- 10-15 Min Read
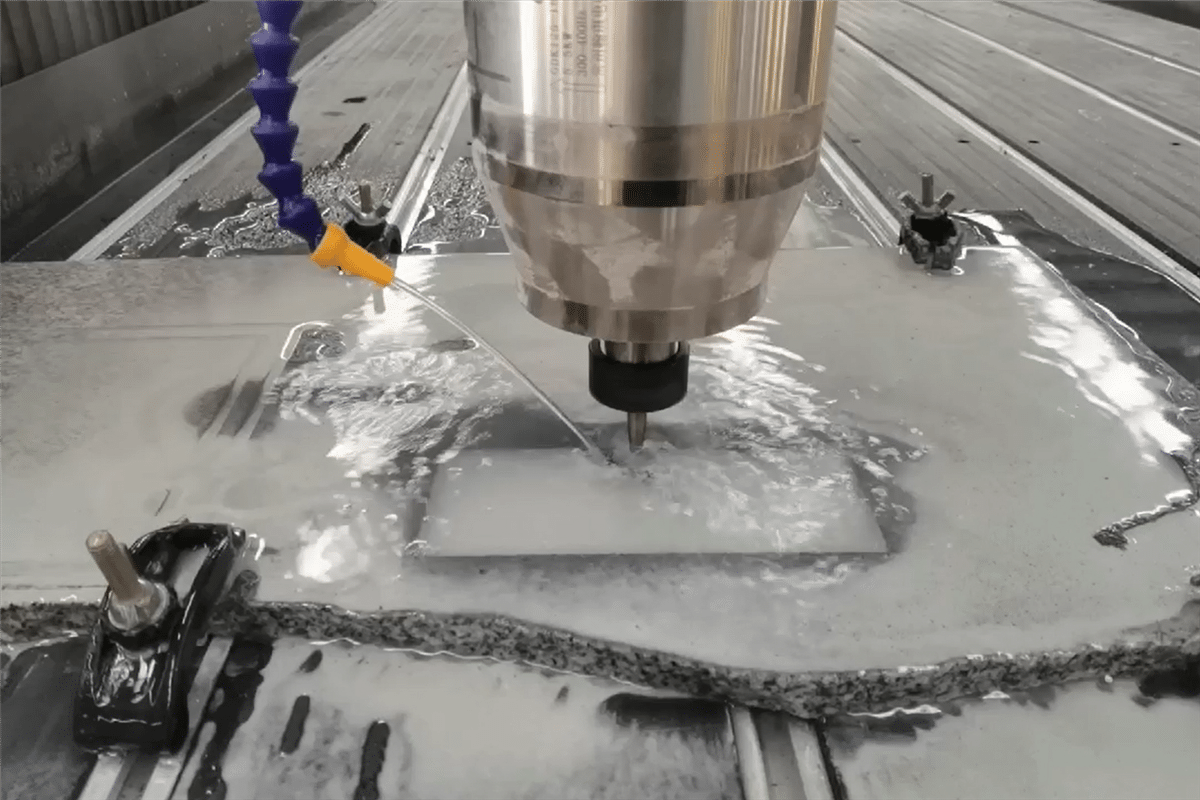
Stone carving has been an art form for centuries, traditionally requiring skilled hands and countless hours of meticulous work. However, with the advent of CNC (Computer Numerical Control) technology, stone carving has become more efficient, precise, and accessible. Whether you’re a professional sculptor, an architectural designer, or a hobbyist, using a CNC router to carve stone allows for intricate designs, consistent quality, and reduced labor costs.
CNC routers designed for stone carving can handle a wide range of materials, from soft limestone and marble to hard granite and quartz. This guide will walk you through everything you need to know about carving stone with a CNC router, from choosing the right stone and tools to setting up your machine and optimizing carving techniques. Whether you’re working on signage, decorative elements, or artistic sculptures, understanding the fundamentals of CNC stone carving will help you achieve professional results.
Understanding CNC Routers for Stone Carving
A CNC router is a precision cutting machine that automates the carving, engraving, and shaping of materials using a computer-controlled system. CNC routers are widely used in industries such as woodworking, metal fabrication, and stone processing due to their accuracy, repeatability, and efficiency. First, let’s learn about CNC routers for stone carving.
The Basics of CNC Router Operation
CNC routers work by interpreting digital design files, typically in formats such as DXF, STL, or G-code, to guide the machine’s movements. The key components of a CNC router include:
- Spindle: The high-speed rotating tool that cuts or engraves the material.
- Worktable: The surface where the material is secured for carving.
- Guide Rails and Motion System: These enable precise movement in the X, Y, and Z axes for accurate cutting.
- Control System and Software: Users input design specifications through software such as Mach3, UCCNC, or Fusion 360, which generates toolpaths and controls the router’s movements.
- Cooling and Dust Extraction: Depending on the material, CNC routers may use water cooling systems (for stone and metal) or dust extraction systems (for wood and plastics) to maintain cleanliness and extend tool life.
The CNC router automates the carving process by following programmed toolpaths, ensuring consistent and precise results even for intricate designs.
Key Features of a Stone CNC Router
A stone CNC router is specifically designed to handle the challenges of engraving and cutting hard materials like marble, granite, quartz, and sandstone. Unlike standard CNC routers, stone CNC routers require reinforced structures, high-powered spindles, and specialized cooling systems to ensure efficient and precise carving. Below are the key features that make CNC stone routers suitable for stone engraving and cutting:
- Heavy-Duty Machine Structure: A stone CNC router is built with a reinforced steel or cast iron frame to withstand the high forces and vibrations associated with stone carving. The rigid construction ensures stability and precision, preventing material shifting or tool misalignment.
- High-Powered Water-Cooled Spindle: To handle the hardness of materials like granite and quartz, stone CNC routers are equipped with high-power spindles ranging from 6kW to 15kW. These spindles operate at adjustable speeds and are water-cooled to prevent overheating, extend tool life, and maintain cutting efficiency.
- Diamond-Tipped Cutting and Engraving Tools: Unlike traditional router bits, stone CNC routers use diamond-tipped tools designed to cut through dense materials with precision. These specialized bits come in various shapes, including flat, ball nose, and V-groove, enabling a wide range of engraving depths and detailing.
- Water Cooling System: Stone engraving generates significant heat, which can damage the machine. To counteract this, CNC stone routers feature a water cooling system, which continuously sprays water onto the cutting area. This extends tool life, creating a safer working environment.
These features make CNC stone routers highly efficient, durable, and capable of handling intricate engraving tasks with precision.
Choosing the Right Stone for CNC Carving
Selecting the right stone for CNC carving is beneficial to achieving high-quality engravings while ensuring efficiency and tool longevity. Different stones vary in hardness, texture, and workability, affecting the cutting speed, tool wear, and final surface finish. Below are the key considerations when choosing a stone for CNC carving:
Types of Stone Suitable for CNC Carving
Soft Stones
These stones are easier to work with, making them ideal for fine engraving and artistic designs.
- Marble: Offers a smooth texture and elegant finish, commonly used for sculptures, monuments, and decorative carvings.
- Soapstone: Very soft and easy to carve, often used for artistic engravings and intricate detailing.
- Limestone: A relatively soft stone with good workability, suitable for architectural carvings and decorative panels.
Medium-Hard Stones
These stones offer good durability while still being relatively easy to carve.
- Sandstone: Ideal for detailed carvings, statues, and architectural engravings, though it can produce more dust.
- Travertine: A porous yet durable stone, often used for ornamental and historical engravings.
Hard Stones
Harder stones require diamond-tipped cutting tools and high-power spindles for effective carving.
- Granite: Extremely durable, best suited for tombstones, signage, and industrial applications; requires slower cutting speeds and high-power spindles.
- Quartz: Very hard but provides a beautiful polished finish, commonly used for countertops and decorative elements.
- Basalt: A dense volcanic stone ideal for durable outdoor sculptures and architectural structures.
Factors to Consider When Selecting Stone
Stone Hardness
The hardness of the stone determines how much power and time the CNC router needs for carving. The Mohs hardness scale is often used to classify stones:
- Soft stones (Mohs 1-3): Faster and easier to carve with minimal tool wear.
- Medium-hard stones (Mohs 4-6): Requires moderate cutting speeds and durable tools.
- Hard stones (Mohs 7-9): Requires high-power spindles and diamond tooling for precision cutting.
Surface Smoothness and Grain Structure
The grain structure and texture of a stone affect the level of detail that can be achieved in CNC carving. Selecting a fine-grain, homogeneous stone ensures better engraving resolution and fewer tool-related issues.
- Fine-grained stones (e.g., marble, soapstone): Allow for high-precision detailing and smoother carvings.
- Coarse-grained stones (e.g., granite, sandstone):May limit engraving precision and produce a rougher finish.
Stone Thickness and Workpiece Size
The thickness and overall size of the stone impact the type of CNC router and worktable required. Choosing the appropriate stone thickness ensures structural stability and efficient processing.
- Thin slabs (e.g., 10-30mm thick): Suitable for plaques, tiles, and decorative engravings.
- Thicker blocks (e.g., 50mm and above): Needed for 3D sculptures, statues, and deep relief carvings.
Moisture and Porosity
Some stones have high porosity, meaning they absorb water easily. This can impact cooling efficiency, sealing requirements, and durability:
- Highly porous stones (e.g., limestone, sandstone) may absorb water during carving, requiring proper sealing and drying before use.
- Dense, non-porous stones (e.g., granite, quartz) are ideal for detailed and polished finishes.
Intended Application and Environment
The final use of the carved stone determines which type of material is best suited. Choosing a stone that fits the intended environment ensures long-term durability.
- Indoor applications (e.g., plaques, decorative panels, sculptures): Can use softer stones like marble or limestone.
- Outdoor applications (e.g., monuments, tombstones, architectural facades): Require weather-resistant stones like granite, basalt, or quartz.
- Industrial applications (e.g., machine parts, durable surfaces): Require dense and impact-resistant stones.
Choosing the right stone for CNC carving depends on hardness, grain structure, thickness, and intended application. Soft stones like marble and soapstone are great for fine detailing, while hard stones like granite and quartz offer durability but require more advanced tooling. By selecting the appropriate stone, CNC router users can optimize efficiency, reduce tool wear, and achieve the best engraving results.
Essential Tools and Equipment
When using a CNC router for stone carving, having the right machine setup and cutting tools is beneficial for achieving precision, efficiency, and durability. Below, we introduce the essential tools and equipment from two key aspects: CNC router setup for stone carving and choosing the right cutting tools.
CNC Router Setup for Stone Carving
Setting up a CNC router for stone carving requires specialized components to handle the hardness, weight, and dust generated by stone materials.
- Heavy-Duty CNC Router Machine: A stone CNC router differs from standard woodworking machines as it features a reinforced steel or cast iron frame to absorb vibrations and ensure stability. The worktable must be strong enough to support heavy stone slabs, and vacuum hold-down systems or mechanical clamps are used to keep the stone securely in place.
- High-Powered Water-Cooled Spindle: Since stone is dense and hard, CNC routers for stone engraving require a high-power spindle ranging from 6kW to 15kW. The spindle must be water-cooled to prevent overheating and prolong tool life. Adjustable spindle speeds (0-24,000 RPM) allow for flexibility when working with different stone hardness levels.
- Water Cooling and Dust Suppression System: Stone carving generates significant heat and dust, which can damage both the machine and tools. A water spray system is used to cool the cutting area, reduce tool wear, and suppress dust. Additionally, a drainage system is needed to handle water runoff and stone debris efficiently.
- Precision Motion System: To achieve detailed carvings and smooth engraving, CNC routers must have high-precision linear guides, ball screws, and servo or stepper motors. The Z-axis movement must be adjustable to accommodate varying stone thicknesses and different carving depths.
- Rotary Axis for Cylindrical Carving (Optional): For engraving cylindrical stone objects such as columns, vases, and balusters, a rotary axis attachment allows for 360-degree engraving with high precision. This is an essential tool for advanced 3D carving and artistic stone design.
Choosing the Right Cutting Tools
The choice of cutting tools directly impacts the quality and efficiency of stone carving. Since stone is significantly harder than wood or plastic, CNC routers require diamond-tipped tools for effective cutting and engraving.
Diamond-Tipped Cutting Tools
Unlike standard carbide bits, diamond-coated tools are specifically designed to cut through marble, granite, limestone, quartz, and basalt without excessive wear. These tools come in different shapes to achieve various engraving effects.
Types of Cutting Tools for Stone Carving
- Flat End Mills: Used for rough cutting and material removal.
- Ball Nose Bits: Ideal for 3D carving, relief work, and intricate designs.
- V-Groove Bits: Best for letter engraving and fine detailing.
- Core Drill Bits: Used for deep drilling in stone slabs.
Tool Durability and Selection
- Soft stones (e.g., marble, limestone): Standard diamond-tipped bits work well.
- Hard stones (e.g., granite, quartz): Require industrial-grade diamond tools and slower cutting speeds to prevent tool breakage.
- Intricate detailing: Small-diameter ball nose and V-groove bits ensure precision.
Automatic Tool Changer (ATC) for Multi-Tool Operations
For advanced CNC stone carving, machines with an automatic tool changer (ATC) can switch between different engraving, cutting, and polishing tools without manual intervention, increasing efficiency and precision.
A successful CNC stone carving setup depends on a reinforced CNC router with a high-powered water-cooled spindle, efficient dust and cooling systems, and precise motion control. Choosing diamond-tipped cutting tools tailored to the stone hardness and carving requirements ensures durability and fine detailing. By optimizing both the CNC router setup and the cutting tool selection, users can achieve high-quality, precise, and efficient stone carvings.
Preparing Your Design for CNC Carving Stone
Proper preparation of your design is beneficial for achieving high-quality and precise engravings with a CNC stone router. From creating the digital model to optimizing the toolpath, every step influences the final result. Below, we explore the key aspects of design preparation:
Toolpath Generation
Creating or Importing 3D Models
CNC stone engraving starts with a digital design, which can be created from scratch or imported from existing 3D models.
- Using CAD/CAM Software: Popular CAD programs allow users to design intricate reliefs, sculptures, and engravings with high precision. Once the design is complete, CAM software generates the toolpaths needed for the CNC router to execute the engraving. These software solutions help define the depth, resolution, and type of engraving required while optimizing cutting parameters for stone materials.
- File Formats: STL files are widely used for 3D relief carvings and sculptures, and DXF files are primarily used for 2D engravings and vector-based carvings. Once the model is finalized, the CAM software converts it into G-code, the machine-readable programming language that directs the CNC router’s movements.
- Adjusting the Design: For successful stone engraving, the 3D model must be adjusted to match the CNC router’s precision capabilities. One crucial factor is scale and proportion, ensuring that the design fits within the stone slab dimensions and maintains accurate detail levels. Additionally, depth control must be fine-tuned, too deep can cause tool breakage, while too shallow may result in an unclear engraving.
Toolpath Generation
Once the 3D model is ready, the next step is to generate a precise toolpath that the CNC router will follow.
- Roughing and Finishing: Roughing tool paths are designed to remove large amounts of material quickly, using flat end mills or large-diameter ball nose bits to carve out the basic shape with minimal detail. Finishing tool paths use smaller ball nose bits or V-groove tools to refine the details, ensuring smooth curves and sharp engraving edges.
- Feed Rate and Spindle Speed: Since stone is much harder than wood or plastic, a lower feed rate and moderate spindle speed (6,000–15,000 RPM) are recommended to prevent overheating and tool wear. Softer stones like marble or limestone can handle higher feed rates, while granite and quartz require slower, more controlled movements.
- Avoiding Tool Breakage and Excessive Wear: Tool wear and breakage are common issues when engraving stone, so careful tool path planning is necessary to extend tool life. One effective strategy is using multi-pass cutting to prevent excessive tool stress, this involves removing material in small increments rather than cutting deep in a single pass.
Simulation and Pre-Processing
Before starting the actual engraving, running a simulation and preprocessing check helps prevent costly mistakes.
- Running a Software Simulation: Simulations help identify tool collisions, over-cutting, incorrect depths, or machine limit violations, reducing the risk of material waste and tool damage. This step also allows users to fine-tune feed rates, spindle speeds, and cutting depths, ensuring that the stone engraving process runs smoothly and efficiently.
- Testing on a Small Piece: Different stones, such as marble, granite, and limestone, respond differently to CNC engraving, so testing ensures that the chosen settings produce the desired detail and depth. Adjustments to tool speed, depth of cut, and cooling efficiency can be made based on the test results, preventing costly mistakes in the full-scale production.
Preparing a design for CNC stone engraving requires careful planning in 3D modeling, toolpath generation, simulation, and machine setup. By optimizing each step, you can ensure efficient engraving, minimal tool wear, and high-quality results. Proper design preparation also reduces errors and improves precision, consistency, and overall project success.
The CNC Stone Carving Process
The CNC stone carving process involves several critical stages, including machine setup, carving execution, and post-processing, each requiring careful attention to detail to ensure optimal results. Below is an overview of the essential steps involved in CNC stone carving.
Machine Setup and Safety Precautions
Before beginning the stone carving process, proper machine setup and safety measures must be in place.
- Machine Calibration: The worktable must be level, and the stone piece should be securely clamped or held by a vacuum table to prevent movement during operation. The CNC spindle must be aligned correctly, with the tool positioned at the correct zero point to match the design file.
- Check Water Cooling and Dust Removal Functions: The water cooling system must function correctly to prevent overheating of the spindle. Additionally, an industrial dust removal system or misting system should be active to capture fine stone dust and debris. Regular checks on water flow, drainage, and dust filters ensure optimal system performance.
- Operator Safety Equipment: Workers should wear protective eyewear to shield their eyes from dust and small stone particles. A dust-proof face covering prevents inhalation of hazardous fine dust, which can cause respiratory issues. Heavy-duty gloves and protective clothing protect the hands and body from sharp stone edges, while hearing protection reduces exposure to loud machine noise.
Carving the Stone
Once the machine setup is complete, the CNC router begins carving the stone, following the programmed G-code toolpath.
- From Roughing to Finishing: The roughing stage uses large-diameter flat or ball nose end mills to carve out the basic shape, reducing the bulk of the material quickly. After roughing, the finishing stage utilizes smaller ball nose bits or V-groove bits to refine edges, add texture, and bring out intricate details.
- Adjusting the Cutting Depth and Speed: Harder stones like granite and quartz require shallower cuts per pass (0.5-2mm) and slower feed rates, while softer stones like marble and limestone can handle deeper cuts (2-5mm) with slightly higher feed rates. The spindle speed (typically 6,000-15,000 RPM) should be adjusted to balance smooth cutting and minimal tool wear.
- Monitoring the Machine for Tool Wear: Operators should regularly check for signs of tool wear, such as reduced cutting efficiency, increased chipping, or rough surface finishes. Worn-out diamond tools should be replaced immediately to maintain engraving accuracy.
Post-Processing and Finishing
After the engraving is complete, post-processing and finishing enhance the appearance and durability of the carved stone.
- Cleaning the Carved Stone: After the CNC engraving process is complete, the first step in post-processing is cleaning the stone surface to remove dust, debris, and residual cutting fluids. The most common method is rinsing with water while using a soft brush or compressed air to clear out fine particles trapped in the engraving details.
- Polishing Techniques: Polishing enhances the smoothness and appearance of the engraved stone, making details stand out. For a matte finish, the stone can be lightly sanded using fine-grit sandpaper or a rotary polisher. For a glossy finish, specialized diamond polishing pads can be used, gradually increasing fineness to achieve a reflective surface.
- Manually Adding Final Details: Despite the precision of CNC engraving, some fine details may need manual refinement to achieve a perfect finish. Hand tools such as chisels, carving knives, or micro-polishers can be used to sharpen intricate patterns or enhance textures in relief carvings.
By following proper safety measures, optimizing tool paths, and using effective finishing techniques, CNC router engraving machine can produce durable, intricate, and visually stunning stone designs suitable for various industries, from artistic sculptures to architectural engravings.
Troubleshooting and Maintenance of Stone CNC Router
Since CNC stone carving involves high spindle power, abrasive materials, and continuous cooling systems, routine checks and timely troubleshooting help prevent breakdowns, reduce downtime, and maintain precision. Below, we explore the key aspects of common troubleshooting solutions and routine maintenance practices for stone CNC routers.
Troubleshooting Common Issues
- Tool Wear and Breakage: Frequent tool wear or breakage can lead to poor engraving quality and increased operational costs. To prevent this, operators should use diamond-tipped cutting tools designed for stone, reduce cutting depth per pass, and ensure that the water cooling system is functioning properly to minimize friction and overheating.
- Inconsistent Engraving Depth: Uneven engraving depths, missed details, or over-cutting is often caused by an unlevel workpiece, improper Z-axis calibration, or worn-out tools. To resolve this, ensure that the stone is securely clamped or vacuum-held. Regular calibration of the Z-axis zero point helps maintain depth accuracy, while replacing worn tools ensures consistent detailing.
- Dust and Debris Accumulation: Stone CNC routers generate fine dust and debris, which can clog the cooling system, affect engraving accuracy, and damage internal components. To prevent buildup, ensure the water spray system is functioning correctly and that drainage is unobstructed. Using a vacuum system to remove excess debris after each job helps keep the machine clean and running smoothly.
- Spindle Overheating: A stone CNC router’s spindle operates under heavy loads, and overheating can lead to reduced efficiency or permanent damage. Operators should check the water pump flow rate, clean cooling hoses regularly, and adjust spindle speed based on the stone type being engraved.
- Software and Control Errors: To troubleshoot, ensure that the correct file format (.nc, .tap, .cnc) is used and that the CNC software is properly configured. Loose motor connections or damaged drive belts should be inspected and repaired if necessary. Keeping the machine firmware and software updated ensures smoother operation and fewer compatibility issues.
Routine Maintenance Practices
- Daily Maintenance: After each operation, clean the machine bed, spindle area, and cutting tools to remove dust and debris. Check the water cooling system for proper flow, and inspect tool holders and clamps for any looseness.
- Weekly Maintenance: Every week, inspect and tighten bolts, clamps, and drive belts to prevent machine vibration. Verify spindle motor efficiency and check tool wear for signs, replacing cutting bits as needed.
- Monthly Maintenance: Monthly maintenance should include cleaning dust extraction filters, draining and refilling the cooling system, and checking stepper/servo motor performance. Running a machine calibration test at least once a month helps maintain accuracy and consistency in engravings.
- Long-Term Maintenance (Every 6-12 Months): For long-term reliability, perform a deep inspection of all CNC router components every 6-12 months. This includes replacing worn-out spindle bearings, checking for electrical faults, and realigning linear guides and ball screws. The water cooling system should be flushed and refilled to prevent blockages, and safety systems should be tested.
Regular troubleshooting and preventive maintenance are beneficial for keeping a stone CNC router in optimal condition. Addressing tool wear, cooling system performance, and dust accumulation ensures smooth operation and high-quality engraving. By following daily, weekly, and long-term maintenance schedules, operators can significantly reduce downtime, improve accuracy, and extend machine lifespan, making CNC stone carving more efficient and cost-effective.
Summarize
Carving stone with a CNC router combines precision, efficiency, and creative flexibility, making it an ideal solution for industries ranging from architecture and monument engraving to artistic sculpture and industrial applications. By following a structured process, users can achieve high-quality and detailed stone carvings with minimal material waste. Selecting the right stone type, tools, and cutting parameters ensures optimal performance, while regular maintenance and troubleshooting keep the CNC router in peak condition.
AccTek CNC is a trusted manufacturer for anyone investing in a powerful and precise CNC stone carving machine. Whether engraving architectural details, monuments, or decorative sculptures, AccTek CNC routers provide the efficiency, accuracy, and ease of operation needed to achieve professional-grade stone carvings. Backed by durable machine construction and exceptional after-sales support, AccTek CNC is the ideal choice for those seeking superior quality and efficiency in CNC stone carving.