- 8-12 Min Read
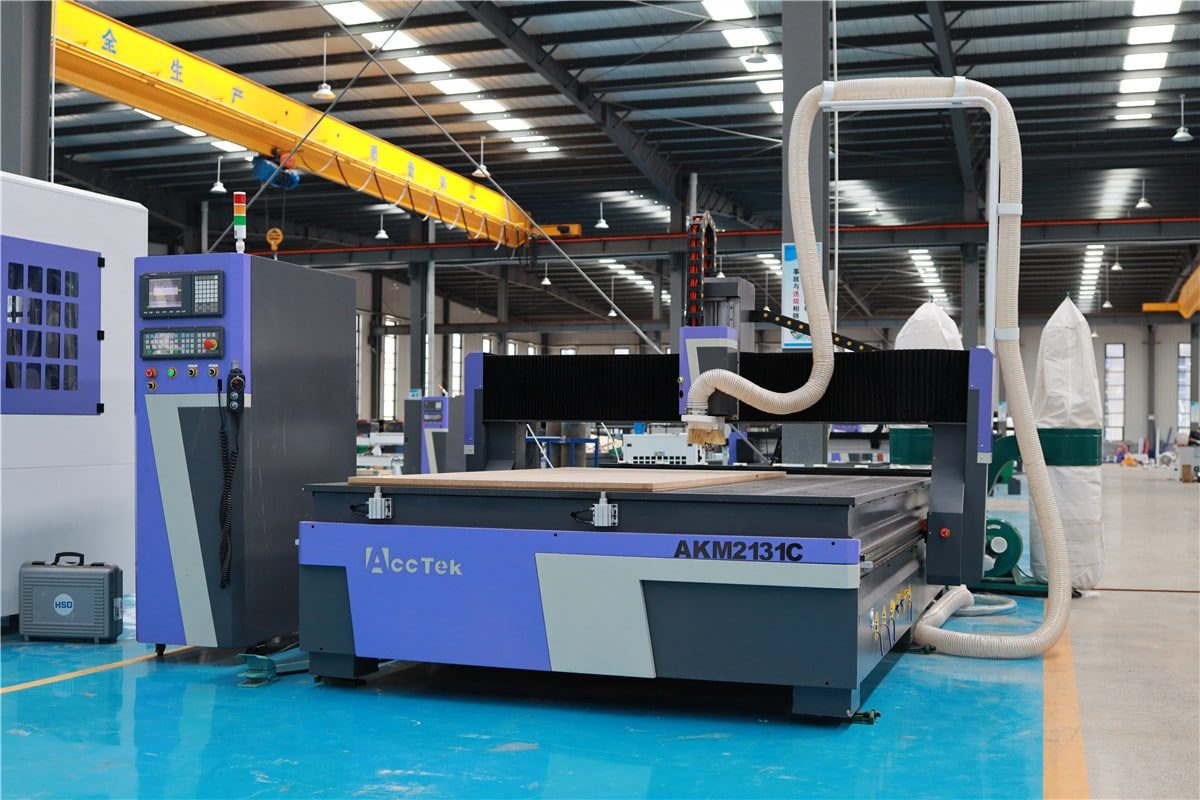
CNC routers are integral to many industries, including woodworking and plastics manufacturing, but their use can lead to significant environmental concerns. So when operating a CNC router, it is important to understand not only the technical aspects but also the environmental and regulatory considerations involved. In addition, businesses must navigate a complex landscape of regulations to ensure compliance and avoid potential penalties.
This article explores the key environmental concerns associated with CNC router operations, such as waste management, energy consumption, and emissions, and delves into the regulatory frameworks that govern their use. By examining current standards and best practices, we aim to provide a comprehensive overview of how businesses can navigate the complex interplay between technological innovation and environmental stewardship. Understanding these considerations is beneficial for optimizing operations, minimizing environmental footprints, and maintaining legal compliance.
Impact of CNC router operation on the environment
The operation of CNC routers can have several environmental impacts, particularly concerning dust in the air, noise pollution, and energy consumption. Understanding these impacts is beneficial for minimizing negative effects on the environment and ensuring the well-being of workers and surrounding communities.
Dust and Particles in the Air
- Fine Dust Emission: CNC routers, particularly when cutting or milling materials like wood, plastics, and composites, generate significant amounts of fine dust. These particles are small enough to remain airborne for extended periods, leading to higher concentrations in enclosed spaces. When these fine dust particles are released into the atmosphere, they contribute to air pollution, potentially spreading over a wide area, depending on the ventilation and extraction systems in place.
- Air Quality Issues: The fine dust generated by CNC routers can lead to severe air quality problems, both indoors and outdoors. In industrial settings, poor air quality can affect worker health, leading to respiratory issues, eye irritation, and other health concerns. Outdoors, the dispersion of fine dust can reduce overall air quality in the surrounding environment, contributing to smog formation and exacerbating conditions for individuals with pre-existing respiratory conditions.
- Potential Environmental Impact: Beyond the immediate air quality concerns, the particulate matter generated by CNC router operations can have broader environmental impacts. When these particles settle, they can contaminate soil and water sources, potentially disrupting local ecosystems. Additionally, if the materials being cut contain harmful substances, these contaminants can leach into the environment, leading to long-term ecological damage.
Noise Pollution
- High Noise Levels: CNC routers are often associated with high noise levels, particularly in industrial settings where large machines operate continuously. In some cases, depending on the speed, material, and tooling, noise levels can even reach 100 dB or higher, creating a loud and disruptive environment.
- Impact on Workers and Communities: Prolonged exposure to high noise levels can have serious health implications for workers operating CNC routers. It can lead to hearing loss, tinnitus, and increased stress levels. The constant noise can also contribute to fatigue, reduced concentration, and decreased productivity. When a CNC router production workshop is located near a residential area, the noise generated by the operation may exceed the workplace and disrupt the daily activities of the community. This can cause dissatisfaction and complaints from community residents, leading to conflicts with residents.
Energy Consumption
- Power Requirements: CNC routers are energy-intensive machines, and require substantial amounts of electricity to operate. The power consumption depends on several factors, including the size and complexity of the CNC router, the type of material being processed, the cutting speed, and the duration of the operation. High-power CNC routers, especially those used for industrial applications, can consume significant amounts of energy.
- Carbon Footprint: The energy consumption of CNC routers directly impacts their carbon footprint, as the majority of electricity generation still relies on fossil fuels, which produce greenhouse gases (GHGs). The more energy-intensive the CNC router operation, the larger the carbon footprint. This contributes to global climate change by increasing the levels of carbon dioxide (CO2) and other GHGs in the atmosphere.
The environmental impacts of CNC router operations are multifaceted and need to be carefully managed to minimize their ecological footprint. Managing these impacts requires a combination of efficient machine operation, proper waste disposal practices, and the adoption of greener technologies and energy sources.
CNC router operation regulatory framework
The regulatory framework for CNC router operations is shaped by several key organizations and agencies, each focusing on different aspects of safety, environmental protection, and compliance. These regulations ensure that CNC router operations are conducted in a manner that protects workers, minimizes environmental impact, and adheres to local and national standards.
Occupational Safety and Health Administration (OSHA)
OSHA’s standards are designed to protect workers from the various hazards associated with operating CNC machines, including exposure to fine dust, noise, and the risk of injury. OSHA requires employers to implement safety measures such as proper ventilation, personal protective equipment (PPE), and machine guarding to prevent accidents and reduce health risks. Compliance with OSHA standards is mandatory for businesses in the United States, and failure to adhere can result in significant fines and penalties.
Environmental Protection Agency (EPA)
The EPA oversees the environmental impact of CNC router operations, particularly concerning air quality, waste management, and emissions. The EPA’s regulations ensure that businesses take steps to minimize their environmental footprint, such as controlling dust emissions and properly disposing of waste materials. Companies must also comply with EPA guidelines on energy consumption and carbon emissions, which are beneficial for reducing the environmental impact of industrial activities. The EPA may require businesses to obtain permits for certain types of emissions and to follow strict protocols for reporting and managing environmental data.
National Institute for Occupational Safety and Health (NIOSH)
NIOSH, although not a regulatory body, provides valuable research and recommendations on workplace safety, particularly in the context of CNC router operations. NIOSH develops guidelines and best practices aimed at reducing occupational hazards, such as exposure to fine dust and noise pollution. These recommendations often inform OSHA standards and help businesses implement effective safety measures. NIOSH also conducts research on emerging risks and technologies, helping to keep safety practices up-to-date with the latest industry developments.
Local and State Regulations
In addition to federal regulations, CNC router operations must also comply with local and state regulations, which can vary widely depending on the jurisdiction. These regulations may include specific requirements for waste disposal, noise control, and air quality management that are tailored to the local environment and community standards. State-level occupational safety regulations may also impose additional requirements beyond those mandated by OSHA, particularly in states with more stringent safety and environmental laws. Businesses must stay informed of these local and state regulations to ensure full compliance and avoid potential legal issues.
Together, these regulatory bodies create a comprehensive framework that governs the safe and environmentally responsible operation of CNC routers. Compliance with these regulations not only ensures legal adherence but also promotes a safer workplace and a healthier environment.
Compliance and Best Practices
Ensuring compliance with the regulatory framework for CNC router operations is beneficial for maintaining a safe, efficient, and environmentally responsible workplace. Beyond meeting legal requirements, adopting best practices can enhance operational efficiency, protect worker health, and reduce environmental impact.
Dust collection and ventilation systems
- Local Exhaust Ventilation (LEV): The use of LEV systems in CNC router operations to reduce the exposure of workers to harmful dust, particularly when cutting materials that generate fine or hazardous particles. Best practices for LEV include regularly inspecting and maintaining the system to ensure it is functioning effectively, properly positioning extraction hoods close to the dust source, and using high-efficiency filters to capture even the smallest particles.
- Ambient Air Filtration: These systems circulate air through filters that remove residual dust and particles that escape LEV capture. Best practices for ambient air filtration include selecting systems with appropriate filtration capacity for the size of the workspace, regularly replacing filters to maintain air quality, and strategically placing units to ensure even air circulation. Ambient air filtration helps maintain a clean environment, reducing the risk of respiratory issues for workers and ensuring compliance with workplace air quality regulations.
Noise Mitigation Strategies
- Fencing and Barriers: These structures can be strategically placed around noisy equipment or along the perimeter of the work area to absorb and deflect sound, minimizing its impact on both workers and the surrounding environment. Best practices for fencing and barriers include selecting materials with high sound-absorption properties, such as acoustic panels, and ensuring that barriers are properly sealed to prevent sound leakage. Additionally, barriers should be regularly inspected and maintained to ensure they continue to provide effective noise reduction.
- Personal Protective Equipment (PPE): Compliance with OSHA regulations requires employers to provide hearing protection, such as earplugs or earmuffs, when noise levels exceed 85 decibels over an 8-hour period. Best practices for PPE include conducting regular noise assessments to determine the appropriate level of protection needed, providing a range of hearing protection options to accommodate different worker preferences, and ensuring that PPE is properly fitted and worn consistently.
Energy Efficiency Measures
- Equipment Selection: Compliance with standards such as those set by the Environmental Protection Agency (EPA) or local energy codes may require businesses to select machinery that meets specific energy efficiency criteria. Best practices for equipment selection include opting for CNC routers and auxiliary systems, such as dust collectors and air compressors, that are certified for energy efficiency, such as those with ENERGY STAR ratings. Additionally, selecting equipment with advanced features like variable frequency drives (VFDs) can optimize power usage by adjusting motor speed according to the workload, further reducing energy consumption.
- Sustainable Practices: Compliance with energy management regulations may involve adhering to guidelines for reducing overall energy use and integrating renewable energy sources where possible. Best practices in this area include scheduling CNC operations during off-peak energy hours to take advantage of lower electricity rates and reduce strain on the power grid. Incorporating renewable energy sources, such as solar or wind power, into the operation’s energy mix can also contribute to sustainability goals.
By adhering to compliance requirements and implementing these best practices, businesses can minimize risks, enhance productivity, and contribute to a more sustainable and safe working environment.
The Role of Technology in Environmental Compliance
Technology plays a critical role in helping CNC router operations meet environmental compliance requirements while promoting sustainability. By leveraging technology, companies can not only ensure compliance with environmental laws but also enhance operational efficiency and sustainability.
Detection and Reporting Systems
- Real-Time Monitoring: One of the key technological tools for environmental compliance is the use of advanced monitoring systems. Sensors and automated systems continuously track key environmental metrics, such as emissions, energy consumption, and waste generation, providing immediate feedback if thresholds are exceeded. This allows businesses to promptly address any issues, preventing potential violations and ensuring continuous compliance. By leveraging real-time data, companies can maintain a proactive approach to environmental management, reducing their overall impact on the environment.
- Reporting Tools: Advanced reporting tools are another key aspect of technology’s role in environmental compliance. These tools streamline the process of collecting, analyzing, and submitting the necessary data to regulatory bodies such as the Environmental Protection Agency (EPA). Automated reporting systems can generate accurate and comprehensive reports that demonstrate compliance with air quality, energy efficiency, and waste management regulations. Additionally, these tools help businesses maintain detailed records of their environmental performance, which can be invaluable during audits or when applying for certifications related to sustainability.
Innovations in Sustainable Manufacturing
- Environmentally Friendly Materials: The development and use of environmentally friendly materials in CNC router operations are increasingly supported by technological advancements. Innovations in material science have led to the creation of sustainable alternatives to traditional raw materials, such as recycled plastics, biodegradable composites, and low-emission adhesives. These materials not only reduce the environmental impact of production processes but also help companies meet stringent environmental standards. By adopting these eco-friendly options, businesses can lower their carbon footprint and minimize the generation of hazardous waste, contributing to a more sustainable operation.
- Circular Economy Practices: Technology also facilitates the implementation of circular economy practices in CNC router operations, promoting resource efficiency and waste reduction. Circular economy principles involve designing products and processes to maximize the reuse, recycling, and repurposing of materials, thereby reducing the need for virgin resources and minimizing waste. Technologies such as digital design and additive manufacturing enable companies to create components with minimal material waste, while advanced sorting and recycling systems make it easier to reclaim and reuse materials at the end of their lifecycle. By embracing circular economy practices, businesses can align with regulatory requirements and enhance their overall sustainability efforts.
Technology is a powerful enabler of environmental compliance in CNC router operations. Through real-time monitoring, advanced reporting tools, the use of environmentally friendly materials, and the adoption of circular economy practices, companies can not only meet regulatory obligations but also contribute to a more sustainable and responsible industry.
Summarize
In the increasingly regulated landscape of manufacturing, CNC router operations must navigate a complex web of environmental and regulatory considerations. By leveraging advanced technology, companies can better manage their environmental responsibilities and stay ahead of regulatory demands. As the industry continues to evolve, staying informed about regulatory changes and continuously improving environmental practices will be beneficial for CNC router operators to thrive in a competitive and environmentally conscious market. Continue reading “Addressing Environmental Concerns in CNC Router Waste Disposal” to learn more about environmentally friendly strategies.
As a well-known CNC router manufacturer, AccTek CNC offers more than just high-quality machines, we provide the essential knowledge and support needed to operate these machines effectively and sustainably. With their commitment to excellence, AccTek CNC ensures that you not only receive right equipment but also the expertise to maximize its potential while adhering to environmental and regulatory standards. Whether you are looking to enhance productivity or ensure compliance, AccTek CNC is your trusted partner in achieving success with CNC router operations.