- 10-15 Min Read
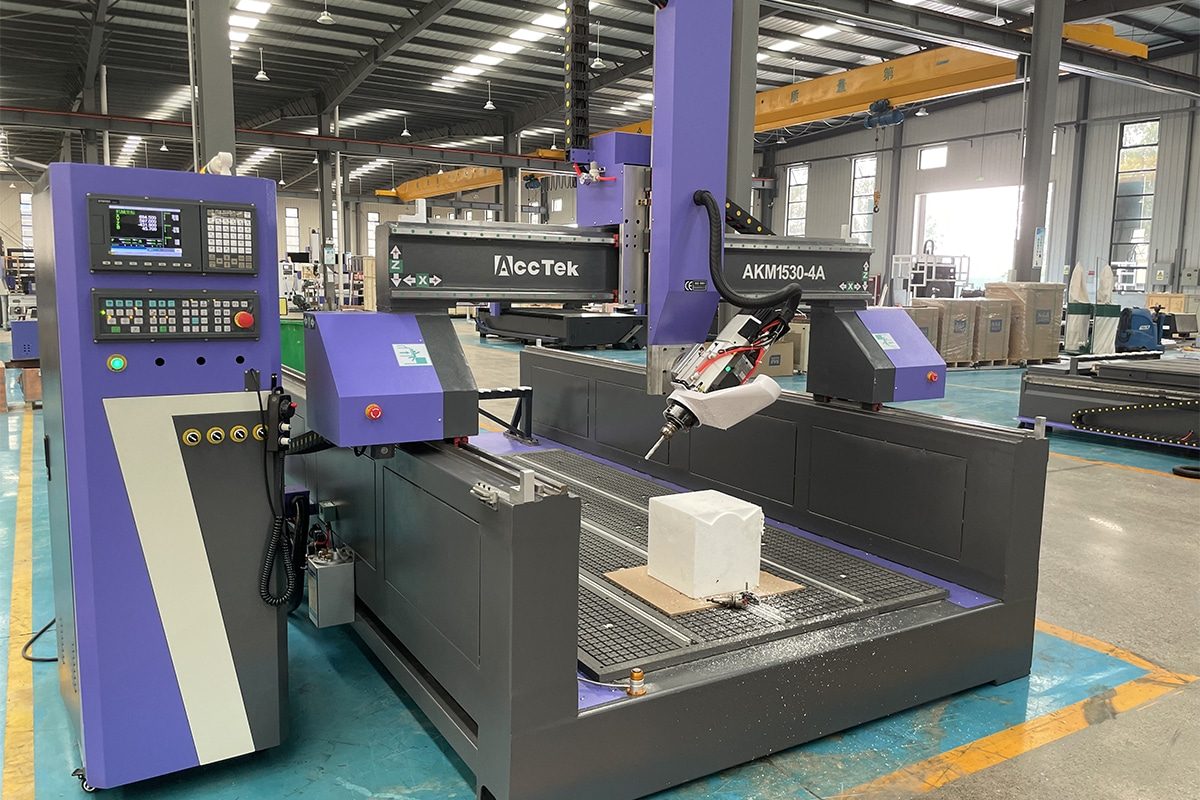
CNC routers are powerful tools used in woodworking, metalworking, and plastic fabrication, offering precision and efficiency in cutting, carving, and engraving. However, achieving the best results depends largely on selecting the right router bit. The router bit determines the quality of the cut, the speed of the operation, and the compatibility with different materials.
With a wide variety of router bits available, each designed for specific applications, choosing the right one can be challenging. This guide will help you understand the different types of router bits, key selection criteria, and best practices for maximizing tool longevity. Whether you are cutting wood, plastic, or metal, making the right choice will enhance precision, extend tool life, and improve overall CNC routing performance.
Understanding Router Bits
Router bits are the cutting tools used in CNC routers to shape, carve, and cut various materials. They come in a variety of shapes, sizes, and materials, each designed for specific applications. Understanding the key components and types of router bits is beneficial for selecting the most suitable option for your CNC router.
Components of a Router Bit
Every router bit consists of several key parts that determine its performance:
- Shank: The cylindrical part of the bit that fits into the router’s collet. Common sizes include 1/4-inch, 1/2-inch, and metric equivalents.
- Cutting Edge: The sharp portion of the bit responsible for material removal. The shape and design of the cutting edge impact the type of cut produced.
- Flutes: The grooves that run along the cutting edge, allowing chips to be removed from the cut. The number and type of flutes affect the cutting speed, finish quality, and material evacuation.
- Coating: Some bits have special coatings (such as TiAlN or DLC) to improve heat resistance, reduce friction, and enhance durability.
Types of Router Bits
Different types of router bits are used for various CNC applications. Choosing the right bit depends on the material being cut and the desired cutting result.
- Straight Bits: The most commonly used router bits, featuring a simple cylindrical cutting edge that moves vertically through the material. They are ideal for cutting slots, dados, rabbets, and pockets in wood, plastic, and soft metals. Due to their straightforward design, they provide clean, sharp edges and are widely used in both hand-held and CNC routing applications.
- Spiral Bits: They have a helical cutting edge that improves chip evacuation and cutting efficiency. They come in three variations: up-cut, down-cut, and compression. Up-cut spiral bits pull chips upward, providing fast material removal but potentially causing surface tear-out. Down-cut spiral bits push chips downward, creating a cleaner top surface but requiring better chip management. Compression bits combine both features to reduce chipping on both sides, making them ideal for laminated materials.
- Ball Nose Bits: They have a rounded tip, making them essential for 3D carving, contouring, and detailed engraving. They are commonly used in sign-making, decorative cutting, and sculptural projects where smooth, rounded cuts are needed. These bits help create intricate relief designs, reducing the need for extensive sanding and finishing.
- V-Bits: V-bits have an angled cutting edge that tapers to a sharp point, making them perfect for engraving, sign-making, and chamfering. Available in different angles, they produce deep, precise cuts for lettering, inlays, and decorative designs. V-bits are widely used in CNC applications for achieving sharp, clean details in engraving projects.
- Cove Bits: Feature a concave cutting edge designed to create rounded grooves and decorative molding details. Commonly used in furniture making and cabinetry, they add smooth, curved profiles to wood edges. Cove bits are excellent for adding an elegant touch to doors, frames, and decorative trims.
- Round Nose Bits: Also known as core box bits, have a half-circle cutting profile, making them ideal for cutting rounded grooves and flutes. These bits are often used for decorative accents, carving, and engraving projects where a smooth, rounded groove is required. They are especially popular in CNC woodworking for creating ornamental details in furniture and signs.
- Chamfer Bits: Create beveled edges, making them useful for decorative edges, miter joints, and paneling work. They cut at an angle, producing a clean, sharp transition between surfaces. These bits are frequently used in woodworking and cabinetry to enhance the aesthetic appeal of furniture and to prepare edges for seamless joint connections.
How Router Bits Affect Cutting Performance
The type of router bit directly impacts:
- Cut Quality: The right bit minimizes tear-out, chatter, and rough edges.
- Speed and Efficiency: Some bits remove material faster than others, optimizing workflow.
- Material Compatibility: Certain bits work best for specific materials like wood, plastic, aluminum, or composites.
By understanding the structure and function of router bits, CNC users can make informed decisions to optimize cutting performance and achieve precise results.
Key Factors to Consider When Choosing a Router Bit
Selecting the right router bit is beneficial for achieving high-quality cuts, prolonging tool life, and ensuring efficient CNC routing. Below are the key factors to consider when choosing a router bit for your specific application.
Material Compatibility
Different materials require different types of router bits to ensure optimal performance and prevent damage.
- Wood (Softwood & Hardwood): Carbide-tipped or solid carbide bits work best for durability and sharpness.
- Plastics & Acrylics: Single-flute or spiral bits minimize melting and chipping.
- Metals (Aluminum, Brass, etc.): Single or double-flute carbide bits with high-speed capabilities are recommended for smooth cuts.
- Composites (MDF, Plywood, Laminates): Compression bits prevent chipping on both the top and bottom surfaces.
Number of Flutes
The number of flutes affects chip removal, cutting speed, and finish quality.
- Single-Flute Bits: Best for soft materials (plastics, aluminum) as they allow for fast chip removal.
- Two-Flute Bits: Provide a balance between speed and smoothness, commonly used for wood and composites.
- Multi-Flute Bits: Deliver the smoothest cuts but require slower feed rates, ideal for fine-detail work.
Cutting Edge and Coating
The cutting-edge material and coating determine the bit’s durability and performance.
- High-Speed Steel (HSS): This is Affordable but wears out faster, suitable for softwood.
- Carbide-Tipped: Longer lifespan and sharper cuts, suitable for hardwood, MDF, and laminates.
- Solid Carbide: Most durable, ideal for demanding CNC applications.
- Coatings (TiAlN, DLC, etc.): Enhance heat resistance and tool longevity, useful for high-speed operations.
Bit Diameter and Cutting Length
The size of the router bit affects the precision, depth, and efficiency of cuts.
- Smaller Diameter (1/8″, 1/4″): Provides detailed and intricate cuts.
- Larger Diameter (1/2″, 3/4″): Covers more surface area and improves stability.
- Cutting Length: Should be appropriate for the material thickness to avoid excessive strain on the bit.
Feed Rate and Spindle Speed Compatibility
Each router bit has an optimal feed rate and spindle speed for best performance.
- High feed rate and slow spindle speed: This reduces heat buildup but may cause rough cuts.
- Low feed rate and high spindle speed: Produces smooth cuts but increases wear on the bit.
- Matching bit design with proper machine settings: Prevents overheating, chatter, and tool breakage.
Bit Shank Size
The shank diameter determines stability and compatibility with the CNC router.
- 1/4-inch Shank: Common in small CNC routers, provides flexibility but may vibrate at high speeds.
- 1/2-inch Shank: Offers greater stability, reduces deflection, and extends tool life.
- Collet Compatibility: Ensure your router can accommodate the shank size for secure fitting.
Cost vs. Quality
Investing in high-quality bits can save money in the long run by reducing tool replacement frequency.
- Budget Bits: They may wear out quickly, leading to rough cuts and tool breakage.
- Premium Carbide Bits: These offer extended durability and precision, making them cost-effective over time.
Selecting the right router bit involves evaluating the material, bit type, flute design, coating, size, and machine compatibility. Understanding these factors ensures better cutting performance, improved tool longevity, and superior CNC results. Always consider the specific requirements of your project to achieve the best outcomes.
Application-Specific Considerations
Selecting the right router bit depends on the specific application, as different tasks require different cutting geometries, materials, and features. Below are key considerations for selecting router bits based on specific applications:
Edge Profiling
Edge profiling involves shaping the edges of a workpiece to add decorative or functional details. The choice of router bit depends on the desired edge finish and the material being worked on. Here are the recommended router bits:
- Chamfer Bits: These create clean, angled edges and are useful for beveled designs.
- Cove Bits: Produce concave curves for decorative moldings.
- Round Over Bits: Soften sharp edges with a rounded profile.
- Ogee Bits: Used for elegant, S-shaped edge details in furniture and cabinetry.
- Considerations: A gradual increase in depth during multiple passes prevents burning and excessive wear on the bit.
Joinery
Precision joinery requires router bits that create strong and seamless connections between workpieces. The type of joint being used determines the ideal router bit selection. Here are the recommended router bits:
- Dovetail Bits: Essential for strong interlocking joints, often used in cabinetry and drawer construction.
- Mortise & Tenon Bits: These create slots and corresponding tenons for frame-and-panel joinery.
- Straight Bits: Used for basic groove and dado joints.
- Flush Trim Bits: Help ensure perfect alignment when working with templates.
- Considerations: The bit size must match the thickness of the material to ensure a secure joint.
Carving and Marquetry Work
Carving and marquetry work involve intricate detailing and fine decorative elements, requiring specialized router bits that allow for precision cutting and engraving. Here are the recommended router bits:
- V-Bits: Ideal for engraving fine details, lettering, and decorative line work.
- Ball Nose Bits: Used for creating smooth curves and detailed relief carving.
- Round Nose Bits: Suitable for cutting deep, rounded grooves and decorative accents.
- Tapered Ball Nose Bits: These provide finer details in deep carvings while maintaining rigidity.
- Considerations: Slower feed rates and moderate spindle speeds help maintain accuracy in intricate designs.
3D Engraving
3D engraving requires router bits that can handle complex depth variations while maintaining smooth transitions and fine detailing. These bits are used to carve detailed reliefs, sculptures, and topographical designs. Here are the recommended router bits:
- Ball Nose Bits: Ideal for smooth, curved engravings in 3D relief work.
- Tapered Ball Nose Bits: These offer enhanced control and precision for deep, intricate engravings.
- V-Bits: Used for achieving fine details and shading effects in 3D designs.
- Considerations: Slower speeds and proper dust extraction help achieve a clean, polished surface.
Choosing the right router bit based on application-specific needs ensures precision, efficiency, and quality in CNC routing. Whether for decorative edging, joinery, intricate carving, or 3D engraving, selecting the correct bit type, material, and cutting strategy enhances the final results and extends tool longevity.
Get Professional Advice
Selecting the right router bit is not just about understanding bit types and applications—it’s also essential to consult manufacturer recommendations and seek expert advice to ensure the best performance and longevity of your CNC router.
Follow Manufacturer Recommendations
Each CNC router and router bit manufacturer provides specific guidelines regarding:
- Material Compatibility: Manufacturers specify which bits work best for wood, metal, plastic, or composite materials.
- Operating Parameters: Recommended feed rates, spindle speeds, and depth of cut ensure optimal cutting performance.
- Bit Coatings & Durability: Different coatings and materials (e.g., carbide vs. HSS) are suited for various applications.
- Machine Compatibility: Certain bits work best with specific CNC routers, depending on their collet size, motor power, and cutting speeds.
- Always check the manufacturer’s specifications to avoid using an unsuitable bit that may result in poor cutting quality, excessive wear, or even damage to the router or workpiece.
Seek Professional Advice
If you’re unsure which router bit to choose for a specific project, seeking expert advice can save time and improve results.
- Consult CNC Equipment Suppliers: Many CNC router manufacturers offer customer support to help select the best bit for a particular machine and material.
- Work with Experienced CNC Operators: Learning from experienced users can provide practical insights into bit selection, machine setup, and troubleshooting.
- Join CNC Communities & Forums: Engaging in discussions with CNC professionals can help refine your bit selection strategy and improve cutting efficiency.
Choosing the right router bit goes beyond understanding bit types, it involves following manufacturer guidelines, staying informed about new advancements, and seeking professional advice. By doing so, CNC users can ensure precise cutting, longer tool life, and optimized machine performance for every application.
Testing and Experimentation: Optimizing Your Router Bit Selection
Choosing the right router bit for a CNC router is not just about theory—it requires practical testing and experimentation to achieve the best results. Factors like material properties, machine settings, and cutting conditions can all affect performance, so router bit selection needs to be fine-tuned through real-world testing.
Running Test Cuts
Before committing to a full production run, it’s best to conduct test cuts on a sample piece of material. This allows you to evaluate:
- Cut Quality: Check for smooth edges, minimal tear-out, and clean finishes.
- Chip Evacuation: Ensure proper flute design and feed rates for efficient chip removal.
- Heat Generation: Observe whether the material burns or melts, indicating improper speed settings.
Adjusting Feed Rate and Spindle Speed
Optimal cutting performance depends on balancing the feed rate and spindle speed:
- Too slow a feed rate: This may cause excessive friction, burning, and premature bit wear.
- Too fast a feed rate: This can lead to rough cuts, tool chatter, and breakage.
- Correct spindle speed: This should match the material and bit type to prevent overheating and ensure smooth cutting.
Evaluating Bit Performance on Different Materials
A single router bit may behave differently across various materials. Testing ensures:
- The right bit geometry is used for each material type (e.g., up-cut vs. down-cut for wood, single-flute for plastics).
- The cut depth and pass strategy are adjusted to avoid tool strain.
- The finish quality meets expectations before moving to production.
Experimenting with Different Bit Coatings and Designs
Testing bits with different coatings (e.g., TiAlN for heat resistance, DLC for durability) can help determine the best choice for longevity and efficiency. Likewise, experimenting with different flute designs (single, double, multi-flute) can optimize chip removal and surface finish.
Testing and experimentation are key to optimizing router bit selection for each specific CNC project. Running test cuts, adjusting settings, and evaluating bit performance across materials will help you maximize efficiency, extend tool life, and achieve consistently high-quality results. Taking the time to fine-tune your router bit selection ensures better productivity, cost savings, and superior craftsmanship in every CNC operation.
Router Bit Maintenance and Longevity
Proper maintenance of router bits is beneficial for ensuring their longevity, maintaining cutting precision, and preventing damage to both the tool and the workpiece. Regular care extends the life of the bit, enhances cutting performance, and reduces operational costs. Below are key maintenance practices to keep router bits in optimal condition.
Regular Cleaning
Over time, router bits accumulate dust, resin, and adhesive buildup, which can reduce cutting efficiency and cause overheating. Here are the best Cleaning Practices:
- Use a router bit cleaner or a mild degreaser to remove built-up residue.
- A soft-bristle brush (such as a toothbrush) helps clean the flutes and cutting edges.
- For stubborn debris, soaking the bit in a commercial cleaning solution for a few minutes can help loosen the buildup.
- Dry the bit thoroughly after cleaning to prevent rust.
Proper Storage
Improper storage can lead to dulling, chipping, or corrosion of the cutting edges. Here are the storage tips:
- Keep router bits in a dedicated case or rack to prevent them from colliding with other tools.
- Store them in a dry environment to avoid rust, especially if working in humid conditions.
- Use protective caps on sharp edges to prevent accidental damage when handling.
Inspect for Wear and Damage
Before and after each use, inspect router bits for signs of wear or damage. Items to be checked include:
- Dull cutting edges: If a bit is struggling to cut cleanly or is burning the material, it may need sharpening or replacement.
- Chipped or broken flutes: Even small chips can lead to poor cutting results and rough edges on the workpiece.
- Uneven wear: Excessive wear on one side of the bit may indicate improper feed rates or machine misalignment.
Sharpening Router Bits
A dull router bit leads to rough cuts, increased heat, and excessive strain on the CNC router. Here are the sharpening tips:
- Carbide-tipped bits can be professionally sharpened using a diamond wheel for best results.
- HSS (High-Speed Steel) bits can be manually sharpened with a fine grinding stone.
- Avoid over-sharpening, as removing too much material can change the bit’s cutting geometry and reduce effectiveness.
Avoid Overheating and Excessive Stress
Excessive heat is one of the leading causes of premature router bit failure. Here are the prevention strategies:
- Use sharp bits to reduce resistance and heat generation.
- Adjust the depth of the cut to avoid overloading the bit in a single pass.
- Apply coolants or air blowers when cutting metals to prevent overheating.
Replace Worn-Out Bits Promptly
Even with proper maintenance, router bits eventually wear out and need replacement. When to Replace a Router Bit:
- If sharpening no longer restores cutting performance.
- If the bit has visible cracks, chips, or deformities.
- If the bit is causing excessive tear-out, burning, or rough edges despite proper settings.
Maintaining router bits through regular cleaning, proper storage, periodic inspection, sharpening, and correct usage extends their lifespan and ensures optimal cutting performance. By following these best practices, CNC users can achieve cleaner cuts, improve efficiency, and reduce tool replacement costs over time.
Summarize
Choosing the right router drill bit is a crucial step in achieving precision, efficiency, and durability in CNC routing. By understanding the key factors to consider and seeking expert advice, CNC operators can select the most suitable bit for their specific project needs. Selecting a bit is only the first step, testing and optimizing your router bit choice is equally important to ensure the best performance. Prioritizing quality and continuous optimization, you can enhance your CNC routing process and achieve consistently superior results in every project. Continue reading “How to Prevent CNC Router Bit Damage?” for tips on keeping your router bit in top shape.
AccTek CNC is a professional CNC router manufacturer in China, committed to delivering high-performance CNC solutions for businesses and professionals worldwide. With their high-quality CNC routers and a commitment to innovation, customer support, and durable tooling solutions, AccTek CNC is the trusted choice for businesses looking to enhance productivity and precision in CNC machining.