- 7-10 Min Read
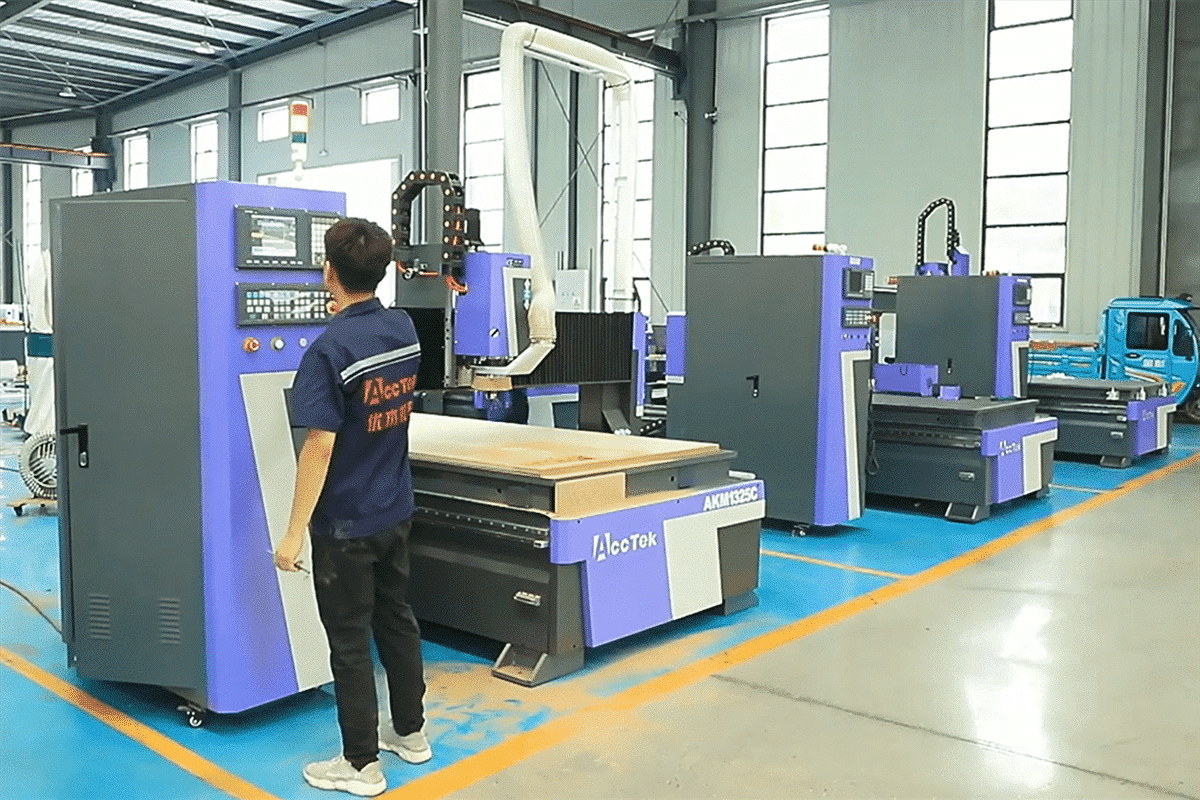
In the world of precision manufacturing, a CNC (Computer Numerical Control) router stands as a cornerstone for creating detailed, accurate parts. However, to harness the full potential of this versatile machine, proper calibration is a critical process. Calibration ensures that your CNC router operates with the utmost accuracy, reducing errors and increasing the quality of your output. This process involves fine-tuning the machine’s various components and settings to align perfectly with the intended design specifications. Whether you are a seasoned professional or a newcomer to CNC technology, mastering these calibration techniques will significantly enhance the precision and efficiency of your work.
This guide will walk you through the crucial steps of calibration, ensuring each axis and component operates at its peak potential. From aligning mechanical parts to fine-tuning software settings, you’ll learn how to transform your CNC router into a finely-tuned instrument, capable of delivering optimal performance for all your machining projects. By following these guidelines, you can maximize your CNC router’s accuracy and efficiency, ultimately improving your overall productivity and the quality of your projects.
The Importance of Calibration in CNC Routing
Calibration is a foundational aspect of CNC routing that impacts every aspect of the machining process, from accuracy and consistency to safety and efficiency. Regular and precise calibration ensures that the CNC router operates at its best, producing high-quality parts and maintaining optimal performance. Here are details of the importance of calibration in CNC routing.
- Accuracy and Precision: Calibration ensures that the CNC router cuts materials to the exact specifications set in the design. Even small errors in calibration can lead to significant discrepancies in the final product, resulting in parts that do not fit together correctly or do not meet the required tolerances.
- Consistency: Calibration ensures that the CNC router can consistently produce identical parts in repeated cycles, maintaining uniformity across production runs.
- Surface Finish and Quality: Proper calibration minimizes errors such as chatter, tool marks, and irregularities, leading to higher-quality finishes. A well-calibrated machine will produce clean cuts with smooth edges, reducing the need for additional finishing work.
- Efficiency and Productivity: Accurate cuts mean less material waste, which translates to cost savings and more efficient use of resources. When a CNC router is properly calibrated, it reduces the likelihood of rework and adjustments, thereby saving time and increasing overall productivity.
- Tool Life and Maintenance: Proper calibration helps in maintaining the health of the cutting tools and the machine itself. By ensuring theCNC router operates correctly, calibration reduces the wear and tear on the tools, leading to longer tool life and less frequent replacements. It also minimizes the risk of damage to the machine, reducing downtime and maintenance costs.
- Quality Control: Calibration is an integral part of quality control in CNC routing. It ensures that each part meets the quality standards required for the application. High-quality products enhance customer satisfaction and reduce the rate of returns and rework.
- Safety: A properly calibrated CNC router operates more safely. Incorrect calibration can lead to unexpected movements or errors during operation, which can be hazardous to operators. Ensuring the machine is correctly calibrated minimizes the risk of accidents.
- Troubleshooting and Diagnostics: Regular calibration can help identify potential issues with the CNC router before they become significant problems. By routinely checking and calibrating the machine, operators can spot irregularities early and address them promptly, preventing costly repairs and prolonged downtime.
Step-by-step Guide to Calibrating a CNC Router
Calibrating a CNC router is a meticulous process that ensures your machine operates with the highest level of accuracy, precision, and efficiency. Here’s a step-by-step guide to help you calibrate your CNC router for optimal performance:
Initial Machine Check
- Check the Frame and Base: Ensure the machine’s frame and base are stable and free from any visible cracks or damage. Use a spirit level to confirm that the base is perfectly level. Adjust the feet or base supports as needed.
- Inspect Rails and Bearings: Look for any signs of wear, debris, or damage on the linear rails and bearings. Clean and lubricate if necessary.
- Look for Wear and Tear: Examine the spindle and tool holder for any signs of wear, and ensure the tool is held securely.
- Checking for Loose Fasteners and Connections: Check all bolts, screws, and other fasteners on the machine frame, gantry, and moving components. Tighten any that are loose.
Axis Calibration
- X, Y, Z Axis Calibration: Ensure the machine is on a stable, level surface. Check for any physical obstructions that might affect movement. Most CNC routers come with software that can assist in calibrating the axes. Input the desired and actual travel distances to calculate the correction factors.
- Rotation Axis Calibration: Align the rotation axis (often referred to as the A-axis or fourth axis) parallel to the X or Y axis, depending on the machine design. Use precision fixtures or jigs to ensure the workpiece is correctly positioned relative to the rotation axis.
Ball Screw and Lead Screw Calibration
- Ball Screw or Lead Screw Pitch Verification: Measure the pitch of the ball screw or lead screw (distance between threads) using precise tools like a micrometer or pitch gauge. Command the CNC to move a specific distance and measure the actual travel. Compare this with the expected travel to identify discrepancies.
- Ball Screw Lubrication and Maintenance: Regularly lubricate the ball screws according to the manufacturer’s recommendations. Use appropriate lubricants (grease or oil) specified for your machine. Apply lubrication either manually or through an automatic lubrication system if equipped. Ensure even coverage along the entire screw length.
Spindle Calibration
- Calibration of Spindle Speed: Using a tachometer to measure the actual spindle speed and compare it to the set speed on the CNC control panel. Fine-tuning the spindle speed parameters in the CNC software if discrepancies are found, ensuring the actual speed matches the programmed speed.
- Tool Length Calibration: Using a tool setting probe or touch-off device to automatically measure the tool length. In the absence of a probe, manually measure the tool length using a caliper and input the data into the CNC system.
Toolpath and G-code Verification
- Tool Path Simulation: Using CAD/CAM software to create a virtual representation of the tool path, verifying that the programmed path aligns with the intended design. Modifying feed rates, cutting speeds, and tool paths based on simulation results to optimize performance and avoid errors.
- Trial Run and Trial Cutting: Running the CNC router with the spindle turned off to ensure the machine follows the expected tool path accurately. Making any last adjustments based on the trial cut results to ensure optimal performance in actual production runs.
Home and Limit Switch Calibration
- Home Cycle Calibration: Use the CNC control software to define the exact home position. This typically involves moving the machine to a specific point and setting this as the home in the software. After setting the home position, run a few test cycles to ensure the machine consistently returns to the exact home position. This can involve marking the start point and checking the machine returns to this point after several cycles.
- Limit Switch Calibration: Manually trigger each limit switch to ensure it is properly positioned. Adjust the mounting if necessary so that each switch activates before the machine reaches its mechanical limits. Use the CNC software to move the machine slowly towards the limit switches and observe if the machine stops correctly. Adjust the switch positions if the machine doesn’t stop accurately at the desired points.
Temperature Compensation
- Heat Effects on Calibration: CNC routers, like any other machines, are affected by heat which can cause materials to expand or contract, impacting precision. For example, the spindle motor generates heat which can cause the spindle itself to expand, slightly altering the tool length.
- Temperature Monitoring and Control: Install temperature sensors on key components such as the spindle, the machine frame, and the work environment. These sensors can provide real-time data on temperature variations. Regularly check the temperature readings and ensure the cooling systems are functioning correctly. Log temperature data to identify trends and make necessary adjustments.
Document Record Keeping
- Develop Calibration Documentation: Develop a detailed document outlining the step-by-step procedure for calibrating a CNC router. Document all measurement results during the calibration process, including deviations from the desired specifications.
- Documentation Storage: Store all calibration documents digitally for easy access, searchability, and backup. If necessary, keep physical copies in a secure, organized location.
Regular Maintenance and Recalibration
- Scheduled Maintenance Tasks: Establish a regular maintenance schedule for the CNC router, including tasks such as cleaning, lubrication, and inspection of mechanical components.
- Periodic Recalibration: Schedule regular recalibration intervals based on usage frequency and environmental factors. This ensures that the machine remains accurate and reliable over time.
Operator Calibration Training
Operator training is an important step to ensure correct CNC router calibration. Effective training programs should cover a range of topics to ensure operators are well-versed in the calibration process, safety protocols, and troubleshooting techniques. Here’s a comprehensive outline of the training that should be provided:
- Understanding CNC Routers: Operators should be familiar with the basic functions and components of CNC routers, including the spindle, cutting tools, worktable, and control panel.
- Safety Training: Proper use of safety gear such as goggles, ear protection, and gloves. Understanding emergency stop procedures, safe handling of materials, and awareness of potential hazards.
- Software Training: Basic training on G-code and other CNC programming languages used to operate and calibrate the CNC router. Familiarity with CAD (Computer-Aided Design) and CAM (Computer-Aided Manufacturing) software used to design parts and generate toolpaths.
- Calibration Procedures: Proper setup of the CNC router, including aligning the workpiece, setting zero points, and securing the material. Ensuring fixtures and jigs are correctly positioned and secured to maintain accuracy during operation.
- Measurement and Inspection Techniques: Proficiency in using calipers, micrometers, dial indicators, and other precision measuring tools to check the dimensions of parts and ensure they meet specifications. Understanding quality control procedures to verify that the calibration has been performed correctly and that the CNC router produces parts within tolerances.
- Maintenance and Troubleshooting: Regular maintenance tasks such as cleaning the machine, lubricating moving parts, and checking for wear and tear. Identifying and resolving common calibration issues such as misalignment, tool wear, and software errors.
- Practical Training and Hands-On Experience: Hands-on training sessions where operators practice calibrating the CNC router under supervision. This includes setting up the machine, running test cuts, and making adjustments based on the results. Simulating real-world scenarios and troubleshooting exercises to build confidence and problem-solving skills.
- Advanced Calibration Techniques: Learning about advanced toolpath strategies and how they affect calibration and overall machining accuracy. Keeping up-to-date with the latest machine upgrades and software updates that may affect calibration procedures.
- Ongoing Education and Refresher Courses: Periodic training updates to reinforce skills and introduce new techniques or tools. Establishing systems for operators to provide feedback on training effectiveness and suggest improvements.
Effective training for CNC router operators on calibration encompasses a mix of theoretical knowledge and practical skills. By covering these areas comprehensively, operators will be well-prepared to perform CNC router calibration accurately and efficiently. This structured training approach not only enhances the skill level of the operators but also contributes to the overall quality and consistency of the machining process.
Summarize
The calibration of a CNC router is not merely a routine task but a fundamental aspect of optimizing its performance and ensuring the highest quality output. By adhering to meticulous procedures, maintaining thorough documentation, and investing in ongoing training, operators can uphold the precision and reliability of the machine. Consistent calibration fosters efficiency, reduces downtime, and ultimately contributes to the success of machining operations. With a commitment to precision and excellence, coupled with a proactive approach to calibration, CNC routers can consistently deliver exceptional results, meeting the demands of modern manufacturing with precision and reliability.
AccTek CNC is a well-known CNC router manufacturer and supplier in China. Whether you’re seeking precision in woodworking, metalworking, plastics machining, or other industries, we have the expertise and solutions to meet your needs. AccTek CNC is committed to delivering quality, reliability, and efficiency in every aspect of our products and services. Contact us today, and let us help you increase workshop productivity with precise CNC router equipment.