- 14-20 Min Read
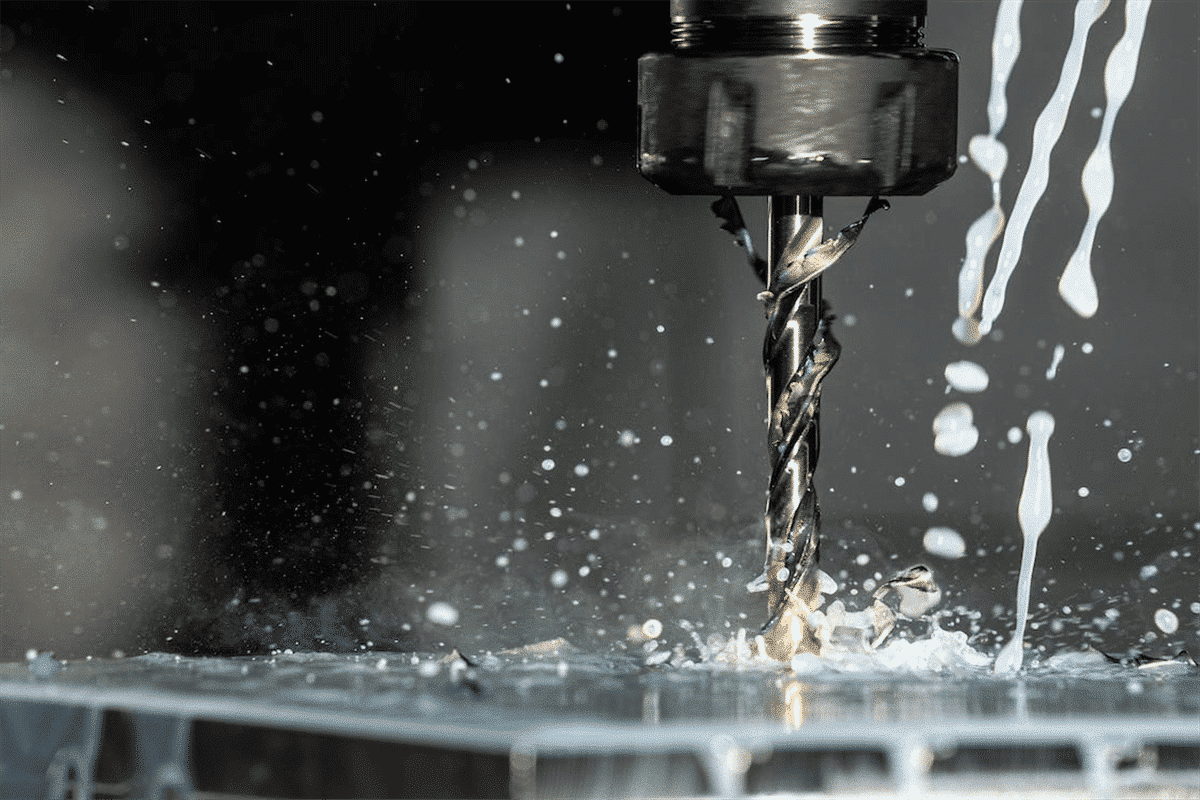
In the world of CNC machining, the router bit is the basic tool that transforms raw material into a finished product with precision and efficiency. Whether you are a seasoned professional or a hobbyist, selecting the right CNC router bit is beneficial for achieving optimal performance and quality in your projects. But with a myriad of options available, navigating the landscape of CNC router bits can be a daunting task for beginners. From understanding the different types of bits to deciphering the nuances of materials and coatings, the journey to finding the perfect bit for your project requires careful consideration and informed decision-making.
In this comprehensive buyer’s guide, we are designed to navigate you through the myriad of options available, equipping you with the knowledge and insights needed to make confident choices. Whether you’re delving into the world of CNC machining for the first time or looking to expand your repertoire, join us as we uncover the key factors to consider when selecting router bits and explore advanced techniques to unleash the full potential of these indispensable tools.
The Importance of Choosing the Right CNC Router Bit
Selecting the right CNC router bit is a critical decision that can significantly impact the quality, efficiency, and overall success of your machining projects. Here’s why this choice is so important:
- Precision and Quality of Work: The type and quality of the router bit you use directly affect the precision of your cuts and the overall finish of your workpiece. Different bits are designed for specific tasks—such as cutting, engraving, or shaping—and using the appropriate bit ensures clean, accurate results with minimal need for post-processing.
- Efficiency and Productivity: Using the correct router bit can dramatically improve your workflow efficiency. Bits designed for specific materials and cuts reduce the machining time, minimize tool wear, and lower the risk of errors or damage. This leads to faster project completion and better use of your machine’s capabilities, ultimately boosting productivity.
- Material Compatibility: Not all router bits are created equal, especially when it comes to the material you’re working with. Wood, plastic, metal, and composites each require bits with specific geometries and coatings to handle their unique properties. Choosing the right bit for your material ensures optimal performance, reduces wear and tear on both the bit and the CNC machine, and prevents costly material wastage.
- Cost-Effectiveness: Investing in high-quality, appropriate router bits can save you money in the long run. While it might be tempting to opt for cheaper alternatives, inferior bits can wear out quickly, produce poor results, and even damage your workpiece or CNC machine. High-quality bits, though potentially more expensive upfront, offer better durability and performance, resulting in long-term savings.
- Versatility and Capability Expansion: Having the right selection of CNC router bits expands the capabilities of your CNC machine, allowing you to take on a wider variety of projects with confidence. Specialized bits enable complex cuts and intricate designs that would be difficult, if not impossible, to achieve with general-purpose bits. This versatility can open up new opportunities for creativity and business growth.
- Safety: Using the wrong router bit can pose serious safety risks. Bits that are not suited for the material or the task at hand can break, causing damage to the machine and posing injury hazards to the operator. Choosing the right bit ensures safer operation, protecting both the user and the equipment.
The importance of selecting the right CNC router bit cannot be overstated. It is an investment in the quality, efficiency, and safety of your work. By understanding the specific requirements of your project and choosing the appropriate bit, you set the foundation for successful and precise CNC machining.
Types of CNC Router Bits
CNC router bits come in a variety of types, each designed for specific tasks and materials. Understanding the different types of bits and their uses is beneficial for achieving optimal results in your CNC projects. Here are some common types of CNC router bits:
End Mills
- Flat End Mills: These bits have a flat tip and are used for cutting flat surfaces, roughing out material, and making precise cuts and pockets. They are versatile and suitable for a wide range of materials.
- Ball Nose End Mills: These bits have a rounded tip, perfect for creating smooth, contoured surfaces and 3D carving. They excel in applications requiring detailed and intricate work, such as mold making and engraving.
- V-Bits: Characterized by a V-shaped tip, V-bits are excellent for V-carving, sign making, and engraving. They are used to create sharp, intricate details and clean edges.
Router Bits
- Straight Bits: These bits are used for making straight cuts and grooves. They are ideal for cutting dadoes, rabbets, and mortises.
- Round-Over Bits: Designed to create a rounded edge on the material, these bits are commonly used for adding decorative edges to furniture and cabinetry.
- Ogee Bits: These bits produce an S-shaped profile, adding an elegant, decorative edge to moldings and trim work.
Specialty Bits
- Engraving Bits: Available in various shapes and angles, these bits are specifically designed for detailed engraving work, suitable for creating fine text and intricate patterns.
- Surfacing Bits: With a wide cutting diameter, surfacing bits are used for flattening large surface areas, such as preparing spoil boards or leveling slabs.
- Keyhole Bits: These bits create keyhole-shaped slots for hanging hardware, commonly used on the back of picture frames and plaques.
- Thread Mills: Used to cut threads into materials, thread mills provide an alternative to traditional tapping methods. They are particularly useful for creating threads in hard materials or for large diameters.
Toolpath-Specific Bits
- Up-Cut Bits: These bits pull the material chips upwards, which helps in clearing out the material and reducing heat. They are suitable for deeper cuts and provide a clean bottom edge but may cause splintering on the top surface.
- Down-Cut Bits: These bits push the material chips downwards, producing a clean top edge with minimal splintering. However, they are not as effective at clearing chips from the cut and are typically used for shallower cuts.
- Compression Bits: Combining both up-cut and down-cut flutes, compression bits minimize tear-out and leave clean edges on both the top and bottom surfaces, making them perfect for cutting laminates, plywood, and composites.
- Spiral Bits: Available in single, double, and triple flute designs, spiral bits offer varying balances of cutting speed and finish quality. They are versatile and suitable for a range of materials, from wood to plastics to metals.
Understanding the different types of CNC router bits and their specific applications allows you to select the right tool for your project, ensuring optimal performance and quality in your machining tasks.
Materials used in CNC router bit
CNC router bits are manufactured from various materials, each offering distinct properties that make them suitable for specific tasks and materials. The most common materials are High-Speed Steel (HSS), carbide, and diamond. Here’s a detailed overview of each:
High-Speed Steel (HSS) Bit
High-Speed Steel (HSS) is a popular material for CNC router bits, known for its durability, versatility, and cost-effectiveness. HSS bits are designed to perform well at high speeds and maintain their hardness even at elevated temperatures, making them a reliable choice for a variety of machining tasks.
Applications
- Woodworking: Ideal for cutting, shaping, and engraving softwoods and hardwoods.
- Metalworking: Suitable for cutting softer metals like aluminum, brass, and mild steel. They are often used in prototyping and small-scale metal fabrication.
- Plastic Cutting: Effective for machining various plastics, including acrylic and polycarbonate.
- Composite Materials: Can be used to cut certain composite materials, though care must be taken due to potential wear.
- Prototyping and Hobbyist Projects: Frequently used in DIY projects, prototyping, and small-scale manufacturing due to their affordability and versatility.
Advantages
- Affordability: HSS bits are less expensive than carbide bits, making them a cost-effective choice for many applications.
- Versatility: These bits can handle a variety of materials and tasks, making them a versatile tool in any workshop.
- Resharpenable: HSS bits can be resharpened multiple times, extending their lifespan and maintaining cutting performance.
- Toughness: They are less brittle than carbide bits, making them less prone to chipping and breaking, which is especially useful when working with tougher materials.
Limitations
- Wear Resistance: HSS bits wear out faster than carbide bits, especially when used on harder materials or in high-volume production settings.
- Heat Sensitivity: Although resistant to high temperatures, HSS bits are not as heat-resistant as carbide, which can lead to faster dulling when used at extremely high speeds or with hard materials.
- Limited to Softer Materials: While versatile, HSS bits are not suitable for cutting very hard or abrasive materials, where carbide or other materials would be a better choice.
Carbide Bit
Carbide bits are made from a compound of carbon and tungsten, offering exceptional hardness and wear resistance. These bits are designed to maintain their sharpness and precision even under high-speed and high-heat conditions, making them a preferred choice for demanding machining tasks.
Applications
- Woodworking: Cutting, shaping, and engraving hardwoods, softwoods, MDF, plywood, and other engineered wood products.
- Metalworking: Machining harder metals such as stainless steel, cast iron, and non-ferrous metals like aluminum and brass. They are ideal for metal fabrication and precision engineering tasks.
- Plastic Cutting: Cutting and engraving tougher plastics and composites, including acrylic, polycarbonate, PVC, and fiberglass.
Advantages
- Durability: Carbide bits have a longer lifespan compared to high-speed steel (HSS) bits due to their high wear resistance.
- Heat Resistance: Carbide bits maintain their hardness and sharpness at high temperatures, allowing for faster cutting speeds and prolonged use without losing efficiency.
- Precision: They provide clean, precise cuts and are less prone to dulling, which is beneficial for achieving high-quality finishes on various materials.
- Efficiency: The longer lifespan and consistent performance of carbide bits mean fewer tool changes and less downtime, enhancing overall productivity.
Limitations
- Cost: Carbide bits are more expensive than HSS bits. The higher upfront cost can be a consideration for budget-conscious users, though their longer lifespan often offsets this expense.
- Brittleness: While carbide is extremely hard, it is also more brittle than HSS. This makes carbide bits more susceptible to chipping or breaking if mishandled or subjected to excessive force.
- Specialized Use: For some softer materials and less demanding applications, the benefits of carbide bits might not justify their higher cost. In such cases, HSS bits might be more appropriate.
Diamond Bit
Diamond CNC router bits are at the pinnacle of cutting tool technology, offering unmatched hardness and durability. These bits are typically either coated with diamond particles (diamond-coated) or made from a solid polycrystalline diamond (PCD). They are designed for the most demanding machining tasks, where exceptional precision and longevity are required.
Applications
- Glass and Ceramics: Ideal for cutting and engraving glass, ceramics, and other brittle, hard materials.
- Stone and Concrete: Used for machining natural and synthetic stones, as well as concrete and masonry.
- Abrasive Composites: Effective for cutting highly abrasive composite materials, such as carbon fiber, fiberglass, and laminated materials.
- High-Precision Work: The first choice for tasks requiring extreme precision and fine detail, such as in the electronics, fine jewelry, and medical device industries.
Advantages
- Extreme Hardness: Diamond is the hardest known material, providing superior cutting ability and maintaining sharpness far longer than any other material.
- Wear Resistance: Exceptional durability and resistance to wear, making diamond bits ideal for cutting abrasive materials without significant loss of performance.
- Precision: Offers the finest cutting edge, enabling highly detailed and precise work.
- Longevity: Extremely long-lasting, reducing the frequency of bit changes and minimizing downtime in production processes.
Limitations
- Cost: Diamond bits are significantly more expensive than both HSS and carbide bits. The high initial cost can be a barrier for some users, though their extended lifespan often justifies the investment.
- Specialized Applications: Best suited for specific, high-value tasks and materials. For general-purpose use or softer materials, HSS or carbide bits may be more appropriate and cost-effective.
- Handling and Use: This requires careful handling to avoid damage, as diamond bits, while extremely hard, can be susceptible to chipping if improperly used.
CNC Router Bits Coating
Coatings on CNC router bits play a key role in enhancing performance and extending the lifespan of the tools. Three common coatings are Titanium Nitride (TiN), Titanium Aluminum Nitride (TiAlN), and Diamond-Like Carbon (DLC). Each of these coatings provides specific benefits that make them suitable for various applications and materials.
Titanium Nitride (TiN) Coating
Titanium Nitride (TiN) coating is a widely used surface treatment for CNC router bits, known for enhancing the performance and extending the lifespan of cutting tools. This golden-colored coating provides several benefits that improve the efficiency and durability of CNC router bits.
Role
- Wear Resistance: TiN coating significantly enhances the wear resistance of CNC router bits, protecting them from abrasion and mechanical wear.
- Heat Resistance: TiN provides excellent thermal stability, allowing the bit to withstand higher temperatures without losing hardness.
- Lubricity: The smooth surface of the TiN coating reduces friction between the bit and the material being cut, resulting in smoother cuts and less heat generation.
- Corrosion Resistance: TiN coating offers protection against corrosion, extending tool life in humid or corrosive environments.
Performance
- Enhanced Durability: The primary benefit of TiN coating is the significant increase in the durability and lifespan of the router bit. The coating reduces the rate of wear and tear, allowing the bit to maintain its cutting edge for longer periods.
- Improved Cutting Efficiency: Reduced friction and better heat dissipation result in smoother cuts and less resistance, enhancing the overall efficiency of the cutting process. This leads to cleaner, more precise cuts.
- Extended Tool Life: TiN-coated bits can handle more cutting cycles before needing replacement or resharpening, which reduces downtime and increases productivity in high-volume machining operations.
- Higher Cutting Speeds: With improved thermal stability, TiN-coated bits can operate at higher cutting speeds and feeds, increasing the throughput of machining processes.
Applications
- Woodworking: TiN-coated bits are used for cutting and shaping both softwoods and hardwoods, as well as engineered wood products like MDF and plywood.
- Metalworking: These bits are suitable for machining a variety of metals, including aluminum, brass, and some steel.
- Plastic Cutting: TiN-coated bits are effective for cutting plastics and composites, reducing the risk of melting or deformation due to heat buildup.
- Composites and Laminates: Ideal for cutting abrasive composite materials and laminates, where the wear resistance of the TiN coating prevents rapid dulling of the bit.
Aluminum Titanium Nitride (AlTiN) Coating
Aluminum Titanium Nitride (AlTiN) is a popular coating used on CNC router bits to enhance their performance and extend their lifespan. This advanced coating is known for its exceptional hardness, heat resistance, and oxidation resistance, making it suitable for demanding machining tasks.
Role
- Increased Hardness: AlTiN-coated bits are significantly harder than uncoated bits, allowing them to maintain a sharp cutting edge for longer periods.
- Heat Resistance: The coating improves the bit’s ability to withstand high temperatures generated during cutting, reducing thermal degradation.
- Oxidation Resistance: AlTiN provides a protective barrier against oxidation, preventing the bit from corroding and maintaining its cutting performance.
- Reduced Friction: The coating reduces friction between the bit and the work material, leading to smoother cuts and less wear on the bit.
Performance
- Longevity: The enhanced hardness and heat resistance of AlTiN-coated bits significantly extend their lifespan compared to uncoated bits or those with less advanced coatings.
- Cutting Speed: These bits can operate at higher cutting speeds, improving productivity and efficiency in machining operations.
- Surface Finish: The reduced friction and maintained sharpness result in a superior surface finish on the machined parts.
- Wear Resistance: The coating provides excellent wear resistance, reducing the frequency of bit replacements and maintenance.
Applications
- Hard Metals: Suitable for machining harder metals such as stainless steel, cast iron, and high-temperature alloys.
- Abrasive Materials: Effective for cutting abrasive materials like composites and hard plastics.
- High-Temperature Applications: Used in applications where high heat generation is a concern.
- Precision Machining: Used in applications requiring high precision and a superior surface finish, such as mold making and medical devices.
Diamond-Like Carbon (DLC) Coating
Diamond-like carbon (DLC) coating is an advanced surface treatment used to enhance the performance of CNC router bits. This coating mimics many of the desirable properties of diamond, providing significant improvements in wear resistance, hardness, and friction reduction.
Role
- Wear Resistance: DLC coating significantly reduces wear on the cutting edges of the bit, allowing for longer tool life and consistent performance over extended periods.
- Extreme Hardness: DLC provides a very hard and wear-resistant surface, making the bit more resistant to deformation and maintaining sharpness.
- Friction Reduction: DLC’s low friction properties minimize heat generation and reduce the likelihood of material sticking to the bit, which is especially beneficial when cutting metals and plastics.
- Corrosion Resistance: Highly resistant to chemical reactions and corrosion, further extending the lifespan of the bit.
Performance
- Superior Durability: The increased hardness and wear resistance of DLC-coated bits result in a longer lifespan.
- Improved Cutting Quality: With reduced friction and heat generation, DLC-coated bits can produce cleaner cuts with better surface finishes, especially in challenging materials.
- Higher Cutting Speeds: The improved thermal properties allow for higher cutting speeds without compromising the bit’s integrity, enhancing productivity.
- Versatility: DLC coating makes the bits suitable for a wider range of materials, including hard metals and abrasive composites.
Applications
- Metalworking: Ideal for cutting hard metals such as stainless steel, titanium, and hardened alloys. The coating helps maintain sharpness and cutting efficiency in demanding conditions.
- Plastic and Composite Cutting: Effective for machining abrasive plastics and composites, including carbon fiber and fiberglass. The reduced friction prevents melting and material build-up on the bit.
- High-Precision Machining: Frequently used for high-precision parts and components that require excellent surface finish and dimensional accuracy.
CNC Router Bit Handle Types and Sizes
The handle, or shank, of a CNC router bit is a critical component that ensures proper fitting into the router’s collet and stable operation during cutting. Understanding the different handle types and sizes is beneficial for selecting the right bit for your specific machine and application.
Shank Types
- Straight Shank: The straight shank is the most common type of shank used in CNC router bits. It has a uniform cylindrical shape along its entire length, making it easy to insert into the CNC router’s collet. Provides a stable and secure fit in the collet, commonly used for a wide variety of bits. Suitable for general-purpose use in woodworking, metalworking, and plastic cutting.
- Tapered Shank: The tapered shank features a gradual reduction in diameter from the bit end towards the shank end. This design allows for a more precise and secure fit in specialized collets or holders. The tapered design provides a more accurate and stable fit, reducing runout and vibration. Commonly used in metalworking and applications needing precise alignment and stability.
- Collet Shank: The collet shank is designed specifically to fit into a collet system, which is a clamping device that holds the bit securely in theCNC Collet shanks can be straight or have additional features like flutes or grooves to improve grip. Collet systems provide a strong and uniform clamping force around the shank, minimizing slippage. Ideal for tasks that require high rotational speeds, as the secure fit minimizes the risk of bit ejection.
Shank Sizes
- Standard Sizes: These handles come in various standard sizes to accommodate different bit shank diameters. The two most common standard sizes are 1/4 inch and 1/2 inch, though other sizes such as 1/8 inch or 3/8 inch may also be available depending on the CNC router model.
- Compatibility: Compatibility of the handle depends on the specific CNC router’s collet system. Some routers may have interchangeable collet systems, allowing you to switch between different sizes to accommodate various bit shank diameters. Additionally, some CNC routers may have proprietary collet systems, so it’s essential to check compatibility with the manufacturer’s specifications or documentation.
Application-specific considerations
When selecting a CNC router bit, it’s essential to consider the specific application you intend to use it for. Different applications require different cutting characteristics, materials, and finishes. Here are application-specific considerations:
Woodworking
- Material Type and Hardness: Different woods have varying hardness levels. Choose router bits with appropriate cutting edge materials (e.g., carbide) and geometries suitable for the specific wood type.
- Cutting Edge Geometry: For wood, common bit types include straight bits, spiral bits, and up/down cut bits. Choose the appropriate geometry based on the desired finish, chip evacuation, and material removal rate.
- Flute Configuration: Opt for router bits with multiple flutes for smoother cuts in wood. Single-flute bits are suitable for faster material removal but may leave rougher surfaces.
- Chip Evacuation: Efficient chip evacuation is beneficial to prevent clogging and overheating. Consider bits with up-cut or compression designs for effective chip removal, especially in deeper cuts.
Metalworking
- Material Compatibility: Select router bits designed specifically for metalworking, typically made from high-speed steel (HSS) or carbide. Carbide bits are preferred for their durability and heat resistance.
- Cutting Speed and Feed Rate: Metal requires slower cutting speeds and lower feed rates compared to wood. Choose router bits optimized for metal cutting with appropriate coatings to reduce friction and heat buildup.
- Helix Angle: Bits with higher helix angles (e.g., 30° or 45°) are suitable for metalworking as they provide efficient chip evacuation and reduce the risk of workpiece deformation.
Plastics
- Material Type: Plastics come in various types (e.g., acrylic, PVC, HDPE) with different properties. Choose router bits suitable for the specific plastic material to minimize melting, chipping, or cracking.
- Cutting Edge Material: Carbide router bits with polished or coated surfaces are ideal for plastics, offering improved chip removal and reduced friction to prevent material buildup.
- Router Bit Geometry: Use straight or spiral bits with up-cut or down-cut designs for clean cuts and smooth edges in plastics. Avoid bits with aggressive flutes that may cause chatter or surface defects.
Composites
- Material Composition: Composites consist of layers of different materials (e.g., fiberglass, carbon fiber) embedded in a resin matrix. Choose router bits capable of cutting both the fibers and the resin without delamination or fraying.
- Router Bit Coatings: Coated router bits (e.g., diamond-like carbon, titanium nitride) offer enhanced wear resistance and heat dissipation when machining composites, prolonging tool life and maintaining edge sharpness.
- Chip Control: Bits with specialized flute designs (e.g., diamond-patterned or diamond-coated) can help control chip formation and minimize dust buildup, especially when cutting fibrous composite materials.
By considering these factors and selecting router bits optimized for each material type, you can achieve precise, efficient, and high-quality machining results in woodworking, metalworking, plastics, and composites.
Summarize
Choosing the right CNC router bit is beneficial for achieving precise, efficient, and high-quality results in your machining projects. By understanding the different types of bits, and considering factors like material compatibility, bit size, and cutting speed, you can make informed decisions that enhance both efficiency and precision. Additionally, the choice of shank size and type ensures compatibility with your CNC router, enhancing performance and safety. Ultimately, investing time and effort in choosing the right CNC router bit tailored to your specific needs will pay off in the form of superior craftsmanship and operational efficiency.
AccTek CNC is a leader in the production and manufacturing of CNC routers, offering a variety of models designed to meet the diverse needs of users. With a focus on customization, AccTek CNC allows for adjustments in workbench size, tool selection, and control systems, ensuring that each user receives a solution perfectly tailored to their specific processing requirements. Whether you need a highly specialized setup or a versatile machine for various tasks, AccTek CNC provides the expertise and flexibility to deliver optimal performance and efficiency. Contact us today to start your CNC router plan.