- 8-12 Min Read
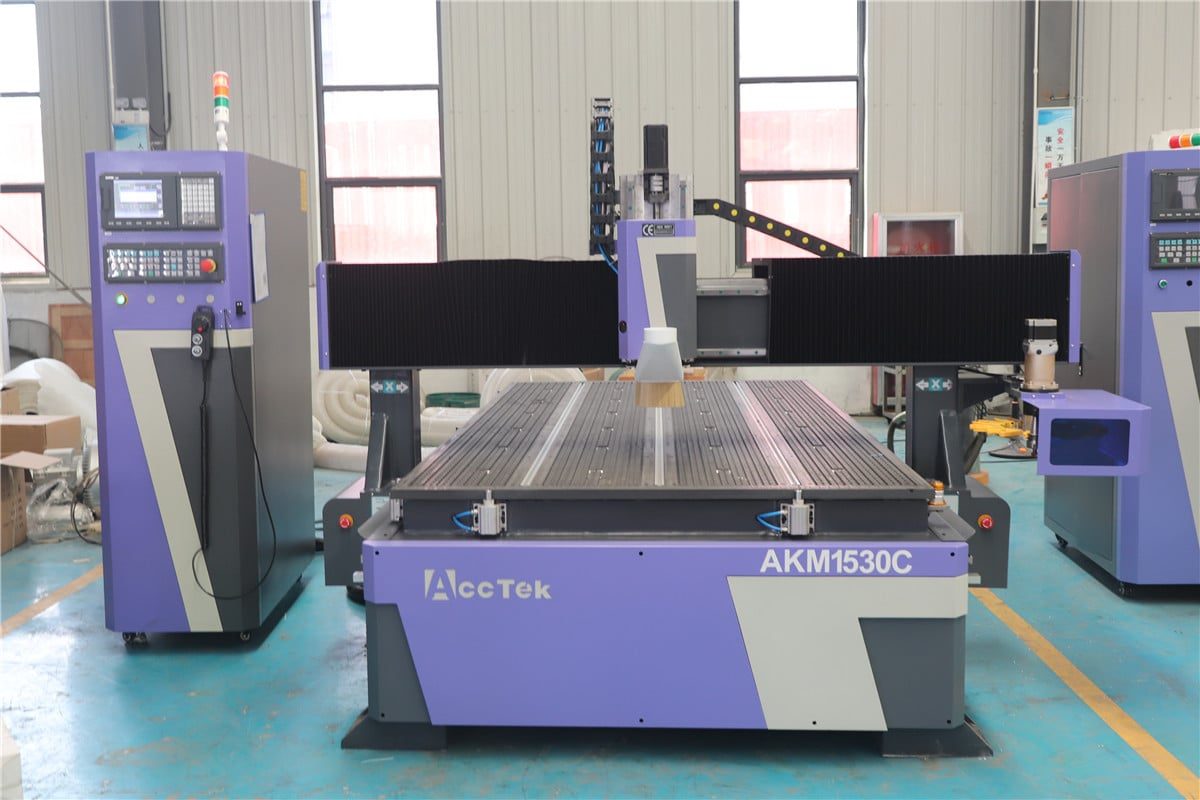
Selecting the right CNC router is a critical step for manufacturers aiming to optimize production processes and achieve their desired output efficiently. With the wide range of CNC routers available, each designed to handle varying materials, workloads, and complexities, making the right choice can feel overwhelming. An oversized CNC router may lead to underutilization, driving up costs without delivering proportional benefits. Conversely, an undersized machine can result in overcapacity, creating bottlenecks and hampering your ability to meet demand.
Choosing the right CNC router for your production needs can significantly improve the efficiency, cost-effectiveness, and scalability of your operations. This article provides a comprehensive guide to help you choose a CNC router that fits your production requirements while leaving room for flexibility and growth. By evaluating production requirements and considering factors that influence capacity, we will explore how to make an informed decision that maximizes efficiency and avoids the costly consequences of mismatched equipment.
Understanding CNC router production capabilities
The production capacity of a CNC router refers to the maximum output it can achieve within a specified timeframe, based on its design, specifications, and operational conditions. It encompasses factors such as the machine’s cutting speed, spindle power, material compatibility, and automation level. Here, let us understand more about capacity and demand.
The Relationship Between Production Capacity and Manufacturing Efficiency
The production capacity of a CNC router acts as a bridge between the machine’s performance and the operational requirements, ensuring that workflows are optimized for maximum output with minimal waste. Here is the relationship between the two:
- Precise Matching: When the production capacity of a CNC router is accurately matched to the manufacturing requirements, the workflow operates at peak efficiency. A machine with the right capacity ensures that materials are processed at the desired speed and precision without delays or idle time.
- Underutilization: Underutilization occurs when a CNC router’s production capacity exceeds the actual manufacturing needs. While it may provide room for future scalability, underutilization leads to inefficiencies in the short term.
- Overcapacity: Overcapacity arises when a CNC router’s production capacity is insufficient to meet manufacturing demands. This mismatch leads to production delays, bottlenecks, and increased strain on the machine, as it may need to run at full capacity or beyond for extended periods.
In essence, aligning the production capacity of a CNC router with manufacturing requirements is key to achieving operational efficiency. It ensures that the machine contributes its maximum potential to the production process without incurring unnecessary costs or delays, ultimately boosting the overall effectiveness of the manufacturing system.
Challenges of Underutilization and Overcapacity
Selecting a CNC router with the wrong capacity can lead to significant operational inefficiencies. This scenario can lead to a range of operational challenges:
Underutilization
- Higher Operational Costs: Fixed costs such as maintenance, energy consumption, and operator wages remain constant, regardless of whether the machine is running at full capacity or idle. This increases the cost per unit of production, reducing profitability.
- Low Return on Investment (ROI): When a machine operates below its potential, the financial returns fail to justify the initial investment, impacting overall business efficiency.
- Wasted Resources: Idle or underutilized machines take up valuable floor space and resources that could be allocated to other productive operations.
Overcapacity
- Production Delays: Insufficient capacity creates bottlenecks in the workflow, preventing manufacturers from meeting deadlines and fulfilling customer orders on time.
- Increased Machine Wear: Overloading the machine to meet higher demand results in accelerated wear and tear, increasing the frequency of breakdowns and maintenance costs.
- Reduced Product Quality: Operating a CNC router beyond its designed capacity can compromise precision and accuracy, leading to defects and subpar product quality.
Both underutilization and overcapacity highlight the importance of selecting a CNC router that aligns with production needs. Striking the right balance ensures optimal resource utilization, minimizes costs, and enhances manufacturing efficiency.
Factors Affecting Production Requirements
Understanding the factors that influence production requirements is beneficial for selecting equipment like CNC routers that meet operational needs without leading to inefficiencies. Here are the key factors:
Industry-Specific Requirements
Different industries have unique production needs that directly influence CNC router requirements.
- Furniture Industry: Requires larger bed sizes for cutting large wood panels and prioritizes smooth finishes for aesthetic appeal.
- Signage and Advertising Industry: Emphasizes speed and the ability to handle diverse materials like acrylic, metal, and wood for intricate designs.
The production scale, from custom one-offs to mass production, also varies by industry, impacting the machine’s capacity and automation level.
Material Type and Size
The type of material processed significantly affects production requirements:
- Hard Materials (e.g., metals): Require high-power spindles, robust tooling, and slower processing speeds to ensure precision and durability.
- Soft Materials (e.g., wood, foam): Allow for faster cutting speeds and may prioritize larger cutting areas over extreme precision.
Material thickness and size further influence machine bed dimensions and power needs. For example, larger sheets of material demand CNC routers with extended cutting beds and toolpaths that can accommodate oversized workpieces.
Product Complexity and Details
The complexity of the product being manufactured determines the CNC router’s precision, tooling, and multi-axis capabilities:
- Simple Designs: Require fewer tool changes, simpler programming, and standard 3-axis CNC routers.
- Intricate or Highly Detailed Products: Necessitate advanced features such as 4-axis or 5-axis functionality to handle complex geometries, fine detailing, and high precision.
The level of detail required, such as smooth edges or intricate carvings, also impacts the choice of CNC router speed, tool types, and software capabilities.
By carefully analyzing these factors, manufacturers can ensure their CNC router investments align with current and future production needs, avoiding underutilization or overcapacity while maintaining operational efficiency.
Evaluate production requirements
Determining production requirements is a critical step in selecting the right CNC router to ensure operational efficiency, cost-effectiveness, and scalability. This involves analyzing current capabilities, forecasting future needs, and collaborating across departments for a comprehensive assessment. Below are the key steps to effectively determine production requirements:
Analyze Current Production Data
Analyzing current production data provides a clear understanding of your existing capacity and operational patterns. This process involves:
- Evaluate Production Volumes: Assess average output, peak production periods, and cycle times to understand your existing capacity and whether it meets demand.
- Material Requirements: Identify the types, sizes, and quantities of materials used regularly, as these dictate the machine specifications needed.
- Machine Performance Records: Review data on downtime, maintenance frequency, and machine utilization to highlight inefficiencies or areas for improvement.
- Cost Per Unit: Calculate production costs to determine whether current methods align with budget and profitability goals.
This data provides a clear baseline for current production capabilities. By identifying trends and bottlenecks, you can pinpoint areas where current equipment meets, exceeds, or falls short of requirements.
Forecasts and Growth Projections
Anticipating future production needs based on market trends and business goals ensures your CNC router investment supports long-term goals. Forecasting involves:
- Market Demand Projections: Use sales data and market research to predict increases in product demand or seasonal fluctuations.
- Product Diversification: Account for new product lines or changes in product design. This may require enhanced machine capabilities, such as multi-axis operations or the ability to process additional materials.
- Scalability Requirements: Factor in planned expansions or upgrades to ensure the CNC router can handle future workloads.
- Technology Trends: Consider advancements in CNC technology that could impact production capabilities or efficiency.
Growth forecasting ensures that the selected CNC router not only meets current production needs but also supports future scalability and flexibility.
Inter-Departmental Collaboration
Collaborating across departments provides a holistic understanding of production requirements:
- Design and R&D Teams: Consult with teams about material specifications, design complexity, and precision needs.
- Sales and Marketing Teams: Gather input on projected order volumes, customer preferences, and emerging market opportunities.
- Operations Teams: Evaluate feedback on current workflow bottlenecks, downtime issues, and equipment limitations.
- Finance Department: Ensure the budget aligns with production goals, balancing investment with expected ROI.
Collaboration ensures that production requirements are not viewed in isolation but are aligned with company goals, operational realities, and financial constraints.
By systematically evaluating these aspects, manufacturers can comprehensively determine their production requirements. This approach ensures informed decisions when selecting CNC routers that optimize current operations while accommodating future growth.
Key Factors Affecting Production Capacity
Production capacity is a critical metric that determines how efficiently a manufacturing operation can meet demand. Several factors influence the production capacity of equipment like CNC routers, ranging from machine specifications to operational workflows. Below are the key factors:
Machine Size and Working Area
The size of the CNC router and its working area significantly impact productivity by determining the scope and scale of tasks it can handle.
- Material Dimensions: Larger working areas allow for processing bigger sheets or multiple smaller pieces simultaneously, reducing the need for frequent repositioning or multiple passes.
- Batch Processing: A spacious cutting bed supports higher productivity by accommodating multiple parts in one setup, improving throughput.
- Flexibility: Machines with adjustable or modular working areas provide versatility, enabling efficient processing of various material sizes and shapes.
A properly sized machine optimizes material handling and minimizes downtime, enhancing overall productivity.
Spindle Power and Tooling
The spindle is the core component of a CNC router, directly influencing its cutting capabilities and efficiency.
- Spindle Power: Higher-power spindles can cut through harder and thicker materials more efficiently, reducing cycle times. Lower-power spindles may limit processing speed or require multiple passes, slowing productivity.
- Tooling Options: The availability and compatibility of cutting tools (e.g., drills, end mills, and bits) determine the machine’s ability to handle diverse materials and complex designs. Automatic tool changers further boost productivity by minimizing manual intervention during tool swaps.
A powerful spindle and effective tooling reduce processing time and improve the machine’s ability to handle varied tasks, increasing productivity.
Cutting Speed and Feed Rate
Cutting speed (spindle RPM) and feed rate (movement of the tool along the material) are critical parameters that affect the rate at which materials are processed.
- Optimized Parameters: Setting the right cutting speed and feed rate ensures efficient material removal without compromising precision or tool life.
- Material Compatibility: Different materials require tailored speeds and feed rates. For example, metals may need slower speeds, while wood and plastics can be processed faster.
- Software and Programming: Advanced software can automatically adjust these parameters for maximum efficiency, ensuring consistent results across different jobs.
Faster and optimized cutting speeds and feed rates accelerate production while maintaining accuracy, directly boosting productivity.
By focusing on these factors, manufacturers can optimize their CNC router’s production capacity, ensuring that it aligns with both current and future operational demands.
Strategies to Avoid Underutilization and Overcapacity
Balancing Accuracy and Production Speed
- Optimized Parameter Settings: Adjust cutting speed and feed rates to balance production speed with the accuracy required for specific jobs. Faster speeds may increase throughput, but maintaining precision ensures high-quality output.
- Job Prioritization: Use high-precision settings for intricate designs and higher speeds for simpler tasks to optimize production cycles without sacrificing quality.
- Advanced Software: Leverage software that dynamically adjusts speed and accuracy parameters based on job requirements, ensuring the machine operates efficiently.
Ensures the CNC router operates at its optimal capacity, avoiding underutilization from overly conservative settings and overcapacity from excessive demand for precision on simple tasks.
Evaluating Toolpath Efficiency
- Optimized Toolpath Design: Use CAD/CAM software to create efficient toolpaths that minimize unnecessary movements and reduce cycle time.
- Nested Cutting Strategies: Arrange multiple parts on the cutting bed to maximize material usage and reduce setup times.
- Simulation and Testing: Run simulations to identify bottlenecks in the toolpath and refine operations for better efficiency.
Streamlined toolpaths reduce idle time and maximize productivity, preventing underutilization due to inefficiencies or overcapacity from prolonged cycle times.
Machine Utilization Monitoring and Analysis
- Utilization Tracking Software: Implement monitoring systems to track real-time usage, downtime, and idle periods to identify trends.
- Performance Benchmarks: Establish KPIs, such as capacity utilization rates, to measure whether the CNC router is underused or overburdened.
- Data-Driven Adjustments: Use the insights from monitoring to redistribute workloads, schedule maintenance, or identify when to scale up or down.
Ensures consistent and balanced machine usage, reducing the risk of overcapacity during peak demand or underutilization during slower periods.
Customization and Scalability
- Modular Machine Design: Invest in CNC routers with upgradeable components, such as larger beds or additional axes, to adapt to changing production needs.
- Custom Configurations: Choose machines that allow for tailored features like automation systems or advanced spindles to meet specific production demands.
- Future-Proofing: Plan for scalability to handle increased production volumes or diversify into new product lines without overcommitting to excess capacity.
Provides flexibility to adjust capacity based on current and future production requirements, avoiding both underutilization and overcapacity.
Cost Considerations Related to Production Volume
- ROI Analysis: Evaluate the cost per unit of production to ensure the machine’s capacity aligns with demand and delivers a strong return on investment.
- Batch Size Optimization: Analyze production costs for different batch sizes and schedule jobs to minimize overhead while maximizing throughput.
- Strategic Investments: Avoid overinvesting in high-capacity machines for low-volume production and underinvesting in smaller machines when scaling up.
Balances operational costs with production needs, ensuring the machine is neither underused nor overloaded, while maintaining profitability.
By combining these strategies, manufacturers can ensure the machine operates at its ideal capacity, avoiding the inefficiencies of underutilization and the strain of overcapacity, while supporting long-term business goals.
Summarize
Choosing a CNC router that meets your production requirements is a critical step in optimizing your manufacturing process and ensuring long-term success. By evaluating key factors such as machine size, spindle power, material compatibility, and production scalability, you can align your investment with both current needs and future growth. A well-chosen CNC router not only enhances operational performance but also provides the flexibility to adapt to evolving demands, ensuring your business remains competitive in a dynamic market. To learn more, read “Reviewing a CNC Router: Key Questions to Ask the Manufacturer.”
If you’re searching for a reliable CNC router that meets your specific production requirements, AccTek CNC stands out as a trusted and professional manufacturer. Our CNC routers are built with advanced features like customizable sizes, powerful spindles, and user-friendly control systems, ensuring they align seamlessly with your operational goals. AccTek CNC provides excellent customer support and after-sales service and is committed to being your reliable partner for long-term success.