- 10-15 Min Read
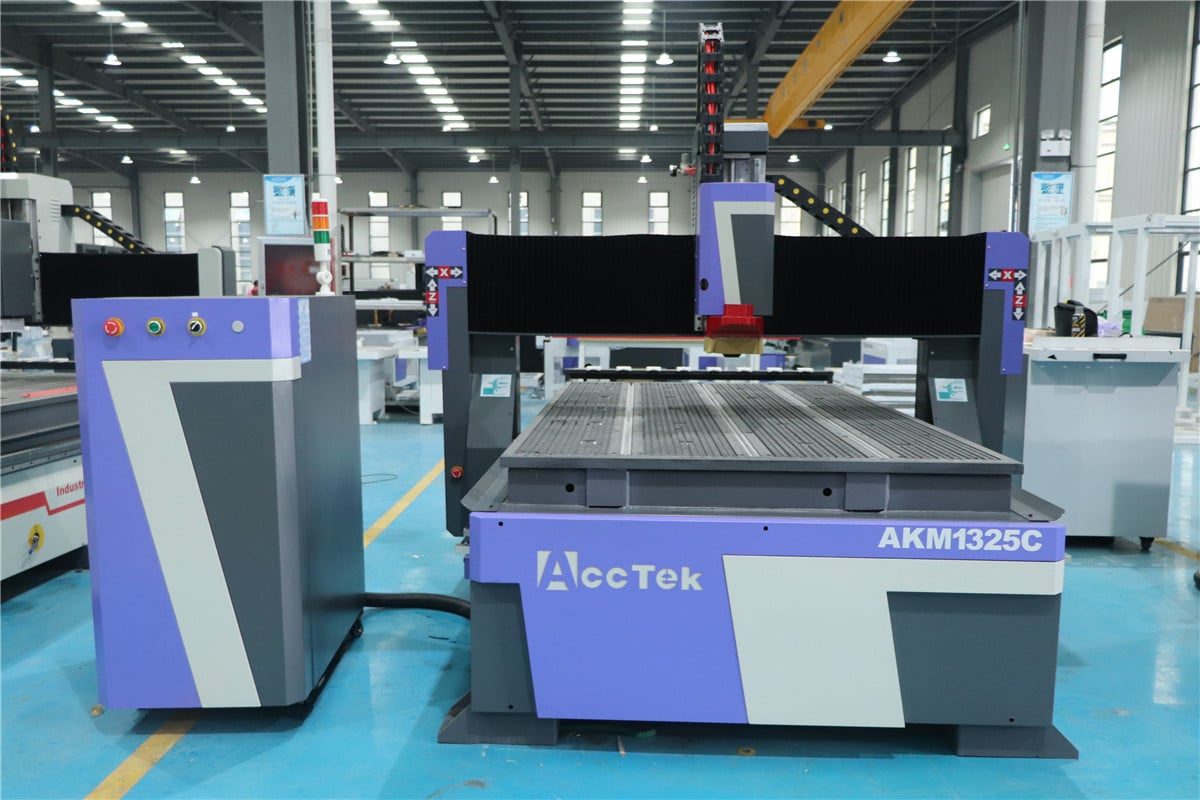
CNC routers have become essential tools in various industries, from woodworking and metalworking to signage and prototyping. These machines offer unmatched precision and efficiency by automating complex cutting, carving, and engraving tasks. However, a common question arises among beginners and professionals alike: Does a CNC router require a computer to function effectively? The answer lies in understanding how CNC technology works.
CNC routers rely on software and digital commands to perform tasks with precision, often requiring a computer to generate and transfer designs to the machine. However, with advancements in technology, some CNC routers offer built-in controls, standalone interfaces, or offline modes. This article explores the essential computer requirements for CNC routers, alternatives for operating without a computer, and how these machines integrate seamlessly with computer systems. It also highlights practical considerations for different production setups and best practices to ensure smooth operation, whether you choose a computer-controlled or standalone CNC solution.
Understanding CNC router
A CNC router is a cutting machine controlled by computer software that automates tasks such as cutting, carving, drilling, and engraving on various materials. CNC routers are widely used in industries like woodworking, metalworking, furniture design, signage, and prototyping. These machines bring precision and efficiency to tasks that would be labor-intensive if done manually. Here is more information about CNC routers:
How Does a CNC Router Work?
The machine operates based on G-code instructions, which tell the CNC router how to move along the X, Y, and Z axes. Here’s a step-by-step overview of how it functions:
- Design and G-Code Generation: The CNC router’s process begins with creating a design using CAD software. The design is converted into G-code by CAM software, which serves as the machine’s instructions. G-code dictates the CNC router’s movements, speed, and cutting depth along the X, Y, and Z axes.
- Control System Operation: The CNC router’s control system reads the G-code and translates it into commands for the motors that control the machine’s movement. This system acts as the brain of the CNC router, coordinating the movement of the spindle and axes to ensure accurate cuts.
- Movement and Motion Control: The X, Y, and Z axes enable the CNC router to move in three dimensions, ensuring precision in all directions. Stepper or servo motors drive these axes based on the control system’s instructions.
- Spindle and Tool Operation: The spindle is the rotating motor that drives the router bit or tool at high speeds. The tool selection depends on the material and task (e.g., cutting, engraving, or drilling). As the spindle rotates, it removes material along the programmed path, executing the job with minimal manual intervention.
- Material Handling and Worktable: The worktable holds the material in place during the cutting process. Materials are secured using clamps, vacuum beds, or adhesives to prevent movement and ensure precision.
- Post-Processing and Quality Control: After the CNC routing operation, the finished product is carefully inspected to ensure it meets the design specifications. Post-processing steps, such as sanding or polishing, may be required to achieve the desired finish.
A CNC router is by translate digital designs into precise mechanical movements to cut or engrave materials automatically. The process requires coordination between design software, control systems, motors, and tools to ensure accuracy and efficiency. Whether working on wood, metal, or plastic, the CNC router automates complex manufacturing tasks, making it an essential tool in various industries.
Computer Requirements for CNC Routers
The computer requirements for operating a CNC router can be broken down into three critical aspects: Computer-Aided Design (CAD) software, Computer-Aided Manufacturing (CAM) software, and CNC Controller software. Each plays a specific role in the workflow, and having a properly equipped computer ensures smooth operation across all phases—from design to execution.
Computer-Aided Design (CAD) Software
CAD software is used to create 2D drawings or 3D models of the part or object to be manufactured. It demands high processing power, memory, and graphical capability, especially when dealing with complex models. Computer Requirements for CAD Software:
- Processor (CPU): Multi-core processors (Intel i5/i7 or AMD Ryzen 5/7) for fast rendering and smooth operation.
- RAM: 8GB minimum, 16GB or more recommended for large 3D models and multitasking.
- Graphics Card (GPU): Dedicated graphics cards (NVIDIA GTX/RTX or AMD Radeon) to handle rendering and 3D visualization.
- Storage: 256GB SSD or higher to quickly load software and save design files.
- Screen Resolution: 1920×1080 (Full HD) or higher for better visibility when working on detailed designs.
Computer-Aided Manufacturing (CAM) Software
CAM software translates CAD designs into machine-readable G-code that instructs the CNC router on how to move and operate. It involves generating toolpaths and simulating machine operations, which require processing power to ensure accuracy and speed. Computer Requirements for CAM Software:
- Processor (CPU): High-performance processors like Intel i7/i9 or AMD Ryzen 7/9 for toolpath generation and simulation.
- RAM: 16GB or more to handle complex toolpaths and multiple software applications.
- Graphics Card (GPU): Mid-range to high-end GPUs for rendering simulations in real-time.
- Storage: SSD for fast file transfers and loading times.
- Connectivity: USB ports, SD card readers, or Ethernet ports to export G-code to the CNC router.
CNC Controller Software
The CNC controller software executes the G-code to operate the machine in real time, controlling the movement of the spindle and axes. While less demanding than CAD/CAM software, reliable performance is beneficial for precise operations. Computer Requirements for CNC Controller Software:
- Processor (CPU): Dual-core or quad-core processors (Intel i3/i5 or AMD Ryzen 3/5) are sufficient.
- RAM: 8GB for smooth operation of control software (e.g., Mach3, UCCNC, or GRBL).
- Storage: 128GB SSD to store G-code and machine settings.
- Connectivity: USB or Ethernet ports for direct connection to the CNC router.
- Power Backup: A UPS is recommended to prevent disruptions during long operations.
A CNC router’s computer requirements vary across the different stages of the workflow. CAD software demands higher processing power, RAM, and graphics capabilities for complex designs. CAM software requires robust performance for toolpath generation and simulation, while CNC controller software needs a reliable computer to ensure smooth real-time operation. Ensuring your computer meets these requirements will maximize your CNC router’s efficiency and accuracy across all stages.
Alternatives to Computer Control for CNC Routers
While many CNC routers rely on computers for design and control, there are several alternatives to computer control that enable more flexible operation. These methods include stand-alone CNC controllers, manual control and jog, and offline programming with USB transmission. Each option provides varying levels of independence, ease of use, and functionality, depending on the production environment.
Stand-Alone CNC Controllers
Stand-alone CNC controllers function as independent control units, eliminating the need for a computer to operate the machine. These systems come with an integrated control panel, often featuring a touchscreen or physical buttons, and allow users to load G-code files directly into the controller. Here are its key features:
- Operates without a computer, using internal memory or an SD card/USB stick for G-code files.
- Offers a user-friendly interface with essential control options.
- Some models provide basic on-screen editing capabilities for minor adjustments.
Standalone CNC controllers are ideal for repetitive tasks in industrial or workshop settings that do not require constant access to a computer, which reduces reliance on external hardware and improves reliability during long operations.
Manual Control and Jog Functionality
Many CNC routers feature manual control panels that allow users to jog the machine along the X, Y, and Z axes. Jogging refers to manually moving the CNC router’s spindle or cutting head to align the material and set the starting point. This method is useful for setup, adjustments, and simpler tasks without requiring a computer connection. Here are its key features:
- Control via a physical panel with buttons, dials, or joysticks for axis movement.
- Allows manual alignment, positioning, and calibration of the CNC router.
- Some CNC routers include a handwheel or pendant for convenient manual control.
Manual control and jogging are useful for fine-tuning and aligning materials before starting an automated task, providing quick manual intervention when required during operation.
Offline Programming and USB Transmission
Offline programming enables users to prepare G-code files on a computer and then transfer them to the CNC router via a USB flash drive, SD card, or other portable storage devices. This method eliminates the need for a continuous computer connection, allowing the CNC router to execute tasks independently once the program is uploaded. Here are its key features:
- G-code files are generated using CAD/CAM software on a separate computer.
- Files are transferred to the CNC router through a USB or SD card, and then executed offline.
- Some CNC routers allow users to select and run programs directly from the device interface.
Offline programming and USB transfer increase operational flexibility, especially in remote or production environments. This control method reduces clutter in the workspace by minimizing cables and external devices.
These alternatives to computer control provide flexible ways to operate CNC routers without constant reliance on a computer. Stand-alone CNC controllers offer independence and reliability for continuous operation, while manual control and jog functions allow quick adjustments and precise material alignment. Offline programming and USB transmission make it easy to load and execute tasks remotely. Choosing the appropriate alternative depends on the specific workflow requirements, making CNC routers adaptable to diverse production environments.
Integration of CNC Routers with Computer Systems
Integrating CNC routers with computer systems enhances precision, efficiency, and flexibility in both local and remote operations. This integration enhances precision, efficiency, and versatility across the entire workflow, from designing parts to executing complex cuts. Below are key aspects of how CNC routers integrate with computer systems. Each plays a key role in ensuring smooth communication between software, hardware, and the CNC router.
Network Connection and Remote Control
Modern CNC routers can connect to computer systems via local networks or cloud platforms, enabling centralized management and remote operation. These features provide greater flexibility, allowing users to control and monitor the CNC router from different locations. Here is how it works:
- Local Network Integration: CNC routers connect to the computer via Ethernet or Wi-Fi, allowing seamless communication between the design software and the machine. Operators can upload G-code files directly over the network without needing physical media like USB drives.
- Cloud and Remote Access: Cloud-based platforms store CAD designs and G-code files, making them accessible from multiple locations and devices. Mobile apps or web interfaces allow remote monitoring and control over Wi-Fi or Bluetooth.
- Centralized Management: In large-scale operations, multiple CNC routers can be connected to a single computer or network for synchronized operation, improving workflow efficiency.
Integrating CNC routers with computer systems through network connections and remote control provides enhanced flexibility and operational efficiency. Remote control through mobile apps or web interfaces allows operators to make adjustments and oversee operations from any location, reducing downtime and improving productivity. This integration is particularly advantageous in large-scale operations or when managing distributed production sites, ensuring continuous workflow without requiring operators to be physically present.
Computer Hardware Considerations
The computer system used for a CNC router must meet certain hardware requirements to run design, control, and monitoring software effectively. Insufficient hardware may lead to performance issues, causing delays or errors during operation. Here are the key hardware considerations:
- Processor (CPU): High-speed processors, such as Intel i5/i7 or AMD Ryzen 5/7, are recommended for CAD/CAM software to handle complex designs and toolpath calculations efficiently.
- RAM: At least 8GB of RAM is required for smooth operation, but 16GB or more is recommended for multitasking between design software, control software, and monitoring applications.
- Storage: A Solid-State Drive (SSD) with 256GB or more ensures fast loading of software and quick access to design files.
- Graphics Card (GPU): Dedicated GPUs (e.g., NVIDIA or AMD) to render 3D models and simulations, especially when working with intricate designs.
- Connectivity Ports: The computer should have sufficient USB or Ethernet ports for direct connection with the CNC router, and possibly Wi-Fi support for remote monitoring.
- Power Backup (UPS): A Uninterruptible Power Supply (UPS) ensures continued operation during power outages, protecting the CNC router from disruptions and preventing data loss.
The right computer hardware the smooth execution of design, simulation, and control software. A high-performance processor enables fast design rendering and accurate simulations, while sufficient RAM and SSD storage support multitasking and quick file access. Reliable connectivity ports allow seamless interaction with the CNC router, and a power backup system (UPS) prevents disruptions during critical operations. Optimized hardware minimizes software crashes and delays, ensuring precision in complex machining tasks and enhancing the overall efficiency of CNC operations.
Integrating CNC routers with computer systems involves more than just connecting devices, it requires network connectivity for remote control and robust hardware to support software operations. Network and cloud integration allow users to manage multiple machines and operate them remotely, while appropriate computer hardware ensures that design and control software run smoothly. This comprehensive integration improves precision, efficiency, and flexibility, making CNC routers more effective tools in modern manufacturing environments.
Practical Considerations and Best Practices for CNC Router Integration
When integrating CNC routers with computer systems, several practical considerations and best practices should be followed to ensure efficient, reliable, and productive operations. Proper training ensures operators can use the equipment effectively, while ongoing maintenance and reliable support prevent downtime and extend the lifespan of both the CNC router and associated systems.
Training and Education
Using a computer interface alongside a CNC router can simplify operations and improve efficiency, but it also introduces new requirements for users in terms of learning software and machine control.
Practical Considerations
- Software Skills: Operators need to be proficient in CAD/CAM software (e.g., Fusion 360, AutoCAD, or VCarve) to design parts and generate toolpaths.
- Learning Curve: Training users to manage software workflows (designing, simulating, and converting files to G-code) can take time and practice.
- Control System Knowledge: Some CNC routers use proprietary or open-source control software, such as Mach3, UCCNC, or GRBL. Training in these systems ensures users can effectively send commands and monitor the machine in real-time.
- Computer Literacy: Even for entry-level use, operators must be comfortable with basic computer operations, including file management and troubleshooting.
Best Practices
- Standardized Training Programs: Implement structured courses for CNC programming and machine operation to reduce the learning curve.
- Simulation Software: Use simulators to allow operators to practice in a virtual environment before working with the actual CNC router.
- Guided Troubleshooting Resources: Provide operators with accessible resources (manuals, FAQs, or online support) to manage basic software and control issues.
- User-Friendly Interfaces: Select CNC control software with intuitive interfaces to reduce training time for less experienced users.
Maintenance and Support
A computer-integrated CNC router can improve operational accuracy but also requires additional consideration for system maintenance and long-term support.
Practical Considerations
- Software Updates: Control software needs periodic updates to ensure compatibility with the latest CNC technologies and operating systems.
- Backup and File Management: CNC routers rely on digital files, which makes it crucial to have proper backup protocols to avoid losing designs or toolpath data.
- Hardware compatibility: Make sure your computer hardware (such as processor, RAM, and connectivity options) matches the requirements of the CNC control software.
- Computer Malfunctions: If the computer controlling the CNC router fails, production could stop, so backup computers or offline control alternatives might be needed.
Best Practices
- Scheduled System Checks: Regularly inspect both the CNC router’s hardware and computer system to ensure smooth communication between the two.
- Dedicated Computer Systems: It is recommended to use a dedicated computer for CNC operations, avoiding distractions from other software or applications.
- Cloud-Based Storage Solutions: Use cloud-based backup options to securely store CNC files and toolpaths, minimizing the risk of data loss.
- Remote Support Access: Ensure the computer has remote access capabilities, enabling technicians to diagnose and solve issues without being on-site.
- Offline Controls as a Backup: Some CNC routers offer pendant controllers that allow limited operation without a computer, serving as a backup for simpler tasks.
A strong focus on training and education ensures that operators are well-equipped to use CNC routers effectively and safely, while maintenance and support practices ensure the equipment remains reliable and productive. Together, these practices improve operational efficiency, prevent costly downtime, and maximize the lifespan of both the CNC router and the computer systems integrated with it.
Summarize
While a computer is not always mandatory for every CNC router setup, it helps in maximizing the machine’s potential. Whether using a fully computer-integrated system or an offline mode, the choice depends on the specific needs of the user. For users seeking high customization and versatility, a computer remains indispensable. However, stand-alone controllers and offline modes offer viable solutions for simpler tasks or workshops looking to minimize reliance on external devices. Understanding these options allows users to select the most suitable setup to meet their operational needs effectively.
If you’re looking for a reliable CNC router solution, AccTek CNC, a well-known CNC router manufacturer in China, offers the perfect balance of innovation and flexibility. Whether you need a high-performance CNC router for intricate designs or a simple setup for repetitive tasks, AccTek CNC’s versatile machines adapt to your specific needs. With a commitment to product quality, advanced technology, and customer support, AccTek CNC ensures smooth, efficient operations for businesses of all sizes.