- 12-17 Min Read
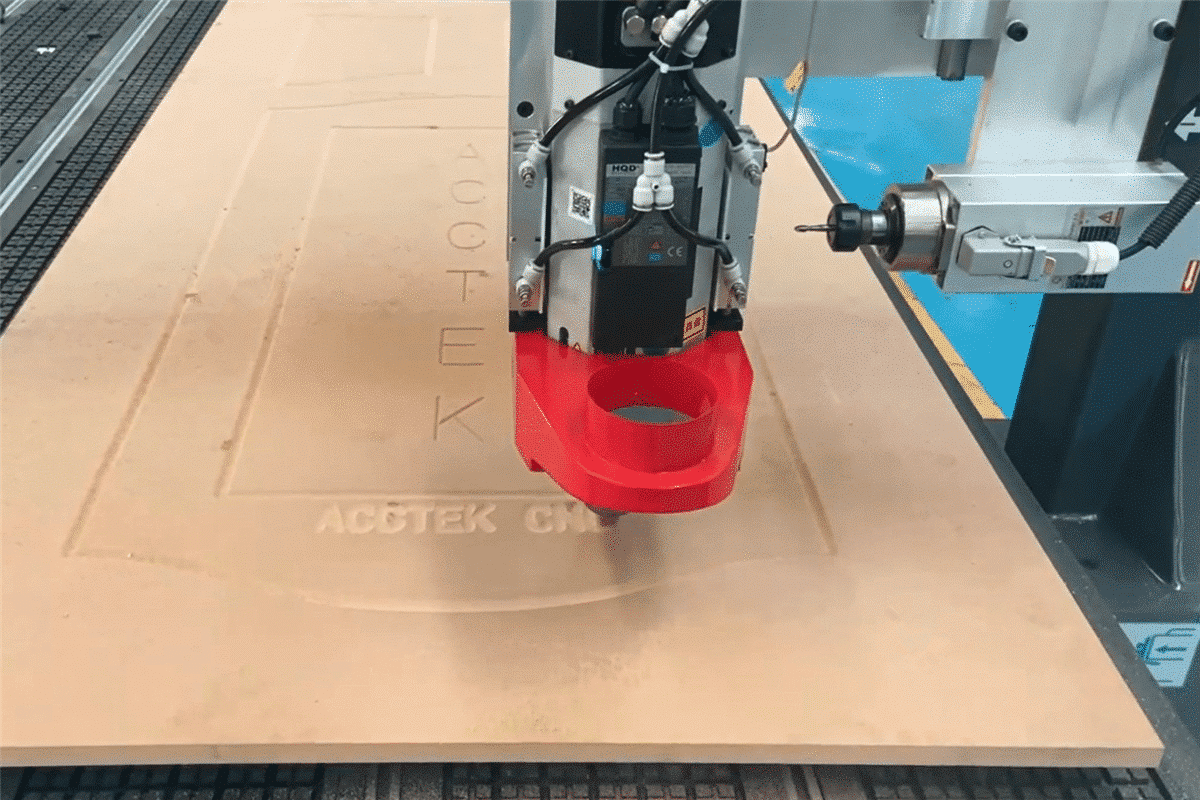
In the realm of modern manufacturing, Computer Numerical Control (CNC) routers stand out for their precision and efficiency in cutting and shaping materials. However, the effectiveness of these advanced machines can be severely compromised by improper tool path optimization. When tool paths are not meticulously planned, issues such as excessive tool dwell time and heat generation arise, leading to reduced tool lifespan, compromised workpiece quality, and increased operational costs.
This article delves into the critical importance of optimizing tool paths in CNC router operations. By understanding the repercussions of improper tool path optimization, manufacturers can proactively implement strategies to enhance efficiency, minimize dwell time, and mitigate heat generation. From advanced software solutions to strategic planning techniques, we explore various methodologies aimed at elevating CNC router performance and maximizing productivity. Join us as we navigate through the complexities of tool path optimization, uncovering actionable insights to propel your CNC machining processes toward greater efficiency and success.
Understanding Tool Path Optimization
Tool path optimization lies at the core of maximizing efficiency and productivity in CNC router operations. It involves the strategic planning and refinement of the route that the cutting tool follows as it moves across the workpiece. This optimization process is multifaceted, encompassing various aspects such as definition, impact, and challenges, here are their details:
Definition
Tool path optimization refers to the systematic analysis and adjustment of the trajectory followed by the cutting tool during machining operations. It aims to streamline the movement of the tool, minimizing unnecessary motions and maximizing the utilization of available resources. By optimizing tool paths, manufacturers can enhance cutting precision, reduce cycle times, and ultimately improve overall productivity.
Impact
The impact of tool path optimization extends across every facet of CNC router operations. Properly optimized tool paths reduce machining time, leading to faster production cycles and increased throughput. This efficiency also minimizes tool dwell time, prolonging tool life and reducing maintenance costs. Additionally, by minimizing unnecessary movements, tool path optimization can mitigate the risk of errors and improve the quality and accuracy of finished parts.
Challenges
Despite its potential benefits, tool path optimization presents several challenges that manufacturers must overcome. Achieving the ideal tool path requires a deep understanding of both the material being machined and the capabilities of the CNC router. Variations in material properties, machine dynamics, and cutting conditions add layers of complexity. Additionally, optimizing tool paths involves sophisticated software tools and algorithms, which can be expensive and require specialized knowledge to implement effectively. There is also the challenge of balancing speed with precision—an overly aggressive optimization can compromise the quality of the final product.
In navigating these complexities, manufacturers must leverage innovative technologies and strategic methodologies to overcome challenges and unlock the full potential of tool path optimization in CNC router operations. By doing so, they can optimize efficiency, minimize production costs, and stay competitive in today’s rapidly evolving manufacturing landscape.
Understanding residence time and heat generation
Residence time and heat generation are two critical factors in CNC router operations that directly affect the quality of machining and the longevity of tools. These factors are closely related to tool path optimization, as improper optimization can exacerbate both issues, leading to suboptimal performance and increased operational costs. Let’s delve deeper into each concept:
Residence Time
Residence time refers to the duration for which the cutting tool remains in contact with a particular area of the workpiece during the machining process. It is influenced by various factors such as cutting speed, feed rate, depth of cut, and the complexity of the tool path. Longer residence times can result from inefficient tool paths or excessive dwell time, where the tool remains stationary or moves slowly through the material. Excessive residence time can have several adverse effects:
- Increased tool wear: Prolonged contact with the workpiece can accelerate tool wear and diminish cutting performance, leading to frequent tool replacements and higher operational costs.
- Heat accumulation: Extended residence times can cause heat to build up at the cutting interface, leading to thermal expansion of the workpiece material and potential distortion or deformation of finished parts.
- Reduced machining accuracy: Lengthy residence times increase the likelihood of thermal deformation and material buildup on cutting edges, compromising the precision and surface finish of machined components.
- Cycle Time Extends: Increased residence time extends the overall machining cycle time, reducing the throughput and efficiency of the manufacturing process.
Heat Generation
Heat generation in CNC router operations occurs primarily due to friction between the cutting tool and the workpiece material. As the tool removes material during machining, frictional forces convert mechanical energy into heat, which can accumulate in the cutting zone and surrounding areas. Factors such as cutting speed, feed rate, tool geometry, and material properties influence the magnitude of heat generated during machining. Excessive heat generation can lead to several detrimental effects:
- Tool degradation: High temperatures can degrade cutting tool materials, reducing their hardness and wear resistance over time. This can result in diminished cutting performance, increased tool breakage, and the need for frequent tool replacements.
- Workpiece damage: Elevated temperatures can cause thermal stress and material distortion in the workpiece, leading to dimensional inaccuracies, surface roughness, and even structural integrity issues in finished parts.
- Tool life reduction: Heat-induced wear mechanisms such as thermal softening, oxidation, and diffusion wear can shorten the lifespan of cutting tools, necessitating frequent tool changes and increasing production downtime.
Factors Affecting Residence Time and Heat Generation
Several factors affect residence time and heat generation in CNC router operations. Understanding these factors is beneficial for optimizing tool paths, improving machining efficiency, and ensuring the quality of finished parts. Let’s explore these factors in detail:
Tool Selection and Geometry
- Tool Material: The material of the cutting tool affects its durability, heat resistance, and performance. Tools made from high-speed steel (HSS), carbide, or ceramics offer different advantages in terms of wear resistance and heat dissipation.
- Tool Geometry: A positive rake angle reduces cutting forces and heat generation, while a negative rake angle can increase tool strength but also increase heat. Proper clearance angles reduce friction between the tool and the workpiece, minimizing heat buildup. A sharp cutting edge reduces heat generation by facilitating smoother cutting action, while a larger radius can increase tool life but may generate more heat.
- Coatings: Coatings such as TiN (Titanium Nitride) or AlTiN (Aluminum Titanium Nitride) enhance tool performance by reducing friction and improving heat resistance.
Cutting Parameters
- Cutting Speed: Higher cutting speeds can reduce dwell time by increasing material removal rates, but they can also increase heat generation if not balanced properly with other parameters.
- Feed Rate: Increasing the feed rate reduces dwell time but must be optimized to avoid excessive tool load and heat generation.
- Depth of Cut: Deeper cuts can increase material removal rates but also prolong the tool’s contact time with the material, leading to higher heat generation.
Material Properties
- Workpiece Material: Materials with high hardness or low thermal conductivity, such as stainless steel or titanium, tend to generate more heat during machining.
- Thermal Conductivity: Materials with higher thermal conductivity, like aluminum, dissipate heat more effectively, reducing the risk of heat buildup.
- Hardness and Toughness: Harder materials require more energy to cut, leading to higher heat generation. Tough materials can cause more tool wear and increase dwell time due to the need for slower cutting speeds.
Tool Path Complexity
- Tool Path Strategy: Strategies such as trochoidal milling, which involves continuous, small circular motions, can reduce heat generation by minimizing tool engagement time and improving chip evacuation.
- Movement Optimization: Efficient tool paths that minimize unnecessary movements and optimize cutting sequences help reduce dwell time and heat buildup.
- Transition Movements: Smooth transitions between cuts and minimizing rapid movements can help maintain consistent cutting conditions and reduce heat spikes.
- Multi-axis Machining: Utilizing multi-axis machining capabilities allows for more efficient tool paths, reducing dwell time and improving heat management by spreading cutting forces across different axes.
The consequences of inefficient toolpath optimization
Inefficient toolpath optimization can lead to several detrimental consequences that affect various aspects of CNC router operations, from productivity and cost to the quality of finished products and machine lifespan. Here are the primary consequences:
Tool Wear and Breakage
- Accelerated Tool Wear: Inefficient tool paths often involve unnecessary or excessive tool engagement with the material, leading to rapid tool wear. This results in tools losing their cutting edge sharpness more quickly than expected.
- Frequent Tool Changes: High rates of tool wear necessitate more frequent tool changes, leading to increased machine downtime and disruption of the production process. This can significantly reduce overall productivity.
- Tool Breakage: Inefficient tool paths can create uneven load distributions and excessive stress on the tool, increasing the risk of tool breakage. Tool breakage not only halts production but can also damage the workpiece and potentially the machine itself.
- Heat Accumulation: Inefficient paths can lead to prolonged tool contact and insufficient cooling, causing excessive heat buildup. This heat can degrade the tool material, reducing its hardness and wear resistance, further accelerating wear and increasing the likelihood of breakage.
Reduced Machining Accuracy
- Dimensional Inaccuracies: Inefficient tool paths can cause tools to deviate from the desired path, leading to dimensional errors in the machined parts. This is often due to factors like tool deflection and uneven cutting forces.
- Poor Surface Finish: Inefficient cutting strategies can result in inconsistent cutting conditions, leading to a poor surface finish. The tool may leave visible marks or rough surfaces, requiring additional finishing operations.
- Thermal Distortion: Excessive heat generation from inefficient tool paths can cause thermal expansion of the workpiece, leading to distortion and reduced dimensional accuracy. This thermal distortion can make it challenging to achieve tight tolerances.
- Increased Vibrations: Suboptimal tool paths can induce vibrations and chatter, further compromising machining accuracy and surface quality. These vibrations can be detrimental, especially when machining complex or delicate components.
Increased Production Costs
- Higher Tooling Costs: Accelerated wear and frequent breakage of tools lead to higher tooling costs. The need for constant replacement and maintenance of tools increases operational expenses.
- Increased Maintenance Costs: Inefficient tool paths put additional stress on CNC machines, leading to increased wear and tear. This necessitates more frequent maintenance and repairs, driving up maintenance costs.
- Longer Cycle Times: Inefficient tool paths result in longer machining times, reducing the overall throughput and productivity. Longer cycle times mean fewer parts are produced within a given timeframe, affecting profitability.
- Higher Energy Consumption: Prolonged machining times and inefficient tool movements result in higher energy consumption. Increased energy use not only raises operational costs but also impacts the sustainability of manufacturing operations.
- Scrap and Rework: Reduced machining accuracy can lead to an increase in defective parts that do not meet quality standards. This results in higher rates of scrap and the need for rework, further increasing production costs and reducing efficiency.
- Operational Inefficiencies: The cumulative effect of frequent tool changes, increased maintenance, longer cycle times, and higher scrap rates lead to significant operational inefficiencies. These inefficiencies can disrupt production schedules and impact overall manufacturing performance.
Strategies for Improving Toolpath Efficiency
Improving tool path efficiency in CNC router operations involves leveraging advanced technologies and optimizing various aspects of the machining process. Here are several strategies to enhance toolpath efficiency. By integrating these strategies, manufacturers can achieve higher productivity, reduced tool wear, and improved machining quality.
Advanced CAM Software and Programming
- Optimized Toolpath Algorithms: Use advanced CAM (Computer-Aided Manufacturing) software that incorporates sophisticated algorithms to generate optimized tool paths. These algorithms minimize unnecessary movements, reduce machining time, and enhance cutting efficiency.
- Simulation and Verification: Utilize the simulation capabilities of CAM software to visualize and verify tool paths before actual machining. This helps identify and correct potential issues, ensuring efficient and error-free operations.
- Programming Techniques: Implement advanced programming techniques such as parametric programming, which allows for dynamic adjustments based on specific conditions and requirements. This flexibility can lead to more efficient and adaptive machining processes.
Adaptive Tool Paths
- Adaptive Clearing: Employ adaptive clearing strategies that adjust the tool path dynamically to maintain a consistent material removal rate. This reduces the load on the tool, minimizes wear, and improves overall efficiency.
- Real-Time Adjustments: Integrate adaptive control systems that monitor machining conditions in real-time and make necessary adjustments to the tool path. These systems can respond to changes in material properties, tool wear, and other variables to optimize performance continuously.
- Tool Engagement Optimization: Design tool paths that optimize tool engagement with the material, reducing dwell time and heat generation. Techniques like constant engagement cutting help maintain steady cutting conditions and improve efficiency.
High-Speed Machining Technology
- High-Speed Spindles: Use high-speed spindles that allow for higher cutting speeds and feed rates. This technology enables faster material removal and shorter cycle times, enhancing overall productivity.
- High-Speed Tool Paths: Develop tool paths specifically designed for high-speed machining, which prioritize smooth and continuous movements to prevent abrupt changes in direction that can cause vibrations and inefficiencies.
- Advanced Tool Materials: Utilize cutting tools made from advanced materials, such as carbide or ceramics, which can withstand the high temperatures and forces associated with high-speed machining. These tools maintain their cutting edge longer, improving efficiency.
Trochoid Routing
- Trochoidal Milling: Implement trochoidal milling techniques, which involve circular tool movements that reduce the engagement time and distribute cutting forces more evenly. This approach is particularly effective for hard materials and deep cuts, minimizing tool wear and heat buildup.
- Reduced Tool Load: Trochoidal routing reduces the load on the tool by minimizing the amount of material in contact with the cutting edge at any given time. This results in smoother cuts and extends tool life.
- Efficient Chip Evacuation: The continuous, small circular movements in trochoidal routing facilitate better chip evacuation, preventing chips from accumulating and causing heat buildup or tool damage.
Optimizing Routing Parameters
- Cutting Speed and Feed Rate: Optimize cutting speed and feed rate parameters to achieve the best balance between material removal rate and tool wear. Using manufacturer recommendations and conducting trial runs can help identify optimal settings.
- Depth of Cut: Adjust the depth of cut to balance efficiency and tool load. Shallow cuts may be inefficient, while deep cuts can overburden the tool. The right depth of cut should be found for optimal performance.
- Spindle Speed: Fine-tune spindle speed in conjunction with cutting speed and feed rate to maintain efficient cutting conditions. The right spindle speed reduces heat generation and improves surface finish.
Advanced technology for toolpath optimization
In the realm of CNC router operations, advanced technology significantly enhances tool path optimization, leading to improved efficiency, accuracy, and productivity. Simulation and analysis tools provide detailed insights and error detection capabilities, while artificial intelligence brings adaptability, predictive analytics, and real-time optimization to the machining process. Together, these technologies offer powerful solutions for improving efficiency, accuracy, and productivity in CNC router operations.
Tool Path Simulation and Analysis
- Visualization of Machining Processes: Advanced CAM software allows users to visualize the entire machining process in a virtual environment. This visualization helps in understanding the tool movements, identifying potential collisions, and ensuring that the tool paths are optimized for efficiency.
- Error Detection and Correction: Simulation tools can detect errors in tool paths, such as potential collisions, tool over-travel, and areas where the tool might gouge the workpiece. By identifying these issues in the simulation phase, manufacturers can make necessary adjustments before machining, reducing the risk of costly mistakes.
- Optimization of Cutting Strategies: Simulations enable the testing of different cutting strategies and tool paths without wasting material or machine time. Users can experiment with various approaches to determine the most efficient and effective strategy for a given task.
- Detailed Analysis of Cutting Parameters: CAM software offers tools for analyzing cutting parameters, such as cutting speed, feed rate, and depth of cut. By examining these parameters in detail, users can optimize them for improved tool life and machining efficiency.
Artificial Intelligence in CAM
- Machine Learning and Predictive Analytics: AI algorithms analyze historical machining data to identify patterns and trends. This analysis helps in predicting tool wear, optimizing tool paths, and improving overall machining strategies based on past performance.
- Adaptive Tool Path Optimization: AI-driven CAM systems can adapt tool paths in real-time based on current machining conditions. For example, if the system detects increased tool wear or harder material, it can adjust the feed rate and cutting speed to maintain optimal performance.
- Dynamic Feed Rate and Speed Adjustments: AI systems can dynamically adjust feed rates and spindle speeds in response to real-time data. This adaptability ensures that the tool operates under optimal conditions at all times, improving efficiency and reducing wear.
The integration of advanced tool path simulation and analysis tools, along with AI-driven optimization techniques, represents a paradigm shift in CNC machining. By harnessing the power of these technologies, manufacturers can achieve unprecedented levels of efficiency, accuracy, and productivity in their machining operations. Continued research and development in this field promise even greater advancements, further propelling the evolution of tool path optimization in the manufacturing industry.
Future trends in toolpath optimization
The future of toolpath optimization in CNC router operations is poised to be shaped by several emerging trends and technological advancements. These trends aim to further enhance efficiency, precision, and productivity in manufacturing processes. Here are some of the key future trends in toolpath optimization:
- Enhanced Artificial Intelligence and Machine Learning: AI-driven CAM systems will autonomously generate toolpaths by learning from past machining experiences and adapting to specific production requirements. These systems will dynamically adjust toolpaths based on changing conditions, such as tool wear or material variations, without the need for manual intervention.
- Dynamic Feed Rate and Speed Control: Future CNC systems will dynamically adjust feed rates and spindle speeds based on real-time sensor data, optimizing cutting conditions and minimizing tool wear. Adaptive control algorithms will maintain optimal chip load and cutting forces for maximum efficiency and surface finish.
- Multi-Objective Optimization: Toolpath optimization algorithms will consider multiple objectives simultaneously, such as minimizing machining time, reducing tool wear, optimizing surface finish, and conserving energy. Multi-objective optimization techniques will find the best compromise among these conflicting goals to achieve overall process efficiency.
- Customizable Optimization Criteria: CAM software will provide customizable optimization criteria that allow users to prioritize specific objectives based on their preferences and production requirements. This flexibility will enable manufacturers to tailor toolpath optimization to suit their unique needs and constraints.
- Cloud-Based CAM Platforms: CAM software will migrate to cloud-based platforms, allowing users to access powerful optimization algorithms and computing resources remotely. Cloud-based CAM solutions will facilitate collaboration among design, engineering, and manufacturing teams, enabling seamless integration of toolpath optimization into the product development process.
- Sustainability and Energy Efficiency: Future toolpath optimization strategies will place a greater emphasis on sustainability and energy efficiency. CAM systems will incorporate lifecycle analysis to evaluate the environmental impact of different toolpath strategies. This will enable manufacturers to choose paths that align with their sustainability goals.
In addition to the trends we mentioned above, the future of tool path optimization in CNC router operations will have more possibilities. These trends will revolutionize CNC machining, enabling manufacturers to achieve unprecedented levels of efficiency, quality, and sustainability in their production processes.
Summarize
The importance of proper tool path optimization in CNC router operations cannot be overstated. Improper tool path optimization can lead to some negative consequences that can be minimized by implementing the optimization strategies provided in this article. As the field of CNC machining continues to evolve, embracing these advanced strategies and technologies will be beneficial for staying competitive and achieving sustainable manufacturing practices. Continuous innovation and refinement in tool path optimization will lead to more efficient, accurate, and cost-effective CNC router operations, ultimately driving productivity and success in the manufacturing industry.
AccTek CNC, a well-known CNC router manufacturer in China, not only provides industrial CNC routers but also dedicates itself to equipping users with essential knowledge and information for optimal machine operation. By following us, you gain access to a wealth of operating guides and expert insights that will help you maximize the efficiency and performance of your CNC routers. Stay connected with AccTek CNC to continuously enhance your machining skills and ensure you are always at the forefront of CNC technology.