- 12-16 Min Read
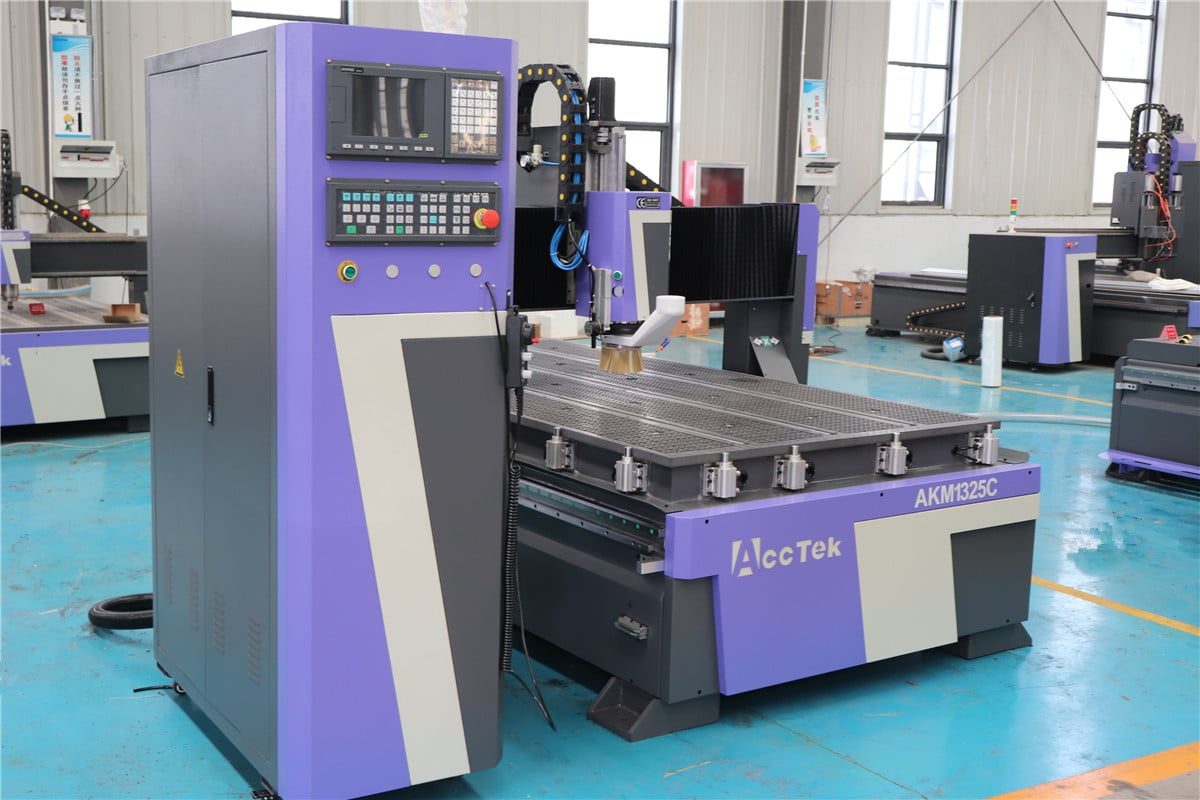
Choosing the right size and capacity for a CNC router is a pivotal decision that can greatly impact the efficiency and success of your machining operations. A well-sized CNC router ensures that you can handle your specific production needs without overloading the machine or wasting resources. However, determining the perfect fit involves careful evaluation of factors such as the types of materials you’ll be working with, the scale of your projects, and the complexity of your designs. Selecting a machine that is too small may result in limited production capabilities, while opting for one that is too large could lead to unnecessary costs and underutilization.
In this article, we’ll guide you through the key considerations when determining the appropriate size and capacity of a CNC router. Whether you’re working with wood, metals, or composites, understanding your machining requirements is beneficial for optimizing performance and maximizing your investment. From assessing your material dimensions to calculating the ideal production volume, this guide will help you make an informed decision that aligns with your specific machining needs.
Understanding CNC router size and capacity
When selecting a CNC router, understanding its size, capacity, and performance is key to optimizing its use for your specific machining needs. Before choosing the right machine, let’s first understand the basic information of CNC routers.
What is CNC Router Size?
CNC router size refers to both the overall dimensions of the machine and, more importantly, the size of the cutting bed or work area. The cutting bed defines the maximum dimensions of the materials you can process. CNC routers come in a range of sizes, from small desktop models with work areas as small as 24″ x 36″ (600 mm x 900 mm) to large industrial machines with cutting beds over 10′ x 20′ (3000 mm x 6000 mm). The machine’s size directly affects your ability to handle larger or more complex projects, as well as how much floor space the machine requires in your workspace.
Capacity and Performance
Capacity and performance in a CNC router refer to the machine’s ability to handle various materials and the thickness or depth it can cut. This is largely determined by the CNC router’s spindle power, Z-axis travel (vertical movement), and overall machine construction. A CNC router with a higher spindle power can cut through tougher and denser materials, such as metals, hardwoods, or composites, with greater ease. The Z-axis travel determines how thick the material can be. Performance factors like precision, cutting speed, and repeatability also play a role in how efficiently the machine can meet your production requirements. Machines with greater capacity often come with stronger motors and more robust components to ensure long-term reliability.
Types of CNC Routers
CNC routers come in several types, each designed for different applications and material sizes:
- Desktop CNC Routers: Small machines with limited cutting power, ideal for hobbyists or light commercial use. These machines handle smaller projects like engraving or cutting soft materials but are restricted by their smaller work areas and cutting depth.
- Mid-Range CNC Routers: Suitable for small to medium-sized businesses, these machines offer larger work areas and higher spindle power, allowing for more versatility. They can cut a range of materials, including wood, plastics, and soft metals, making them ideal for various commercial applications.
- Industrial CNC Routers: Built for large-scale production, these heavy-duty machines feature powerful spindles and large cutting beds. They are capable of cutting thicker materials with high precision and speed. Industrial CNC routers are often used in manufacturing environments where large-scale production needs to be done efficiently.
By considering the size, capacity, and performance of a CNC router in the context of your specific needs, you can make a well-informed choice that ensures your machine performs optimally for your projects.
Evaluate processing needs and requirements
Evaluating your processing needs and requirements is the first step to begin when determining the right CNC router size and capacity. Here are the important considerations, each of which will help you determine the right CNC router in terms of size, capacity, and features.
Workpiece Size and Material
The size and type of materials you plan to work with are fundamental in choosing the appropriate CNC router. Consider the following:
- Workpiece Size: The dimensions of the workpieces you plan to machine will dictate the size of the CNC router’s cutting bed. If you work with large sheets of material, such as plywood, you’ll need a larger machine with a spacious work area, such as 4′ x 8′ or larger. Conversely, if you mainly produce smaller parts or detailed designs, a desktop or mid-range CNC router may suffice.
- Material Type: The type of material impacts both the machine’s power requirements and durability. Are you cutting soft materials like wood and plastic, or tougher materials such as aluminum and steel? Different materials require different spindle power and machine strength. For example, softer materials can be cut efficiently with lower spindle power, while metals require higher power and robust construction to handle the increased stress on the machine.
Complexity of Machining Operations
The complexity of the machining tasks is another critical aspect:
- Intricate Designs: The complexity of your designs and cuts will also play a role in choosing the right CNC router. Intricate designs with tight tolerances may require a machine with higher precision and accuracy. Machines with advanced motion control systems and software that can support complex design files are ideal for projects requiring fine detail and smooth finishes.
- Multiple Machining Operations: If your project requires various machining operations such as drilling, routing, cutting, and engraving, ensure the machine has the right features, including tool changers or multiple spindles, to switch between operations seamlessly.
- Z-Axis Travel: For projects that require machining thicker materials or 3D shaping, check the Z-axis travel height. A higher Z-axis travel will allow the CNC router to accommodate thicker materials and perform complex carving operations.
Production Volume and Throughput
Production volume and throughput will help you decide the machine’s durability and speed:
- High Volume Production: For operations that demand high output and continuous production, you need a robust CNC router designed to handle long working hours without compromising on accuracy. Look for CNC routers with strong, industrial-grade components, high cutting speeds, and reliable cooling systems to prevent overheating during extended runs.
- Low Volume or Custom Work: If your business primarily focuses on low-volume production or custom projects, a smaller, more versatile CNC router may be more cost-effective. These machines can still deliver precision and high-quality results, but without the high costs and space requirements of an industrial-grade machine.
- Batch Processing and Automation: Consider whether automation features, such as automatic tool changers or material loading systems, are necessary for your operations. These features are particularly beneficial if you aim to optimize throughput in high-volume production environments.
By thoroughly evaluating your material types, sizes, production volume, and the complexity of your projects, you can better match your CNC router to your specific processing needs. This ensures optimal performance, cost-efficiency, and room for future scalability.
Key considerations for sizing CNC routers
When determining the appropriate size for a CNC router, several key considerations come into play. These factors help ensure that the machine fits your operational needs while maximizing efficiency and performance. The following are the four essential aspects to evaluate:
Workspace and Workshop Layout
The physical space available in your workshop is one of the first considerations when choosing a CNC router size. Larger CNC routers, such as those with a 4′ x 8′ cutting bed, require substantial floor space, not only for the machine but also for material handling and safe operator movement. Consider the full footprint of the machine, including room for access during maintenance, loading/unloading materials, and positioning necessary equipment like dust collection systems. Additionally, you need to assess whether your workspace allows for easy transport of materials in and out of the CNC router, particularly if you’re working with large sheets or heavy materials.
Rigidity and Stability
The size of the CNC router impacts its rigidity and stability, which plays an important role in ensuring precision and accuracy during operation. Larger CNC routers, especially those used for cutting harder materials like metal or composites, need to be constructed with a strong, rigid frame to withstand the forces generated during cutting. A stable machine prevents vibrations that can affect cutting precision, especially in high-speed operations. Ensure that the CNC router’s size correlates with robust construction to maintain the machine’s stability and improve performance, particularly in industrial settings.
Spindle Power and Tooling
The spindle power and tooling capabilities of the CNC router must align with the size and the types of materials you plan to process. Larger CNC routers with more expansive cutting beds typically require higher spindle power to cut through thick or dense materials effectively. The spindle power also determines the range of tooling options available, allowing you to use larger or more specialized cutting tools. When sizing a CNC router, ensure that the machine’s spindle power can handle your production demands, especially if you plan to cut metals or other hard materials.
Control System and Software
As the size of the CNC router increases, so does the complexity of the control system and software needed to manage the machine’s operations. Larger industrial CNC routers often require more sophisticated control systems that can handle complex tasks, multi-axis movements, and higher production volumes. The control software must be compatible with your design needs, supporting CAD/CAM programs that allow for intricate cuts and smooth operation. When determining the size of your CNC router, consider how advanced the control system and software need to be to optimize performance and streamline workflow, especially for large or intricate projects.
By considering these four aspects, you can choose the appropriate size CNC router that meets your specific machining requirements. This helps maximize productivity, reduce operational costs, and ensure long-term flexibility.
Choosing the Right CNC Router Size and Configuration
When choosing the correct CNC router size and configuration, it’s essential to consider the type of machine that best suits your specific needs. CNC routers come in various sizes and configurations, each offering unique advantages depending on the scale of your projects and production requirements. Here, we will explore how to choose the right CNC router from four key aspects.
Desktop CNC Router
A desktop CNC router is ideal for small-scale projects or businesses that require a compact machine. These machines are designed for lighter materials such as wood, plastics, and soft metals and are commonly used for engraving, signage, prototyping, and hobbyist work. They have a smaller footprint, making them perfect for limited workspace environments. When choosing a desktop CNC router, consider the size of your workpieces and the precision you need. While these machines offer lower cutting speeds and smaller cutting areas, they are highly versatile for detailed work and are cost-effective for small businesses or startups.
Gantry CNC Router
A gantry CNC router is a versatile option, commonly used in medium to large businesses due to its ability to handle a wide range of materials and applications. Gantry CNC routers are characterized by their overhead gantry structure, allowing for efficient movement across large workpieces. They offer a balance between size, power, and flexibility, making them suitable for furniture making, cabinetry, and large signage projects. When selecting a gantry CNC router, consider the size of the cutting bed and the machine’s power capacity, ensuring it matches the scale of your projects. This configuration is often preferred for businesses that need flexibility in processing various material sizes and types.
Large-Format Industrial CNC Router
A large-format industrial CNC router is designed for high-volume, heavy-duty production and is typically used in industries that require the machining of large materials like full sheets of plywood. These machines come with massive cutting beds, higher spindle power, and advanced automation features, allowing for faster throughput and higher precision. When choosing a large-format CNC router, consider the specific materials and thicknesses you work with, as well as your production volume. These machines are an excellent choice for large-scale manufacturing and fabrication operations, as they are built to withstand continuous, rigorous use.
Customization and Integration
Customization and integration options can help you better when choosing a CNC router to meet your unique production needs. Many CNC routers offer customizable features such as a rotary axis for tube engraving, automatic tool changers, vacuum tables, or material loading/unloading systems. These features can significantly improve the efficiency of your operations and expand the machine’s capabilities. When evaluating customization options, think about your current and future requirements, ensuring the CNC router can adapt to your evolving business needs and growth.
Choosing the right CNC router size and configuration requires a thorough evaluation of your production goals, the scale of your projects, and the materials you work with. Whether you’re selecting a compact desktop CNC router, a versatile gantry CNC router, or a high-capacity large-format industrial CNC router, it’s important to align the machine’s capabilities with your business goals. Additionally, considering customization and integration options will ensure your CNC router is optimized for current tasks and flexible enough to grow with your business in the future.
Evaluate Total Cost of Ownership and Return on Investment
When evaluating the Total Cost of Ownership (TCO) and Return on Investment (ROI) for a CNC router, it is essential to look beyond the initial purchase price and consider long-term expenses and benefits. Both TCO and ROI are crucial in determining the overall financial impact of the CNC router on your business, helping you make informed decisions that align with your production needs and budget.
Initial Investment
The initial investment is the most straightforward aspect of Total Cost of Ownership (TCO). It includes the upfront expenses required to purchase the CNC router and all associated costs that come with setting up the machine. This investment goes beyond just the base price of the CNC router and often includes:
- Purchase Price: The cost of the CNC router itself, which can vary widely based on the machine size, type, and features.
- Installation and Setup: Costs associated with shipping, installing the machine in your workshop, and any necessary facility modifications.
- Training and Software: Many CNC routers require specialized software, which may come with licensing fees, along with the cost of training employees to operate the machine effectively.
- Space Requirements: If the CNC router requires a larger footprint, this could lead to additional costs in terms of workshop layout, space, and facility modifications.
The initial investment is a critical factor in TCO because it determines how much capital you will need upfront. High-end machines with advanced features will have higher initial costs, but may offer long-term advantages, such as better performance and lower operational expenses.
Operating Costs
Operating costs are the recurring expenses incurred during the CNC router’s lifetime and form a significant part of the TCO. These costs include:
- Maintenance and Repairs: Regular maintenance to keep the machine in top condition, including part replacements (e.g., spindles, cutting tools), lubrication, and occasional repairs. Industrial CNC routers, especially those used for high-volume production, may require more frequent maintenance, increasing operating costs.
- Energy Consumption: CNC routers require electricity to operate, with larger and more powerful machines consuming more energy. The energy efficiency of the machine can impact long-term operating costs, especially for companies running their CNC routers for extended periods.
- Tooling and Consumables: Cutting bits, end mills, and other tooling are subject to wear and tear and need periodic replacement. The type of material being processed (e.g., metals vs. plastics) also affects the rate of tooling wear, contributing to varying costs over time.
- Software Updates and Licenses: Some CNC routers require ongoing software support and updates, which can add to operating costs, especially if the machine relies on proprietary software that comes with subscription fees.
These ongoing operational expenses must be factored into the TCO to give a clear picture of the full financial commitment of owning a CNC router over its lifecycle.
Return on Investment (ROI) Analysis
Return on Investment (ROI) is a measure of how effectively the CNC router contributes to profitability relative to its total costs. A high ROI means that the machine is generating substantial profit relative to its cost. To accurately evaluate ROI, consider the following factors:
- Productivity Gains: A CNC router can significantly improve productivity by automating processes, reducing the time needed to complete jobs, and allowing for more precise and consistent results. The faster your machine can produce high-quality workpieces, the more revenue it generates, leading to a quicker return on your investment.
- Material Efficiency: CNC routers can optimize material use by minimizing waste through precise cuts. This efficiency leads to savings on raw materials, improving overall profitability. Over time, reduced material costs can contribute significantly to ROI.
- Labor Savings: Automation reduces the need for manual labor, which directly translates into labor cost savings. CNC routers can perform tasks that would otherwise require multiple employees or longer production times. This can help you maximize efficiency and keep labor costs low.
- Revenue Growth: A CNC router can open up new business opportunities by allowing you to offer new services, such as cutting a wider range of materials or creating more complex designs. Expanding your product offerings can lead to increased revenue streams, further improving ROI.
- Payback Period: ROI analysis should include how quickly the CNC router “pays for itself” through increased profits. A machine with high productivity, minimal maintenance, and versatility will likely have a shorter payback period, making it a better investment in the long run.
Evaluating both Total Cost of Ownership (TCO) and Return on Investment (ROI) allows you to make a well-rounded financial decision when purchasing a CNC router. By considering long-term operational costs and how the machine can contribute to increased productivity, material efficiency, and revenue growth, you ensure that your investment is not only cost-effective but also profitable in the long run. This approach helps you maximize your business’s efficiency and competitiveness, ultimately leading to a stronger bottom line.
Summarize
The right CNC router will not only streamline your production process but also provide long-term value and return on investment, helping you stay competitive and efficient in today’s fast-paced industry. By carefully evaluating factors such as the size and type of materials you work with, the complexity of your projects, production volume, and the available space in your workshop, you can select a machine that best aligns with your specific machining needs. In addition to size and capacity, you can get more comprehensive advice by reading the “Comprehensive CNC Router Buying Guide”.
AccTek CNC, a professional CNC router manufacturer in China, is a good choice for businesses seeking high-quality, reliable, and efficient CNC routers tailored to their specific needs. Whether you require a compact desktop model for intricate work or a large-format industrial machine for high-volume production, AccTek offers a range of CNC routers designed to meet varying project requirements. Backed by advanced technology and strong support services, AccTek CNC ensures that its machines not only streamline your production process but also provide long-term value, making them a top choice for businesses in need of dependable CNC solutions.