- 10-15 Min Read
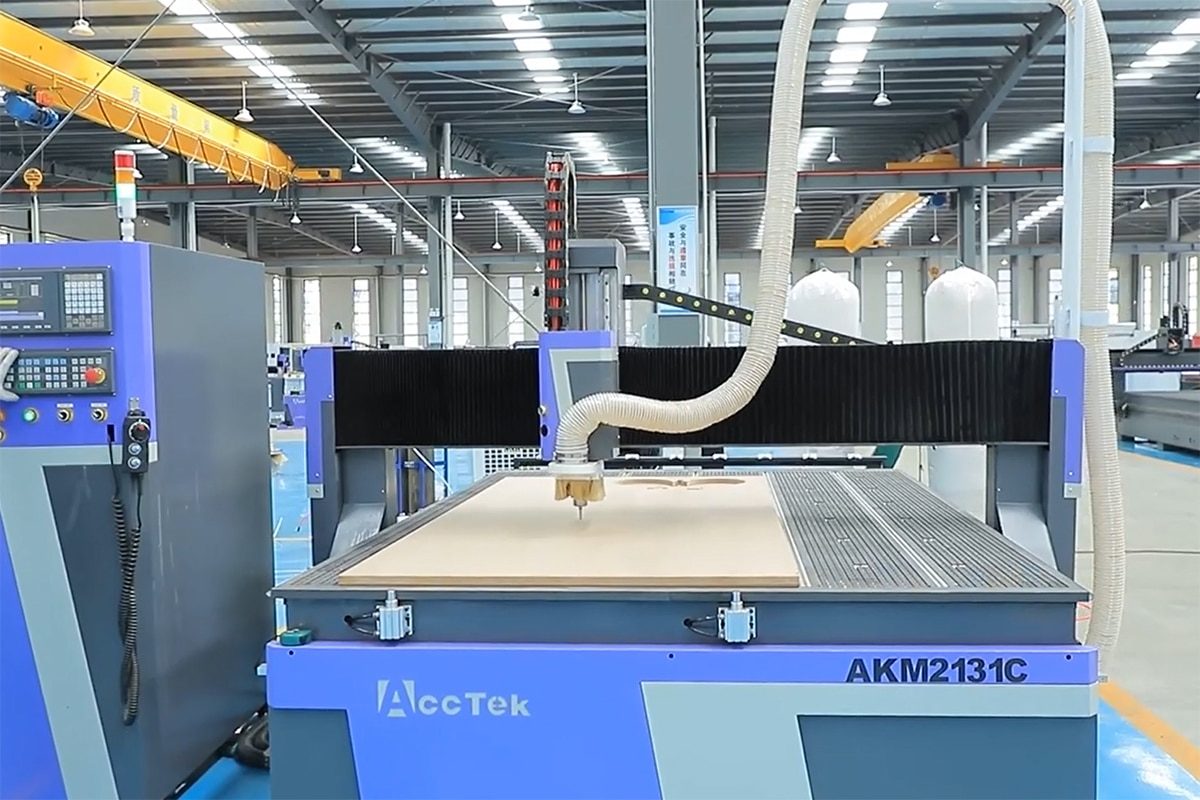
Correct placement of objects on a CNC router is a prerequisite for machining with precision, efficiency and safety. Whether you’re cutting, engraving, or carving, ensuring that the material is correctly positioned and securely held can significantly impact the final result. Misalignment, shifting, or improper securing can lead to errors, material waste, and even damage to the machine.
This guide will walk you through the basic steps for properly placing an object on a CNC router, covering key factors such as material preparation, alignment methods, fixturing techniques, and maintenance inspection. By following these best practices, you can maximize the accuracy and efficiency of your CNC operations, reducing errors and improving overall productivity.
The Importance of Correct Placement on a CNC Router
Properly placing objects on a CNC router is a crucial step that directly affects machining quality, operational efficiency, and overall productivity. To understand why correct placement matters, we can examine its impact from two key aspects: how placement affects processing quality and the benefits of proper placement.
Understanding the Impact of Placement on Processing Quality
The CNC router operates based on precise coordinates, meaning any misalignment or improper positioning can lead to inaccurate machining results. Incorrect placement can cause:
- Offset Cuts and Dimensional Errors: If the material is not properly aligned, the cutting path may deviate from the intended design, resulting in incorrect dimensions.
- Poor Surface Finish: If the material is not securely fixed, vibrations or movement can lead to rough edges, uneven depths, or inconsistent engraving quality.
- Tool Interference and Collisions: Misplaced materials may cause the cutting tool to collide with clamps, fixtures, or the worktable, damaging both the tool and the machine.
The Benefits of Correct Placement
Correctly positioning materials on a CNC router not only improves processing quality but also enhances overall operational efficiency and cost-effectiveness. Key benefits include:
- Higher Accuracy and Consistency: Properly aligned materials ensure the CNC router follows the programmed path precisely, reducing errors and ensuring uniform production quality.
- Optimized Material Utilization: Correct placement allows for better nesting and positioning of cuts, minimizing material waste and lowering production costs.
- Reduced Machine Wear and Tool Breakage: Preventing improper placement reduces the risk of tool crashes and excessive wear, extending the lifespan of both the router and cutting tools.
- Safer Operation: A securely placed workpiece prevents movement during machining, reducing the risk of accidents, tool damage, and operator injury.
- Improving Workflow Efficiency: When materials are placed correctly from the start, operators spend less time adjusting, repositioning, or troubleshooting errors.
By understanding the importance of correct placement, CNC operators can achieve higher quality results, optimize production efficiency, and ensure a safer working environment. The following sections will provide detailed steps on how to correctly position and secure objects for optimal CNC router performance.
Material Preparation for CNC Routing
Proper material preparation is beneficial for achieving precise and efficient CNC routing. Before placing an object on a CNC router, operators must ensure that the material is clean, flat, and correctly sized for machining. The following steps outline key aspects of material preparation:
Selecting and Considering the Quality of Stock Materials
Choosing the right material is the foundation of successful CNC routing. The quality of the stock material directly affects machining accuracy and final product quality.
- Material Type: Ensure that the material is compatible with CNC routing. Common materials include wood, plastics, aluminum, composites, and acrylic.
- Material Quality: Inspect for defects such as knots, cracks, warping, or internal voids, which may cause uneven cutting or tool breakage.
- Consistency: Select materials with uniform density and grain structure to ensure consistent machining performance.
Dimensioning and Surface Treatment of Materials
Properly sizing and treating the material ensures it fits within the CNC router’s work area and improves cutting precision.
- Cutting to Size: Trim large stock to appropriate dimensions before placing it on the CNC router, ensuring it fits within the machine’s cutting range.
- Surface Preparation: Clean the surface with compressed air or a brush to remove dust, oil, or contaminants that could affect adhesion or stability.
- Moisture Consideration: For wood materials, ensure the moisture level is appropriate to prevent warping during machining.
Fixing Materials on the CNC Routing Machine
Proper securing of materials prevents movement during cutting, ensuring precision and safety.
- Clamping Methods: Use T-slot clamps, edge clamps, or toe clamps for securing materials firmly in place.
- Vacuum Table: For flat and non-porous materials, a vacuum table provides strong hold-down without mechanical clamps.
- Adhesive Hold-Downs: Double-sided tape or spray adhesives can be used for lightweight or thin materials to prevent shifting.
- Screws and Nails: For wood or soft materials, screws can secure the material directly to the spoil board.
Considering the Variation of Material Thickness
Material thickness can vary slightly due to manufacturing inconsistencies or environmental factors, affecting cut depth and toolpath accuracy.
- Measuring Thickness: Use a caliper to check multiple points on the material to ensure consistency.
- Compensating for Variations: Adjust Z-axis zeroing to accommodate minor thickness changes, preventing cutting too deep or too shallow.
- Using a Spoil Board: A sacrificial board beneath the material helps account for minor thickness variations and protects the machine bed.
By following these material preparation steps, CNC operators can enhance machining accuracy, reduce errors, and improve overall efficiency, ensuring high-quality output from their CNC router.
Understanding Fixture Design and Construction
Fixtures are essential components in CNC routing, providing stability, accuracy, and repeatability during machining operations. Properly designed fixtures prevent material movement, improve efficiency, and enhance machining precision. To ensure effective fixture implementation, it is important to understand the principles of fixture design and construction.
Fixture Requirements
The primary function of a fixture is to securely hold the workpiece in place while allowing unobstructed cutting. Key requirements for CNC router fixtures include:
- Workpiece Stability: The fixture must prevent shifting, vibrations, or deflection during machining.
- Accessibility: The fixture design should not obstruct the cutting tool’s path or limit machining operations.
- Ease of Setup and Removal: A well-designed fixture should allow for quick installation and removal to reduce machine downtime.
- Repeatability: The fixture should ensure the workpiece is positioned consistently for repeated machining operations.
- Compatibility with Different Materials: Depending on the type of material (wood, metal, plastic), the fixture design must be adapted accordingly.
Types of CNC Milling Machine Fixtures
Different types of fixtures are used based on the shape, size, and material of the workpiece. Common fixture types include:
- T-Slot Clamping Fixtures: It utilizes T-slot tracks on the CNC routerbed for flexible positioning and is suitable for a wide range of materials, including wood, metal, and composites. Adjustable clamps allow repositioning for different workpiece sizes.
- Vacuum Fixtures: Uses suction to hold down flat, non-porous materials without mechanical clamps, ideal for machining thin sheets, acrylic, and lightweight workpieces. This clamping type requires a well-sealed vacuum bed for maximum holding strength.
- Custom-Built Dedicated Fixtures: Designed for specific parts with unique geometries or complex contours, commonly used in high-precision applications requiring consistent workpiece placement. Often includes locating pins, modular inserts, or soft jaws for specialized holding.
- Adhesive and Tape Fixtures: Uses double-sided tape or spray adhesive to secure small, lightweight workpieces, suitable for delicate materials that may be damaged by mechanical clamps. This clamping type requires proper surface preparation to ensure strong adhesion.
Fixture Material Selection
The choice of material for a fixture affects its durability, precision, and cost-effectiveness. Common fixture materials include:
- Aluminum and Steel: Durable and precise, commonly used for high-rigidity applications, especially in metalworking.
- MDF and Plywood: Cost-effective, ideal for sacrificial or custom fixtures in woodworking.
- Plastic and Acrylic: Lightweight and non-marking, suitable for softer materials or specialized machining needs.
- Composites: Fiberglass or carbon-fiber-reinforced plastics are sometimes used for specialized fixtures requiring strength and low weight.
Key Considerations in Fixture Design
For a fixture to perform effectively, it must provide a stable and repeatable setup. Key design principles include:
- Strong Clamping Mechanism: The fixture must hold the workpiece securely without excessive pressure that could deform softer materials.
- Zeroing and Reference Points: Incorporating fixed reference stops or locating pins ensures repeatable alignment for batch machining.
- Clearance for Tool Access: The fixture should not obstruct the router bit, allowing full cutting access without collisions.
- Modularity and Adjustability: Fixtures should allow for quick modifications or adaptability to accommodate different workpiece sizes.
- Wear and Maintenance Considerations: Over time, fixtures can wear out or lose accuracy. Selecting materials and designs that are easy to repair or replace ensures long-term usability.
By understanding fixture design and construction principles, CNC operators can improve machining accuracy, efficiency, and overall productivity. Well-designed fixtures not only enhance precision but also reduce errors, material waste, and setup time, leading to a more streamlined CNC routing process.
Alignment Technology for Precise Placement
Achieving high precision in CNC routing depends on the proper alignment of the workpiece. Advanced alignment technology ensures accurate positioning, minimizes errors, and enhances machining quality. Below, we explore the key aspects of alignment technology for precise placement.
Establishing a Reference Coordinate System
A reference coordinate system serves as the foundation for accurate placement and machining. Properly setting up the coordinate system ensures that all machining operations align with the intended design.
- Machine Zero vs. Work Zero: The machine zero (home position) is a fixed reference, while the work zero is manually set to match the material placement.
- G54-G59 Work Offsets: These offsets allow operators to define custom reference points for different workpieces without changing the machine’s home position.
- Datum Points: Using a fixed corner or center of the workpiece as the origin ensures consistency across multiple production runs.
- Grid and Fixture-Based Alignment: Some CNC router worktables have pre-marked grids or dedicated fixture locations to assist in repeatable positioning.
Using Edge Finders and Probes to Align Workpieces
Edge finders and probing systems enhance workpiece alignment by accurately detecting material edges and corners. Using these tools eliminates manual guesswork, reducing setup time and improving machining accuracy.
- Mechanical Edge Finders: These tools allow manual alignment by physically detecting the edge of the material.
- Electronic Edge Finders: Provide more precision by detecting conductivity changes when the tool touches the workpiece.
- Touch Probes: Automatically measure and set reference points by touching the material and adjusting the CNC software accordingly.
- Laser Alignment Systems: Project laser crosshairs onto the material, enabling visual alignment before machining begins.
Achieving Repeatable Positioning of Reference Features
For mass production or multiple-stage machining, repeatable positioning ensures that every workpiece is placed consistently.
- Dedicated Fixtures and Locating Pins: Pre-installed pins or slots help position materials in the exact same location for repeated jobs.
- Vacuum Workholding with Position Guides: Combining vacuum tables with physical guides ensures secure and consistent placement.
- Alignment Stops and Clamps: Mechanical stops prevent lateral movement, ensuring workpieces remain in the correct position.
- Using Dowel Holes for Double-Sided Machining: When machining both sides of a part, precision dowel holes allow the workpiece to be flipped while maintaining perfect alignment.
Verifying Alignment Accuracy Through Trial Cutting and Measurement
Before executing the full machining process, alignment accuracy must be verified through testing methods:
- Dry Run (Air Cutting): Running the CNC router without engaging the cutting tool allows operators to check the toolpath visually.
- Probe-Based Measurement: CNC touch probes can measure key reference points and compare them to programmed dimensions.
- Trial Cuts on Scrap Material: Cutting a test piece helps identify alignment errors before machining valuable materials.
- Calipers and Dial Indicators: Measuring machined edges and features ensures they match the design specifications.
By implementing these alignment technologies, operators can enhance machining precision, reduce setup times, and improve overall efficiency in CNC manufacturing.
Special Considerations for Different Material Types
When placing materials on a CNC router, different materials require specific handling to prevent movement, misalignment, and surface damage. Below are the key factors to consider when placing each material type correctly on a CNC router.
Wood
Wood is a natural material with inherent variations in grain structure, density, and moisture content, which can affect machining accuracy and surface quality.
- Grain Orientation and Machining Direction: When possible, align the toolpath with the grain to reduce tear-out and achieve cleaner edges.
- Dealing with Variations in Moisture Content: Wood absorbs moisture, which can cause dimensional instability. Use properly dried and acclimated wood to reduce warping.
- Using Spoil Boards: MDF or sacrificial boards help prevent marking from clamps and improve hold-down.
- Workholding Methods: Use T-slot clamps for thick hardwood, vacuum tables for sheet materials, or screws for rough stock.
Metals
CNC routing of metals requires special attention to heat management, workpiece stability, and chip evacuation to maintain precision and tool longevity.
- Avoiding Workpiece Deformation and Distortion: Use even clamping pressure and avoid over-tightening to prevent bending of thin sheet metal. Also, metal expands when heated, allowing for small gaps where necessary.
- Proper Cooling and Chip Evacuation: Some metals require coolant, so positioning should allow proper fluid drainage and chip removal.
- Choosing the Right Workholding Method: A vice or fixture plate is best for rigidly holding small or thick metal parts. A toe clamp is great for securing metal sheets without obstructing the cutting path. A vacuum or magnetic hold-down is ideal for non-ferrous metals (e.g., aluminum, brass) where traditional clamping is difficult.
Plastics and Composites
Plastics and composites can be brittle, prone to delamination, and sensitive to heat, requiring precise control of machining parameters.
- Minimizing Delamination and Surface Damage: Reduce tool pressure to avoid material separation. Place a sacrificial spoil board underneath to prevent edge chipping and warping.
- Controlling Heat During Machining: Plastics can warp or melt under high-speed cutting, ensuring minimal surface contact with clamps.
- Use Soft Clamping Pads: Avoid direct metal-to-plastic contact to prevent marring.
- Vacuum Tables for Thin Sheets: Prevents material from lifting or shifting during high-speed cutting.
Different materials require specialized placement, securing, and stability techniques to optimize CNC machining performance. Wood must be aligned with grain direction and accounted for warping, metals require rigid hold-downs to prevent distortion, plastics and composites need even pressure to avoid warping or surface damage. By selecting the right placement strategy, CNC router operators can ensure better accuracy, reduced material waste, and improved machining efficiency.
Maintenance and Inspection of Fixtures and Alignment Systems
Ensuring accurate placement of materials on a CNC router requires well-maintained fixtures and alignment systems. Regular maintenance improves machining precision, prevents material shifting, and extends the lifespan of equipment. Below are four key aspects of maintaining and inspecting fixtures and alignment systems for optimal CNC operation.
Regular Cleaning and Inspection of CNC Milling Machines and Fixtures
Routine cleaning and inspection help maintain the integrity of fixtures and workholding systems, ensuring a stable and debris-free surface for material placement.
- Cleaning Procedures: Remove chips, dust, and debris after each use to prevent buildup that could affect fixture positioning. Clean vacuum tables and T-slot beds to ensure proper suction and clamping efficiency.
- Inspection Checklist: Check for rust, residue, or coolant buildup that could affect fixture stability. Ensure clamping surfaces remain flat and free from scratches or dents that could misalign materials.
Checking Fixture Stability and Wear
Over time, clamping pressure, repeated use, and environmental factors can lead to wear on fixtures, reducing their effectiveness.
- Ensuring Fixture Stability: Test clamping force to ensure materials are held firmly without unnecessary flexing. Tighten all screws, bolts, and fasteners to maintain fixture rigidity. For vacuum hold-downs, check for leaks or blockages that could reduce suction strength.
- Identifying Wear Issues: Inspect T-slot tracks and fixture bases for signs of wear that may cause instability. Ensure magnetic fixtures maintain their holding power and replace weak magnets if necessary.
Calibration and Verification of Alignment Systems
CNC alignment systems must be calibrated regularly to ensure the workpiece is accurately positioned relative to the cutting tool.
- Checking Machine Zero and Work Offsets: Verify machine home position (G54-G59 offsets) to ensure workpieces are placed consistently. Use a probe or edge finder to confirm material edges align correctly before machining.
- Alignment System Calibration: Test laser or optical alignment systems to ensure accurate positioning of reference marks. Perform grid or squareness checks using a machinist’s square and dial indicator.
Solving Wear Problems of Clamping and Holding Components
Clamping and holding components are subject to constant pressure, vibration, and wear, affecting workpiece stability.
- Identifying Common Clamping Wear Issues: This includes the clamps losing grip strength due to worn-out threads or mechanical fatigue, vacuum leaks in vacuum tables leading to weak holding power, and adhesive hold-downs losing effectiveness from residue buildup or poor adhesion.
- Solutions for Restoring Holding Efficiency: Replace worn clamps, screws, and bolts to maintain strong grip force. Refurbish vacuum tables by cleaning or sealing leaks to restore suction performance. Use new adhesive solutions or replace worn tapes for better hold on lightweight materials.
By implementing regular maintenance and inspection of fixtures and alignment systems, CNC router operators can ensure high-precision machining, improved repeatability, and reduced downtime. A well-maintained setup not only enhances accuracy but also extends the lifespan of CNC components, leading to more efficient and cost-effective operations.
Summarize
Correctly placing objects on a CNC router is fundamental to achieving precise, efficient, and high-quality machining results. By carefully preparing materials, using appropriate fixtures, and ensuring accurate alignment, operators can minimize errors, reduce waste, and extend the lifespan of both tools and workpieces. Different materials require specific placement strategies, and understanding their unique properties helps optimize machining performance. Mastering these placement techniques enhances workflow efficiency, improves consistency, and ultimately leads to superior CNC machining outcomes.
When it comes to precision, reliability, and efficiency in CNC routing, AccTek CNC stands out as a professional CNC router manufacturer dedicated to providing high-quality solutions. AccTek CNC routers feature robust worktables, precise alignment tools, and versatile clamping systems to ensure stable and repeatable material placement. For manufacturers, businesses, and craftsmen looking for precision-engineered CNC routers that simplify material placement and guarantee consistent output, AccTek CNC is the ideal choice.