- 10-14 Min Read
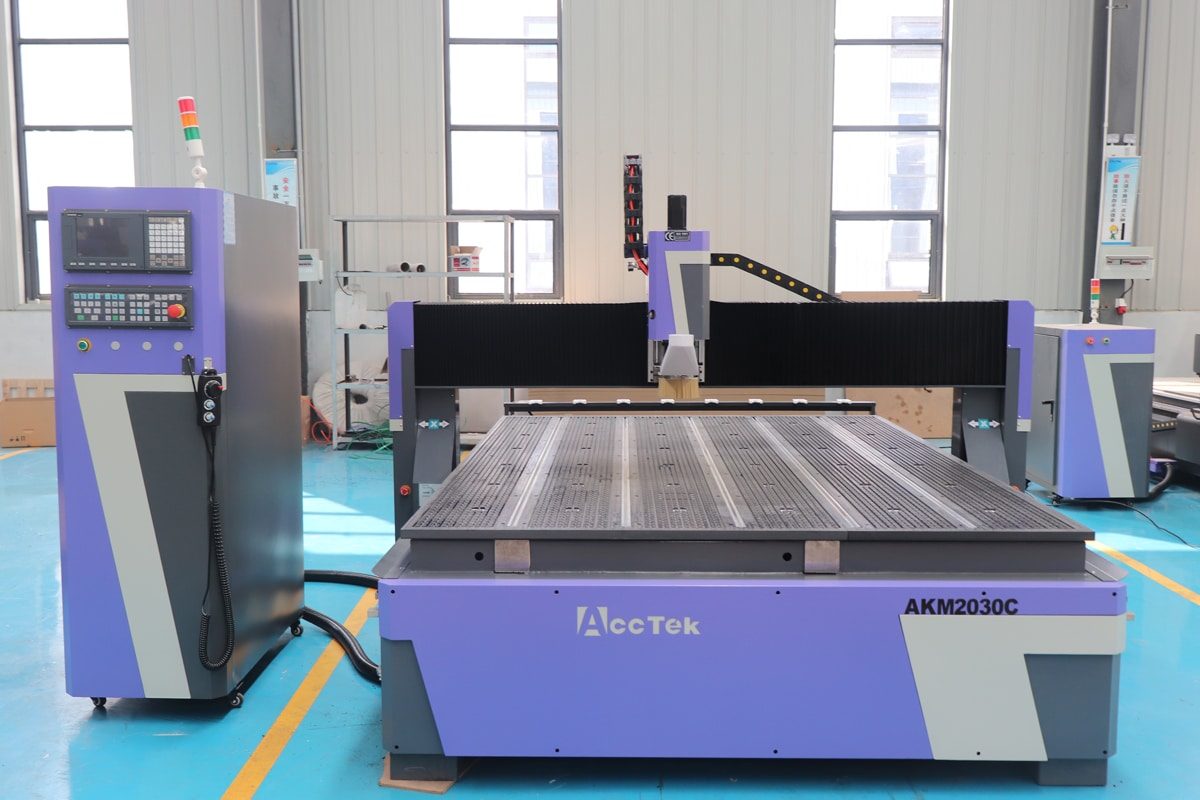
When operating a CNC router, achieving a balance between speed and precision is beneficial for efficiency and high-quality results. One of the key parameters that directly impacts cutting performance is the feed rate, the speed at which the cutting tool moves through the material. Selecting the correct feed rate ensures a smooth cut and extends tool life. However, calculating the optimal feed rate requires understanding various factors.
In this guide, we will break down the key elements that influence feed rate, introduce the standard formula for calculation, and provide practical tips to help you fine-tune your CNC router settings. Whether you’re cutting wood, plastic, or metal, knowing how to determine the right feed rate will improve both productivity and accuracy in your CNC operations.
Understanding Feed Rate in CNC Routing
What is Feed Rate?
A CNC router is a computer numerical control (CNC) machine that is used for tasks such as cutting out parts, creating intricate designs, and producing prototypes. The term “CNC” refers to the computerized control of the machine, allowing precise and automated movement of the cutting tool or router bit. Here we introduce you to its basic information.
Importance of Feed Rate in CNC Routing
Selecting the correct feed rate is beneficial for achieving high-quality machining results. It affects:
- Cut Quality & Surface Finish: A well-optimized feed rate ensures smooth edges and prevents burn marks or chatter. Too slow a feed rate can cause excessive tool wear, while too fast a feed rate may lead to rough cuts and inaccuracies.
- Tool Life & Wear: An incorrect feed rate can cause excessive tool wear or even tool breakage. Maintaining an optimal feed rate helps extend the life of the cutting tool, reducing replacement costs.
- Machining Efficiency: Faster feed rates increase production speed, but must be balanced with spindle speed and material characteristics. A properly calculated feed rate reduces downtime and enhances workflow.
- Heat Generation & Chip Evacuation: Incorrect feed rates can lead to excessive heat buildup, damaging both the tool and the workpiece. Proper feed rates ensure efficient chip removal, preventing clogging and improving cutting performance.
The Relationship Between Feed Rate, Spindle Speed, and Depth of Cut
Feed rate is closely linked to spindle speed (RPM) and depth of cut (DOC). These three parameters must be balanced to achieve optimal cutting performance:
- Spindle Speed (RPM): The number of revolutions the cutting tool makes per minute. Higher RPMs require higher feed rates to prevent excessive heat buildup.
- Depth of Cut (DOC): The amount of material removed in one pass. A deeper cut generally requires a slower feed rate to prevent tool overload.
- Feed Rate (IPM or mm/min): The speed at which the tool advances through the material, which determines the material removal rate.
Adjusting these parameters properly ensures a smooth and efficient cutting process while preventing tool damage or material defects.
The Role of Chip Load in Feed Rate Calculation
Chip load refers to the amount of material removed per flute per revolution. It directly affects feed rate calculations and is influenced by:
- The material being cut (wood, plastic, metal, etc.).
- The type and number of flutes on the cutting tool.
- The spindle speed and overall machine power.
A properly calculated chip load ensures optimal tool engagement with the material, leading to efficient cutting and prolonged tool life.
Understanding feed rate in CNC routing is beneficial for maintaining precision, efficiency, and durability in machining operations. The next section will explore the key factors that influence the ideal feed rate for different CNC applications.
Key Factors Affecting CNC Router Feed Rate
When determining the optimal feed rate for a CNC router, several factors must be considered to ensure efficiency, precision, and tool longevity. Below are the key factors that affect the CNC router feed rate:
Material Properties
Different materials have varying hardness, density, and machinability, which impact how fast the cutting tool can move through them. Key considerations include:
- Soft Materials (Wood, MDF, Plastics): Supports higher feed rates due to lower cutting resistance. Require careful feed rate adjustments to avoid excessive heat buildup (melting in plastics or burning in wood).
- Hard Materials (Metals such as Aluminum, Brass, Stainless Steel): Require slower feed rates to prevent tool wear and overheating. Metals like aluminum allow for faster feed rates compared to harder materials like stainless steel.
- Composite Materials (Carbon Fiber, Laminates): Need controlled feed rates to prevent delamination and excessive tool wear. Specialized tooling, such as diamond-coated bits, may be required.
Tool Selection
The choice of cutting tool significantly impacts the feed rate, as different tools are designed for varying levels of material removal and cutting conditions. Key considerations include:
- Tool Diameter: Larger diameter tools can handle higher feed rates because they are more rigid and dissipate heat better. Smaller tools require lower feed rates to prevent breakage.
- Number of Flutes: Tools with fewer flutes allow for higher chip loads and are ideal for softer materials like wood and plastic. Tools with more flutes require lower feed rates and are suited for metals where fine finishes are needed.
- Tool Material & Coating: Coated tools (TiN, TiAlN, etc.) reduce friction and improve tool longevity, allowing for more aggressive feed rates. Carbide tools last longer and support higher feed rates compared to high-speed steel (HSS) tools.
- Cutting Edge Geometry: Specialized tool designs, such as compression bits for plywood or down-cut bits for clean surface finishes, affect the optimal feed rate for a given operation.
Machine Capabilities
Considering machine capabilities ensures a balance between speed and precision without overloading the system. Factors to consider include:
- Spindle Power and Speed (RPM): A high-powered spindle can sustain higher feed rates without stalling. The RPM must be balanced with the feed rate to maintain proper chip load and cutting efficiency.
- Machine Rigidity and Stability: Industrial CNC routers with heavy-duty frames support higher feed rates due to reduced vibrations. Light-duty or hobbyist CNC routers require slower feed rates to maintain accuracy.
- Drive System and Motion Control: CNC routers with servo motors and high-precision ball screws can handle higher feed rates with consistent accuracy. Machines with stepper motors and belt-driven systems may require lower feed rates to avoid backlash and inaccuracies.
Cutting Strategies
The specific cutting technique used in the CNC process also influences the optimal feed rate. Different strategies require different approaches:
- Profiling and Contour Cutting: Moderate feed rates for smooth edge finishes. Single-pass cutting requires slower speeds, while multiple shallow passes allow for higher feed rates.
- Pocketing and Engraving:
- Lower feed rates for intricate cuts and detailed engravings. Higher feed rates may be possible with shallow step-down values.
- Roughing Cuts: Higher feed rates are used to remove material quickly before finishing passes. It can be optimized using adaptive toolpaths to maintain a consistent chip load.
- Finishing Cuts: Slower feed rates improve surface quality. Tool engagement is reduced to ensure precision without excessive force.
Optimizing the feed rate of a CNC router requires careful consideration of tool selection, material properties, machine capabilities, and cutting strategies. Balancing these factors ensures efficient machining, extended tool life, and high-quality results. By understanding and adjusting these variables, CNC operators can achieve optimal cutting performance while preventing tool wear and machining defects.
Basic Feed Rate Calculation for CNC Routing
To determine the optimal feed rate for a CNC router, the following standard formula is used:
Feed Rate=RPM×Number of Flutes×Chip Load
Here, feed rate (IPM or mm/min) is the speed at which the tool moves through the material. RPM (revolutions per minute) is the spindle speed of the cutting tool. The number of flutes is the number of cutting edges on the tool. Chip load (inches or mm per flute) is the amount of material removed per flute per revolution.
Step-by-Step Guide to Feed Rate Calculation
- Determine Spindle Speed (RPM): The spindle speed depends on the material and cutting tool being used. Typical values can be found in manufacturer guidelines or CNC cutting charts.
- Identify the Number of Flutes: The number of flutes on the cutting tool influences how much material is removed per revolution. Common tools have 1, 2, 3, or more flutes.
- Find the Recommended Chip Load: Chip load values vary based on material type and tool diameter. These values can be obtained from tooling manufacturer recommendations.
- Apply the Formula: Plug the values into the formula to calculate the feed rate.
Example Calculation
- Material: Hardwood
- Tool: ¼-inch (6.35mm) end mill with 2 flutes
- Spindle Speed (RPM): 18,000 RPM
- Recommended Chip Load: 0.005 inches per flute
Calculation: Feed Rate=18,000×2×0.005=180IPM. So, the recommended feed rate is 180 inches per minute (IPM).
Adjustments for Optimal Performance
- Higher feed rates may be used for soft materials like MDF or plastics.
- Lower feed rates are recommended for hard materials like aluminum or stainless steel.
- If the tool is overheating, increase feed rate or decrease spindle speed.
- If the cut is too rough, reduce feed rate slightly for better control.
By following these basic calculations and adjustments, CNC router operators can optimize feed rate settings for efficient, precise, and high-quality machining.
Using Feed Rate Calculators and Software
Determining the optimal feed rate manually can be time-consuming and prone to errors. To simplify the process, CNC router operators often use feed rate calculators and specialized software to achieve precision and efficiency. These tools automatically calculate the ideal feed rate based on material properties, tooling specifications, and machining conditions.
Benefits of Using Feed Rate Calculators and Software
Utilizing a feed rate calculator or CNC software provides several advantages:
- Accuracy & Consistency: Eliminates guesswork and ensures proper calculations based on predefined parameters.
- Time Efficiency: Saves time compared to manual calculations, enabling faster setup.
- Material Optimization: Reduces waste by ensuring proper cutting speeds and feed rates.
- Tool Longevity: Prevents premature tool wear by maintaining correct chip loads.
- Enhanced Surface Finish: Improves cut quality by optimizing cutting parameters.
Common Feed Rate Calculators and Software
Several CNC software programs and online tools help in calculating the optimal feed rate.
Online Feed Rate Calculators
Many manufacturers and CNC communities offer free online feed rate calculators where users input key parameters. Popular online calculators include:
- G-Wizard Calculator (by CNC Cookbook)
- FSWizard
- HSMAdvisor
- Manufacturers’ Feed Rate Charts (offered by brands like Amana Tool, Speeds & Feeds, and Harvey Tool)
CNC Software with Built-in Feed Rate Calculation
Most modern CNC software packages include automatic feed rate calculation features. These allow users to input cutting conditions and receive optimal parameters. Examples include:
- Fusion 360: Advanced CAM software with automatic feed rate optimization.
- VCarve Pro: Ideal for CNC routing with built-in speeds and feeds control.
- Mastercam: Industry-standard software for feed rate calculation and toolpath generation.
- SolidCAM & HSMWorks: High-efficiency machining (HEM) software with automatic feed and speed adjustment.
How to Use a Feed Rate Calculator
Follow these steps to calculate the optimal feed rate using a feed rate calculator:
- Input Tool Information: Select the tool diameter and number of flutes from your tool database. Specify the tool material (carbide, high-speed steel, etc.).
- Select Material Type: Choose the workpiece material (wood, aluminum, stainless steel, plastic, etc.).
- Enter Cutting Parameters: Define spindle speed (RPM) based on manufacturer recommendations. Set the depth of cut (DOC) and width of cut (WOC). Choose the desired chip load per flute (often provided in material-specific charts).
- Calculate the Feed Rate: Click “Calculate” to generate the recommended feed rate in inches per minute (IPM) or millimeters per minute (mm/min).
Adjustments & Real-Time Monitoring
Even with software assistance, feed rates may require fine-tuning during operation. Consider the following:
- Monitor Cutting Sounds: A smooth, steady sound indicates proper settings, while chattering or screeching suggests adjustments are needed.
- Check Chip Formation: Properly sized chips indicate correct feed rates, while dust-like chips may mean the feed rate is too low.
- Adjust for Machine Rigidity: Softer machines may require slower feed rates compared to industrial-grade CNC routers.
CNC software ensures precision, efficiency, and tool longevity. Whether using an online calculator or advanced CAM software, automating feed rate calculations improves machining quality, reduces tool wear, and enhances overall productivity.
Practical Tips for Feed Rate Optimization
Optimizing the feed rate in CNC routing involves starting with manufacturer recommendations, testing gradually, monitoring chips and sounds, and adjusting for different materials and machine capabilities. Below are practical tips to help CNC operators adjust and fine-tune the feed rate for the best machining results.
Start with Manufacturer Recommendations
- Use tool manufacturer’s speed and feed charts as a baseline.
- Follow material-specific guidelines for chip load, RPM, and feed rate.
- Adjust settings based on real-time cutting conditions.
- Example: If a tool manufacturer suggests a chip load of 0.005 inches per tooth for aluminum with a 2-flute end mill at 15,000 RPM, the feed rate calculation would be: Feed Rate=15,000×2×005=150 IPM
Use Test Cuts and Gradual Adjustments
- Start with a conservative feed rate and gradually increase it.
- Run test cuts on scrap material before full production.
- Make small 5-10% incremental changes to find the optimal speed.
- Example: If a feed rate of 100 IPM seems too aggressive, reduce it in steps of 10 IPM until the cut quality improves.
Monitor Chip Formation
- Proper chip formation indicates an optimized feed rate.
- Dust-like particles: Feed rate is too low, causing rubbing.
- Thick, heavy chips: Feed rate is too high, overloading the tool.
- Tip: Adjust the feed rate to maintain medium-sized, curled chips, ensuring efficient material removal without excessive heat buildup.
Listen to Cutting Sounds
- Smooth, steady cutting noise: Optimal feed rate.
- Screeching or whining: Feed rate too low, causing tool friction.
- Chattering or banging: Feed rate too high, leading to tool deflection.
- Tip: Gradually adjust feed rate while listening to the sound of the cut to maintain stability and minimize tool wear.
Adjust Feed Rate Based on Material Type
- Softwood, MDF, Plastics: Use higher feed rates to prevent burning.
- Hardwoods: Moderate feed rates to avoid tool overheating.
- Aluminum & Soft Metals: Increase feed rate slightly to ensure proper chip evacuation.
- Steel & Hard Metals: Use lower feed rates to minimize tool wear and excessive heat.
- Tip: For dense or abrasive materials, lower the feed rate and use carbide-coated tools for longevity.
Consider Tool and Machine Capabilities
- Larger tool diameters can handle higher feed rates.
- More rigid CNC routers support faster feed rates with better accuracy.
- Hobbyist or desktop CNC routers require lower feed rates to avoid flex and inaccuracies.
- Tip: If using a lightweight CNC router, reduce the feed rate by 10-20% compared to industrial machines.
Balance Feed Rate with Spindle Speed (RPM)
- Higher RPMs require higher feed rates to maintain proper chip load.
- Lower RPMs need slower feed rates to prevent tool overload.
- Keep the ratio balanced to avoid excessive heat buildup or premature tool wear.
- Example: For a ¼-inch (6.35mm) 2-flute end mill cutting wood at 18,000 RPM, a proper feed rate should be around 150-180 IPM to maintain efficiency.
Optimize Cutting Strategies for Efficiency
- Use adaptive toolpaths to maintain consistent chip load.
- Reduce depth of cut (DOC) for higher feed rates.
- Consider climb milling instead of conventional milling for smoother cuts.
- Example: In roughing operations, increase the feed rate and reduce the cutting depth to remove material quickly while minimizing tool wear.
Monitor Tool Wear and Surface Finish
- Uneven tool wear suggests the feed rate is too aggressive.
- Burn marks or rough edges indicate improper feed settings.
- Check the tool condition after each job to determine if adjustments are needed.
- Tip: For longer tool life, optimize feed rate to prevent excessive wear while maintaining high material removal rates.
By fine-tuning feed rates in real-time and leveraging cutting strategies, CNC router operators can achieve higher efficiency, better surface finishes, and extended tool life.
Summarize
Calculating the feed rate of a CNC router is a critical step in optimizing machining performance, ensuring high precision, and extending tool life. By understanding the relationship between RPM, number of flutes, and chip load, operators can determine an ideal feed rate that balances speed and accuracy. Utilizing feed rate formulas, manufacturer recommendations, and real-time adjustments based on cutting feedback allows for improved efficiency and reduced tool wear. With a well-calculated feed rate, CNC operators can achieve smoother cuts, faster production, and enhanced machine longevity, leading to better overall machining outcomes.
AccTek CNC, a professional CNC router manufacturer in China, offers high-precision and efficient machines designed to optimize feed rate calculations for superior machining performance. Whether cutting wood, plastics, or metals, AccTek CNC ensures smooth, precise, and high-speed machining, reducing tool wear while maximizing productivity. For businesses seeking reliable, high-performance CNC routers, AccTek provides high-quality machines to help businesses maximize productivity.