- 10-15 Min Read
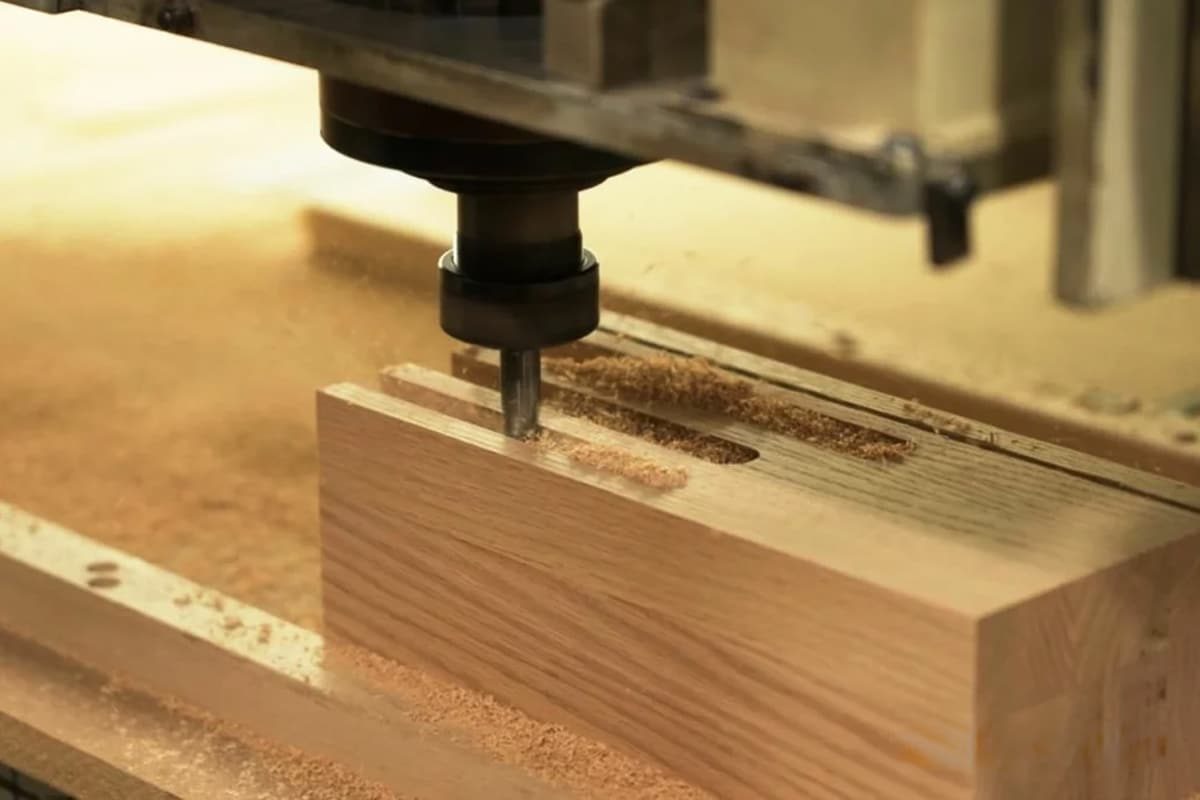
When working with a CNC router, one of the most critical—but often overlooked—choices you’ll make is how many slots, or flutes, your cutting tool should have. The number of flutes directly affects chip removal, surface finish, cutting speed, and tool life. Whether you’re cutting wood, plastic, or metal, selecting the right flute count can dramatically improve machining performance and efficiency.
But how do you know whether to go with a single flute or something with four or more? What works best for soft materials versus hard ones? In this comprehensive guide, we’ll break down everything you need to know about flute count, from how it impacts tool performance to how to choose the right configuration for your specific application. Let’s dive in and make sure you’re using the right tool for the job.
Understanding Flutes
In CNC routing, the terms flutes and grooves are often used interchangeably. A flute is a channel cut into the body of a CNC router tool, and it serves two main purposes: it acts as a cutting edge and provides a pathway for chip evacuation.
What Are Flutes?
Flutes are the spiral or straight grooves along the cutting tool. Each flute contains a sharp cutting edge that slices into the material as the tool spins. The number of flutes on a bit determines how many cutting edges are engaged during operation. Here is the functions of flutes:
- Cutting: Each flute helps remove a portion of material with every rotation.
- Chip Removal: Flutes provide space for the chips (cut material) to exit the cut area.
- Cooling: By efficiently removing chips, flutes help reduce heat buildup at the cutting surface.
- Surface Finish: More flutes typically mean more contact points with the material, which can improve surface smoothness.
How Flutes Affect Tool Performance
The number of flutes on a CNC router tool significantly affects how it performs during cutting.
- Material Removal Rate (MRR): The material removal rate refers to how quickly the tool can remove material during cutting. It’s influenced by spindle speed, feed rate, depth of cut, and the number of grooves. A higher flute count means more cutting edges are in contact with the material, allowing more material to be removed per revolution, and increasing the MRR.
- Chip Evacuation: As the tool cuts, it produces chips that must be cleared away to prevent clogging and maintain cutting efficiency. The space between flutes acts as a channel for chip evacuation. Fewer flutes create wider chip channels, allowing for better chip removal. More flutes reduce chip space, increasing the risk of buildup and tool wear.
- Thermal Management: Cutting generates heat, and poor heat dissipation can damage both the tool and the material. Chip removal plays a major role in heat control, as chips carry away a portion of the heat generated during cutting. Efficient chip evacuation means better cooling of the cutting area. Tools with fewer flutes manage heat better because they clear chips more effectively. Tools with more flutes may trap heat, increasing the risk of burning, melting, or premature tool failure.
Flute count is more than a design detail, it directly impacts how efficiently, cleanly, and safely your CNC router performs. Balancing material removal rate, chip evacuation, and thermal control is key to choosing the right tool for your specific material and cutting needs.
Common Flute Configurations
Choosing the right number of flutes is beneficial for optimizing cutting performance. Each configuration offers unique benefits and trade-offs depending on the material being cut and the machining goal. Below are the most common flute configurations used in CNC routing:
Single-Flute Tools
A single-flute tool has only one cutting edge and the largest flute space. It’s designed for maximum chip clearance and is ideal for high-speed machining of soft materials.
Advantages
- Superior chip evacuation due to wide flute spacing.
- Minimized heat buildup, as chips are removed quickly.
- Excellent for high-speed cutting, especially on lightweight machines or with lower horsepower spindles.
Limitations
- Lower surface finish quality compared to multi-flute tools.
- Not ideal for very hard materials due to limited cutting contact.
Best Applications
- Soft plastics (e.g., acrylic, HDPE).
- Aluminum and other soft non-ferrous metals.
- Foam and softwood.
Two-Flute Tools
The most versatile and widely used flute configuration. With two cutting edges, this tool balances chip removal with cutting speed and finish quality.
Advantages
- Good chip evacuation with decent flute space.
- Improved surface finish over single-flute tools.
- Balanced cutting forces for stability.
Limitations
- Moderate MRR (Material Removal Rate) compared to tools with more flutes.
- Still not ideal for very fine finishing work.
Best Applications
- Softwood and hardwood.
- MDF and plywood.
- Plastics and soft aluminum.
Three-Flute Tools
Three-flute tools provide an excellent middle ground between chip clearance and surface finish. They have a higher material removal rate than two-flute tools while still managing chip evacuation reasonably well.
Advantages
- Higher MRR thanks to more cutting edges.
- Smoother surface finish than two-flute tools.
- Good tool strength and rigidity.
Limitations
- Reduced chip clearance space compared to two-flute tools.
- May require more spindle power and better chip control systems.
Best Applications
- Hardwoods.
- Aluminum (with appropriate coating and cooling).
- Fiberglass and composite panels.
Four-Flute and Higher Tools
These tools are designed for high-speed cutting and finishing. With four or more flutes, they offer the most cutting edges and contact points, resulting in superior finishes.
Advantages
- Excellent surface finish due to constant tool engagement.
- High tool strength and rigidity, ideal for precise work.
- Increased productivity in high-feed operations.
Limitations
- Poor chip evacuation is not ideal for materials that produce large or sticky chips.
- Higher risk of tool clogging or heat buildup if used improperly.
- Often requires high spindle power and/or lubrication.
Best Applications
- Hardwoods and dense engineered wood.
- Dry machining of metals with light chip loads.
- Finish passes in composite materials.
Selecting the right flute configuration depends on your material type, desired finish, cutting speed, and the capabilities of your CNC router. For soft materials and fast cuts, fewer flutes provide better chip control and cooling. For harder materials or finishing tasks, higher flute counts deliver a smoother result but require careful chip management and machine capability.
Factors to Consider When Choosing Flute Count
Selecting the appropriate number of flutes for your CNC router tool isn’t just about preference—it directly impacts cutting performance, efficiency, and final results. Here are the most important factors to consider when determining the ideal flute count:
Material Type
Different materials behave differently during cutting. The type of material you’re working with is one of the most important considerations:
- Soft Materials (e.g., plastic, softwood, aluminum): These produce larger or sticky chips, which can clog tools. Fewer flutes (1 or 2) are ideal because they provide more space for chip evacuation.
- Hard Materials (e.g., hardwood, composites, steel): These produce smaller chips and require more cutting edges for clean finishes. More flutes (3 or more) can be used to improve surface quality and tool strength.
Chip Evacuation Needs
- Chip buildup can damage both the tool and the workpiece, especially in enclosed or deep cuts. Flute count determines how easily chips can escape:
- Fewer flutes = wider chip channels = better chip evacuation.
- More flutes = narrower chip channels = higher risk of clogging.
If your operation produces large chips or requires deep pocketing, prioritize flute configurations that maximize chip clearance.
Surface Finish Requirements
The more cutting edges a tool has, the smoother the finish it can leave:
- Higher flute count = more cutting contact = smoother finish.
- For roughing, 1–2 flutes may be sufficient.
- For finishing, 3–4 flutes or more are typically used to achieve a finer surface.
Cutting Speed and Feed Rate
Flute count affects how fast you can move the tool while maintaining a clean cut:
- More flutes = more cuts per revolution = potentially faster feed rates.
- However, higher speeds must be balanced with chip clearance to avoid overheating or clogging.
Your spindle power and machine rigidity also influence how well a multi-flute tool can perform at higher speeds.
Tool Rigidity and Strength
More flutes generally mean more core material and a stiffer tool:
- Tools with 3 or more flutes are stronger and less prone to deflection, which helps when cutting hard or dense materials.
- Single- or two-flute tools may flex more but are better for lighter cuts and softer materials.
Heat Management
- Efficient chip evacuation helps control heat buildup, which can degrade tool life and damage heat-sensitive materials:
- Fewer flutes = better cooling, since chips carry heat away from the cut.
- More flutes = higher heat retention, which may require slower speeds or coolant/lubrication.
Type of Operation (Roughing vs. Finishing)
- Roughing: Use fewer flutes (1–2) for aggressive material removal and easier chip clearance.
- Finishing: Use more flutes (3–4+) for a smoother final surface and finer detail.
There’s no one-size-fits-all flute count. The right choice depends on your material, application, machine capability, and desired result. By carefully evaluating the factors above, you can select the optimal tool that maximizes performance, efficiency, and quality in your CNC routing operations.
Advanced Flute Design and Coating
While flute count plays a major role in tool performance, flute geometry and surface coating are equally important, especially in demanding CNC routing applications. Advances in design and technology have made it possible to enhance cutting efficiency, tool life, and material compatibility.
Advanced Flute Design
Modern CNC router tools go beyond just the number of flutes. The shape, angle, and direction of the flutes can significantly influence performance.
- Helix Angle: This is the angle at which the flute spirals around the tool. A higher helix angle provides smoother cutting and better chip evacuation, while a lower helix angle offers more strength and is better for hard materials.
- Variable Flute Geometry: Some high-performance tools feature variable flute spacing to reduce vibration and chatter during cutting. This leads to a cleaner surface finish and extended tool life.
- Center-Cutting vs. Non-Center-Cutting: Tools with center-cutting flutes can plunge directly into materials, which is useful for pocketing operations. Non-center-cutting tools require ramp-in paths.
- Upcut vs. Downcut Flutes: Upcut flutes pull chips upward, ideal for deep cuts and better chip removal. Downcut flutes push chips down, great for top-surface finish in wood and laminates. Compression bits combine both for clean top and bottom edges—often used in plywood and composites.
Tool Coatings
- Coatings are applied to cutting tools to enhance durability, reduce friction, and improve heat resistance. The right coating extends tool life and allows for faster cutting.
- TiN (Titanium Nitride): A general-purpose gold-colored coating that increases hardness and wear resistance. Suitable for cutting wood and some plastics.
- TiCN (Titanium Carbonitride): A harder, slicker coating than TiN, often used for abrasive materials like MDF or hardwood.
- TiAlN / AlTiN (Titanium Aluminum Nitride): These coatings provide excellent heat resistance, making them ideal for high-speed cutting and metal applications like aluminum or steel.
- DLC (Diamond-Like Carbon): Extremely low-friction and wear-resistant, DLC coatings are perfect for non-ferrous metals and sticky plastics like PVC or UHMW.
- Uncoated Tools: Often used for soft materials like foam or softwood, where heat and wear are less of a concern.
Advanced flute design and high-performance coatings can take your CNC machining to the next level. Whether you’re seeking longer tool life, cleaner finishes, or better performance in tough materials, pairing the right flute geometry with the appropriate coating will ensure you get the most out of your CNC router tools.
Flute Count and Toolpath Strategies
Choosing the right flute count doesn’t just affect how your tool cuts—it also influences how you plan your toolpaths. Here is the relationship between the two:
Feed Rate and Spindle Speed
Flute count directly affects how much material is removed per revolution and how fast the tool can be fed into the material.
- More flutes: More cutting edges per rotation, allowing higher feed rates without overloading any single edge. However, you must ensure chips are still small enough to be evacuated effectively, especially with higher flute counts.
- Toolpath tip: Use higher feed rates with multi-flute tools when cutting hard materials, but make sure to adjust spindle speed to maintain proper chip load.
Plunge and Pocketing Strategies
When plunging or cutting pockets, flute count influences how well the tool can evacuate chips during vertical or confined movements.
- Fewer flutes (1–2) are ideal for plunging or deep pockets, where chip buildup is a risk. More flutes may require a ramp-in strategy or helical entry to avoid heat buildup and tool stress.
- Toolpath tip: Avoid direct plunging with high-flute-count tools, use gentle entry motions like ramps or spirals.
Step-Over and Step-Down Depths
The amount of material removed per pass (step-over and step-down) should match your flute configuration:
- Low flute count tools can handle deeper cuts per pass due to better chip clearance. Higher flute count tools should use shallower passes to reduce heat and allow for smoother finishes.
- Toolpath tip: For roughing, use aggressive step-downs with 1-2 flutes. For finishing, use smaller step-overs with 3-4+ flutes.
Tool Engagement and Chatter Control
Tools with variable flute spacing or higher flute counts can help reduce vibrations (chatter) during cutting, especially on intricate or long toolpaths.
- Higher flute count tools distribute cutting forces more evenly, ideal for tight curves and detailed contours. Variable flute designs further minimize harmonics, which improves surface quality.
- Toolpath tip: When cutting complex shapes or tight contours, multi-flute or variable-flute tools can improve stability and finish.
Material Removal Efficiency
Toolpaths designed for high-efficiency roughing (like adaptive clearing or trochoidal paths) can be optimized based on flute count:
- Low-flute tools (1–2) are better suited for adaptive clearing, as they handle large chip volumes well. High-flute tools (3–4+) are better for high-speed finishing or contour passes.
- Toolpath tip: Match the flute count to the type of path—roughing paths need chip evacuation, finishing paths need edge contact and control.
Effective CNC machining isn’t just about the tool you choose, it’s also about how you use it. Aligning your toolpath strategy with your tool’s flute count ensures you get the best combination of speed, accuracy, chip control, and surface finish. By understanding this interaction, you can extend tool life, avoid costly errors, and produce cleaner, more efficient results.
Maintenance and Tool Life Optimization
Proper maintenance is beneficial to prolong the life of your CNC router tools and ensure consistent cutting quality. Flute geometry, cutting conditions, and material type all influence wear rates, but with the right practices, you can significantly extend tool life and maintain high performance.
Regular Inspection and Cleaning
Over time, material buildup, especially resin or aluminum chips can clog the flutes, reduce cutting efficiency, and increase heat. Here are the best practices:
- Inspect tools before and after use for wear, chips, or buildup.
- Clean flutes with a soft brush or compressed air.
- Use a dedicated cleaner or solvent for resin or plastic buildup (avoid corrosive chemicals).
Proper Chip Evacuation
Clogged flutes increase friction and heat, causing premature wear or even tool breakage. Here are the best practices:
- Use dust collection or air blast systems to help remove chips.
- Avoid re-cutting chips by adjusting toolpaths and clearing the cutting area regularly.
- Choose lower flute counts for soft or gummy materials to improve chip flow.
Use the Right Cutting Parameters
Running a tool too fast or too slow can degrade cutting edges quickly. Here are the best practices:
- Adjust feed rate and spindle speed to maintain optimal chip load for your flute count.
- Follow the manufacturer’s recommended settings based on material and tool type.
- Monitor tool deflection and vibrations, chatter can signal improper speeds or a worn tool.
Rotate and Replace Tools Strategically
Even high-quality tools wear over time, especially with frequent use or on abrasive materials like MDF or composites. Here are the best practices:
- Keep a log of tool usage (especially in production settings).
- Rotate between identical tools to distribute wear.
- Replace tools at the first sign of dulling or burning, pushing a dull tool can damage both the workpiece and spindle.
Use Coated Tools When Needed
Tool coatings like TiN, TiAlN, or DLC can reduce friction and heat, improving tool life dramatically. Here are the best practices:
- Use coated tools for tough materials like hardwood, aluminum, or composites.
- Avoid using coated tools on extremely soft materials where coatings may be unnecessary.
Store Tools Properly
Poor storage can damage cutting edges and cause rust or oxidation. Here are the best practices:
- Store tools in protective cases or foam-lined drawers.
- Avoid tool-to-tool contact, especially with sharp flutes.
- Keep tools dry and away from moisture or corrosive environments.
Maintaining your CNC router tools doesn’t just protect your investment, it ensures safer, cleaner, and more efficient machining. With regular inspection, the right cutting parameters, and attention to chip evacuation, you can maximize flute performance and significantly extend tool life across a wide range of materials and applications.
Summarize
Choosing the right number of flutes in a CNC router tool is a key factor that directly impacts cutting quality, efficiency, and tool life. Each flute configuration serves a specific purpose, by considering key factors such as material type, cutting speed, surface requirements, and toolpath strategy, you can choose the optimal flute count for your specific application. In the end, always test, adjust, and refine based on real-world results, because the right tool makes all the difference.
If you’re looking for a reliable CNC router to pair with the right cutting tools, AccTek CNC is a good choice. As a professional CNC router manufacturer based in China, AccTek is known for producing high-quality, precision-driven machines. Our CNC routers are designed with versatility and performance in mind, making them ideal for both beginners and experienced operators who want to get the most out of their cutting tools.
CNC routers are versatile tools that can be adapted to different applications within these industries, making them valuable for both prototyping and production purposes. The specific capabilities and features of a CNC router may vary, so choosing the right machine for a particular application is important.