- 9-13 Min Read
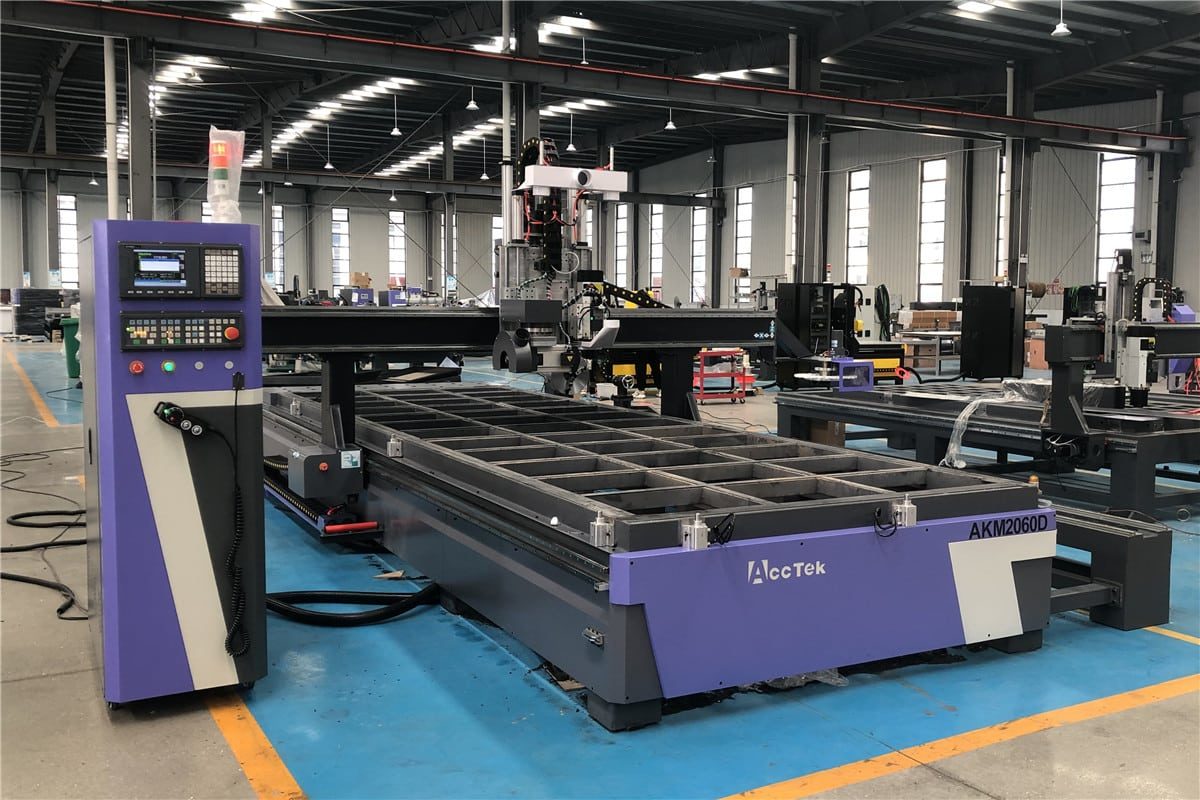
In the world of precision machining and woodworking, a CNC (Computer Numerical Control) router stands as a critical tool for manufacturers, craftsmen, and hobbyists alike. The efficiency, accuracy, and versatility of a CNC router largely depend on the quality of its framework. A high-quality CNC router framework ensures stability, durability, and precision, which are beneficial for producing intricate designs and maintaining consistency across large production runs.
This article aims to explore the critical characteristics that define a high-quality CNC router frame. From material selection to design integrity, each aspect contributes to the machine’s ability to perform complex tasks with high precision. Additionally, we will delve into the various factors that affect the quality of a CNC router frame. These factors include the manufacturing process, the materials used, and the design principles applied. Whether you are upgrading your current equipment or purchasing a new CNC router, this guide will provide the insights needed to ensure you choose a machine with a robust and reliable frame that meets your specific requirements.
Understanding the CNC Router Framework
In the world of CNC machining, the framework of a CNC router is a fundamental component that dictates the machine’s performance, precision, and durability. The framework, often referred to as the frame, serves as the backbone of the machine, providing the structural integrity required to maintain accuracy during intricate and high-speed operations. Here we will have a more detailed understanding of the CNC router framework.
The Role of the CNC Router Frame
- The Pillar of CNC Machining: The CNC router frame serves as the foundational support for the entire machine, acting as the pillar that holds everything together. It holds the workpiece in a fixed position, allowing the cutting tools to operate efficiently and accurately. The frame provides the necessary stability to the CNC router, ensuring that all components are securely held in place.
- Structural Factors: The structure of the CNC router frame is designed to withstand various forces and vibrations generated during machining. This includes the cutting forces from the spindle as it interacts with the workpiece and the inertial forces from the movement of the gantry and axes. The frame’s structure typically comprises materials like steel or aluminum, chosen for their strength and ability to dampen vibrations. A robust structure minimizes deflection and resonance, which can adversely affect machining accuracy and surface finish.
- Support of the Gantry and Axis: The frame also supports the gantry and axes of the CNC router. The gantry, which holds the spindle, must move smoothly and accurately along the X and Y axes, while the Z axis controls the vertical movement of the spindle. The frame must ensure that these movements are precise and repeatable. This support includes the integration of linear guides, ball screws, and other motion control components that enable smooth and controlled movement of the gantry and axes.
The Importance of the CNC Router Frame
- Basis of Accuracy: The accuracy of a CNC router is heavily dependent on the rigidity and stability of its frame. A sturdy frame minimizes deflection and deformation, which can lead to errors in the machining process. By providing a stable base, the frame ensures that the cutting tool follows the programmed path accurately, resulting in precise cuts and high-quality finishes. Any compromise in the frame’s integrity can lead to misalignments and deviations, reducing the machine’s overall accuracy.
- Durability and Lifespan: The durability and lifespan of a CNC router are directly linked to the quality of its frame. A well-constructed frame made from high-quality materials can withstand the rigors of continuous use, harsh environments, and heavy-duty applications. This durability translates to a longer lifespan for the machine, reducing the need for frequent repairs or replacements. Additionally, a durable frame protects other critical components of the machine, such as the spindle and motors, from excessive wear and tear, further extending the overall life of the CNC router.
The CNC router frame is a crucial element that underpins the entire operation of the machine. Investing in a high-quality CNC router frame ensures that you achieve consistent, precise results and a long-lasting, reliable machine that meets your machining needs.
Material Selection for CNC Router Frame
The material of the frame directly impacts the overall performance of the CNC router. Here are the materials commonly used for CNC router frames:
Steel
- Advantages: Steel is known for its high strength and rigidity. It provides excellent support for the machine, minimizing flex and ensuring stable operations. Steel also has good vibration damping properties and is highly durable, making it a popular choice for industrial-grade CNC routers.
- Disadvantages: Steel is heavy, which can make the machine less portable. It is also susceptible to corrosion if not properly treated or coated.
Cast Iron
- Advantages: Cast iron offers exceptional rigidity and vibration damping, making it ideal for high-precision applications. Its thermal stability helps maintain dimensional accuracy. Cast iron frames are highly durable and provide a solid foundation for heavy-duty machining.
- Disadvantages: Cast iron is very heavy and can be more challenging to work with during manufacturing. It is also brittle compared to other materials, which means it can crack under extreme stress.
Aluminum
- Advantages: Aluminum is lightweight yet strong, making it suitable for CNC routers that require portability without sacrificing strength. It is resistant to corrosion and easier to machine and fabricate compared to steel and cast iron. Aluminum also offers good thermal stability.
- Disadvantages: Aluminum has lower rigidity compared to steel and cast iron, which can result in more vibrations during machining. It may not be suitable for heavy-duty applications that require high levels of precision and stability.
Composite Materials
- Advantages: Composite materials, such as epoxy granite, combine high strength with excellent vibration damping properties. They are thermally stable and can be molded into complex shapes, offering design flexibility. Composites are also resistant to corrosion and can be lighter than metal frames.
- Disadvantages: Composite materials can be more expensive and may require specialized manufacturing processes. They may also have different wear characteristics compared to traditional metals.
Extruded Aluminum Profiles
- Advantages: Extruded aluminum profiles are lightweight, easy to assemble, and offer good strength for smaller CNC routers. They are modular, allowing for easy customization and upgrades. These profiles also provide reasonable vibration damping and thermal stability.
- Disadvantages: Extruded aluminum profiles may not offer the same level of rigidity and stability as solid aluminum or steel frames. They are better suited for light to medium-duty applications.
The material selection for a CNC router frame is a critical decision that affects the machine’s performance, precision, and longevity. Steel and cast iron are excellent choices for industrial and heavy-duty applications due to their strength and rigidity, while aluminum and composite materials offer advantages in terms of weight, corrosion resistance, and ease of manufacturing. Understanding the specific requirements of your machining tasks will help you choose the most suitable material for your CNC router frame, ensuring optimal performance and durability.
Framework Design and Construction of CNC Router
A well-designed framework ensures stability, minimizes vibrations, and supports the precise movement of the gantry and axes. Here are the key aspects of designing and constructing a high-quality CNC router framework:
Box Section Design
Box section design is a fundamental aspect of CNC router frames that significantly enhances the machine’s rigidity and stability. This design involves creating a closed rectangular or square tube structure, providing several advantages:
- Increased Rigidity: The box section design maximizes rigidity and resistance to flexing under load. The closed shape distributes forces evenly across the frame, minimizing deformation during operation.
- Enhanced Stability: By forming a continuous loop, the box section design improves the overall stability of the CNC router. This stability is beneficial for maintaining precision during high-speed or heavy-duty machining tasks.
Vibration Reduction: The enclosed nature of the box section helps dampen vibrations, which can negatively affect the quality of the machining process. Reduced vibrations lead to smoother and more accurate cuts.
Ribbing and Reinforcement
Ribbing and reinforcement are critical components in the design and construction of a CNC router frame, providing additional strength and support to key areas:
- Ribbing: Internal ribbing within the frame structure adds extra support and rigidity. These ribs are strategically placed to reinforce high-stress areas, preventing flexing and maintaining structural integrity under load.
- Reinforced Corners and Joints: Corners and joints are often the points of highest stress in a CNC router frame. Reinforcing these areas with additional material or using gussets ensures they remain strong and stable, even during demanding operations.
- Stress Distribution: Ribbing and reinforcement help in distributing stress more evenly throughout the frame. This distribution prevents localized deformation and extends the overall lifespan of the CNC router.
Modularization
Modularization in the design and construction of CNC router frames offers flexibility, ease of maintenance, and customization options:
- Ease of Assembly and Disassembly: A modular design allows for straightforward assembly and disassembly of the frame. This feature is particularly beneficial for transportation, installation, and maintenance, as it enables quick and easy access to different parts of the machine.
- Customization and Upgrades: Modular frames can be easily customized or upgraded to meet specific needs. Users can add or replace components without overhauling the entire frame, allowing for greater adaptability to different machining tasks or advancements in technology.
- Simplified Maintenance: With a modular design, routine maintenance and repairs are simplified. Users can easily remove and replace individual modules or sections, minimizing downtime and ensuring the CNC router remains operational for longer periods.
By incorporating a box section design, ribbing and reinforcement, and modularization, manufacturers can create robust and reliable frames that support high-quality machining operations. The box section design enhances rigidity and stability, ribbing and reinforcement ensure strength and longevity, and modularization provides flexibility and ease of maintenance. Together, these design principles contribute to a superior CNC router that meets the demands of various industrial and commercial applications.
CNC router frame manufacturing requirements
Manufacturing a CNC router frame involves several stringent requirements to ensure the final product’s performance, durability, and precision. Precision machining and high assembly quality are fundamental to the manufacturing of CNC router frames. Here are the specific requirements:
Precision Machining
Precision machining is a critical aspect of CNC router frame manufacturing. It ensures that each component of the frame meets the exact specifications required for optimal performance. Here’s how precision machining plays a role in the process:
- Tight Tolerances: Precision machining involves working with tolerances in the range of micrometers. Ensuring that all parts conform to these tight tolerances helps in maintaining the structural integrity and alignment of the frame.
- Surface Finish: Achieving a smooth surface finish through precision grinding and polishing processes reduces friction and wear on moving parts, enhancing the longevity and performance of the frame.
- Dimensional Accuracy: Consistent dimensional accuracy across all components ensures that they fit together perfectly during assembly, minimizing gaps and misalignments that could affect the machine’s stability and precision.
Assembly Quality
The assembly quality of a CNC router frame is just as important as the precision of its individual components. High assembly quality ensures that the frame is stable, aligned, and capable of maintaining its integrity under operational stresses. Here’s how assembly quality is achieved:
- Welding and Fastening: High-quality welding techniques, such as MIG or TIG welding, are employed to join components securely. The use of appropriate fasteners and proper torque settings ensures that all parts are tightly held together, preventing any movement or loosening over time.
- Reinforcement: Critical stress points are reinforced with additional material or gussets to enhance the frame’s strength. These reinforcements are carefully integrated during assembly to ensure they do not interfere with other components or the overall design.
- Inspection and Testing: Rigorous inspection processes are carried out during and after assembly to ensure that all components are correctly installed and aligned. Dimensional checks, load tests, and vibration analysis are performed to verify that the frame meets the required standards.
- Quality Assurance: A thorough quality assurance process is in place to check every aspect of the assembly. This includes verifying the tightness of fasteners, the integrity of welds, and the alignment of moving parts. Any deviations from the standards are addressed immediately to maintain the high quality of the frame.
Precision machining ensures that each component meets exact specifications, providing the necessary accuracy and consistency. High assembly quality ensures that these components are perfectly aligned and securely attached, resulting in a stable and reliable CNC router frame. Together, these aspects contribute to the creation of high-performance CNC routers that meet the demands of various industrial and commercial applications.
Integration of CNC Router Framework and Auxiliary Systems
The integration of auxiliary systems into a CNC router framework is beneficial for enhancing the functionality, efficiency, and overall performance of the machine. These auxiliary systems work in tandem with the primary structure to ensure optimal operation, precision, and user convenience. Here’s how the CNC router framework integrates with various auxiliary systems:
- Linear Guides and Rails: The CNC router framework is designed to accommodate high-precision linear guides and rails. These components facilitate the smooth and accurate movement of the gantry and axes.
- Motor and Drive Systems: The frame is equipped with robust mounting points for motors and drive systems. These mounts are designed to hold the motors securely in place, minimizing vibrations and ensuring stable operation.
- Control Systems: The framework includes designated areas for mounting control boxes and electronic components. These areas are designed to provide easy access for maintenance and upgrades while protecting the electronics from dust and debris.
- Cooling Systems: For high-power CNC routers, the framework may incorporate provisions for cooling systems. These can include mounts for fans, heat exchangers, or liquid cooling units to prevent overheating of critical components such as the spindle and motors.
- Lubrication Systems: The frame design includes lubrication points for linear guides, ball screws, and other moving parts. Automated lubrication systems can be integrated to ensure that these components receive consistent lubrication, reducing wear and extending their lifespan.
- Dust Collection and Chip Management: The framework can include integrated ports and channels for connecting to dust collection systems. These ports help remove dust and chips generated during machining, maintaining a clean work environment and protecting the machine’s components.
- Vacuum Table and Workholding Systems: For applications requiring secure workpiece holding, the CNC router frame can be designed to integrate with vacuum tables. The frame supports the vacuum table and includes channels for vacuum lines, ensuring efficient and reliable workpiece clamping.
- Automatic Tool Changers (ATCs): The integration of ATCs into the frame allows for automated switching of tools during machining operations. The frame includes mounts and connections for the ATC system, enhancing productivity and reducing manual intervention.
- Spindle Mounts: The framework is designed to securely hold the spindle, ensuring it is precisely aligned with the machine’s axes. This alignment is beneficial for maintaining cutting accuracy and surface finish quality.
The integration of auxiliary systems into the CNC router framework is a vital aspect of machine design and construction. These systems enhance the machine’s functionality, precision, and efficiency, ensuring that it can meet the demands of various industrial and commercial applications. This comprehensive integration ensures that the CNC router operates smoothly and efficiently, providing consistent and high-quality results for a wide range of machining tasks.
Summarize
The foundation of any high-performing CNC router lies in its frame. A high-quality CNC router frame is the cornerstone of precision, stability, and durability, all of which are essential for achieving exceptional machining results. From the careful selection of robust materials to precision machining and meticulous assembly, every aspect of frame design and construction affects the overall performance of the machine. The pursuit of excellence in CNC router frame design and construction is an ongoing commitment to innovation, precision, and quality. By prioritizing these aspects, you can ensure that your CNC router stands up to the demands of modern machining tasks, providing consistent and high-quality results for years to come.
At AccTek CNC, our commitment to excellence is reflected in the design and construction of our CNC router frames. Made of welded steel structures, our frames boast a strong load-bearing capacity, ensuring maximum straightness and rigidity. This robust design guarantees stability and prevents deformation, even during long-term use, providing you with reliable and precise machining performance. Choose AccTek CNC for your next CNC router and experience the difference that a high-quality frame can make.