- 15-20 Min Read
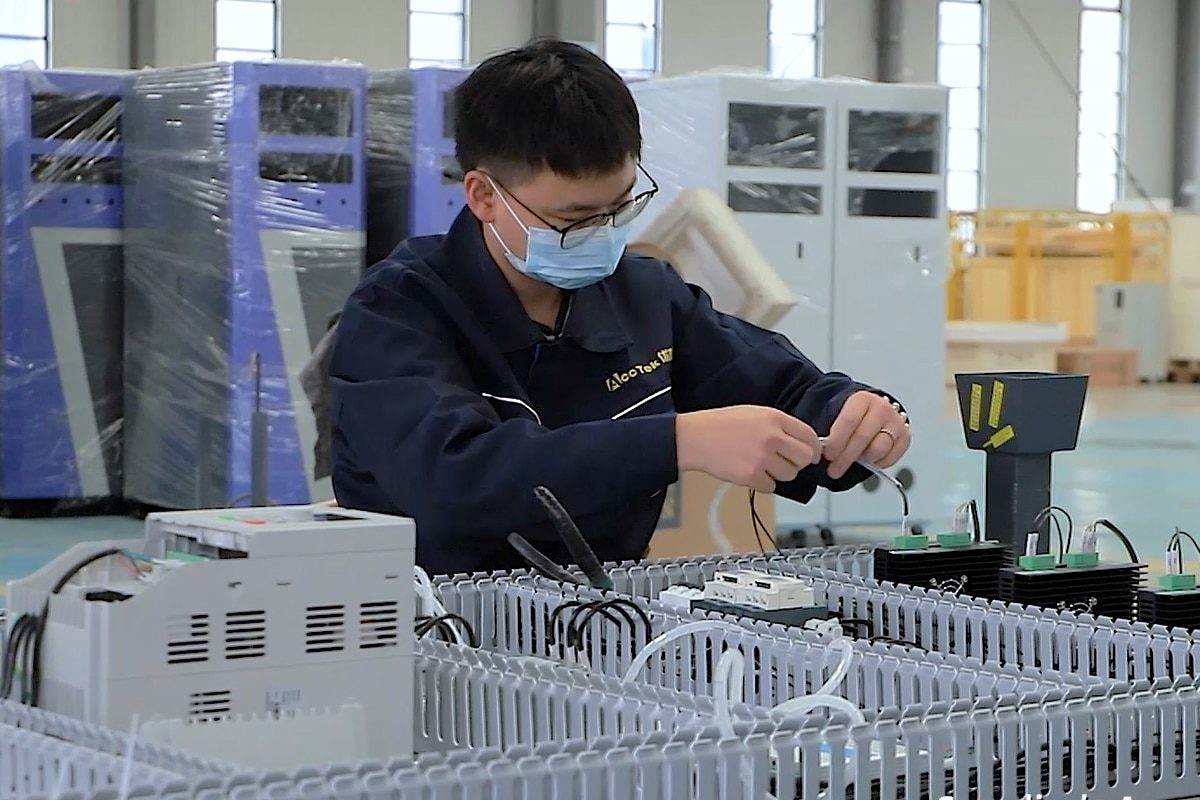
A CNC router is a powerful tool used in woodworking, metalworking, and other industries for precision cutting, engraving, and shaping materials. However, before you can start using it, you need to set it up and connect it properly. Ensuring a correct connection not only guarantees smooth operation but also prevents potential issues that could affect performance and safety.
This guide will walk you through the essential steps to connect a CNC router, from preparing the workspace to wiring components, installing cables, and troubleshooting common issues. Whether you’re setting up a new machine or reconnecting an existing one, following these steps will help ensure a reliable and efficient CNC system.
Understanding CNC Router Electrical Components
A CNC router consists of various electrical components that work together to ensure precise movement and control. Understanding these components is a prerequisite for proper installation, troubleshooting, and maintenance. Below are the key electrical components found in a CNC router system:
Spindle
The spindle is the heart of the CNC router, responsible for cutting, engraving, and shaping materials. It consists of:
- Spindle Motor: Rotates the cutting tool at high speeds, typically ranging from a few thousand to over 24,000 RPM.
- Variable Frequency Drive (VFD): Controls the spindle speed and torque by adjusting the electrical frequency.
- Cooling System: Spindles can be either air-cooled (using built-in fans) or water-cooled (using a pump and radiator).
Motor System
Motors drive the movement of the CNC router along the X, Y, and Z axes. The two main types are:
- Stepper Motors: Move in discrete steps, providing high precision at lower speeds. Commonly used in hobbyist and mid-range CNC routers.
- Servo Motors: Offer closed-loop control with feedback sensors, ensuring smoother and more precise movement. Commonly used in industrial CNC routers.
- Motor Drivers: Convert signals from the control system into electrical power to drive the motors.
Power Supply System
The power supply system provides the necessary electrical energy to run all components:
- Main Power Supply: Converts AC power from the wall outlet to the required DC voltage for the CNC system.
- Low Voltage Power Supply: Powers control boards, sensors, and other low-energy components.
- High Voltage Power Supply: Drives high-energy components such as the spindle and motors.
Control Panel and Controller
The control panel is the command center of the CNC router, allowing the operator to input commands and monitor machine operation. It includes:
- CNC Controller: The brain of the CNC router, processing G-code and sending movement signals to the motors.
- Interface Ports: USB, Ethernet, or parallel ports for connecting the CNC router to a computer or external control system.
- Display Screen and Keypad: Some machines include an LCD or touchscreen interface for manual control.
Limit Switches
Limit switches ensure safe and accurate movement by detecting the end points of each axis:
- Homing Switches: Help the CNC router find its reference point upon startup.
- Soft and Hard Limits: Prevent over-travel and potential machine damage by stopping motion when a limit is reached.
Emergency Stop Button (E-Stop)
A critical safety feature, the emergency stop button (E-stop) instantly shuts down the machine in case of an emergency.
- Wired E-Stop: Directly interrupts the power supply to the machine.
- Wireless E-Stop: Some advanced CNC systems offer remote emergency stop options.
Auxiliary Devices
Auxiliary devices enhance the performance, safety, and ease of use of the CNC router:
- Coolant System: Keeps the spindle and cutting tools cool, reducing wear and improving cutting efficiency.
- Dust Collection System: Removes debris and fine particles to maintain a clean working environment.
- Workpiece Clamping System: This may include vacuum tables or clamps to secure the material in place.
- Lighting System: Provides better visibility, improving accuracy and safety during operation.
Proper understanding and maintenance of these components will ensure that your CNC router operates smoothly and efficiently, reducing downtime and improving precision in your machining tasks.
Pre-Installation Preparation for a CNC Router
Before connecting and setting up a CNC router, proper pre-installation preparation is beneficial to ensure smooth operation, safety, and longevity of the machine. The following steps will guide you through the necessary preparations.
Work Area Organization and Layout
Proper workspace organization is beneficial for smooth CNC router operation. Consider the following factors:
- Stable and Level Surface: Ensure the machine is placed on a solid, level surface to prevent vibrations that could affect precision.
- Space Allocation: Ensure enough clearance around the machine for easy access, material handling, and maintenance.
- Ventilation and Cooling: Position the machine in a well-ventilated area, especially if using a water-cooled spindle or a dust collection system.
- Electrical Access: The location should have easy access to a stable power supply that meets the machine’s voltage and current requirements.
- Dust and Debris Control: If working with wood, plastic, or other materials that generate dust, set up a dust collection system to maintain a clean workspace and protect machine components.
Understanding Electrical Requirements and Specifications
A CNC router requires a stable and adequate power supply. Key electrical considerations include:
- Voltage and Current Rating: Check the machine’s power requirements (e.g., 110V, 220V, or higher). Ensure your electrical outlet can handle the current draw.
- Power Phase Requirement: Some CNC routers operate on single-phase power, while industrial machines may require three-phase power.
- Dedicated Circuit: To prevent overload and electrical fluctuations, it is recommended to connect the CNC router to a dedicated power circuit.
Selecting Wiring Materials and Components
Choosing the right wiring materials ensures safe and efficient electrical connections. Consider the following:
- Wire Gauge Selection: Use wires that match the power and current needs of the CNC router. Higher power machines require thicker gauge wires.
- Shielded Cables: Use shielded cables for signal and motor wiring to reduce electromagnetic interference (EMI) that can cause erratic machine behavior.
- Connectors and Terminals: Select high-quality connectors to ensure secure and stable connections, preventing power loss and signal interruptions.
- Cable Management Accessories: Use cable trays, conduits, and zip ties to keep wiring organized and protected from mechanical damage.
Creating Wiring Diagrams and Schematics
Planning a clear and well-structured wiring diagram helps streamline installation and troubleshooting. Key elements include:
- Power Supply Routing: Map out how power flows from the main supply to different machine components (controller, motors, spindle, sensors).
- Signal Wiring Layout: Plan connections between the CNC controller, stepper/servo motors, and limit switches.
- Emergency Stop and Safety Switches: Clearly mark safety-related wiring to ensure easy identification and quick access in case of an emergency.
- Cooling System Wiring: Include wiring for water pumps or cooling fans if the machine requires thermal management.
- Labeling and Documentation: Label all wires and connections to simplify future maintenance and troubleshooting.
Safety Precautions
Prioritizing safety during CNC router installation prevents accidents and ensures long-term reliability. Follow these safety measures:
- Power Isolation: Always disconnect the CNC router from the power source before making electrical connections.
- Proper Grounding: Ensure that all electrical components are properly grounded to prevent electrical shocks and protect against power surges.
- Protective Gear: Wear insulated gloves when handling electrical components and safety goggles to protect against debris during operation.
- Compliance with Electrical Standards: Follow national and local electrical codes to ensure safe installation and prevent violations.
- Training and Manuals: Review the CNC router manual and ensure operators are trained in handling and troubleshooting the machine.
Proper pre-installation preparation ensures a hassle-free setup and long-term efficiency of your CNC router. By performing the above preparations, users can avoid common installation problems and optimize the performance of their CNC routers.
Wiring Setup for CNC Router Components
After the preparation is completed, we start the connection step of a CNC router. Each component, from the spindle to the control board, must be correctly connected to ensure stable performance, precise movement, and reliable safety mechanisms. Here is an overview of the wiring setup for key CNC router components.
Spindle Wiring
The spindle is the primary cutting tool in a CNC router, and its wiring ensures proper power delivery and control. Here is the wiring process:
- Wire the Spindle to the VFD (Variable Frequency Drive): Match the U, V, and W terminals on the VFD to the spindle motor wires.
- Control Signal Wiring: Connect the VFD to the CNC controller for speed control via PWM or analog signals.
- Verify Rotation Direction: If the spindle rotates in the wrong direction, swap two motor wires.
Motor Wiring
The motors drive the movement of the CNC router along the X, Y, and Z axes. These can be stepper motors or servo motors. Here is the wiring process:
- Identify Motor Wires: Stepper motors usually have four, six, or eight wires, while servo motors have additional feedback wiring.
- Connect to Motor Drivers: Match motor phase wiring with the motor driver terminals (A+, A-, B+, B- for stepper motors).
- Power and Signal Connection: Ensure proper voltage supply to the motor driver and connect control signal wires from the CNC controller.
- Testing and Calibration: Run a test movement to ensure the proper direction and functionality of the motors.
Power Wiring
The power supply provides the necessary electrical energy for the CNC router’s components. Here is the wiring process:
- Main Power Connection: Ensure the CNC router is plugged into a dedicated circuit with the correct voltage (110V/220V or 380V for industrial machines).
- Power Supply Unit (PSU) Setup: Convert AC power to DC for stepper/servo motors, controllers, and sensors.
- Grounding: Proper grounding is necessary to prevent electrical interference and equipment damage.
- Fuse or Circuit Breaker Installation: Install a fuse or circuit breaker to prevent damage from power surges or short circuits.
CNC Controller Wiring
The CNC controller is the brain of the machine, managing motion control and processing commands from the computer. Here is the wiring process:
- Connect the Power Supply to the Controller: Match the correct polarity to avoid damage.
- Signal Cable Connection: Use shielded cables to connect the controller to the motors, limit switches, and other peripherals.
- Communication Interface: Connect the controller to the computer via USB, Ethernet, or parallel port, depending on the machine’s setup.
- Secure and Organize Wires: Use cable ties and wire ducts to keep connections tidy and prevent signal interference.
Limit Switch Wiring
Limit switches prevent over-travel and help in homing the machine. Here is the wiring process:
- Determine Switch Type: Normally Open (NO) or Normally Closed (NC) configuration.
- Connect to the Controller: Wire each axis limit switch to the designated input ports on the CNC controller.
- Use Shielded Cables: Use shielded cables to minimize electrical noise and false triggers.
- Test the Switches: Jog the machine to confirm proper activation and stopping at limit positions.
Emergency Stop Button Wiring
An emergency stop (E-stop) button immediately halts all operations in case of a malfunction or danger. Here is the wiring process:
- Determine Wiring Type: The E-stop button can be wired in series with the main power line or connected to the controller as an input signal.
- Wire to the Controller or Power Line: Ensure proper placement for easy access in an emergency.
- Test for Proper Functionality: Verify that the machine stops immediately when the button is activated.
Auxiliary Device Wiring
Additional devices enhance CNC router operation and safety. Here is the wiring process:
- Cooling System: Connect a water pump (for water-cooled spindles) to the power supply and confirm continuous flow. Install fans if air-cooled.
- Lighting System: Wire LED lights to improve visibility around the work area.
- Dust Collection System: Connect dust extraction units to an independent power source or relay switch for automatic activation.
Final Wiring Checks
Before powering up the CNC router, perform these checks:
- Ensure all wires are securely fastened and connections are correctly matched.
- Verify the grounding system to prevent electrical shocks.
- Check for short circuits or loose connections.
- Organize and shield wiring to prevent electromagnetic interference.
- Test each component step by step before running a full job.
A well-executed wiring setup ensures that a CNC router operates efficiently, accurately, and safely. By following the correct wiring procedures, users can minimize the risk of errors and ensure smooth machine performance. Proper organization, shielding, and safety precautions should always be observed to maintain reliable operation and prevent potential electrical issues.
Cable Management and Cabling for CNC Routers
A well-organized wiring system minimizes electrical interference, reduces mechanical stress, and simplifies troubleshooting. Poorly managed cables can lead to performance issues, accidental damage, or safety hazards. Here are the best practices for cable management.
Organizing Harnesses and Cables
A structured wiring layout improves CNC router reliability and ease of maintenance.
- Bundle Cables into Harnesses: Use zip ties, cable sleeves, or Velcro straps to bundle similar cables (e.g., motor power, sensor, signal) into groups to keep them in order.
- Segregate Power and Signal Wires: Separate high-voltage power lines from low-voltage signal cables to prevent electromagnetic interference (EMI). Route motor power cables and spindle cables away from the limit switch and control signal wiring.
- Maintain Proper Bend Radius: Follow the minimum bend radius recommended for each cable type to avoid sharp bends that could damage the insulation or cause signal degradation.
Routing to Minimize Interference and Hazards
Proper routing techniques help avoid signal noise, accidental disconnections, and tripping hazards.
- Designate Separate Paths for Different Cable Types: Route high-power cables separately from data cables to avoid signal disruption. Use shielded cables for stepper motor wiring, limit switches, and control signals.
- Keep Cables Away from Moving Parts: Secure cables to the machine frame or cable ducts for stability. Ensure that the wiring does not get pinched or tangled in the machine’s moving components.
- Use Conduits and Cable Trays: Install protective conduits to shield cables from dust, debris, and mechanical stress. Use cable trays to guide the wiring neatly along the machine’s structure.
- Provide Strain Relief at Connection Points: Secure cables at both ends to prevent pulling or stress on connectors. Use strain relief brackets near the controller board, power supply, and spindle motor.
Securing and Protecting Wiring in the Rack
Ensuring the wiring inside the control cabinet or rack is properly secured helps prevent electrical faults and improves airflow.
- Use Cable Management Panels: Install panels with built-in clips or brackets to keep cables organized.
- Ensure Proper Grounding: Ground all metal racks and shields to reduce electrical noise and improve safety.
- Maintain Adequate Airflow: Arrange cables to avoid blocking cooling fans or ventilation areas.
Labeling and Documentation for Easy Troubleshooting
Clearly labeled cables and well-documented schematics simplify future maintenance and upgrades.
- Use Durable Labels: Label both ends of each cable with machine-readable tags or color-coded markers.
- Follow a Standardized Naming Convention: Assign unique labels to each connection (e.g., M1-PWR for Motor 1 Power, S-LIMIT for Spindle Limit Switch).
- Create a Wiring Diagram: Maintain updated schematics that show cable routes, voltage ratings, and connection points. Include details on wire gauge, shielding, and grounding locations.
- Keep a Troubleshooting Log: Record past issues and solutions for quick reference.
By following best practices, you can ensure stable operation and reduce maintenance efforts. A well-organized wiring setup not only enhances machine performance but also simplifies future upgrades and repairs.
Troubleshooting Common Wiring Problems
Wiring problems in a CNC router can cause operational failures, reduced accuracy, and unexpected shutdowns. Identifying and resolving these issues promptly ensures smooth performance and prevents long-term damage. Here are some common wiring problems and solutions to help CNC operators solve them effectively.
Identifying Wiring Errors and Faults
Wiring errors are among the most common issues affecting CNC routers. They can lead to malfunctions, signal loss, or even damage to components.
- To identify wiring faults, first, inspect all cables for loose connections, frayed wires, or incorrect routing. Miswiring of power and signal cables can cause system instability, while poorly connected terminals can lead to intermittent failures. Check that each wire is properly secured to its corresponding terminal on the controller, motors, and power supply.
- Using a multimeter to measure continuity can help detect broken wires or poor connections. A lack of continuity indicates a broken circuit, requiring wire replacement or reconnection. Additionally, checking for short circuits by testing resistance between power and ground wires ensures that there are no unintended electrical paths that could damage components.
- If a component is not responding, swap it with a known working wire or connector to see if the issue persists. If the problem moves with the swapped component, the fault is likely with the wiring rather than the component itself.
Resolving Motor Stalls or Inconsistent Motion
Stepper and servo motors rely on precise electrical signals to function correctly. When wiring is incorrect, motors may stall, move inconsistently, or vibrate without proper movement.
- Motor stalls are often caused by inadequate power delivery or loose motor wiring. Verify that the power supply provides sufficient voltage and current for the motors, ensuring that motor drivers are correctly configured. If motors receive inadequate power, they may not generate enough torque to move the CNC router smoothly.
- Incorrect motor wiring, such as swapped phase connections, can lead to erratic motion or reversed movement. Cross-check motor driver wiring against the manufacturer’s diagram to ensure proper phase connections. Additionally, ensure that motor signal cables are securely connected to the control board.
- If motors experience sudden jerks or skip steps, electromagnetic interference (EMI) may be disrupting the signal. Shielded cables should be used for motor wiring, and power cables should be routed separately from signal lines to minimize interference.
Resolving Electrical Noise and Interference
Electrical noise can cause unexpected behavior in CNC routers, including false limit switch triggers, erratic motor movement, and inconsistent spindle speed. Interference is often generated by high-power components such as spindle motors and stepper drivers.
- One of the most effective ways to reduce interference is to use shielded cables for all signal and motor wiring. Shielded cables prevent external electrical noise from affecting sensitive signals. Proper grounding of all components also helps dissipate unwanted electrical energy, reducing EMI-related issues.
- Separating power and signal cables is another crucial step. Running high-voltage power lines alongside low-voltage signal wires can induce noise, leading to unpredictable behavior. Cables should be routed in different paths, preferably with at least a few inches of separation.
- Ferrite cores can be installed on signal and power cables to filter out high-frequency noise. These simple components help absorb unwanted EMI, stabilizing CNC router performance.
- If limit switches or sensors are falsely triggering, interference from nearby machinery or fluorescent lighting could be the culprit. Re-routing cables, adding shielding, or adjusting debounce settings in the CNC software can help mitigate false signals.
Dealing with Power Failures or Voltage Drops
A stable power supply is beneficial for the smooth operation of a CNC router. Sudden power failures or voltage drops can cause unexpected shutdowns, incomplete cuts, or even damage to machine components.
- The first step in diagnosing power-related issues is to verify the power input. Ensure that the CNC router is connected to a dedicated circuit that meets its voltage and current requirements. Sharing a power source with other high-power machines can cause fluctuations that impact CNC performance.
- Loose power connections can also lead to intermittent shutdowns. Inspect all power terminals and tighten any loose connections to prevent sudden disconnections. Additionally, check the power supply unit (PSU) for any signs of overheating or capacitor failure, which could indicate an unstable voltage output.
- Voltage drops often occur when using undersized power cables. If the wires supplying power to the CNC router are too thin, they may not deliver sufficient current, leading to inconsistent performance. Upgrading to a thicker gauge power cable can help reduce resistance and prevent voltage loss.
- For areas with unstable electricity, using an uninterruptible power supply (UPS) or a voltage stabilizer can help maintain consistent power delivery. A UPS provides backup power during outages, while a stabilizer regulates voltage fluctuations to protect sensitive electronics.
Troubleshooting wiring issues in a CNC router requires a systematic approach. Proper cable management and routine inspections can prevent many of these issues, ensuring a reliable and efficient CNC router operation.
Maintenance Practices for CNC Router Wiring
Over time, wires can loosen, degrade, or suffer from environmental exposure, leading to potential safety risks and operational disruptions. By following proper maintenance practices, you can minimize downtime, reduce repair costs, and maintain optimal machine efficiency. Here are essential maintenance tips.
Regular Inspection and Cleaning of Circuits and Components
Dirt, dust, and loose connections can cause electrical failures or interfere with machine performance. Regular inspections help detect potential problems early.
- Check for Loose Connections: CNC routers experience vibration, which can loosen terminals over time. Periodically tighten all electrical connections.
- Inspect Wiring for Damage: Look for frayed insulation, exposed wires, or overheating marks, which indicate wear or potential electrical hazards.
- Keep Wires Free from Dust and Debris: Use compressed air or a dry cloth to clean wiring and connections, especially around control panels and motor terminals.
Ensure Proper Ventilation: Keep cooling fans and vents free from dust buildup to prevent overheating.
Replacement of Worn or Damaged Wiring
Old or damaged wiring can lead to erratic machine behavior, electrical shorts, or component failures. Periodic replacement is necessary for safe and efficient operation.
- Identify High-Wear Areas: Cables near moving parts, such as stepper motors or drag chains, are more prone to wear and should be checked frequently.
- Replace Frayed or Brittle Wires: If insulation is cracked or wires are exposed, replace them immediately to prevent electrical hazards.
- Upgrade to Higher-Quality Cables: If experiencing frequent failures, consider using shielded or high-flex cables designed for CNC applications.
- Use Proper Strain Relief: Secure cables near connectors to prevent stress from bending or pulling.
Updating Wiring Diagrams and Documentation
As modifications or repairs are made, keeping wiring diagrams up to date ensures future troubleshooting and upgrades are easier.
- Record Wiring Changes: Any modifications, such as rewiring a motor or upgrading a power supply, should be documented for future reference.
- Label Wires Clearly: Use heat-shrink labels, adhesive tags, or color-coded markings to differentiate power, signal, and ground wires.
- Maintain a Digital and Physical Copy of Wiring Diagrams: Keeping both hard copies and digital backups ensures quick access when troubleshooting.
Regular Calibration and Adjustment of Electrical Systems
Electrical components such as motor drivers, power supplies, and sensors require periodic calibration to maintain accuracy and efficiency.
- Check Stepper and Servo Motor Tuning: Adjust motor driver settings to ensure smooth motion and prevent missed steps.
- Verify Power Supply Voltage and Current: Use a multimeter to confirm stable voltage output to critical components.
- Test Limit Switch and Homing Accuracy: Ensure limit switches trigger properly and that homing sequences return to consistent positions.
- Confirm Spindle Speed Control: If using a VFD-controlled spindle, verify that speed adjustments match programmed values.
Implementing these best maintenance practices ensures long-term stability and reduces downtime, keeping the CNC router running at peak efficiency.
Summarize
Connecting a CNC router properly is beneficial for ensuring smooth operation, precision, and long-term reliability. By following a structured approach, you can avoid common pitfalls and optimize your machine’s performance. Whether you’re a beginner setting up your first CNC router or an experienced user optimizing a professional machine, attention to detail in the connection process will lead to improved safety and a longer machine lifespan. With the right setup, your CNC router will be ready to deliver precision and efficiency for all your cutting, engraving, and machining projects.
If you are looking for a CNC router that is easy to connect, safe to operate, and built to last, AccTek CNC is an excellent choice. With high-quality manufacturing, professional wiring setups, and reliable after-sales support, AccTek CNC ensures that your machine runs smoothly and efficiently for years to come. Whether for woodworking, metalworking, or industrial applications, AccTek CNC routers provide the performance and reliability you need to succeed.
What challenges does CNC router face?
By following best practices, you can ensure stable operation and reduce maintenance efforts. A well-organized wiring setup not only enhances machine performance but also simplifies future upgrades and repairs.