- 12-17 Min Read
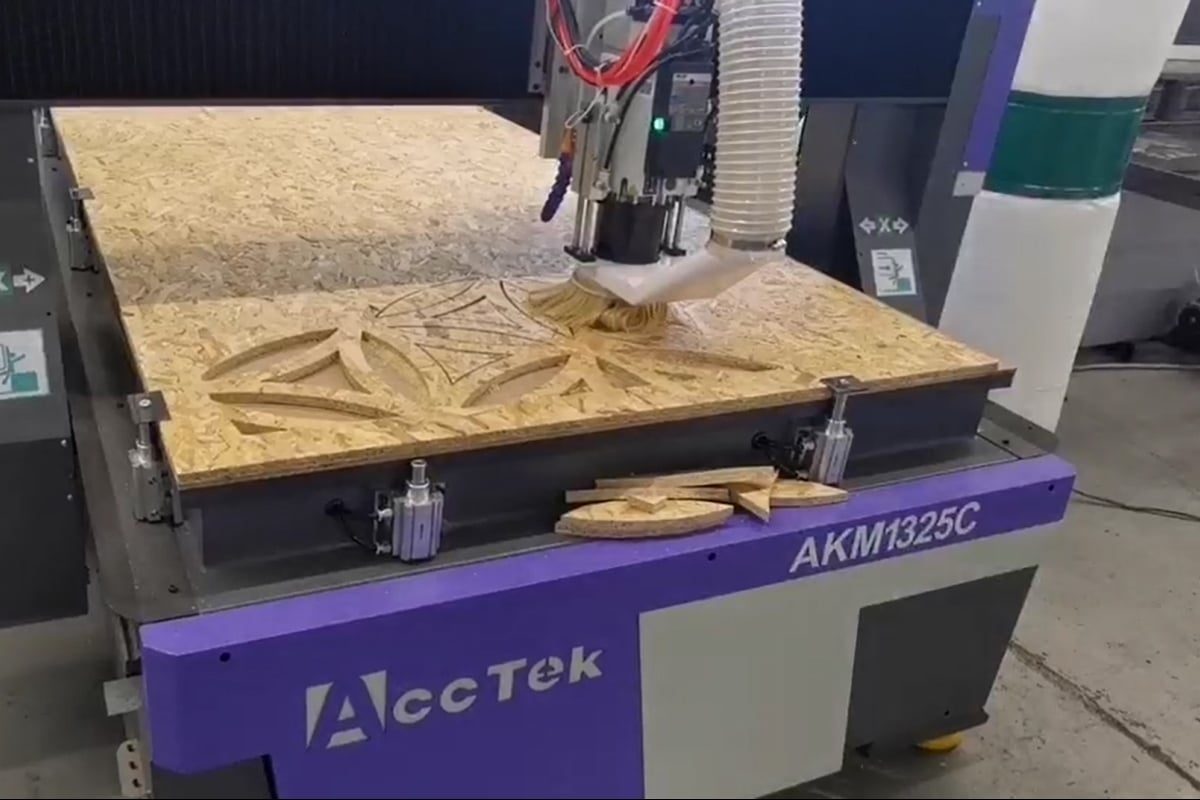
CNC routers are widely used across woodworking, plastic fabrication, and even light metal machining due to their precision, versatility, and automation capabilities. One of the most frequently asked questions by new and experienced users alike is: How deep can a CNC router cut? The answer isn’t always straightforward, it depends on several key factors, including the machine’s power, the type of cutting tool, the material being processed, and how the job is programmed.
Understanding cutting depth is beneficial for ensuring quality results, avoiding tool breakage, and optimizing production efficiency. Whether you’re aiming to carve intricate designs in softwood or create deep pockets in aluminum, knowing the limitations and potential of your CNC router can make all the difference. In this article, we’ll break down the elements that influence cutting depth, typical values across different materials, and how to approach deep cutting safely and effectively.
Factors That Affect Cutting Depth
Several variables influence how deep a CNC router can cut in a single pass or overall. Understanding these factors helps you choose the right tools, materials, and settings to achieve optimal results. In this section, we’ll explore the key elements that directly affect cutting depth and provide insight into how each should be considered when planning a CNC routing job.
CNC Router Type and Machine Rigidity
The physical structure and classification of your CNC router play a major role in cutting depth:
- Hobby-grade or desktop CNC routers typically have limited structural rigidity and are not designed to handle very deep cuts, especially in harder materials. These machines are best suited for light-duty applications and shallow passes.
- Industrial-grade CNC routers feature robust gantries, heavy-duty frames, and reinforced guide systems. These provide the stability required for deeper, more aggressive cuts. The stronger the machine’s structure, the less it will flex or vibrate during operation, which is beneficial for maintaining accuracy and protecting the tool from breakage during deep cuts.
Spindle Power and RPM
The spindle is the powerhouse of the CNC router, and its performance significantly influences cutting depth.
- The spindle’s power (measured in kW or HP) determines how easily it can handle resistance when cutting deep into materials. Spindles with higher power ratings (e.g., 2.2kW to 9kW) can handle more resistance and are capable of driving the cutting tool deeper into the material without stalling or burning.
- RPM also matters. Each material and tool has an ideal spindle speed range. If the RPM is too low for a deep cut, it can cause tool chatter or poor edge quality. It may burn wood or melt plastic if it is too high, especially without proper cooling. Therefore, the spindle speed (RPM) needs to match the material and tool to prevent burning or chatter.
Cutting Tool Type and Length
Tool selection is directly tied to cutting depth.
- Flute length: The bit’s flute length determines how deep it can cut in a single pass. Cutting deeper than the flute length risks overheating, tool deflection, and damage to both the bit and the workpiece.
- Types of cutting bits: Spiral bits tend to evacuate chips more efficiently, while straight bits are often used for shallower clean-up passes. Compression bits can handle deeper cuts in wood laminates without tear-out.
- Tool material: Such as solid carbide or high-speed steel, impacts how well the bit can maintain edge sharpness under load.
Material Type and Density
Different materials offer different levels of resistance, which in turn affects how deep you can cut:
- Soft materials like foam, softwood, and plastic allow for deeper single-pass cuts.
- Hardwoods such as oak and maple, or dense materials like acrylic and aluminum, require shallow, controlled passes to avoid burning, chipping, or stalling the spindle.
- Metals, especially non-ferrous types like aluminum and brass, demand high spindle power, effective chip evacuation, and very shallow passes to avoid tool breakage.
Cutting Strategy
CAM software allows for the creation of optimized toolpaths that affect how deep the router can cut effectively. Strategies include:
- Depth per Pass vs. Total depth: A general rule is to limit the depth per pass to no more than the diameter of the bit. Total cutting depth is often a function of how many safe passes you can take without compromising tool or machine life.
- Roughing vs Finishing passes: Roughing passes remove large amounts of material quickly with multiple moderate-depth passes. Finishing passes, which are shallower and slower to deliver clean edges and precise final dimensions.
- Step-down settings and toolpath strategies: Using step-down strategies allows the machine to gradually remove material layer by layer, reducing stress on the tool and improving overall cut quality. The adaptive clearing or ramp-down entry moves can also reduce tool stress and enable deeper cuts without sudden plunges.
Machine Stability and Vibration Control
As the cutting depth increases, the forces acting on the router bit and machine also increase. Machines with poor stability or worn guide rails are more prone to vibrations and deflection during deep cuts. These conditions not only reduce accuracy but can damage your tools or materials.
Reinforced table support, proper workpiece clamping, and high-quality linear motion components are necessary to maintain alignment and control at greater depths.
The depth a CNC router can cut isn’t dictated by a single factor—it’s the result of a well-balanced combination of machine capability, tooling, material characteristics, and software strategy. Whether you’re working on shallow engraving or deep profile cuts, aligning your approach with these factors is key to successful CNC routing.
Typical Cutting Depths by Material
Understanding how different materials respond to cutting helps users set realistic expectations for depth and performance. Each material has its own characteristics, including density, heat sensitivity, and structural integrity, which directly affect how deep a CNC router can cut per pass and overall. Below are typical cutting depths by common material categories, assuming standard tooling and proper machine setup.
Wood
- Softwood (e.g., Pine, Cedar): Softwoods are relatively easy to cut and allow deeper passes, especially when using sharp spiral bits and a high-power spindle. Typical depth per pass is 3–6 mm (1/8–1/4 inch), and max total depth is up to 50 mm (2 inches), depending on tool length and machine power.
- Hardwood (e.g., Oak, Maple, Walnut): Hardwoods are denser and more fibrous, which requires shallower passes to maintain edge quality and avoid burning or chipping. Typical depth per pass is 2–3 mm (1/16–1/8 inch), and max total depth is 25–40 mm (1–5 inches).
- Plywood and MDF: These materials are cut cleanly with sharp bits, but dust extraction and chip evacuation are important due to fine debris. Typical depth per pass is 2–4 mm (1/16–5/32 inch), and max total depth is 18–25 mm (3/4–1 inch).
Plastics
- Acrylic, Polycarbonate, PVC: Plastics are heat-sensitive. Cutting too deep or too fast may cause melting or rough edges. Use single-flute or O-flute bits and maintain proper cooling. Typical depth per pass is 1–2 mm (0.04–08 inch), and max total depth is 10–20 mm (3/8–3/4 inch).
- HDPE, Nylon, Delrin: These engineering plastics are more forgiving but require attention to chip removal and RPM optimization. Typical depth per pass is 2–3 mm (1/16–1/8 inch), and max total depth is 25 mm (1 inch).
Metals
- Aluminum: Aluminum requires rigid setups, sharp carbide tools, and good lubrication. Shallow passes are beneficial to avoid tool wear or breakage. Typical depth per pass is 0.5–1 mm (0.02–04 inch), and max total depth is 10–15 mm (3/8–5/8 inch).
- Brass, Copper: These metals are tougher to machine and prone to chatter. Depth should be conservative, especially with small-diameter tools. Typical depth per pass is 0.3–8 mm (0.01–0.03 inch), and max total depth is 6–10 mm (1/4–3/8 inch).
Foam and Composites
- EPS, EVA, Urethane Foam: Foams allow full-depth cutting in one pass in many cases, depending on bit length. Low spindle load and minimal tool wear make deep cutting easy. Typical depth per pass is 5–20 mm (1/4–3/4 inch), and max total depth is up to 100 mm (4 inches)
- Carbon Fiber and Fiberglass Panels: Composite materials are abrasive and fragile. Use diamond-coated tools and shallow passes to prevent delamination or tool wear. Typical depth per pass is 0.5–1 mm (0.02–04 inch), and max total depth varies by thickness and tool.
Soft Metals and Alloys (Optional)
If your CNC router supports it, additional soft metals like magnesium or zinc alloys may be routed similarly to aluminum, but require high-rigidity setups and specialized tooling.
Material type is one of the most decisive factors in determining safe and effective cutting depth. While foams and softwoods allow for aggressive, deep cuts, harder materials like metals and composites demand precision, patience, and conservative settings. Always refer to your tooling manufacturer’s guidelines and perform test cuts when pushing cutting limits.
Tips to Maximize Cutting Depth Safely
Maximizing cutting depth is not just about pushing your machine to the limit—it’s about doing so safely, efficiently, and with consistent results. Deeper cuts can boost productivity and reduce pass count, but they also increase stress on the machine, tools, and materials. Below are practical tips to help you achieve greater cutting depth without compromising quality, tool life, or safety.
Choose the Right Tool for the Job
- Use longer flute bits designed for deep cuts, but ensure they are strong enough to resist deflection.
- Prefer solid carbide or coated tools for greater durability, especially when cutting harder materials.
- Compression and spiral upcut bits aid chip evacuation and reduce heat buildup.
Use Proper Step-Down Settings
- Never attempt full-depth cuts in one go unless the material is extremely soft (like foam).
- Follow the rule of thumb: depth per pass ≈ 50–100% of tool diameter, adjusted for material type and machine rigidity.
- In CAM software, apply multiple step-downs for smoother and safer material removal.
Optimize Spindle Speed and Feed Rate
- Match spindle RPM and feed rate to the tool and material using manufacturer’s guidelines or chip-load calculators.
- Spindle speeds that are too slow can cause burnout and tool wear, while speeds that are too fast can cause chatter and tool breakage. Speed and feed rates need to be balanced to maintain consistent chip thickness and prevent heat buildup.
- Ensure the RPM doesn’t exceed the safe limit for the bit, especially during deep cuts.
Ensure Machine Rigidity and Stability
- Use a machine with a strong frame, rigid gantry, and stable worktable to reduce vibration during deep cuts.
- Routinely check for loose components, worn linear guides, or unstable Z-axis assemblies.
- Upgrade to ball screws and linear rails if your current setup shows excessive flex under load.
Improve Material Hold-Down
- Deep cuts exert more lateral force, increasing the risk of material shifting. Use vacuum tables, clamps, or double-sided tape to secure the workpiece firmly.
- Consider using spoiler boards or sacrificial layers to allow full-thickness cuts without damaging the CNC router bed.
- For large or flexible materials, provide additional backing or side support to prevent lift or bow.
Enhance Chip Evacuation and Cooling
- Use dust collection systems, air blast, or mist cooling to keep the cutting area clean and cool.
- Deeper cuts create more chips, and good chip removal prevents clogging, overheating, and melting (especially in plastics and metals).
- For metals, consider lubricating sprays or cutting fluids when your machine setup allows.
Apply Progressive Toolpath Strategies
- Use ramp-in or helical entry moves instead of plunging straight down into the material.
- Employ adaptive clearing or high-efficiency roughing to maintain consistent tool engagement and reduce load spikes.
- Use finish passes to clean up deeper cuts with better edge quality.
Use Simulation and Test Cuts
- Simulate toolpaths in CAM software to identify problematic areas, such as sudden plunges or excessive engagement.
- When working at or near the machine’s depth limit, test your toolpath on scrap material to fine-tune depth, speed, and feed settings.
- Gradually increase pass depth during testing to determine your machine’s safe cutting threshold.
Monitoring and Maintenance
- If your CNC controller supports it, monitor machine load, motor temperature, and vibration during deep cuts.
- Use load data to avoid overloading the machine when increasing cutting depth or speed.
- Perform routine maintenance on spindle bearings, tool holders, rails, and belts to maintain precision.
- Dull bits require more force to cut, generate more heat, and are more likely to break during deep cuts. Inspect tools after heavy jobs and replace them when signs of wear, chipping, or dullness appear.
Cutting deeper with a CNC router can significantly boost efficiency, but it requires a well-thought-out approach. By combining the right tools, feeds, speeds, and machine setup with smart toolpath strategies and proper cooling, you can safely push the boundaries of your machine’s capabilities. Always prioritize stability, precision, and safety to achieve the best possible results.
Common Mistakes to Avoid
Cutting deep with a CNC router offers many benefits, but it also comes with increased risk if not approached correctly. Many users, especially those new to CNC operations, make avoidable mistakes that lead to poor results, tool damage, or even machine failure. Below are some of the most common errors to watch out for when attempting deep cuts:
Overestimating the Strength of the Drill Bit
Many users assume that router bits, especially larger or longer ones, can handle any depth or material. In reality, even solid carbide bits have physical limits. Overloading a bit by cutting too deep, too fast, or into hard material can cause deflection, premature dulling, or breakage. Here is how to avoid it:
- Choose the right bit for the application (e.g., solid carbide for hardwoods, compression bits for laminates).
- Stay within the safe flute length; don’t cut beyond it, or you’ll risk overheating and breakage.
- Use shorter bits when possible to reduce flex and improve precision.
- Regularly inspect your bits for signs of wear, such as dull edges or chipping.
Using Inappropriate Cutting Depth
Setting the depth of cut too aggressively is a frequent cause of failure, either trying to complete a deep pocket in one pass or exceeding recommended step-down values. This strains the spindle, increases heat, and results in poor surface finish or tool damage. Here is how to avoid it:
- Follow the rule of thumb: Depth per pass should not exceed 0.5–1× the tool diameter for most materials.
- Use multi-pass cutting strategies to remove material in layers, reducing load and heat buildup.
- Configure roughing passes followed by a lighter finishing pass for clean edges.
- Use CAM software to simulate toolpaths and adjust step-down levels accordingly.
Ignoring Material Limitations
Not all materials behave the same during routing. Some, like MDF and foam, tolerate deep cuts well; others, like hardwood, acrylic, or aluminum, require special care. Attempting deep or fast cuts on hard or heat-sensitive materials without adjustment can lead to burning, chipping, or melting. Here is how to avoid it:
- Understand the material’s density, grain, and thermal sensitivity before cutting.
- Reduce depth per pass for hard or brittle materials to avoid stress fractures or deformation.
- Adjust spindle speed and feed rate to prevent overheating, especially for plastics and metals.
- Run test cuts on scrap material to validate settings before starting a production job.
Lack of Dust/Chip Management for Deeper Grooves
During deep cuts or pocketing, chips and debris often accumulate in the groove. Without proper evacuation, these chips are re-cut by the tool, increasing friction, causing heat buildup, reducing cutting efficiency, and dulling the bit faster. Here is how to avoid it:
- Use a powerful dust collection system to remove debris continuously during cutting.
- For deeper grooves, consider an air blast nozzle or vacuum shoe to keep the toolpath clear.
- Choose upcut spiral bits for better chip ejection when cutting deeper into materials.
- Periodically pause the job (if needed) to clear chips manually when cutting extremely deep or narrow features.
Avoiding these four critical mistakes is key to running efficient and safe CNC routing operations. By respecting tool limits, adjusting strategies for specific materials, and maintaining a clean cutting path, you can extend tool life, improve accuracy, and achieve high-quality results in every job.
Frequently Asked Questions (FAQs)
Can a CNC router cut through 2-inch hardwood?
Yes, a CNC router can cut through 2-inch hardwood, but it depends on several factors:
- You’ll need a powerful spindle (at least 2.2 kW or more), a rigid machine frame, and a long-flute bit capable of reaching that depth.
- The cut should be done in multiple shallow passes to reduce strain on the bit and avoid burning or chipping.
- Proper clamping and chip evacuation are necessary when cutting hardwood at this depth.
- Always verify your router’s Z-axis travel and bit clearance to ensure full-depth access.
What's the deepest a standard router bit can go?
Most standard router bits have flute lengths ranging from 1 to 1.5 inches (25–38 mm). Cutting deeper than the flute length is not recommended as it leads to poor chip evacuation, heat buildup, and tool stress. However, extended-length bits can cut up to 2–3 inches (50–75 mm), but they are more prone to deflection. To avoid this:
- Lower the Feed Rate and RPM: Reduce spindle RPM by 10–20% to minimize tool flex and heat.
- Use a rigid, vibration-resistant machine set up to maintain accuracy, protect tooling, and ensure a smooth, controlled process.
How do I know if I'm cutting too deep?
To judge whether the cutting depth on a CNC router is too deep, pay close attention to both the machine’s behavior and the quality of the cut. Signs that indicate excessive cutting depth include noticeable vibration or chattering sounds during operation, visible burn marks on the material, rough or torn edges, and premature wear or breakage of the cutting bit. To avoid this:
- Limit your depth per pass to 0.5–1× the bit diameter.
- Monitor the cutting sound and surface finish for signs of overload.
- Use simulation tools in your CAM software to test step-down values.
What bit should I use for deep cuts?
For deep cuts, use long-flute, solid carbide bits with strong rigidity. Recommended types include:
- Spiral upcut bits: Ideal for deep grooves and effective chip evacuation.
- Compression bits: Great for deep cuts in plywood or laminates, as they prevent top/bottom tear-out.
- Single-flute or O-flute bits: Effective for plastics and aluminum with improved chip clearance.
- Tip: Choose a bit with at least the flute length equal to your desired cut depth, and ensure your machine can accommodate the bit length without bottoming out.
Summarize
The cutting depth of a CNC router depends on a combination of factors, including the machine’s rigidity, spindle power, tool selection, material properties, and cutting strategies. While standard cutting depths typically range from a few millimeters to an inch per pass, deeper cuts of 2–3 inches are achievable with the right setup and approach. But these deeper cuts require careful planning, the step-by-step strategy will yield cleaner cuts and more consistent results. Continue reading “How to Choose a Suitable Router Bit for CNC Router” for more useful suggestions.
If you’re looking to start a cutting project with precision and reliability, AccTek CNC is your trusted partner. As a professional CNC router manufacturer, AccTek offers a wide range of high-performance machines designed to handle everything from intricate engraving to heavy-duty deep cutting. Contact me today to get a CNC router recommendation customized to your in-depth cutting needs. From machine selection to application support, our expert team is ready to help you succeed.