- 8-12 Min Read
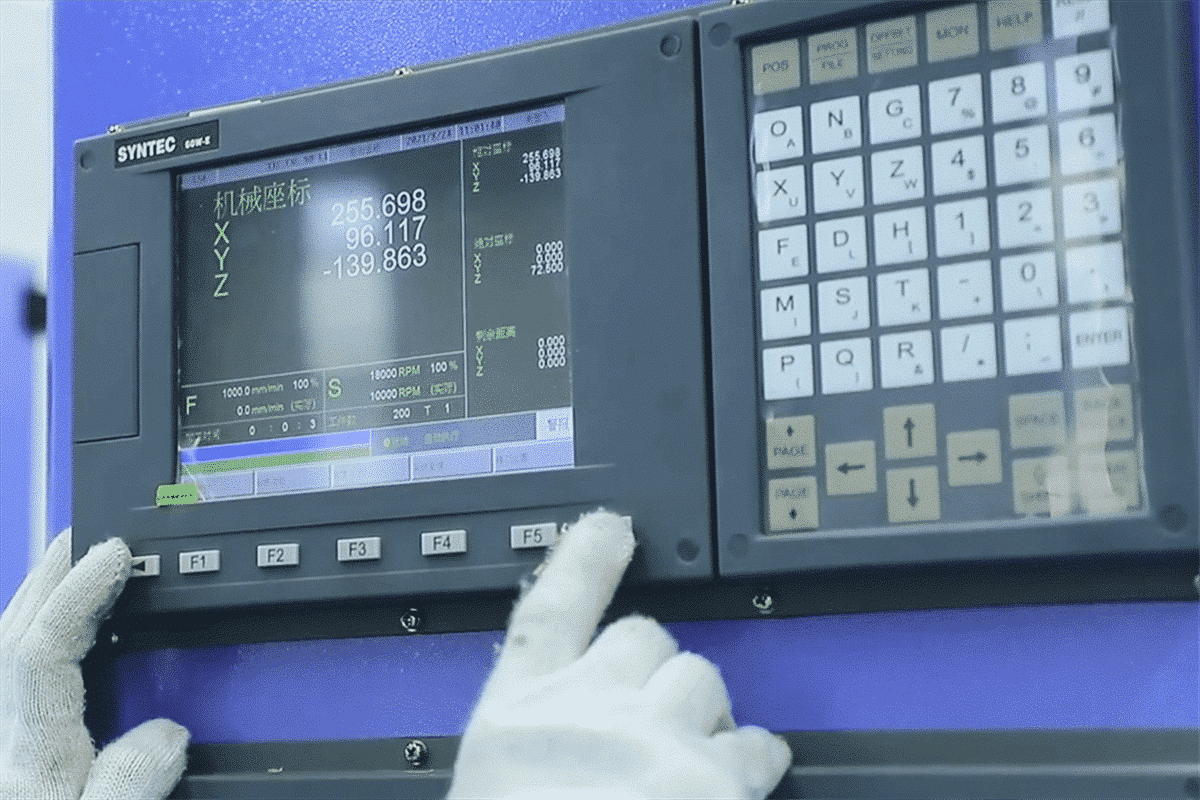
In today’s manufacturing landscape, CNC routers are an effective tool for streamlining the production process in industries such as woodworking and signage. However, the efficiency and precision of these machines are heavily reliant on the software that drives them. CNC router software must not only control the machine but also integrate seamlessly with design processes, CAM systems, and production workflows. Selecting the right software ensures smooth operations, enhances productivity, and minimizes errors during the manufacturing cycle.
This article explores key aspects of evaluating CNC router software for compatibility with design and manufacturing workflows. We’ll look into how well various software solutions integrate with CAD and CAM platforms, the importance of post-processing compatibility, and considerations like ease of use, automation features, and scalability. Whether you’re a small business or an industrial manufacturer, understanding these factors will help you make informed decisions and optimize your CNC router operations.
Understand CNC router software and its role in the workflow
CNC router software serves as the brain of CNC operations, bridging the gap between design concepts and precise machine movements. Understanding how these software tools interact with each other and fit into the overall workflow is beneficial for achieving a productive, streamlined CNC router operation.
The Role of CNC Router Software
CNC router software serves as the backbone of efficient production, transforming design ideas into precise machine operations. It encompasses different types of software, including CAD (Computer-Aided Design) for creating models, CAM (Computer-Aided Manufacturing) for generating toolpaths, and control software that translates these toolpaths into commands for the CNC router. Together, these software tools ensure smooth operations, high precision, and optimal material usage. Beyond executing designs, CNC router software provides advanced functionalities such as simulation, troubleshooting, and real-time machine monitoring, which help operators minimize errors and downtime, improving overall efficiency.
Integration with Design Workflow
Seamless integration into the design workflow is key to efficient production. CNC router software must align with CAD tools to allow quick and accurate data transfer from design to manufacturing stages. This integration ensures that design updates or revisions are automatically reflected in production, reducing the need for manual adjustments. Additionally, compatibility with various design formats enhances flexibility, enabling easy collaboration between designers and machine operators. Features like parametric modeling and layer-based toolpaths also help maintain design intent throughout the workflow, ensuring that the creative vision translates accurately into physical products.
Consistency with Manufacturing Workflow
CNC router software must also align with the manufacturing workflow to ensure consistent, high-quality production. It generates toolpaths optimized for speed, precision, and material efficiency while minimizing cutting errors. By supporting automation features such as batch processing, post-processing adjustments, and real-time monitoring, the software ensures that the CNC router operates smoothly and meets production targets. Moreover, the ability to align with production schedules and manage tool wear ensures consistency across jobs, reducing waste and improving product quality. This synchronization between software and manufacturing operations is key to achieving scalability and maintaining a competitive edge in production.
From seamless design-to-production transitions to optimized machining processes, the right software setup ensures that every step is aligned for efficiency and precision. Understanding the role of CNC router software is the key to unlocking the full potential of CNC technology, leading to higher quality outputs and a more agile production environment.
Evaluating the Compatibility of Design Tools and File Formats
Evaluating the compatibility of design tools and file formats is beneficial for ensuring a smooth transition from design to manufacturing in CNC router operations. The ability to seamlessly transfer files between CAD software and CNC router systems minimizes errors, reduces manual rework, and enhances production efficiency. This section explores four key aspects to consider when assessing compatibility:
File Format Compatibility
File format compatibility ensures that CNC router software can accurately interpret designs created using various CAD tools. Commonly supported formats include DXF, DWG, STL, and SVG, which store essential design data such as dimensions, shapes, and layers. Additionally, many CAM systems rely on G-code files to control machine movements. Robust compatibility minimizes conversion errors, ensuring the design’s precision is preserved throughout the process. Selecting software that supports a wide range of file types allows greater flexibility and reduces the risk of data loss or inconsistencies during file transfers.
Direct Integration with CAD Software
Direct integration between CNC router software and CAD tools streamlines the design-to-production workflow. Some CNC solutions offer native integration with popular CAD software like AutoCAD, SolidWorks, and Fusion 360. This integration enables designers and machine operators to work collaboratively, with design updates automatically reflected in the CAM environment. Such seamless connections eliminate manual file transfers and rework, enhancing productivity and reducing the chances of errors caused by version mismatches.
Plug-ins and Add-ons
Many CNC router systems offer plug-ins or add-ons to enhance compatibility with specific CAD programs or to unlock additional features. These extensions allow users to generate machine-specific toolpaths directly from within their CAD environment, further simplifying the workflow. For instance, a plug-in may allow a designer to generate G-code or set tool parameters directly within SolidWorks, avoiding the need for separate CAM software. Evaluating the availability and ease of use of these plug-ins ensures that the chosen software fits smoothly into existing design practices.
Compatibility Testing
Before fully adopting new CNC router software, it’s essential to conduct compatibility testing with the intended design tools and file formats. This involves running sample files through the workflow to identify potential issues, such as unsupported elements, conversion errors, or data loss. Testing ensures that the software performs as expected under real-world conditions and helps operators identify solutions to any compatibility challenges. Regular testing is important when working with complex designs or when introducing new CAD tools or formats into the workflow.
A well-integrated system reduces friction between design and manufacturing, allowing teams to collaborate effectively and maintain design accuracy throughout production. By evaluating these four aspects, manufacturers can avoid disruptions, improve productivity, and ensure that the CNC router delivers high-quality results from the first cut to the last.
Evaluating CAM Functionality and Toolpath Generation
CAM software transforms digital designs into machine-ready instructions, dictating how a CNC router moves and interacts with materials. Evaluating the CAM functionality and toolpath generation capabilities of CNC router software is beneficial to ensure precision, efficiency, and flexibility in the manufacturing process. This evaluation can be broken down into several key aspects:
CAM Feature Set
A robust CAM software offers a wide range of features to accommodate various machining tasks. These include support for different cutting strategies, such as contouring, pocketing, drilling, and engraving, as well as both 2D and 3D toolpath generation. Advanced features like adaptive clearing, climb and conventional milling, and multi-axis machining allow for more complex operations and enhanced efficiency. The software should also offer optimization tools such as automatic nesting, feed rate adjustments, and cutting strategy selection to improve material usage, reduce cycle times, and enhance cutting precision.
Tool Library and Management
An effective CAM system must provide comprehensive tool management capabilities. The tool library stores key information about tools, such as diameter, flute count, cutting speed, and feed rate, which allows operators to select and configure the right tools quickly. Some CAM software can also track tool wear, helping ensure consistent quality across jobs. Automated toolpath generation based on tool parameters can further minimize manual setup and reduce errors, improving both the speed and consistency of production.
Simulation and Verification
Simulation tools can visualize the operation of a CNC router before actual cutting begins. CAM software with detailed simulation capabilities allows operators to verify the toolpaths, detect potential issues like tool collisions or material interference, and refine parameters to avoid costly mistakes. Real-time visualization of tool movement and error detection ensures that production runs smoothly, reducing waste and preventing machine downtime. Some CAM systems also offer visual feedback on cutting times and material usage, providing valuable insights for optimization.
Post-Processing and Machine Control
Once the toolpaths are generated, the CAM software must convert them into machine-readable G-code or other formats specific to the CNC router. High-quality post-processing capabilities ensure that the generated code is compatible with the router’s control system, accounting for unique machine parameters. The ability to customize post-processing settings ensures seamless communication between software and hardware, reducing the risk of miscommunication and downtime. Advanced CAM software may also enable real-time machine control and monitoring, allowing operators to adjust toolpaths during operation and enhance workflow flexibility.
Evaluating the CAM capabilities across these four aspects ensures that the software aligns with the needs of the manufacturing process. A well-rounded CAM solution not only provides precision and efficiency but also simplifies tool management, reduces setup times, and minimizes production risks, making it a critical component in CNC router operations.
Integration with Manufacturing Processes and Workflow Optimization
Proper integration ensures that every stage—from design to production—is aligned, reducing bottlenecks, minimizing downtime, and optimizing resource utilization. Here are four key aspects to consider when evaluating integration and workflow optimization:
Material Management
Effective material management is a key component of integrating CNC router software with manufacturing processes. The software should align with inventory systems to track material usage in real time, ensuring that sufficient materials are available for scheduled jobs. Integration with ERP or MES systems allows operators to manage stock levels efficiently, minimize waste, and avoid production delays caused by material shortages. Advanced CNC router systems can also optimize material layouts through nesting functions, helping to reduce scrap and maximize the use of raw materials.
Workflow Automation
Workflow automation streamlines production by minimizing manual input and standardizing processes. CNC router software with automation capabilities can handle repetitive tasks such as toolpath generation, tool changes, and batch processing. Automated workflows reduce human error, improve consistency, and accelerate job completion. Integration with other manufacturing systems ensures that the CNC router receives updated schedules and instructions in real-time, enabling efficient transitions between jobs and reducing downtime. Workflow templates and pre-configured settings further enhance productivity, especially for recurring or high-volume production runs.
Quality Control and Inspection
Maintaining product quality is key to any manufacturing process. CNC router software can integrate with quality control systems to ensure that each product meets required specifications. Features like in-process monitoring, tolerance checks, and automated inspection routines help identify errors early, preventing defective products from reaching the next stage of production. Some CNC systems also support feedback loops, allowing operators to adjust toolpaths or parameters based on real-time inspection data, ensuring consistent product quality and reducing waste.
Scalability and Flexibility
For manufacturers to remain competitive, their CNC router operations must be scalable and adaptable to changing demands. CNC router software with flexible settings and multi-machine support allows manufacturers to scale production seamlessly. Integration with MES or ERP systems helps manage workloads across multiple machines and shifts, ensuring optimal resource allocation. Additionally, flexible software solutions can accommodate diverse materials, job types, and design updates, allowing manufacturers to respond quickly to market changes or customer requirements without significant reconfiguration.
By focusing on material management, workflow automation, quality control, and scalability, CNC router software ensures efficient integration with manufacturing processes. These capabilities not only optimize day-to-day operations but also enhance long-term productivity, adaptability, and profitability, enabling manufacturers to stay ahead in a competitive market.
Best Practices for Implementing CNC Router Software
Following best practices helps businesses integrate the software seamlessly into their workflows, reducing downtime and optimizing output quality. Here are some key best practices to consider:
Needs Assessment and Needs Analysis
The foundation of a successful software implementation begins with a thorough needs assessment and analysis. This involves evaluating the specific requirements of your business, including the types of materials you work with, production volume, design tools used, and the level of automation desired. Engage key stakeholders, such as machine operators, engineers, and management, to identify pain points in the existing workflow and determine essential software features. This process ensures that the selected software aligns with both current needs and future growth, helping avoid costly mismatches or unnecessary complexity.
Pilot and Evaluation
Introducing new CNC router software should be a step-by-step process. Begin with pilot testing to identify any compatibility issues with existing systems, tools, and processes. Choose a small-scale or non-critical project to evaluate the software’s performance in real-world conditions. During this phase, assess key factors like toolpath generation, file compatibility, system integration, and output quality. Collect feedback from operators and identify any potential issues that could disrupt full-scale production. A successful pilot helps refine processes, uncover hidden challenges, and build confidence in the new system before a complete rollout.
Training and Support
Comprehensive training for operators, programmers, and technicians ensures that your team can fully leverage the software’s features. Training programs should cover the software’s core functions, advanced features, troubleshooting techniques, and workflow optimization. Offering on-site training sessions or online courses helps build competence among users. Additionally, providing access to ongoing technical support ensures that users can resolve issues quickly, minimizing downtime. A well-trained team reduces the learning curve, improves operational efficiency, and enables businesses to take full advantage of the software’s capabilities.
Continuous Improvement and Adaptation
Software implementation is not a one-time event but an ongoing process of improvement and adaptation. After deployment, continuously monitor performance indicators such as production speed, tool wear, material usage, and error rates. Collect feedback from operators to identify areas for further optimization or training needs. Regular software updates ensure access to new features, improved security, and bug fixes, while periodic audits help maintain alignment with evolving business goals. By fostering a culture of continuous improvement, businesses can adapt to changing market demands and maintain a competitive edge.
Following these best practices ensures a smooth and effective implementation of CNC router software. Through careful planning, rigorous evaluation, focused training, and continuous adaptation, manufacturers can unlock the full potential of the software, achieving better productivity, precision, and profitability over the long term.
Summarize
The right CNC router software is a powerful tool that helps businesses increase productivity, precision, and flexibility to stay competitive in today’s fast-paced manufacturing environment. By following the steps above, you can properly evaluate the compatibility of CNC router software with your design and manufacturing workflows, ensuring seamless integration across all stages of production. With the right software in place, businesses can adapt more easily to evolving demands, maintain consistent product quality, and unlock new opportunities for growth and innovation.
AccTek CNC is a well-known CNC router manufacturer in China, specializing in delivering advanced CNC solutions that empower businesses to enhance productivity, precision, and flexibility. Our CNC routers are equipped with powerful CAM functionalities, enabling accurate toolpath generation and streamlined automation for diverse production needs. Whether for woodworking, metal fabrication, or custom manufacturing, AccTek CNC provides reliable solutions designed to meet the evolving needs of modern manufacturers.