- 12-17 Min Read
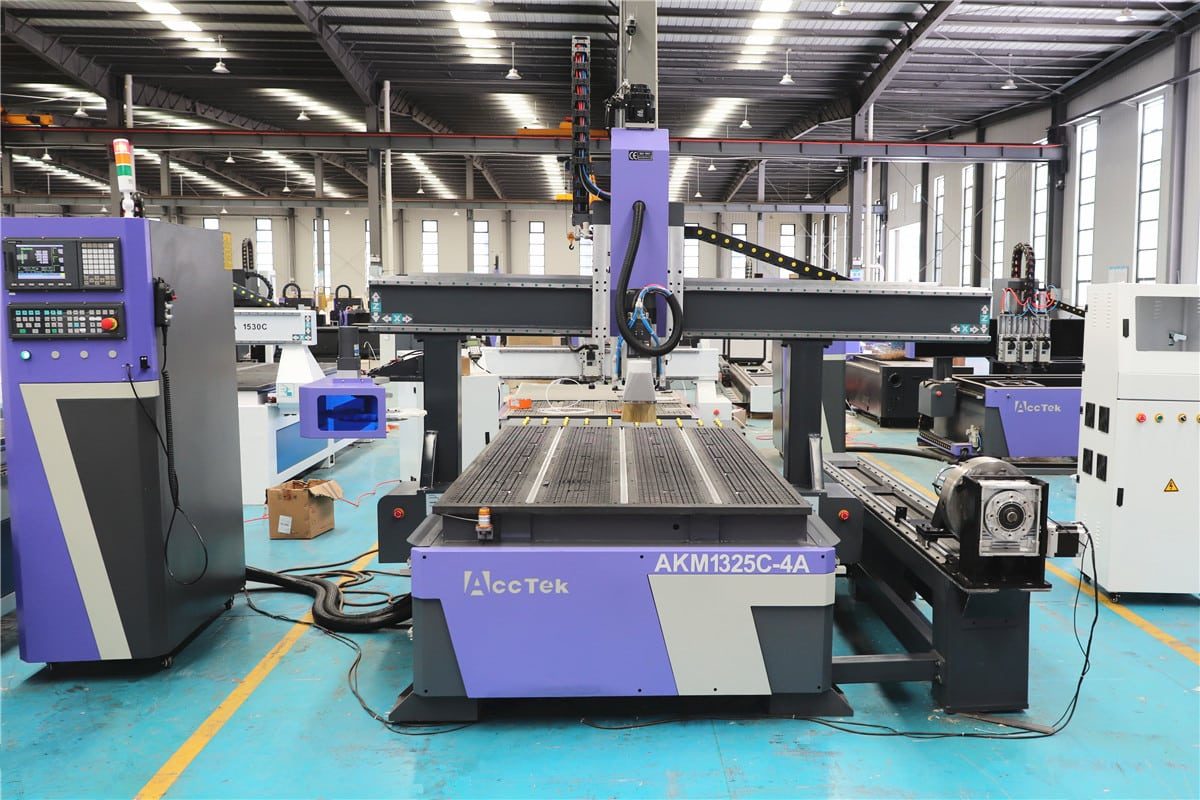
When selecting a CNC router, users often face the challenge of balancing cost and functionality, particularly when working within budget constraints. The decision-making process involves carefully evaluating the machine’s capabilities, against the financial investment required. This delicate balancing act requires users to prioritize essential features that align with their specific needs while making strategic compromises to stay within their financial limits.
In this article, we explore the strategies and considerations that guide users as they navigate the trade-offs between cost and functionality when selecting a CNC router. From prioritizing key features to understanding the long-term implications of their investment, users must make informed decisions that align with both their technical needs and budgetary realities. By examining these factors, we aim to provide insights that can help businesses make the best possible choice, ensuring they invest in a CNC router that delivers both quality and value without exceeding their budget.
Understand the significance of CNC router in modern manufacturing
The significance of CNC routers in modern manufacturing is profound, as they have revolutionized how products are designed, produced, and customized. We explain this in the following two parts:
The Evolution of CNC Routers
CNC routers have undergone significant advancements since their inception, fundamentally changing the manufacturing industry. Initially, manufacturing relied heavily on manual labor and traditional machining methods, which were time-consuming and prone to human error. The introduction of CNC technology marked a shift towards automation, allowing for precise control of cutting tools through computer programming.
Over the years, CNC routers have evolved into highly sophisticated machines that offer enhanced precision, speed, and versatility. This evolution has enabled manufacturers to produce complex designs with minimal waste, improve product consistency, and reduce production time. The continuous development of CNC routers, including advancements in software and hardware, has made them an integral part of modern manufacturing, driving efficiency and innovation.
The Diversified Applications of CNC Routers
In addition to their technological evolution, CNC routers have found diversified applications across various industries, further highlighting their significance in modern manufacturing. From crafting detailed furniture pieces in the woodworking industry to manufacturing signage for the advertising industry, CNC routers are now integral to a wide array of production processes. Their ability to work with multiple materials—such as wood, plastic, metal, and composites—makes them highly adaptable to different manufacturing needs.
This versatility allows businesses to innovate and expand their product offerings, meeting the demands of custom orders, small-batch production, and complex designs that require meticulous attention to detail. As a result, CNC routers have become a critical tool for companies seeking to stay competitive in an increasingly dynamic and diverse market.
The significance of CNC routers in modern manufacturing lies in their evolution, which has brought about greater precision and efficiency, and their diversified applications, which have expanded the capabilities of manufacturers across multiple industries. Their impact is evident across various industries, making them a cornerstone of contemporary production processes.
Budget Constraints in CNC Router Selection
Budget constraints in CNC router selection refer to the financial limitations that a business or individual faces when choosing a machine. These constraints dictate the maximum amount that can be spent on acquiring a CNC router. Understanding budget constraints also means recognizing the long-term implications of the investment, ensuring that the chosen CNC router delivers value over time without compromising on the quality or efficiency required for the specific manufacturing tasks at hand.
The Importance of Manufacturing Budget
The manufacturing budget is a critical factor in CNC router selection, as it dictates the range of options available to a business. Allocating a sufficient budget for a CNC router ensures that you can invest in a machine that meets your production requirements, offers reliability, and has the potential for long-term value. A well-planned budget allows for the consideration of essential features such as machine size, power, precision, and software compatibility, which are necessary to achieve the desired quality and efficiency in production. Additionally, a thoughtful budget helps in balancing the initial investment with long-term operational costs, ensuring that the chosen CNC router contributes positively to the overall profitability of the manufacturing process.
Common Budget Constraints
Common budget constraints in CNC router selection typically include the following aspects:
- Initial Purchase Cost: The upfront cost of purchasing a CNC router is often the most significant budget constraint. Businesses with limited budgets may need to prioritize essential features and opt for a more basic model, potentially sacrificing advanced capabilities or automation features.
- Operational and Maintenance Costs: Beyond the initial purchase, ongoing costs such as power consumption, tooling, software updates, and routine maintenance must be considered. Budget constraints may limit the ability to choose a machine with lower operational costs or one that requires less frequent maintenance, which could lead to higher long-term expenses.
- Customization and Upgrades: Budget limitations may restrict the ability to customize the CNC router or invest in future upgrades. This can impact the machine’s adaptability to evolving production needs, potentially requiring additional investment sooner than anticipated.
- Financing Options: Businesses may face constraints in financing options, such as limited access to credit or higher interest rates, which can affect the total cost of ownership. Budget constraints might lead to choosing less favorable financing terms or selecting a lower-cost machine to avoid financing altogether.
Understanding these budget constraints and their impact on CNC router selection helps businesses make informed decisions, ensuring that the chosen machine aligns with both current manufacturing needs and long-term financial goals.
Factors that influence CNC router selection cost and functionality
Several key factors influence the cost and functionality of a CNC router, shaping the decision-making process for users who need to balance budgetary constraints with performance requirements. These factors include:
- Machine Size and Structure: The physical size of the CNC router and the robustness of its structure significantly impact both cost and functionality. Industrial CNC routers that can handle bigger workpieces or materials tend to be more expensive but offer greater flexibility in terms of the range and scale of projects that can be undertaken. A well-built, sturdy machine structure ensures better stability and precision, which is beneficial for high-quality output, but it also adds to the cost.
- Spindle Power and Tooling: The spindle is the heart of the CNC router, and its power determines the machine’s capability to cut through different materials efficiently. A more powerful spindle can work with harder materials like metals and operate at higher speeds, which enhances productivity but increases the overall cost. Additionally, the type and quality of tooling, such as bits and cutters, affect the machine’s precision and the quality of the finished product, with higher-end tooling adding to the cost.
- Control System and Software: The sophistication of the control system and the accompanying software also plays a pivotal role in CNC router selection. Advanced control systems that offer greater precision, ease of use, and compatibility with various design software can enhance productivity and reduce the learning curve for operators. However, such systems are typically more expensive, requiring users to assess whether the additional functionality justifies the increased cost.
- Material Compatibility and Versatility: A CNC router’s ability to work with a wide range of materials—such as wood, plastic, metal, and composites—affects its versatility and, consequently, its cost. CNC routers designed to handle a wider variety of materials are generally more expensive but offer greater functionality, allowing users to take on a broader range of projects.
- Precision and Accuracy: The level of precision and accuracy that a CNC router can achieve affects the quality of the finished product. High-precision CNC routers use advanced technologies such as linear guides, ball screws, and high-resolution encoders, which improve accuracy but also raise the cost. The ability to consistently produce parts with tight tolerances is a key factor in the machine’s functionality, making precision a significant consideration in the selection process.
- Maintenance and Operational Costs: Beyond the initial purchase price, the ongoing costs of maintaining and operating the CNC router also influence the overall cost. Machines that require frequent maintenance or have high energy consumption may be cheaper upfront but more costly over time. Users must factor in these long-term expenses when selecting a CNC router, especially if they are working within budget constraints.
- Brand and Warranty: The reputation of the brand and the warranty offered with the CNC router can also affect the selection process. Well-known brands with a track record of reliability may command higher prices, but they often provide better customer support, longer warranties, and more readily available spare parts. This can be a necessary consideration for users who prioritize long-term reliability and lower risk, even if it means a higher initial cost.
These factors collectively shape the balance between cost and functionality in CNC router selection, requiring users to carefully evaluate their specific needs and budget to make an informed decision.
Weighing cost and functionality
When selecting a CNC router, weighing the cost and functionality from different perspectives helps users make informed decisions that align with their budget and operational needs. Here’s how this evaluation process can be approached from four key perspectives:
Cost-Driven Decisions
In cost-driven decisions, the primary focus is on minimizing expenses while still obtaining a CNC router that meets basic requirements. Users operating under strict budget constraints may prioritize affordability, opting for a machine that offers essential functionalities at the lowest possible cost. This approach often involves making compromises on advanced features, brand reputation, or long-term durability to stay within financial limits. The challenge lies in ensuring that the selected machine can still perform effectively without leading to higher operational costs or frequent breakdowns in the future.
Feature Prioritization
Feature prioritization involves identifying the most critical functionalities required for specific applications and making them the focal point of the purchasing decision. Users assess which features—such as machine size, spindle power, or material compatibility—are absolutely necessary for their operations and are willing to allocate a larger portion of their budget to secure those capabilities. Less critical features may be sacrificed or downgraded to ensure that the key functionalities are not compromised. This perspective helps users focus on getting the most value for their money by ensuring that the CNC router can perform the tasks that are most important to their business.
Return on Investment (ROI) Analysis
ROI analysis evaluates the long-term financial benefits of a CNC router compared to its initial and ongoing costs. This perspective encourages users to consider how quickly the machine will pay for itself through increased productivity, reduced labor costs, or expanded capabilities that allow for new revenue streams. A higher upfront cost may be justified if the machine offers superior performance, reliability, and lower maintenance costs, leading to better profitability over time. ROI analysis can be used as a key evaluation method for companies that want to invest in CNC routers as a strategic asset to enhance their competitive advantage.
Customization Options
Customization options provide flexibility in tailoring a CNC router to specific operational needs, potentially impacting both cost and functionality. Users may opt for a base model and add features or accessories that are most relevant to their work, such as specialized tooling, enhanced control systems, or material handling capabilities. Customization allows for a more precise fit to the user’s requirements but can also increase costs. Balancing the benefits of customized features against the additional expense is beneficial to ensure that the final configuration delivers the desired functionality without unnecessarily inflating the budget.
Weighing cost and functionality is ultimately about making informed decisions that align with both immediate and long-term goals. By considering these four perspectives, users can make a well-rounded assessment that helps them choose a CNC router that meets their financial constraints while delivering the necessary capabilities for their operations.
Key considerations for CNC router cost analysis
When conducting a cost analysis for selecting a CNC router, it’s essential to consider various aspects that go beyond just the initial purchase price. Here’s how the analysis can be approached in terms of total cost of ownership, financing options, and the choice between used versus new machines:
Total Cost of Ownership (TCO)
Total Cost of Ownership (TCO) provides a comprehensive view of the long-term expenses associated with owning and operating a CNC router. Key considerations include:
- Initial Purchase Price: This is the starting point of the TCO, including the base price of the machine and any initial setup or installation costs.
- Maintenance and Repair Costs: Over time, the machine will require regular maintenance and potential repairs. These costs can vary depending on the machine’s build quality, frequency of use, and the availability of spare parts. Machines with lower upfront costs might have higher long-term maintenance expenses, which should be factored into the TCO.
- Operating Costs: This includes energy consumption, tooling replacement, and consumables like lubricants or coolant. A machine that is more energy-efficient or requires fewer consumables might have a lower TCO even if it’s more expensive initially.
- Depreciation: Understanding how the machine will depreciate over time is important for long-term cost analysis. Some machines may lose value quickly, while others may retain more of their value, which affects the overall TCO.
- Resale Value: The potential resale value of the machine at the end of its useful life can offset some of the TCO. Machines that hold their value better can reduce the net cost of ownership.
Financing Options
Financing options can significantly impact the cost analysis, making it possible to acquire a more expensive machine without straining cash flow. Key considerations include:
- Leasing vs. Purchasing: Leasing a CNC router allows businesses to spread out the cost over time, which can preserve capital and provide flexibility to upgrade to newer models. However, leasing might end up being more expensive in the long run compared to purchasing outright, especially when considering interest rates and lease terms.
- Loan Financing: Taking out a loan to purchase a CNC router can make a more expensive machine accessible. It’s important to compare interest rates, loan terms, and the overall cost of financing to determine if this option is cost-effective.
- Cash Purchase: While purchasing a machine outright with cash avoids interest payments, it requires a significant upfront investment. This option may be viable for businesses with sufficient capital and a strong cash flow, but it ties up funds that could be used for other operational needs.
Used Machines vs. New Machines
Choosing between a used or new CNC router is a critical decision that affects both cost and functionality. Key considerations include:
- Cost Savings: Used machines typically come at a lower purchase price, which can be appealing for businesses on a tight budget. This can allow access to higher-end features or models that would otherwise be unaffordable if bought new.
- Warranty and Support: New machines usually come with a manufacturer’s warranty and access to customer support, which can reduce the risk of unexpected repair costs and provide peace of mind. Used machines might not have this safety net, leading to higher potential costs if repairs are needed.
- Condition and Reliability: While well-maintained used machines can offer good value, there’s a risk of hidden issues that could lead to higher maintenance costs or downtime. A thorough inspection and assessment of the machine’s history are essential when considering a used option.
- Technological Advancements: New machines are likely to feature the latest technology, which can enhance productivity, efficiency, and precision. Used machines may lack these advancements, potentially limiting their functionality or compatibility with newer software and processes.
By carefully analyzing these factors, businesses can make informed decisions that align with their financial goals and operational needs, ensuring they select the CNC router that offers the best value over its entire lifespan.
Recommendations and best practices
When selecting a CNC router, focusing on thorough needs assessment, inter-departmental collaboration, and long-term planning can significantly enhance the decision-making process. Here are suggestions and best practices in these three areas:
Thorough Needs Assessment
- Engage Key Stakeholders: Involve team members from different departments who will be using or impacted by the CNC router, such as production, engineering, and maintenance. Their input can help identify essential features and potential challenges.
- Document Specific Requirements: Clearly define and document the machine’s required capabilities, such as material compatibility, precision levels, production volume, and specific processes it must handle. This helps avoid purchasing a machine that doesn’t fully meet your needs.
- Evaluate Current Processes: Assess existing production processes to understand how the CNC router will integrate. Identify any current inefficiencies that the new machine could address, and determine if additional processes or workflows will need to be adjusted.
- Consider Future Needs: While focusing on current requirements, consider how your needs might evolve. Choose a machine that offers flexibility and scalability to adapt to future production demands.
Inter-Departmental Collaboration
- Foster Open Communication: Establish clear communication channels between departments such as production, finance, and procurement. Regular meetings and updates ensure that everyone is on the same page regarding the CNC router selection criteria and progress.
- Align Goals and Expectations: Ensure that all departments understand the goals of acquiring a CNC router, such as improving production efficiency, reducing costs, or enhancing product quality. Aligning these goals helps prioritize features and avoid conflicts during the selection process.
- Involve IT and Maintenance Early: Include IT and maintenance teams early in the decision-making process. They can provide valuable insights into software compatibility, integration with existing systems, and maintenance requirements, helping to avoid technical issues down the line.
- Collaborate on Training Plans: Work together to develop a comprehensive training plan for operators and other staff members who will interact with the CNC router. Cross-departmental training can improve overall efficiency and reduce downtime.
Long-Term Planning
- Plan for Scalability: Select a CNC router that can scale with your business. Consider potential future expansions or shifts in production needs and choose a machine that can be upgraded or adapted as required.
- Budget for Total Cost of Ownership: Look beyond the initial purchase price and plan for the total cost of ownership, including maintenance, repairs, and potential upgrades. This approach ensures that the machine remains cost-effective over its entire lifecycle.
- Develop a Replacement Strategy: Consider the expected lifespan of the CNC router and develop a strategy for its eventual replacement. This includes planning for depreciation, potential trade-in values, and the impact of new technology on your operations.
- Set Up Continuous Monitoring and Evaluation: Implement a system to continuously monitor the CNC router’s performance and operational impact. Regular evaluations allow you to make data-driven decisions about maintenance, upgrades, or replacement, ensuring long-term efficiency and cost-effectiveness.
By focusing on these areas, you can ensure a more strategic and effective CNC router selection process, leading to better outcomes for your organization, and ensuring it meets your operational requirements now and in the future.
Summarize
Selecting a CNC router within budget constraints involves a careful evaluation of cost versus features to ensure that the machine meets essential operational needs without overspending. Users must prioritize core functionalities while making strategic compromises on less critical features. By balancing these factors, users can choose a CNC router that delivers the necessary performance and efficiency, all while staying within their financial limits. If you want to learn more about this, you can check out “Comprehensive CNC Router Buying Guide” and “Reviewing a CNC Router: Key Questions to Ask the Manufacturer”, which will give you more help.
For businesses seeking a reliable and tailored CNC router solution, AccTek CNC stands out as a well-known manufacturer in China, renowned for its expertise in customization. Whether you have a specific budget or unique processing requirements, we excel in recommending and customizing machines that perfectly align with your operational needs. With a commitment to quality and customer satisfaction, AccTek CNC ensures that you receive a CNC router that not only fits your financial constraints but also enhances your production efficiency and precision. Choose AccTek CNC for a machine that is truly built to meet your exact specifications.