- 10-15 Min Read
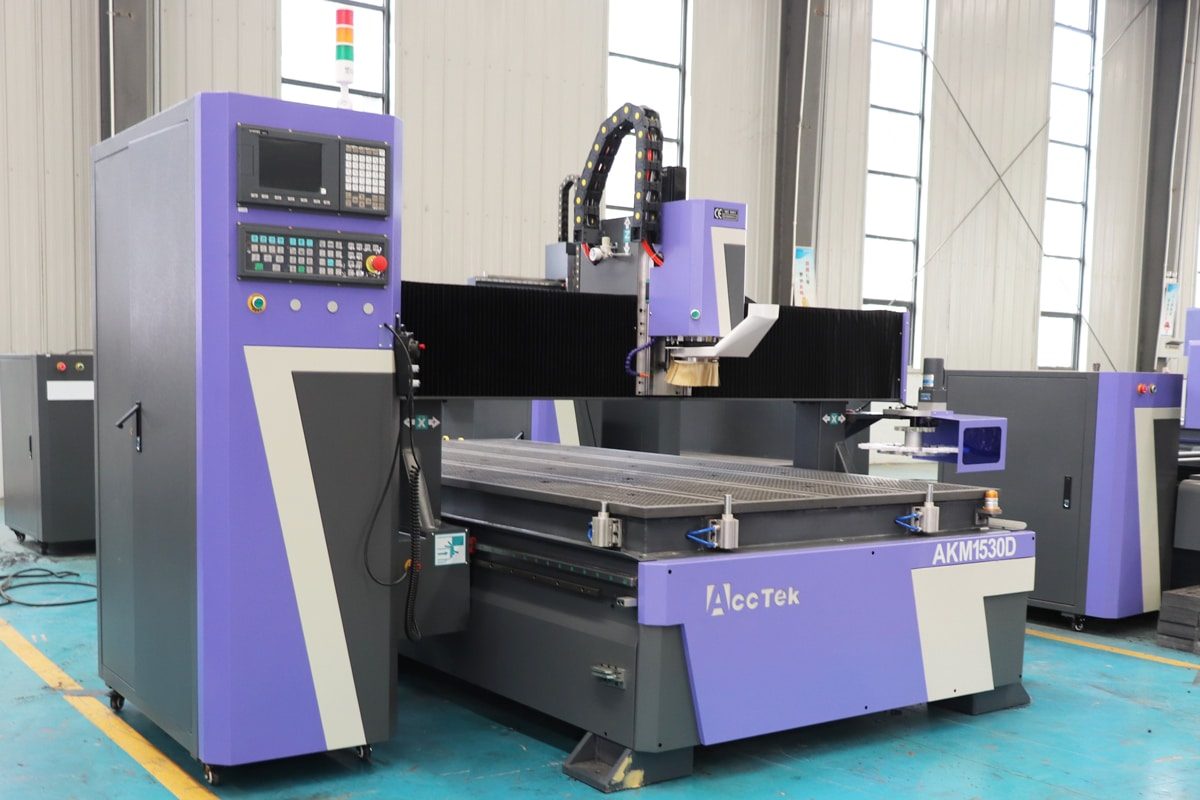
When choosing a CNC router, one of the most critical decisions is selecting the right motor system. Stepper motors and servo motors are the two primary options that drive the movement of CNC machines, each offering distinct advantages and limitations. The choice between these two directly affects precision, speed, efficiency, and overall machine performance.
Stepper motors are known for their affordability and simple control systems. In contrast, servo motors provide higher speed, accuracy, and efficiency. This guide provides a detailed comparison of stepper motors and servo motors, examining key factors such as accuracy, speed, cost, control complexity, and energy efficiency. By the end, you’ll have a clear understanding of which motor type best suits your CNC router needs.
Understanding Stepper Motors
Stepper motors are widely used in small CNC routers due to their ability to achieve precise positioning without requiring complex feedback systems. They convert electrical pulses into discrete mechanical movements, making them ideal for applications that demand accuracy and repeatability. Below, we understand stepper motors from multiple aspects.
Working Principle of Stepper Motors
A stepper motor operates by dividing a full rotation into a series of equally spaced steps. Unlike traditional motors that rotate continuously, stepper motors move incrementally in response to electrical pulses. Each pulse advances the rotor by a fixed angle, known as the step angle, ensuring precise control of movement. Stepper motors function based on the electromagnetic attraction principle:
- The stator contains multiple coils arranged in phases.
- The rotor, which can be a permanent magnet or soft iron, aligns with the stator’s energized coils.
- By sequentially energizing different coils, the rotor is pulled toward the changing magnetic fields, causing stepwise rotation.
Structure and Components
A stepper motor consists of the following key components:
- Stator (Stationary Part): The stator is the outer stationary part of the stepper motor, consisting of multiple electromagnetic coils arranged in a circular pattern. These coils are grouped into phases and are responsible for generating the magnetic fields that drive the rotor’s movement. The number of poles in the stator determines the step angle of the motor, influencing precision and resolution.
- Rotor (Rotating Part): The rotor is the moving part of the stepper motor, designed to align with the magnetic field generated by the stator. Depending on the motor type, the rotor can be a permanent magnet (as in PM stepper motors), a soft iron core (as in variable reluctance stepper motors), or a combination of both (as in hybrid stepper motors).
- Bearings and Shaft: The shaft is a central rotating component that transmits mechanical motion from the rotor to external systems. It is supported by high-precision bearings on both ends, which reduce friction and ensure smooth, stable rotation.
- Housing: The housing encloses the stator and rotor, providing structural integrity and protection against dust, debris, and environmental factors. It is typically made of metal to ensure durability and heat dissipation. Some stepper motor housings include cooling fins or ventilation to prevent overheating during continuous operation.
Control Mechanism
Stepper motors operate using an open-loop control system, meaning they do not require position feedback. Instead, they rely on pre-determined electrical signals to move a specific number of steps. The control process involves:
- The CNC controller sends a pulse sequence to the stepper driver.
- The driver energizes the stator coils in a specific order.
- The rotor aligns with the changing magnetic fields, moving in stepwise increments.
- The number of pulses determines the total movement, while pulse frequency controls speed.
Although stepper motors do not require feedback, some advanced setups include encoders to improve accuracy and prevent missed steps.
Advantages
Stepper motors are widely used in CNC routers due to several benefits:
- Cost-Effective: They are more affordable compared to servo motors, making them ideal for budget-conscious users.
- Simple Control System: Operate in an open-loop system, eliminating the need for complex feedback mechanisms.
- High Holding Torque: Maintains position without continuous power, which is beneficial for applications requiring stationary holding force.
- Reliability and Durability: With fewer components prone to wear, stepper motors are robust and long-lasting.
- Good for Low-Speed Applications: They offer strong torque at lower speeds, making them effective for detailed engraving and cutting.
Limitations
Despite their advantages, stepper motors have some limitations:
- Torque Loss at High Speeds: As speed increases, torque significantly decreases, affecting performance in high-speed operations.
- Open-Loop Control: Without feedback, missed steps can occur, leading to reduced accuracy in high-load applications.
- Resonance and Vibration Issues: Can experience mechanical vibrations, particularly at certain step frequencies, impacting smoothness.
- Less Energy Efficient: Consume power continuously, even when holding position, leading to higher energy usage.
Stepper motors are an excellent choice for CNC routers that require precise motion control at a lower cost. Their simple operation and high reliability make them ideal for applications such as wood engraving, signage, and light material cutting.
Understanding Servo Motors
Servo motors are widely used in industrial CNC routers due to their superior precision, speed, and dynamic performance. Unlike stepper motors, which operate in an open-loop system, servo motors use a closed-loop control system with feedback mechanisms to achieve high accuracy and efficiency. Below, we understand servo motors in detail from multiple aspects.
Working Principle of Servo Motors
A servo motor operates based on a closed-loop control system, meaning it continuously adjusts its position, speed, and torque based on feedback from an encoder or sensor. The core working mechanism involves three main components:
- Controller sends a command signal to the servo drive, specifying the desired movement.
- Servo Drive amplifies the signal and sends the necessary power to the motor.
- Encoder (Feedback Device) continuously monitors the actual motor position and speed, sending data back to the controller to correct any deviations.
This feedback loop ensures that the motor moves precisely to the commanded position, eliminating step loss or positioning errors common in open-loop systems like stepper motors.
Structure and Components
A servo motor consists of the following key components:
- Stator (Stationary Part): The stator consists of a series of electromagnetic windings that generate a rotating magnetic field when powered. This field interacts with the rotor, causing it to move smoothly and efficiently.
- Rotor (Rotating Part): The rotor is connected to the motor shaft and rotates in response to the stator’s magnetic field. In servo motors, the rotor is typically made of high-energy permanent magnets, which allow for strong torque and high-speed operation.
- Encoder (Feedback Device): It continuously measures the rotor’s position, speed, and direction, sending this data to the controller. This feedback allows the system to correct any discrepancies between the desired and actual position, ensuring high accuracy and smooth motion.
- Bearings and Shaft: The motor shaft is directly connected to the rotor and transmits the motion to the CNC router’s moving parts. Bearings support the shaft, reducing friction and enhancing smooth operation.
- Housing and Cooling System: The housing protects internal components from dust, debris, and environmental conditions. Many high-performance servo motors incorporate cooling fans or heat sinks to manage the heat generated during prolonged operation.
Control Mechanism
Servo motors utilize a closed-loop control system, which continuously monitors and adjusts performance using feedback. The control process involves:
- Command Input: The CNC controller sends motion commands to the servo drive.
- Power Adjustment: The servo drive supplies the appropriate voltage and current to the motor.
- Real-Time Feedback: The encoder measures actual motor movement and sends data to the controller.
- Correction & Adjustment: If discrepancies are detected, the servo drive makes immediate adjustments to match the desired motion.
This feedback system allows servo motors to operate with high precision, smooth motion, and dynamic speed control, making them ideal for demanding CNC applications.
Advantages
Servo motors offer several key benefits over stepper motors, particularly for high-speed and high-precision CNC applications:
- High Accuracy and Precision: Closed-loop control ensures precise positioning without missed steps.
- High-Speed Performance: It delivers consistent torque even at high speeds, making it suitable for fast-moving CNC routers.
- Smooth Motion Control: Eliminates vibration and resonance issues common in stepper motors.
- Energy Efficiency: Uses power dynamically, reducing energy consumption when idle or under low load.
- Higher Torque Capabilities: Capable of handling heavy loads and demanding applications.
- Adaptive ControlP: Adjusts torque and speed in real time, ensuring optimal performance for different machining conditions.
Limitations
While servo motors excel in performance, they do have some disadvantages:
- Higher Cost: They are more expensive than stepper motors due to their advanced control and feedback mechanisms.
- Complex Control System: Requires additional components (servo drive, encoder), making setup and integration more complex.
- Tuning and Maintenance: Proper tuning is required to optimize performance, and encoders and feedback systems may need periodic maintenance.
Overheating Risks: In high-power applications, cooling mechanisms (fans or liquid cooling) may be required.
Servo motors are the preferred choice for high-speed, high-precision CNC machining due to their closed-loop control, high torque, and smooth motion. While they come at a higher cost and require more complex integration, their superior accuracy and performance make them ideal for industrial applications, heavy-duty cutting, and precision machining.
Key Comparison Factors
When selecting a motion control system for your CNC router, you first need to understand the differences between stepper motors and servo motors. Below are the key comparison factors that affect performance, cost, and application suitability.
Accuracy & Precision
- Stepper Motors: They achieve precise positioning by moving in discrete steps, typically with a step angle of 1.8° per step (200 steps per revolution for standard models). Their open-loop control system does not rely on feedback, meaning they move in fixed steps. While this allows for repeatable motion, it also makes them susceptible to missed steps under high loads or rapid acceleration, leading to cumulative positioning errors.
- Servo Motors: They offer higher accuracy and precision due to their closed-loop control system, which continuously monitors and corrects position errors using an encoder. This real-time feedback mechanism ensures that the motor reaches the exact commanded position, even under varying loads or at high speeds. Additionally, servo motors dynamically adjust torque and speed to maintain smooth motion without resonance or step loss, making them ideal for applications requiring high precision and reliability.
Speed & Torque Performance
- Stepper Motors: Stepper motors provide high torque at low speeds, making them effective for precise, controlled movements. However, as speed increases, their torque drops significantly. This limits their maximum speed to around 1,000–2,000 RPM in most CNC applications. They are well-suited for applications that require slow, controlled positioning.
- Servo Motors: Maintain high torque across all speed ranges, making them ideal for fast operations. They can reach speeds of 3,000–5,000 RPM or more, depending on the motor specifications. Unlike stepper motors, servo motors do not suffer from torque loss at high speeds because their closed-loop control system continuously adjusts power output based on demand. As a result, servo motors excel in high-speed CNC machining, heavy-duty cutting, and industrial automation.
Cost & Affordability
- Stepper Motors: They have a lower upfront cost, making them more budget-friendly. Their simple open-loop control system eliminates the need for expensive feedback devices, reducing overall system costs. Additionally, stepper motors require less complex drivers, further lowering initial investment and maintenance expenses. This cost-effectiveness makes them ideal for hobbyists, small businesses, and light-duty CNC applications.
- Servo Motors: More expensive than stepper motors due to their advanced control systems, closed-loop feedback mechanisms, and high-performance capabilities. They require servo drives, encoders, and tuning adjustments, increasing both initial purchase and setup costs. However, their higher efficiency, reduced power consumption, and long-term reliability can offset these costs, making them a better investment for industrial applications.
Control System Complexity
- Stepper Motors: They use a simple open-loop control system, meaning they move a fixed number of steps in response to input pulses without requiring feedback. This makes them easier to set up and operate, as they do not need encoders or complex tuning procedures. While this simplicity reduces cost and setup time, it also means that missed steps cannot be corrected, potentially leading to positioning errors under high loads or at high speeds.
- Servo Motors: Relying on a closed-loop control system, which continuously monitors position, speed, and torque through an encoder or resolver. This requires a more complex control setup, involving a servo drive, feedback processing, and PID tuning to optimize performance. Unlike stepper motors, servo systems can automatically correct errors, ensuring precise movement even under variable loads. Their dynamic responsiveness and accuracy make them essential for high-precision and high-speed CNC applications.
Energy Efficiency
- Stepper Motors: Generally less energy-efficient because they draw full current at all times, regardless of whether they are moving or holding position. Their open-loop system lacks dynamic power adjustment, meaning energy is continuously consumed even when no motion is required. This results in higher heat generation, which can lead to additional cooling requirements and energy waste, especially in high-duty applications.
- Servo Motors: More energy-efficient due to their closed-loop control system, which dynamically adjusts power consumption based on load and movement requirements. Unlike stepper motors, they only draw power when needed, significantly reducing energy waste. Additionally, servo motors operate at higher efficiency levels by maintaining optimal torque and speed without excessive current draw. This not only lowers electricity costs but also reduces heat buildup, minimizing the need for additional cooling solutions.
Reliability & Maintenance
- Stepper Motors: Known for their simplicity and durability, making them highly reliable for many CNC applications. With no need for encoders or feedback loops, they have fewer components that can fail, reducing maintenance requirements. However, stepper motors generate more heat due to constant current draw and can experience resonance or missed steps under heavy loads, potentially affecting long-term accuracy.
- Servo Motors: Offer higher reliability in demanding applications due to their closed-loop control and dynamic adjustment capabilities. The built-in feedback system ensures accurate positioning and prevents issues like step loss or stalling, even under varying loads. However, because servo motors include encoders, servo drives, and complex tuning mechanisms, they require periodic calibration and maintenance to ensure optimal performance.
Application Suitability
- Stepper Motors: These are best suited for low to medium-speed CNC applications that require precise but cost-effective motion control. They excel in tasks where high torque at low speeds, repeatable positioning, and simple control systems are sufficient, such as signage, wood engraving, and PCB cutting. Their affordability and ease of integration make them ideal for hobbyists, small businesses, and entry-level CNC routers.
- Servo Motors: They are the preferred choice for high-speed, high-precision, and heavy-load CNC applications, thanks to their closed-loop feedback system, high torque at all speeds, and superior efficiency. They are widely used in industrial CNC routers, such as metal cutting and furniture manufacturing. While they require a higher investment and more complex setup, their ability to handle demanding workloads with consistent performance makes them indispensable for professional and industrial-grade CNC operations.
Understanding the key comparative factors allows users to make an informed decision that balances performance, budget, and long-term productivity. This comparison provides a clear guide for CNC router users to determine the best motor based on their specific needs.
Which Motor Should You Choose?
The choice between a stepper motor and a servo motor depends on your CNC router application, budget, and performance needs. Below is a breakdown of which motor is better suited for different scenarios:
Choose a Stepper Motor If
- You need an affordable, cost-effective solution for your CNC router.
- Your application requires moderate precision and speed without high dynamic loads.
- You prefer a simple control system with easy integration.
- Your CNC tasks involve wood engraving, PCB milling, signage cutting, or light-duty metal cutting.
- You do not need feedback correction or operation at high speeds.
Choose a Servo Motor If
- You require high precision and speed, especially for industrial CNC applications.
- Your machine operates at variable loads and needs real-time feedback correction.
- You need high torque at all speeds for heavy-duty cutting or metal machining.
- Energy efficiency is important, and you want to minimize heat generation.
- Your CNC router is used for large furniture batch production, metal cutting, mold making, or professional machining.
If you need a budget-friendly, reliable motor for low-to-medium-speed applications, a stepper motor is a great choice. However, if precision, speed, and efficiency are your top priorities, and you’re willing to invest in a more advanced control system, a servo motor will deliver superior long-term performance. Carefully assessing your application requirements, budget, and expected workload will help you make the best decision for your CNC router.
Summarize
Stepper motors and servo motors each offer distinct advantages for CNC routers, with stepper motors being more affordable, simpler to control, and well-suited for low-to-medium-speed applications, while servo motors provide higher precision, greater speed, and consistent torque across all operating ranges. If cost-efficiency and ease of use are your priorities, stepper motors are a great choice, but if performance, accuracy, and long-term reliability matter most, investing in servo motors is the smarter option. Before making a decision, carefully evaluate your CNC router’s specific workload, precision needs, and available budget to ensure you choose the motor that best meets your operational goals.
AccTek CNC, a professional CNC router manufacturer, provides high-quality solutions tailored to diverse machining applications. Whether you need a cost-effective stepper motor-driven CNC router for precision engraving and woodworking or a high-performance servo motor-powered system for industrial-grade cutting and metal fabrication, we offer customized configurations to meet your specific requirements. With a commitment to innovation, durability, and customer support, AccTek CNC is the ideal choice for businesses and professionals looking to maximize productivity and achieve superior machining results.