Before starting the cut, verify the following:
- The foam is securely held down and will not shift.
- The correct router bit or drag knife is installed.
- The cutting depth and feed rate are properly set.
- The CNC router is properly calibrated for accuracy.
By following these preparation steps, you ensure smooth, clean, and precise foam cuts, reducing material waste and improving overall production efficiency.
Common Challenges and How to Overcome Them
Cutting foam with a CNC router presents unique challenges due to its soft, compressible, and lightweight nature. Issues such as fraying, material shifting, static buildup, and rough edges can affect the final cut quality. Below, we outline the most common challenges in CNC foam cutting and practical solutions to achieve clean, precise, and efficient results.
Foam Tearing and Fraying
Low-density and soft foams, such as expanded polystyrene (EPS) and polyurethane foam, tend to fray or tear along the edges, leaving rough or fuzzy surfaces. Here are the solutions:
- Use sharp, single-flute, or O-flute router bits designed for soft materials.
- Reduce the feed rate to minimize stress on the foam.
- Adjust spindle speed to find an optimal balance between cutting efficiency and material integrity.
- Use compression bits for laminated foams to create clean edges on both sides.
- Experiment with climb cutting instead of conventional cutting to reduce edge tearing.
Material Shifting or Lifting During Cutting
Foam is lightweight, which makes it prone to shifting or lifting during cutting, causing inaccuracies or misalignment. Here are the solutions:
- Use a vacuum table to hold foam securely without compressing it.
- For smaller workpieces, use double-sided tape or low-tack adhesive spray to keep the material in place.
- For rigid foams, mechanical clamps can be used, but avoid excessive pressure that could deform the foam.
- Use a sacrificial board (spoil board) underneath to ensure stability and prevent the tool from cutting into the machine bed.
Static Electricity Build-Up
Foam materials, especially polystyrene-based foams (EPS, XPS), tend to generate static electricity, which attracts dust and debris to the cutting area. Here are the solutions:
- Install anti-static brushes on the CNC router to dissipate static charge.
- Use a dust collection system to remove foam particles from the work area.
- Wipe foam surfaces with an anti-static spray before cutting.
- Ground the CNC router properly to prevent electrical interference.
Dust and Chip Accumulation
Foam cutting produces fine particles and dust, which can accumulate on the machine, reducing visibility and affecting accuracy. Here are the solutions:
- Use a dust collection system or vacuum attachment to remove foam particles during cutting.
- Apply compressed air to clear the cutting area while machining.
- Use bits with optimized chip evacuation, such as O-flute bits, to minimize clogging.
- Periodically pause cutting to clean the work area and prevent buildup.
Cutting Through Thick Foam Blocks
When cutting thick foam blocks, standard router bits may struggle to reach the full depth, causing uneven cuts. Here are the solutions:
- Use long-reach router bits designed for deep cutting applications.
- Cut in multiple passes, gradually increasing depth to avoid stressing the tool.
- Slow down the feed rate to maintain control over thick foam sections.
- If available, use a 5-axis CNC router to achieve deeper, more complex cuts with better control.
Final Tips for Overcoming Foam Cutting Challenges
- Choose foam-specific cutting tools to reduce fraying and tearing.
- Optimize cutting parameters (spindle speed, feed rate, and depth per pass) based on foam type.
- Secure foam properly using vacuum beds, tape, or clamps to prevent movement.
- Implement dust and static control measures to keep the workspace clean and prevent interference.
- Test cuts on scrap foam before starting the final job to fine-tune settings.
By addressing these common challenges, you can improve foam cutting efficiency, achieve high-quality results, and extend tool life, ensuring professional-grade CNC foam projects.
Applications of CNC Router Cut Foam
CNC router-cut foam is widely used across various industries due to its lightweight, shock-absorbing, insulating, and easily machinable properties. From packaging and insulation to artistic creations and industrial applications, CNC foam cutting provides precision, repeatability, and efficiency in manufacturing and custom projects. Below are some of the most common applications of CNC router-cut foam.
Packaging and Protective Inserts
CNC-cut foam is extensively used in protective packaging for fragile or high-value products. It helps absorb shocks, preventing damage during shipping and storage.
- Custom foam inserts for tool boxes, medical instruments, and electronics.
- Product packaging for cameras, drones, and delicate machinery.
- Flight case inserts for musical instruments, military gear, and industrial equipment.
EVA foam layers for cushioning high-impact items like firearms and sports gear.
Signage and Advertising Displays
Foam is widely used in the signage and advertising industry due to its ease of shaping and cost-effectiveness. CNC routers can create custom logos, 3D lettering, and decorative signboards with high precision.
- Retail and commercial signs: Foam is used to create dimensional letters for branding.
- Event displays and trade show booths: Large, lightweight signage is easy to transport.
- Architectural lettering for indoor and outdoor advertisements.
- POP (Point of Purchase) displays for retail marketing.
Prototyping and Model-Making
CNC routers are widely used in prototyping and model-making, allowing manufacturers, designers, and engineers to create accurate foam mockups before full-scale production. Foam is ideal for architectural models, automotive prototypes, and product design validation due to its ease of machining and cost-effectiveness.
- Architectural models for real estate and urban planning.
- Automotive and aerospace prototypes for testing and design evaluation.
- 3D sculpting and mold-making for industrial applications.
- Industrial concept models before mass production.
Props, Set Design, and Themed Environments
CNC-cut foam is extensively used in film, theater, amusement parks, and exhibitions to create realistic props, set designs, and themed structures. Foam is lightweight, easy to shape, and can be finished with paints and coatings for a realistic appearance.
- Movie and theater props: Lightweight foam makes large props easy to handle.
- Themed environments: Amusement parks use CNC foam to create immersive experiences.
- Custom sculptures and decor for museums, stage productions, and exhibitions.
- 3D artistic installations for special events and advertising campaigns.
Insulation and Soundproofing
Foam is widely used for thermal insulation and soundproofing in construction, recording studios, and industrial applications. CNC routers can precisely cut foam panels for walls, ceilings, and enclosures to improve temperature control and noise reduction.
- Acoustic foam panels for soundproofing music studios and offices.
- Thermal insulation boards for buildings, refrigeration, and HVAC systems.
- Noise barriers for industrial facilities and machinery enclosures.
CNC router-cut foam is versatile and widely used across industries, from packaging and prototyping to 3D sculpting and mold-making. By selecting the right foam type and cutting strategies, manufacturers can achieve high precision, reduced waste, and cost-effective solutions for various projects.
Summarize
Cutting foam with a CNC router is a highly effective way to achieve precise, clean, and repeatable results for a wide range of applications. Whether what foam material you’re cutting, a CNC router provides unmatched accuracy and efficiency when paired with the right tools, cutting strategies, and software. With proper preparation, regular maintenance, and the right CAM software, CNC foam cutting can be a smooth and effective process, allowing you to create high-quality, professional results with ease. To learn more about the application areas of CNC routers, you can continue reading “What Industries Are CNC Routers Used In”.
When it comes to cutting foam with precision and efficiency, AccTek CNC stands out as a professional CNC router manufacturer offering high-quality, reliable solutions for a wide range of applications. Our CNC routers are designed with high-speed spindles, robust cutting beds, and advanced motion control systems to ensure smooth and precise foam machining. If you’re looking for a trusted solution to improve productivity, accuracy, and material optimization, AccTek CNC is a top choice for high-performance foam cutting.