- 12-17 Min Read
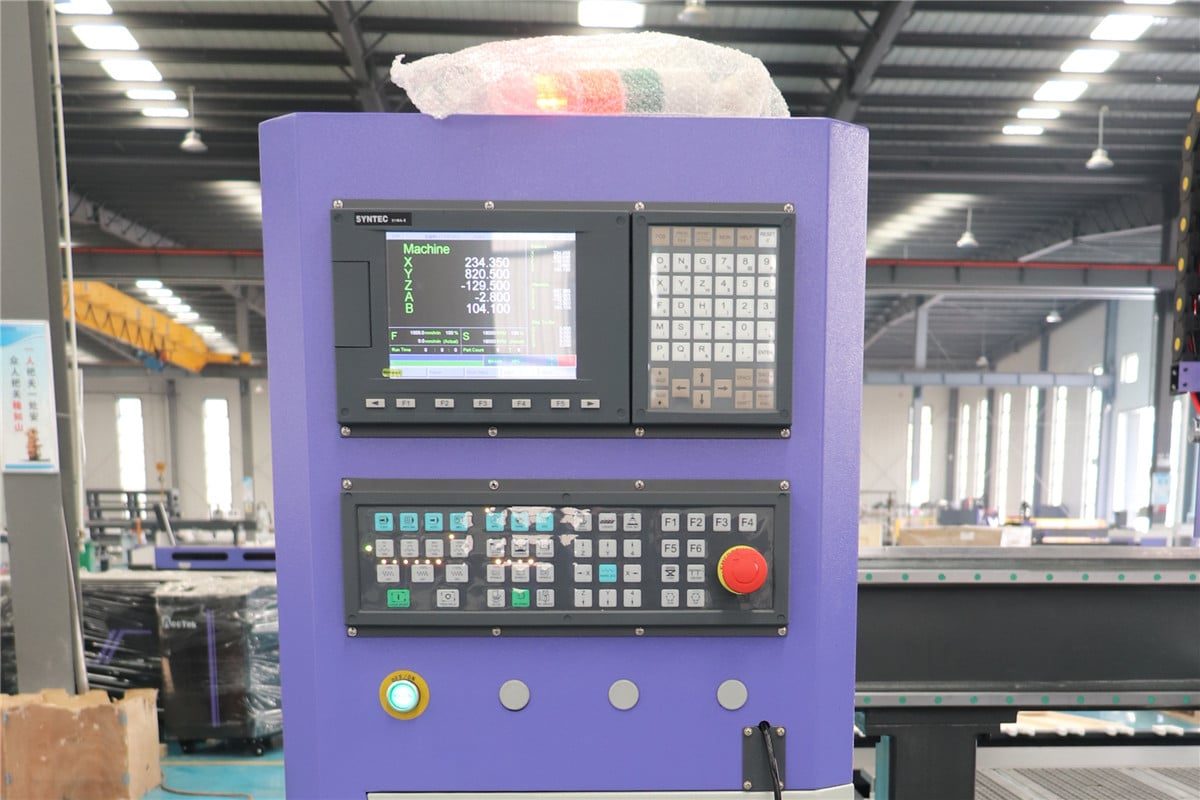
A CNC router controller is the heart of the machine, translating design files into precise movements and actions. The right controller not only ensures accuracy and efficiency but also determines the overall usability and compatibility of your CNC router with various software and operational requirements. With advancements in technology, controllers now come equipped with features that can simplify complex machining tasks, improve workflow, and offer greater customization options. However, with various options available in the market, selecting the most suitable controller can be overwhelming.
Selecting the best CNC router controller requires a thorough understanding of your specific production needs, the materials you work with, and the type of projects you undertake. Factors such as motion control precision, software compatibility, user interface, connectivity options, and cost must all be carefully evaluated. This article will guide you through the key considerations and help you make an informed decision when selecting a CNC router controller, ensuring your investment meets your specific needs and enhances productivity.
Understanding CNC Router Controller
A CNC router controller is the central system responsible for managing and executing the operations of a CNC router. It acts as the brain of the machine, converting design instructions into precise commands that control the movement of the machine’s spindle, axes, and other components. This ensures the accurate cutting, carving, or engraving of materials based on the programmed design. Here are its functions and types:
The Role of the Controller in a CNC Router
The controller in a CNC router serves as the central nervous system of the machine, orchestrating every aspect of its operation. Its role is multifaceted, encompassing task execution, machine coordination, and real-time monitoring. Here’s a detailed breakdown of its essential functions:
- Interpretation of Design Data: The controller translates design files, typically in G-code format, into commands that the CNC router can execute. This involves breaking down complex designs into a series of precise, step-by-step instructions for movements and actions.
- Motion Control and Coordination: One of the primary roles of the controller is to manage the synchronized movement of the CNC router’s axes (X, Y, and Z) and the spindle. This includes managing the path planning, adjusting spindle speeds, and coordinating tool paths to ensure accurate and efficient material processing.
- Real-Time Monitoring and Feedback: Beyond execution, the controller also ensures the smooth and safe operation of the CNC router by monitoring feedback from sensors and limit switches. It can detect and respond to errors, such as axis misalignment or overloading, to prevent damage to the machine or the workpiece.
- Safety and Error Handling: Safety is a critical aspect of the controller’s role. It monitors limit switches, emergency stop buttons, and environmental conditions to ensure safe operation. In the event of an error, the controller halts the machine and displays diagnostic information, helping operators troubleshoot issues effectively.
- Integration with Software: Modern CNC router controllers often integrate seamlessly with CAD/CAM software, streamlining the workflow from design to production. This allows operators to program and simulate tasks before execution, minimizing errors and ensuring efficiency.
The CNC router controller is indispensable for the machine’s performance, acting as the brain that connects design, operation, and execution. By managing motion, ensuring precision, and monitoring safety, the controller transforms the CNC router into a powerful and efficient tool for modern manufacturing. Its capabilities and features often determine the versatility, reliability, and productivity of the entire system.
Types of CNC Router Controllers
CNC router controllers come in various types, each tailored to specific applications and user requirements. The main categories include:
- Computer Controllers: A computer controller is a CNC router system that relies on an external computer to manage its operations. This setup uses specialized software installed on the computer to interpret design files and send commands to the machine.
- DSP Controllers: DSP (Digital Signal Processing) controllers are standalone devices that do not require an external computer, making them more compact and portable. These controllers typically feature an intuitive interface with an LCD screen and simple navigation, allowing users to upload design files via USB and operate the CNC router directly.
- All-in-One Controllers: All-in-one controllers integrate the computer, control hardware, and software into a single unit, simplifying the CNC router setup and operation. These systems are designed to provide plug-and-play functionality with a user-friendly interface, often featuring a touchscreen or dedicated control panel for easy navigation.
Understanding these types helps users choose the right controller to match their production needs, budget, and technical expertise, ensuring optimal machine performance.
Popular CNC router controller options
Popular CNC router controllers vary in terms of complexity, cost, and functionality, from simple DSP controllers to advanced computer-based systems. In this section, we will explore the most widely used CNC router controller options, including their applications, advantages, and limitations, helping you choose the best solution for your specific needs.
Mach3 Controller
Mach3 runs on Windows-based computers and interfaces with the machine’s hardware via a parallel port, USB, or Ethernet connection. Mach3 translates G-code instructions into motion commands, allowing users to control the movement of the machine’s axes and execute machining operations with precision.
- Applications: Mach3 is used primarily in hobbyist and small businesses, such as milling, engraving, routing, and drilling. The software’s broad compatibility with different machine types and hardware setups makes it suitable for both simple and complex machining tasks, particularly in low- to medium-volume production.
- Advantages: One of the main advantages of Mach3 is its affordability and ease of use, making it an excellent choice for hobbyists and small businesses. It offers a user-friendly interface that simplifies CNC machine setup and operation, along with a wealth of customizable options to optimize machine performance.
- Limitations: Mach3 requires a computer with sufficient processing power and compatible hardware interfaces, which may necessitate additional investment. Additionally, it requires a parallel port interface, which is becoming obsolete in modern computers, often requiring additional hardware or modifications to function properly with newer PCs.
Fangling Control System
Fangling control systems are a series of CNC systems developed and manufactured by Fangling Technology Co., Ltd., a leading Chinese company specializing in CNC technology. These control systems are designed to provide reliable and precise control for CNC routers, engraving machines, milling machines, and other CNC equipment.
- Applications: This system is widely used in industries requiring precise cutting operations, such as metal fabrication, automotive manufacturing, and signage production. Its versatility makes it suitable for applications involving complex shapes and high-volume production.
- Advantages: Fangling controllers are known for their reliability and stability, ensuring consistent performance even in demanding production environments. The user-friendly interface makes programming and operating the CNC router straightforward, reducing setup time and training requirements. They offer a good balance of performance and affordability, making them suitable for both hobbyists and small to medium-sized businesses.
- Limitations: While Fangling controllers offer a range of features, they may have limited customization options compared to more advanced controllers. Additionally, users are reliant on the proprietary control software provided by Fangling, which may have limitations in terms of features or compatibility with third-party software.
Weihong Controller
Weihong CNC controllers are produced by Beijing FANCH Machinery Co., Ltd., a leading manufacturer of CNC control systems and equipment. Weihong controllers are known for their reliability, performance, and cost-effectiveness, making them popular choices for CNC machines across various industries.
- Applications: These controllers are utilized in diverse industries, including woodworking, metalworking, and 3C electronics manufacturing. They can handle various CNC machining tasks, including milling, turning, drilling, and more.
- Advantages: Weihong controllers offer high precision, reliability, and versatility, accommodating a wide range of machining tasks. Their advanced algorithms enhance cutting efficiency and quality, while their compatibility with various machine types provides flexibility for different production needs.
- Limitations: Despite their advanced features, Weihong controllers may require a steeper learning curve for new users due to their complexity. Additionally, Weihong controllers may be less commonly available in other parts of the world, which could affect support and spare parts availability.
FANUC Control System
The FANUC Control System is a widely used CNC control system developed by FANUC Corporation, a leading manufacturer of factory automation and industrial robotics systems. It is a comprehensive CNC control solution designed for a wide range of machining and manufacturing applications.
- Applications: FANUC control systems are employed in applications ranging from high-volume, repetitive production to the machining of unique, highly complex parts requiring advanced techniques. Their versatility makes them suitable for both simple and intricate machining tasks.
- Advantages: The primary advantages of FANUC control systems include exceptional performance, ease of use, and robust reliability. They offer seamless integration with various machine tools and automation systems, enhancing productivity and operational efficiency. Additionally, FANUC has a global network of service and support centers, ensuring prompt assistance and maintenance services wherever the equipment is deployed.
- Limitations: Despite their strengths, FANUC control systems can be complex to program and operate, requiring specialized training and expertise. The initial investment and maintenance costs may be higher compared to some other control systems, which could be a consideration for smaller businesses or those with budget constraints.
SYNTEC Control System
SYNTEC is a Taiwanese company that specializes in manufacturing CNC controllers for a variety of machining applications, including milling, turning, and routing. The SYNTEC Control System is a comprehensive solution that includes hardware components, such as motion control cards and operator panels, as well as software for programming and operating CNC machines.
- Applications: Syntec control systems are versatile and widely used across various industries, including mold-making, high-speed milling, engraving, and mill-turn machining. They are suitable for standard machines like lathes, milling centers, CNC routers, and milling machines.
- Advantages: SYNTEC control systems are known for their high precision and accuracy in controlling machine movements, resulting in superior machining quality. Their multi-axis and multi-program capabilities allow for complex simultaneous multi-tool cutting interpolations, increasing machining flexibility.
- Limitations: While Syntec control systems provide advanced features, they may require a learning curve for operators unfamiliar with CNC operations. Additionally, SYNTEC control systems may come with a higher initial cost compared to some other alternatives, which could be a drawback for budget-conscious users.
LNC Control System
LNC Control Systems are popular CNC control systems developed by LNC Technology Co., Ltd., a Taiwanese company specializing in CNC controllers and automation solutions. They encompass both hardware and software components, offering a complete package for controlling machine tools and automation equipment.
- Applications: LNC Control Systems deliver high-speed and high-precision motion control, enabling efficient machining of complex parts with tight tolerances. They are suitable for a wide range of CNC applications, from simple milling and turning operations to complex multi-axis machining and automation tasks.
- Advantages: LNC Control Systems are built to withstand the demands of industrial machining environments, offering reliable performance and long-term durability. They support advanced functions such as high-speed drilling and tapping, high-precision contour control (HPCC), and smooth precision advanced (SPA) for enhanced surface quality.
- Limitations: Setting up and configuring LNC systems to work optimally with specific machines and applications may require technical expertise, which could be a challenge for some users. Compared to some entry-level CNC control solutions, LNC Control Systems may have a higher initial cost, particularly for advanced configurations with additional features.
DSP Control System
DSP Control Systems are standalone units designed specifically for controlling CNC machinery. They employ digital signal processing technology to execute motion control algorithms and generate precise control signals for the CNC router’s motors. DSP controllers typically feature dedicated hardware for motion control tasks, offering reliability and performance optimized for CNC applications.
- Applications: DSP control systems are ideal for small-to-medium-sized workshops, educational setups, and businesses engaged in metalworking, woodworking, engraving, and signage production. Their simple setup and ability to handle basic 2D and 3D cutting tasks make them popular in applications that require high throughput with moderate complexity, such as furniture manufacturing or advertising production.
- Advantages: One of the key advantages of DSP control systems is their cost-effectiveness. These controllers are less expensive compared to PC-based systems. DSP controllers also offer ease of use, as they typically require less setup time and come with an intuitive interface. Their portability is another advantage, as they do not rely on an external computer.
- Limitations: While DSP control systems are reliable and cost-effective, they have limitations in handling complex operations or high-precision tasks. Their processing power is lower compared to more advanced systems, which makes them unsuitable for tasks requiring multi-axis control or intricate machining.
Siemens Control System
Siemens control systems are advanced CNC solutions known for their high performance, flexibility, and scalability. They utilize cutting-edge technology, offering precise motion control, real-time data processing, and integration with various machine types. These systems are also highly compatible with Siemens’ proprietary software and can be seamlessly integrated into automated production lines for enhanced productivity.
- Applications: Siemens control systems are widely used in industries that require high-precision and complex machining tasks, such as automotive manufacturing, aerospace, metalworking, and medical device production. Their versatility makes them suitable for a variety of CNC machines, including multi-axis machining centers, robotic arms, grinding machines, and laser systems.
- Advantages: Siemens control systems offer significant advantages, including robust performance, high-speed processing, and precise motion control across multiple axes. Their advanced features, such as predictive maintenance capabilities, and extensive diagnostic tools, help optimize machine uptime and reduce operational costs. Additionally, Siemens controllers are designed to provide a high level of reliability, making them a trusted choice for industries with stringent operational demands.
- Limitations: While Siemens control systems are highly advanced, they can be costly. The complexity of the system may require significant training and technical expertise to fully utilize its capabilities. Additionally, integrating Siemens controllers with existing non-Siemens equipment can be challenging and may require custom solutions or additional hardware.
The right CNC router controller is beneficial to achieving optimal performance, efficiency, and precision in your machining tasks. Whether you are a hobbyist looking for a simple setup or a professional needing advanced features for complex projects, understanding the strengths and limitations of each option will guide you to the perfect CNC router controller for your needs.
How to Choose the Right CNC Router Controller
Choosing the right CNC router controller requires careful consideration of several factors to ensure the controller is compatible with your machine’s requirements and operational goals. Here are the key elements to keep in mind:
Machine Requirements and Specifications
- Size and Type of CNC Router: Larger CNC routers with bigger worktables and heavier loads require controllers capable of managing higher precision, speed, and force. The type of machine determines the required controller capabilities. Industrial CNC routers typically need more advanced controllers than smaller, hobbyist models.
- Number of Axes and Motion Complexity: CNC routers can be 3-axis, 4-axis, or 5-axis. A 3-axis CNC router is simpler and handles basic cutting and engraving, and a simple controller is sufficient. The 4-axis machine allows for additional rotational motion for more complex tasks, and a 5-axis CNC router offers the highest complexity, enabling simultaneous multi-directional movement. Multi-axis CNC routers handling complex tasks require advanced controllers that support precise motion control, path smoothing, and velocity ramp-up to ensure accurate and high-quality results.
Compatibility with Motors and Drives
- The CNC router controller should be fully compatible with the motors and drives used in your system. Whether you’re using stepper motors or servo motors, ensure that the controller can interface with your motor drivers and control them accurately. Some controllers are optimized for specific motor types, so compatibility with existing equipment needs to be checked to ensure smooth machine operation.
Integration with CAM Software
- Compatibility with G-code Generators: G-code is the language used to communicate instructions between the design software and the CNC router. The controller must be compatible with popular G-code generators used in CAM (Computer-Aided Manufacturing) software.
- Ease of Integration: For a smooth transition from design to production, the CNC controller should integrate seamlessly with CAM software. The simpler the integration process, the quicker the setup time, which leads to improved productivity and fewer chances for error during machine operation.
- Achieving Seamless Workflow: A CNC router controller that works well with CAM software ensures a continuous and efficient workflow, from design to machining. The integration allows for real-time adjustments, which minimizes interruptions during the production process and helps maintain accuracy, ultimately enhancing overall productivity and operational efficiency.
User Interface and Ease of Use
- Operator-Friendly Control Panel: Choosing an operator-friendly control panel can simplify machine operation. It typically features well-organized buttons, knobs, or a touchscreen interface that allows the operator to easily adjust settings, start or stop the machine, and monitor performance.
- Intuitive Software Interface: The controller should feature an intuitive software interface, and provide a clear, easy-to-navigate design. The interface should also allow for simple program uploads, real-time monitoring, and error detection, making it accessible for both beginners and experienced users.
Motion Control Features
- Accuracy: Motion control accuracy ensures that the CNC router follows the programmed path with high precision, translating design data into exact movements. The controller must handle fine adjustments to the machine’s axes, allowing for detailed cuts and intricate designs without deviations, resulting in high-quality outputs and minimizing material waste.
- Acceleration and Deceleration: Select a controller with advanced acceleration and deceleration features to enable smooth transitions during high-speed operations. The ability to control how quickly the machine speeds up and slows down will help avoid sudden jerks or vibrations, ensuring better cutting precision, reducing tool wear, and improving the overall finish of the workpiece.
- Simultaneous Multi-Axis Control: For machines that require complex cuts or intricate geometries, choose a controller that supports simultaneous multi-axis control. This feature allows for the coordination of multiple axes in real-time, providing flexibility, efficiency, and precision across advanced tasks such as 3D carving.
Industry-Specific Requirements
- Depending on your industry, you may need a controller with specific functionalities. For example, if you are working in the metal fabrication industry, you may need a controller that supports high-speed plasma cutting or laser cutting with precise height control. Industry-specific controllers often come with pre-configured settings and add-ons tailored to the specific needs of certain sectors.
Budget Considerations
- Controllers can range from budget-friendly, basic options to high-end systems with advanced features. It’s important to balance your budget with the features you require. For smaller workshops or hobbyists, a simple DSP controller may be sufficient, while larger manufacturing environments may require more expensive, feature-rich options. Make sure to factor in both initial costs and any potential future upgrades when considering the overall investment.
Operator Skills
- The controller you choose should match the skill level of the operators who will be using it. If you have experienced operators, you might opt for a more sophisticated controller with advanced features. However, for less experienced operators or those new to CNC machining, a controller with a more straightforward interface and ease of use might be preferable. Offering training and support for your chosen controller can also help ensure optimal operation and efficiency.
By carefully considering these factors, you can select a CNC router controller that not only meets your current requirements but also offers the flexibility and performance needed to adapt to future production needs.
Summarize
Choosing the right CNC router controller is a critical decision that directly impacts the efficiency, accuracy, and overall performance of your CNC machine. By considering the factors mentioned in the above article, you can select a controller that best suits your specific needs. Whether you’re working with a simple 3-axis CNC router or a more complex multi-axis system, the right controller will ensure smooth operation, precise cuts, and long-term reliability. Take the time to evaluate your options carefully, and make an informed decision that aligns with both your immediate and future production goals.
AccTek CNC, as a professional CNC router manufacturer, offers a wide range of high-quality machines designed to meet diverse customer needs, from small-scale workshops to large industrial applications. With a focus on user-friendly interfaces and robust support, we ensure that controllers are both easy to operate and highly capable, making them an excellent choice for businesses looking to improve their machining efficiency. Whether you’re upgrading your current equipment or investing in a new CNC router, AccTek CNC provides the technology and expertise to help you achieve optimal results.