- 8-12 Min Read
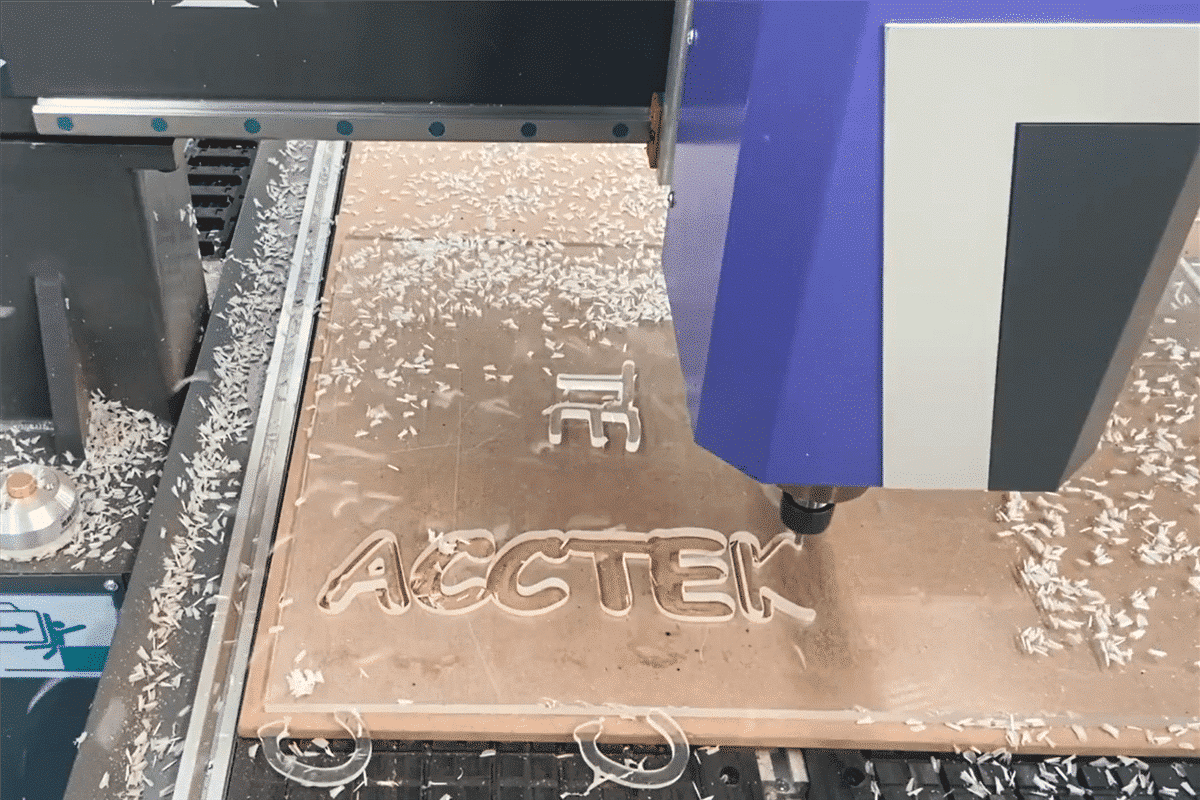
In CNC routing, precision is key to producing high-quality parts and components. However, even the most advanced machines can be hindered by improper chip evacuation. When chips are not efficiently removed from the cutting area, they can lead to a range of problems that compromise the performance of the CNC router. Understanding the effects of improper chip evacuation and learning how to solve these problems is beneficial for maintaining optimal performance in your CNC operations.
Effective chip management strategies can prevent chips from obstructing the cutting path. In this article, we will delve into the effects of improper chip evacuation and explore practical methods to address these challenges, ensuring your CNC routing process runs smoothly and effectively. Whether you are a seasoned professional or new to CNC machining, this guide will help you achieve better results and maintain the performance of your equipment.
Understanding the impact of improper chip removal
Chips, or the small fragments of material generated during the CNC routing process, need to be efficiently removed from the cutting area to maintain the quality and precision of the work. When chip removal is inadequate, these small particles can accumulate, leading to several detrimental effects on both the tool and the workpiece. Here are some specific manifestations of the effects of improper chip removal in CNC routing:
- Chip Re-cutting: When chips are not effectively evacuated from the cutting area, they can become trapped and re-cut by the tool. This re-cutting process introduces additional stress on the tool and the workpiece, leading to a reduction in cutting efficiency and precision. The presence of re-cut chips can cause the tool to deviate from its intended path, resulting in inaccurate cuts and compromised quality of the final product. Additionally, re-cutting can accelerate tool wear, further diminishing the tool’s performance and lifespan.
- Heat Build-up: Chips that remain in the cutting zone can act as insulators, trapping heat and preventing it from dissipating properly. This heat build-up can lead to several problems, including thermal deformation of the workpiece, which can affect its dimensional accuracy. The excessive heat can also cause the cutting tool to lose its hardness, leading to faster wear and potentially causing the tool to become unusable. In extreme cases, the heat can cause the material to fuse with the tool, creating further complications in the machining process.
- Surface Finish Degradation: Improper chip evacuation can directly impact the surface finish of the machined part. Chips that are not cleared away can scratch the surface of the workpiece, leading to unwanted marks and a rougher texture. This degradation in surface finish not only affects the aesthetic quality of the part but can also impact its functional properties. The presence of chips can also result in uneven material removal, contributing to a lack of consistency across the workpiece.
- Tool Damage and Breakage: One of the most severe consequences of improper chip removal is the potential for tool damage and breakage. When chips accumulate, they can create additional resistance against the cutting tool, increasing the load on the tool and leading to mechanical stress. This stress can cause the tool to chip, crack, or even break entirely, especially when working with hard or abrasive materials. Tool breakage not only halts production but can also damage the workpiece and pose safety risks to the operator. Regular tool replacement and the associated downtime can significantly increase operational costs.
These issues caused by improper chip removal not only affect the quality of the final product but can also lead to expensive downtime and maintenance, so efficient chip removal is an important aspect of CNC routing.
Identifying Common Chip Evacuation Problems
In CNC routing, effective chip removal is beneficial for maintaining the quality of the machining process and preventing damage to both the tool and workpiece. However, several issues can arise when chips are not properly managed, each with its own set of challenges that can impact the machining process. Here are some of the most common chip evacuation problems:
Chip Blockage in the Chip Flute
- Causes: Chip blockage in the flute often occurs due to a combination of improper tool selection, incorrect cutting parameters, and the material’s specific characteristics. When a tool with inadequate flute size or helix angle is used for a particular material, chips may fail to evacuate smoothly, leading to blockages. Materials like aluminum or soft plastics, which tend to produce long, stringy chips, are particularly prone to causing this issue. Additionally, if the cutting speed, feed rate, or depth of cut is too aggressive, larger chips can be generated, overwhelming the tool’s ability to clear them.
- Symptoms: Chip blockage in the flute will lead to increased tool wear as chips are re-cut, which creates additional friction and accelerates the wear process. Additionally, the tool may overheat due to trapped heat, and the overall surface finish of the workpiece can suffer, showing roughness or irregularities where the blocked flute disrupts the cutting process.
Chip Accumulation in the Workpiece Cavity
- Causes: Chip accumulation in the workpiece cavity typically arises during deep pocket machining or when working with complex part geometries that have tight spaces. Inadequate chip evacuation strategies, such as insufficient vacuum or airflow systems, exacerbate this issue, as do tool paths that fail to account for chip clearance. In these scenarios, chips can become trapped in the recesses of the workpiece, unable to be effectively removed during the cutting process.
- Symptoms: Chips obstructing the tool path can lead to uneven cuts, requiring additional passes to achieve the desired finish. This accumulation also traps heat, which can cause thermal deformation of the workpiece, leading to dimensional inaccuracies and potentially warping the material. Additionally, the presence of these chips can slow down the cutting process by increasing drag on the tool, reducing overall cutting efficiency.
Low Chip Removal Efficiency
- Causes: Inefficient chip removal is primarily caused by underpowered or poorly configured vacuum or airflow systems, inadequate cutting parameters, and the use of improper tooling. When the vacuum strength is insufficient or airflow is not correctly directed, chips are not effectively cleared from the cutting area, leading to a build-up that can affect the machining process. Similarly, if the cutting parameters are not optimized—such as incorrect feed rates or cutting speeds—chips that are either too large or too difficult to evacuate can be produced, overwhelming the system.
- Symptoms: The inefficient chip removal can significant heat build-up in the cutting area as chips linger and trap heat, causing both the tool and the workpiece to overheat. This condition leads to increased tool wear, as the tool is forced to re-cut chips repeatedly, shortening its lifespan and potentially causing premature failure. Additionally, production delays are a common symptom, as inefficient chip removal results in slower cutting speeds, longer cycle times, and frequent downtime for cleaning or tool replacement.
Coolant and Chip Management
- Causes: Challenges related to coolant and chip management stem from insufficient coolant flow, poor coolant quality, and improper application of coolant during the machining process. If the coolant flow is inadequate, it fails to flush away chips effectively, leading to accumulation in the cutting area. Poorly filtered or contaminated coolant can lose its effectiveness, exacerbating the problem by allowing chips to remain in the machining zone. Additionally, if the coolant is not directed properly, critical areas may be missed, resulting in chip build-up and overheating.
- Symptoms: These issues can cause chip accumulation, particularly in areas where the coolant fails to reach, leading to blockages and reduced cutting efficiency. Overheating is another common symptom, as the lack of sufficient cooling causes both the tool and workpiece to heat up excessively, potentially damaging both and degrading the quality of the machining process. Poor surface quality is also a frequent outcome, as chips left in the cutting area can mar the workpiece, resulting in rough finishes or visible defects.
Understanding these causes and symptoms is beneficial for diagnosing and addressing chip removal issues, ensuring that CNC router operations run smoothly and efficiently.
The Best Chip Removal Solution
The best chip removal solution in CNC routing requires a multi-faceted approach that addresses various aspects of the machining process. Here are five key aspects to address chip removal issues, by understanding them, manufacturers can significantly improve the efficiency and quality of their CNC router operations.
Tool Path Optimization
Tool path optimization is an important step to ensure effective chip removal. By carefully planning the tool’s movements, operators can minimize the chances of chips accumulating in tight spaces or deep cavities. Optimized tool paths take into account the most efficient routes for cutting, which not only enhances productivity but also ensures that chips are consistently evacuated during the machining process. Advanced CAM software often includes features for optimizing tool paths to reduce chip load and improve overall machining efficiency.
Correct Tool Selection
Choosing the correct tool is fundamental to effective chip removal. Tools with the right flute geometry, helix angle, and coating are better suited for evacuating chips quickly and efficiently. For example, tools with larger flute spaces and higher helix angles are ideal for materials that produce longer chips, such as aluminum. Additionally, selecting tools with specialized coatings can reduce friction and prevent chip adhesion, further improving the evacuation process. Proper tool selection not only enhances chip removal but also extends tool life and improves the quality of the final product.
Chip Breaker Implementation
Incorporating chip breakers into the machining process is an effective way to manage chip size and shape. Chip breakers are designed to fragment chips into smaller, more manageable pieces that are easier to evacuate. This is particularly useful when machining materials that tend to produce long, stringy chips, which can easily cause blockages. Implementing chip breakers can significantly reduce the risk of flute blockages and improve overall machining efficiency, as smaller chips are less likely to re-cut and cause tool wear.
Coolant Management System
A well-designed coolant management system plays a significant role in chip removal. Coolant not only helps to cool the tool and workpiece but also assists in flushing chips away from the cutting area. Ensuring that the coolant flow is directed precisely to where it’s needed can prevent chip accumulation and overheating. Additionally, maintaining coolant quality through regular filtration and monitoring helps to prevent contamination that could impair the coolant’s effectiveness. A robust coolant management system enhances both chip evacuation and overall machining performance.
Automatic Chip Extraction
Automatic chip extraction systems are beneficial for maintaining a clean and efficient machining environment. These systems, which often include high-powered vacuums or conveyors, continuously remove chips from the cutting area, preventing accumulation that could disrupt the machining process. Automatic chip extraction is particularly important in high-volume or continuous production environments, where manual chip removal would be impractical. By keeping the workspace clear of debris, these systems help maintain consistent cutting conditions, reduce downtime, and protect both tools and workpieces from damage.
Incorporating these strategies not only improves chip removal but also enhances the overall machining process, leading to better surface finishes, prolonged tool life, and more efficient production cycles. By addressing chip removal comprehensively, manufacturers can minimize the risks associated with chip blockage, accumulation, and overheating, ensuring that CNC routing operations run smoothly and produce high-quality results.
Best Practices for Maintaining Optimal Chip Evacuation
Maintaining optimal chip evacuation in CNC routing is beneficial for ensuring efficient operations, high-quality finishes, and extended tool life. To achieve this goal, best practices need to be implemented in several key areas to improve chip management and overall machining performance. Here are the specific steps:
Regular Maintenance
Regular maintenance of CNC routers and tooling is helpful ensuring consistent and effective chip evacuation. This includes routine inspections of cutting tools, tool holders, and chip evacuation systems like vacuum or coolant systems. Tools should be checked for wear and tear, as dull or damaged tools can hinder chip removal and lead to blockages. Additionally, maintaining clean and properly aligned coolant nozzles and ensuring that vacuum systems are functioning correctly helps in keeping chips away from the cutting area. Preventative maintenance schedules should be followed to address potential issues before they affect chip management.
Operator Training
Operator training is another critical component of maintaining optimal chip evacuation. Skilled operators who understand the importance of chip management can make informed decisions about tool selection, cutting parameters, and the use of coolant or air blast systems. Training should cover the principles of chip formation, the impact of different materials on chip behavior, and how to recognize early signs of evacuation problems. By empowering operators with this knowledge, they can take proactive steps to prevent chip accumulation and ensure smooth machining processes.
Monitoring and Feedback
Implementing real-time monitoring and feedback systems helps optimize chip evacuation. By using sensors and machine monitoring software, operators can track key variables such as tool wear, cutting forces, and temperature, which can affect chip formation and evacuation. These systems provide immediate feedback, allowing operators to make adjustments on the fly to maintain effective chip flow. Additionally, regularly reviewing process data helps identify patterns or recurring issues that may require attention, ensuring that chip management strategies remain effective over time.
Continuous Improvement
Continuous improvement is key to maintaining and enhancing chip evacuation practices. This involves regularly evaluating current processes and systems to identify areas where chip management can be improved. Incorporating feedback from operators, reviewing performance data, and staying updated on the latest advancements in tooling and technology can all contribute to better chip evacuation strategies. By fostering a culture of continuous improvement, manufacturers can adapt to changing materials, tooling, and machining requirements, ensuring that their chip evacuation processes remain effective and efficient.
By adhering to these best practices, operators can maintain optimal chip evacuation, leading to more efficient machining, longer tool life, and superior workpiece quality.
Summarize
Improper chip evacuation during CNC routing can lead to a range of issues that negatively impact machining performance and product quality. To address these challenges, effective solutions must be implemented. This guide covers key strategies for optimal chip removal. By following these recommendations, CNC router operators and manufacturers can enhance their chip management processes, resulting in more efficient operations and higher quality output. Check out “How to Reduce the Impact of Workpiece Adhesion on CNC Router Cutting Quality” to learn more practical strategies to improve cutting quality.
AccTek CNC is dedicated to delivering higher quality machines that empower users to enhance their shop operations and achieve superior finished product quality. In addition, we provide a comprehensive pre-sales and after-sales service team ready to offer professional advice and technical support. Whether you’re selecting the right machine for your needs or troubleshooting an issue, our experts are here to ensure you get the most out of your investment. Whether you’re looking to upgrade your equipment or optimize your production processes, AccTek CNC is your trusted partner for reliable and high-performance machinery.