- 8-12 Min Read
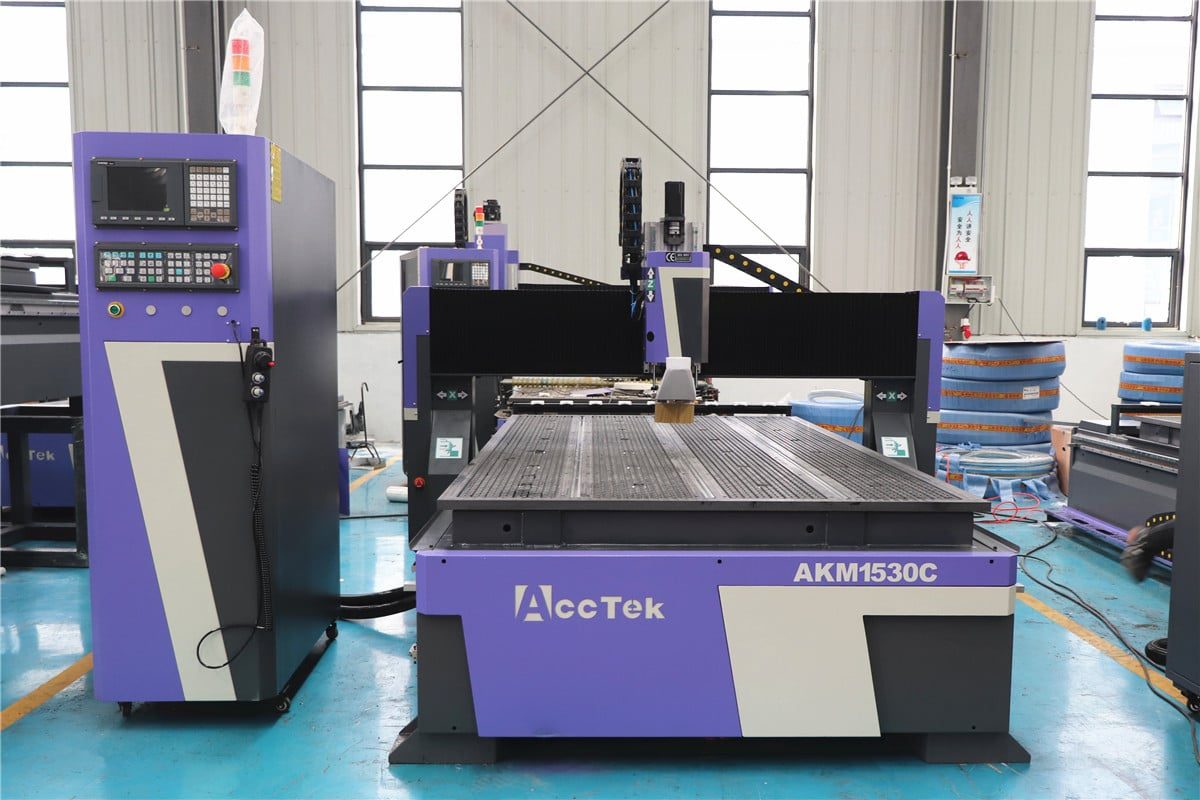
In CNC router operations, achieving high precision and consistent cut quality is a goal across industries. However, one often overlooked factor that significantly influences the final output is resonance. Resonance occurs when the natural frequencies of the machine’s components align with external vibrations generated during cutting, leading to oscillations that compromise accuracy and surface finish. Even subtle vibrations can cause defects like chatter marks, dimensional inaccuracies, and edge irregularities, impacting product quality and production efficiency.
In this article, we explore the concept of resonance in CNC routers and its influence on cutting outcomes. Additionally, we highlight practical strategies to mitigate resonance, from optimizing cutting parameters to enhancing machine stability. By effectively managing resonance, manufacturers can significantly improve cut precision, reduce waste, and ensure consistent output, making resonance management an essential element in CNC router operations.
Understanding resonance in CNC routers
Resonance in CNC routers is a key factor that can influence cutting precision and surface quality. It arises when the natural frequency of a machine’s components aligns with external vibrations generated during cutting. This alignment amplifies oscillations, leading to irregular movements and a decline in the CNC router’s performance. To better understand its impact, it is essential to explore resonance from two key perspectives: what resonance is and the sources of resonance in CNC routers.
What is Resonance?
Resonance occurs when a system vibrates with increasing amplitude due to the synchronization of external forces with its natural frequency. In a CNC router, components such as the frame, spindle, and cutting head each have their own inherent frequency. If the vibrations generated during machining match one of these natural frequencies, the oscillations intensify, resulting in chatter, inaccuracies, and uneven surfaces. Left unchecked, resonance can significantly impair cut quality and increase wear on the machine.
Sources of Resonance in CNC Routers
Resonance in CNC routers can originate from several internal and external factors, all of which contribute to the overall vibration behavior of the machine. Some of the key sources include:
- Mechanical Imbalances: One of the most common sources of resonance in CNC routers is a mechanical imbalance in components like the spindle, cutting tool, or motor. When any of these parts are slightly off-balance, it introduces cyclical vibrations into the system, which can align with the natural frequency of the CNC router. For example, an imbalanced spindle can cause uneven forces during cutting, exacerbating vibrations that may trigger resonance.
- Inaccurate Machine Setup: Misalignment in the CNC router’s structure, such as poorly calibrated linear guides or rails, can lead to irregular movements and vibrations. Loose bolts, joints, or improperly tensioned belts can also create mechanical play, increasing the likelihood of vibrations resonating with the machine’s natural frequencies.
- High-Speed Cutting Operations: High cutting speeds, especially when paired with hard or dense materials, can amplify vibrations in the CNC router. Additionally, the interaction between the cutting tool and the material can generate harmonic vibrations, which, if they match the machine’s natural frequency, can lead to resonance.
- External Vibrations: Environmental factors also contribute to resonance. A CNC router placed on an unstable surface or operating near other heavy machinery may be exposed to external vibrations. These vibrations can combine with those produced by the machine itself, increasing the overall amplitude and potentially leading to resonance.
- Tooling and Workpiece Interaction: The design and condition of cutting tools can influence how vibrations are generated during machining. Worn or damaged cutting tools may introduce irregular forces into the system, while certain tool geometries or workpiece characteristics (such as material hardness) can further exacerbate vibration levels. For instance, harder materials tend to produce more significant cutting forces, increasing the chance of resonance.
- Spindle Speed and Feed Rate: Spindle speed and feed rate are closely tied to the cutting dynamics. Certain spindle speeds can trigger harmonic vibrations that align with the machine’s natural frequencies. Similarly, improper feed rates can create inconsistent material removal, leading to uneven cutting forces that cause vibrations. Optimizing these parameters is key to minimizing resonance.
By understanding what resonance is and the sources behind it, operators can take proactive steps to identify and mitigate it, ensuring that CNC routers perform at their best.
Evaluating the Impact of Resonance on CNC Router Cut Quality
Resonance significantly influences CNC router performance, especially in high-speed and precision operations. Resonance, if left unmanaged, can negatively affect the cut quality of CNC routers, leading to a range of issues that compromise precision, productivity, and material integrity. Below are key areas where resonance impacts cut quality and the specific defects it can cause.
Surface Finish Analysis
Resonance causes oscillations in the cutting tool, producing unwanted vibrations that leave marks on the workpiece surface. These vibrations lead to chatter marks—repetitive patterns or ripples—resulting in a rough or uneven surface finish. The effects include:
- Inconsistent Surface Texture: Vibrations amplify inconsistencies, making the surface appear wavy or jagged.
- Increased Post-Processing Requirements: Additional finishing operations like sanding or polishing become necessary to achieve smooth surfaces, adding labor and production costs.
- Impact on Coating and Treatments: Poor surface finish can affect the adhesion of paints, coatings, or surface treatments, reducing the product’s durability and visual appeal.
Dimensional Accuracy Assessment
Resonance can interfere with the precise control of the cutting tool, causing path deviations and leading to dimensional errors in the final product. When the machine’s vibrations align with its natural frequency, maintaining the desired tool path becomes challenging, resulting in:
- Out-of-Tolerance Dimensions: Even minor deviations can cause parts to fail to meet design specifications.
- Assembly Issues: Inaccurate parts may not fit correctly, impacting the assembly of products, especially in complex structures.
- Increased Scrap Rate: Parts that fall outside the specified dimensional tolerance may need to be discarded, increasing material waste.
Tool Wear and Breakage
The additional vibrations caused by resonance introduce uneven forces on cutting tools, accelerating tool wear and increasing the risk of breakage. The effects include:
- Shortened Tool Life: Tools degrade faster under vibration-induced stress, requiring frequent replacements and increasing operational costs.
- Unexpected Tool Breakage: Resonance amplifies the load on the tool, making it more susceptible to sudden breakage, especially with brittle tool materials.
- Reduced Cutting Efficiency: Worn or broken tools compromise cutting performance, slowing down the process and lowering productivity.
Dynamic Stability Analysis
Dynamic stability refers to the machine’s ability to maintain a steady tool path and cutting speed under varying loads and conditions. Resonance undermines dynamic stability by introducing irregular forces that disrupt cutting operations, leading to:
- Unstable Cutting Paths: The tool may deviate from the programmed path, affecting both cut quality and consistency.
- Reduced Feed Rates and Productivity: Operators may need to slow down cutting speeds to prevent resonance effects, decreasing throughput.
- Machine Wear and Fatigue: Continuous exposure to resonance vibrations can wear down machine components, leading to maintenance issues and reducing the machine’s lifespan.
The impact of resonance on CNC router cutting quality is multi-faceted. Without proper control, resonance can lead to rework, wasted materials, higher operational costs, and machine downtime. Understanding and evaluating these impacts allows operators to implement strategies to mitigate resonance and ensure superior cutting quality.
Strategies to Mitigate Resonance Effects in CNC Routers
Effectively managing resonance is beneficial for achieving optimal cutting quality, extending tool life, and ensuring operational efficiency. Below are key strategies to mitigate the effects of resonance in CNC routers, focusing on mechanical design optimization, cutting parameter optimization, tool and workpiece fixture solutions, and active vibration control systems.
Mechanical Design Optimization
Optimizing the design of the CNC router ensures that vibrations are minimized at their source. Thoughtful design improvements can enhance machine stability and shift natural frequencies away from operational ranges.
- Increase Rigidity: Use a rigid machine frame and high-quality materials to reduce flexibility and vibration.
- Reinforced Components: Strengthen joints, rails, and guides to minimize mechanical play that could contribute to resonance.
- Vibration Damping Structures: Incorporate damping materials (e.g., polymer concrete or vibration-absorbing layers) into the machine’s structure to absorb oscillations.
- Isolated Mounting: Design the CNC router base to isolate it from external vibrations by using rubber feet or vibration-damping mounts.
Cutting Parameter Optimization
Tuning cutting parameters helps avoid resonance by balancing the interaction between the tool, material, and machine dynamics. Adjusting key parameters can shift cutting forces away from resonant frequencies.
- Spindle Speed Adjustment: Fine-tune spindle speeds to avoid frequencies that align with the machine’s natural resonance points.
- Optimized Feed Rates: Set feed rates to match the material properties, ensuring smooth cutting without introducing excessive force.
- Depth of Cut Control: Use smaller depths of cut to reduce cutting force and avoid overloading the tool.
- Multiple Passes: For challenging materials, apply multiple shallow passes instead of one deep pass to minimize vibrations.
- Adaptive Control Systems: Implement control software that adjusts parameters in real-time to maintain stable cutting conditions and reduce the chance of resonance.
Tool and Workpiece Fixture Solutions
Proper tool selection and stable workpiece clamping are beneficial for minimizing resonance. Inadequate fixtures can amplify vibrations, compromising cut quality and accuracy.
- Balanced Cutting Tools: Use tools with precision-balanced designs to ensure even force distribution and minimize vibrations.
- Shorter Tool Overhang: Reduce tool length to minimize deflection and the risk of vibration buildup.
- High-Quality Tool Holders: Use tool holders with built-in damping or anti-vibration technology to suppress oscillations during machining.
- Secure Workpiece Fixtures: Clamp the workpiece tightly using high-quality vises, clamps, or vacuum tables to prevent movement during cutting.
- Anti-Vibration Fixtures: Incorporate damping elements into fixtures to absorb vibrations transmitted from the tool or machine.
Active Vibration Control Systems
Active vibration control systems detect and counteract oscillations in real-time, providing advanced solutions for managing resonance. These systems use sensors and actuators to monitor and adjust cutting dynamics dynamically.
- Vibration Sensors: Install accelerometers on critical components (like the spindle or cutting head) to detect resonance early.
- Real-Time Feedback Loops: Use control systems that analyze vibration data and make real-time adjustments to spindle speed or feed rate.
- Active Dampers: Employ actuators that generate counter-vibrations to cancel out oscillations in the machine structure.
- Smart Spindle Control: Implement spindles with built-in vibration monitoring and adaptive speed adjustment capabilities.
- Machine Learning Algorithms: Use AI-powered systems that predict resonance patterns and proactively adjust machine settings to prevent vibration buildup.
Effectively reducing resonance in CNC routers requires a holistic approach. Each strategy contributes to reducing vibration, ensuring smoother operations, better cut quality, and extended machine and tool life. By applying these measures, manufacturers can enhance the performance and reliability of CNC routers, improving both productivity and product outcomes.
Improving Cutting Quality Through Resonance Management
Effectively managing resonance in CNC routers offers numerous benefits, from enhancing product quality to increasing operational efficiency. Below are the key advantages of improving cutting quality through resonance management:
Enhanced Surface Finish and Aesthetic Quality
When resonance is effectively managed, the tool moves more smoothly, resulting in higher-quality surface finishes. This minimizes defects like chatter marks, ripples, and rough edges, which often require time-consuming post-processing such as sanding or polishing. Improved surface finish has great benefits for industries that value aesthetics, such as furniture manufacturing, signage, and decorative arts. By reducing imperfections, manufacturers can deliver more visually appealing products, enhance customer satisfaction, and eliminate costly rework.
Improved Dimensional Accuracy and Precision
Managing resonance ensures that the tool follows the programmed path with precision, maintaining tight tolerances. Improved dimensional accuracy means fewer rejected parts, better component fit during assembly, and greater consistency in batch production, resulting in higher product reliability and reduced material waste.
Extended Tool Life and Reduced Tool Breakage
Resonance management reduces uneven forces, extending tool life and minimizing unexpected breakage. This not only lowers tooling costs but also reduces downtime caused by frequent tool changes. A longer tool life enhances productivity, allowing operators to run longer production cycles without interruptions, while reducing the overall cost of operations.
Increased Machine Stability and Operational Efficiency
Effective resonance management ensures smoother, more stable operation, minimizing wear on machine components such as spindles, bearings, and linear guides. It also allows operators to optimize feed rates and cutting speeds without compromising quality, resulting in more efficient operations. This stability translates to higher machine uptime, fewer maintenance disruptions, and extended equipment life, contributing to better productivity.
Higher Productivity and Output Quality
Controlling resonance enables manufacturers to achieve faster and more consistent cutting, which improves throughput without sacrificing product quality. With fewer defects and less need for rework, production runs are smoother, and parts are produced more reliably. Operators can work with optimized parameters to increase cutting speeds and maintain quality, improving both output and operational efficiency. The reduction in scrap and downtime also leads to better yield, enabling businesses to meet production targets and deadlines more effectively.
Lower Energy Consumption and Environmental Impact
Resonance management reduces unnecessary oscillations and friction, leading to more efficient machine operations and lower energy consumption. With smoother operations, motors and spindles work more efficiently, reducing power requirements. Additionally, fewer rejected parts and less rework translate to reduced material waste, further lowering environmental impact. Prolonged tool and machine life also means fewer resources spent on replacements and repairs, supporting sustainable manufacturing practices.
Competitive Advantage and Customer Satisfaction
Delivering high-quality products consistently gives manufacturers a competitive edge in the marketplace. When resonance is managed effectively, customers benefit from reliable products with fewer defects and improved performance. This enhances customer satisfaction and builds trust, fostering long-term relationships. Additionally, the ability to produce high-precision parts and meet tight deadlines opens opportunities for manufacturers to take on more complex projects, further strengthening their market position. A reputation for quality and reliability also attracts new customers, driving business growth.
By actively managing resonance, manufacturers can unlock smoother operations, achieve consistent output quality, and build a solid foundation for long-term success.
Summarize
Resonance plays a significant role in the performance and quality of CNC router operations, influencing surface finish, dimensional accuracy, tool longevity, and machine stability. Evaluating these impacts helps manufacturers understand the importance of addressing resonance in their operations. This article explores how resonance affects the cutting quality of CNC routers and emphasizes the importance of managing resonance to achieve precision and efficiency. With the above strategies, you can effectively avoid the effects of resonance on CNC routing.
AccTek CNC is a well-known CNC router manufacturer in China, renowned for delivering high-performance machines tailored to meet the precision needs of diverse industries. Our CNC routers are designed with advanced features, such as optimized mechanical structures, vibration-damping components, and adaptive control systems, to minimize resonance effects. With AccTek’s CNC routers, operators can achieve smooth, accurate cuts while maximizing tool life and operational efficiency.