- 13-18 Min Read
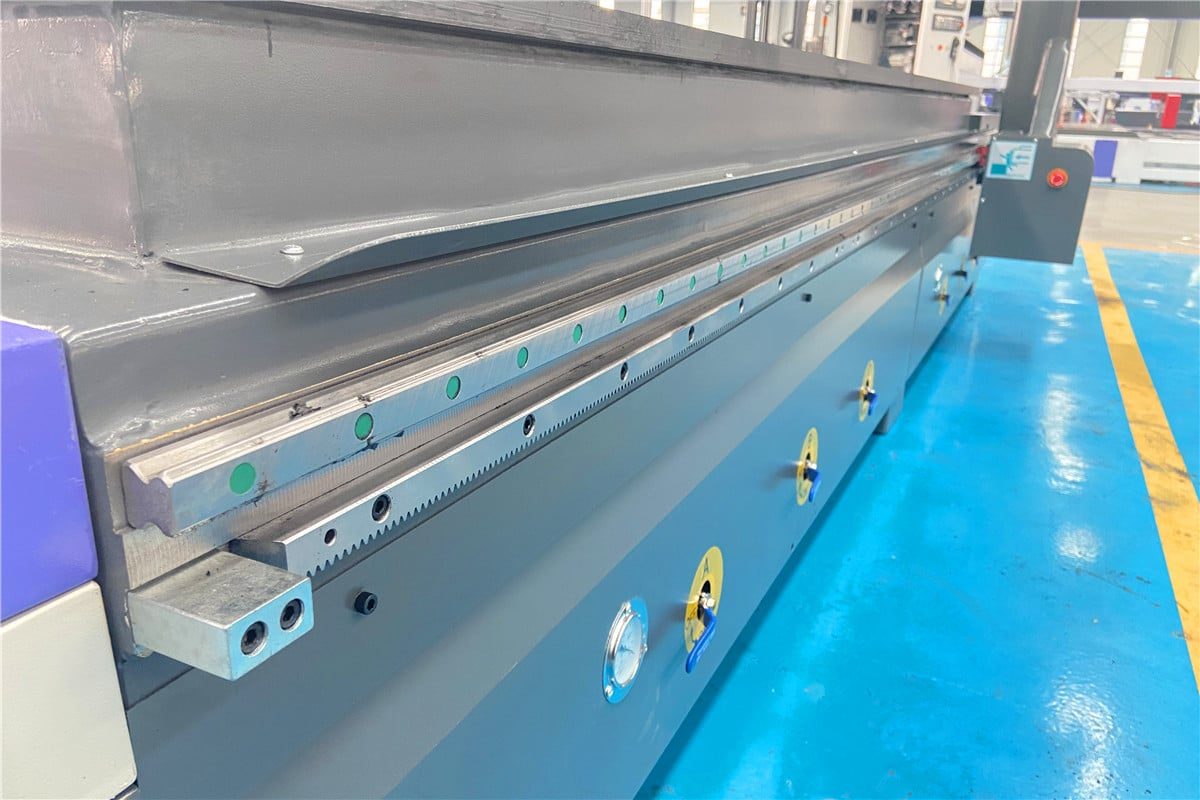
CNC routers are versatile machines capable of cutting and carving a wide variety of materials with precision and efficiency. The precision and efficiency of these machines depend heavily on the smooth operation of their guide systems, which facilitate accurate movements across axes. Selecting the right lubricant for CNC router guides not only minimizes wear and tear but also enhances machine accuracy, reduces downtime, and lowers maintenance costs. With various types of lubricants available, from oils to greases, and specific requirements based on machine design and operating conditions, making the right choice can be difficult.
This article explores the key considerations when selecting a lubricant for CNC router guides, including operating conditions, material compatibility, and environmental factors. Whether you’re maintaining a high-speed CNC router or a machine used in challenging industrial environments, understanding the role of lubrication and the options available is beneficial to keeping your equipment in peak condition. By the end, you’ll know how to make informed decisions that optimize your CNC router’s performance and ensure long-term reliability.
Importance of Lubricating CNC Router Guide Rails
CNC router guide rails are critical components that ensure the precise and smooth movement of the machine’s cutting head along its axes. Proper lubrication of these rails is beneficial to maintain the performance, accuracy, and longevity of the CNC router. Here are the key reasons why lubricating CNC router guide rails is so important.
The Role of Lubrication in CNC Machining
Lubrication ensures the smooth operation of critical components in CNC machining, particularly the guide rails. CNC router guide rails facilitate precise movements along the machine’s axes, enabling accurate cuts and efficient operation. Without proper lubrication, the friction between moving parts can cause excessive wear, heat generation, and eventual damage to the guide rails and associated components. This not only compromises machining accuracy but also increases the risk of mechanical failure. Lubrication minimizes friction, dissipates heat, and reduces the load on the motor systems, ensuring that the CNC router performs at its optimal level.
Benefits of Proper Guide Rail Lubrication
Proper lubrication of guide rails provides numerous benefits that extend the life and efficiency of CNC routers. Here are their specific manifestations:
- Reducing Friction and Wear: One of the primary benefits of proper guideway lubrication is the significant reduction of friction between moving components. Without adequate lubrication, metal-to-metal contact can lead to rapid wear, causing surface degradation and potential damage to the guide rails. Lubricants create a protective layer that minimizes friction, ensuring smoother motion and reducing the likelihood of mechanical failures.
- Improving Precision and Accuracy: Proper guideway lubrication ensures consistent, smooth movements along axes. This minimizes vibrations and jerky motions that could compromise machining accuracy. Lubricated guideways allow the CNC router to maintain tight tolerances and deliver high-quality cuts, especially in applications that require intricate designs or precise dimensions.
- Extending Component Life: Lubrication extends the lifespan of guideways and associated components by protecting them from environmental contaminants like dust, dirt, and moisture. The lubricating layer acts as a barrier, preventing corrosion and mechanical damage over time. This not only reduces the frequency of maintenance but also lowers the overall cost of ownership by delaying the need for component replacement.
- Maintaining Machine Performance: Consistent lubrication is key to maintaining the performance of CNC routers. By ensuring smooth movement and reducing resistance, lubricants help the machine operate efficiently without overloading the motors. This stability leads to reliable and predictable performance, minimizing production disruptions and ensuring the machine meets productivity demands.
Regular and appropriate lubrication reduces maintenance needs and downtime, leading to lower operating costs. Ultimately, proper lubrication safeguards the long-term investment in a CNC router, enhancing its reliability and productivity.
Factors to Consider When Selecting a Lubricant
Choosing the right lubricant for CNC router guide rails is a prerequisite for ensuring the best results for the machine. The lubricant must suit the specific operational conditions and machine requirements. Here are the key factors to consider:
Environmental Conditions
- Temperature and Humidity: For extreme temperature environments, lubricants must maintain their properties, such as flowability or viscosity, across the operating temperature range. High-temperature applications may need synthetic or high-temperature-tolerant lubricants, while low-temperature settings require options with low pour points to avoid thickening. Machines exposed to moisture or high humidity require water-resistant or corrosion-inhibiting lubricants to protect guide rails from rust and degradation.
- Dust and Contaminants: In dusty or dirty environments, lubricants with strong adhesion properties are beneficial to prevent displacement caused by particles. These lubricants create a stable protective film that shields guide rails from abrasive wear caused by dust accumulation. Some lubricants also include cleaning agents to help remove debris, further enhancing their protective qualities. A clean, controlled environment may allow for a broader range of lubricant options.
Machine Specifications and Materials
- Track Materials: The material of the guide rails significantly impacts the choice of lubricant due to differences in their physical and chemical properties. For steel tracks, lubricants with anti-corrosion additives or water-repellent properties are essential. Lubricants for aluminum tracks should provide effective wear protection without being overly abrasive. Choosing a lubricant that aligns with the specific material ensures optimal protection against wear, corrosion, and surface damage, enhancing the longevity and performance of the guide rails.
- Bearing Types: Rolling systems, such as ball or roller bearings, rely on precision and smooth motion. They require lubricants with low viscosity to minimize rolling resistance and maintain high-speed performance. Lubricants for rolling bearings often include additives to reduce friction and prevent overheating, ensuring consistent operation. Sliding systems, such as plain or linear bearings, involve surface-to-surface contact, which generates more friction. These bearings benefit from high-viscosity lubricants that create a robust film to reduce wear and distribute loads evenly.
Load and Speed Requirements
- Heavy-Duty Applications vs. Light-Duty Applications: In applications where CNC routers operate under high loads, the guide rails experience significant stress. These applications require high-viscosity lubricants that can form a strong, durable film to prevent direct metal-to-metal contact. For light-duty operations, low-viscosity lubricants are typically sufficient. These lubricants reduce friction effectively without creating unnecessary drag, ensuring smooth operation and energy efficiency.
- High-Speed vs. Low-Speed Operations: CNC routers operating at high speeds require lubricants with low viscosity to minimize resistance and ensure smooth, rapid movement. Low-viscosity lubricants allow for efficient distribution across the guide rails, reducing friction and heat generation during high-speed motion. In low-speed applications, the contact duration between moving surfaces is longer, which increases the risk of wear. High-viscosity lubricants are better suited for these conditions, as they provide a thicker film that can withstand prolonged surface-to-surface contact.
Compatibility with Other Lubricants and Materials
- Avoiding Chemical Interactions and Contamination: If the machine is transitioning from one lubricant to another, compatibility between the old and new lubricants needs to be considered. Mixing incompatible lubricants can cause chemical reactions, reducing their effectiveness or forming harmful residues that impair the performance of the CNC router. To avoid such issues, it is essential to use lubricants designed to be compatible with each other or to thoroughly clean the guide rails before introducing a new lubricant.
- Compatibility with Seals and Gaskets: Lubricants must be compatible with the seals and gaskets used in the CNC router to prevent leaks, swelling, or material degradation. Selecting a lubricant that is chemically neutral or specifically tested for compatibility with the materials used in the machine’s seals and gaskets ensures that these components remain intact and functional, preventing leaks and ensuring the longevity of the CNC router.
By considering these four aspects, you can ensure the chosen lubricant meets the operational needs of your CNC router while protecting its components and optimizing its performance.
CNC Router Lubricant Types
Selecting the right lubricant type based on your CNC router’s operating conditions ensures optimal performance, reduces maintenance needs, and extends the machine’s lifespan. Here are the primary types of lubricants used in CNC routers:
Oil-Based Lubricants
Oil-based lubricants are commonly used for CNC router guide rails due to their ability to flow freely and provide even coverage. They are particularly effective in high-speed operations, as their low viscosity minimizes resistance and friction.
- Mineral Oil-Based Lubricants: These are derived from petroleum and are commonly used in industrial applications due to their affordability and availability. They provide reliable lubrication for standard operating conditions and can be enhanced with additives to improve properties. These lubricants are suitable for general-purpose applications in CNC routers, particularly in environments with moderate speeds and loads. However, they may not perform as well in extreme temperature or high-stress scenarios, requiring more frequent reapplication compared to synthetic options.
- Synthetic Oil-Based Lubricants: These are engineered oils designed to perform in extreme conditions. They maintain their viscosity and lubricating properties over a wide temperature range and resist oxidation and thermal breakdown better than mineral oils. Synthetic oils often contain advanced additives that enhance thermal stability, oxidation resistance, and wear protection. Although more expensive, their durability and efficiency make them an excellent choice for CNC routers requiring high performance and reduced maintenance frequency.
- Specialty Oil-Based Lubricants: These are designed to meet specific operational needs and provide unique benefits for CNC routers. Food-grade oils, used in CNC routers operating in food processing or pharmaceutical manufacturing, are non-toxic, water-resistant, and compliant with strict hygiene standards. Rust-preventive oils protect metal surfaces from corrosion in humid or wet conditions, ensuring long-term durability. Cutting and cooling oils serve a dual purpose by reducing friction and dissipating heat during high-speed machining operations. These specialty oils cater to specialized applications, enhancing the performance and reliability of CNC routers in various industries.
Grease-Based Lubricants
Grease is a thicker lubricant made by combining oil with a thickening agent. It is well-suited for heavy-duty applications where high load capacities and prolonged protection are necessary.
- Lithium Grease: It provides excellent lubrication, wear protection, and water resistance, making it suitable for a wide range of operating conditions. This grease is effective in both low and high temperatures, maintaining stability and performance under varying thermal conditions. Its smooth texture and ease of application make it ideal for linear guide rails and bearings. However, it may not be the best choice for extreme environments with heavy loads or continuous exposure to moisture.
- Calcium Sulfonate Grease: It offers superior water resistance, corrosion protection, and thermal stability, making it an excellent choice for CNC routers operating in humid or wet conditions. This grease performs exceptionally well under heavy loads, providing robust wear protection for guide rails and bearings. Additionally, its natural resistance to oxidation and degradation extends service intervals, reducing maintenance costs. Though more expensive than lithium grease, its durability and versatility make it ideal for high-demand applications.
- Polyurea Grease: It is particularly well-suited for CNC routers in high-temperature applications, as it retains its properties under extreme heat. This grease is also highly resistant to water, making it a good choice for environments where moisture is a concern. Polyurea grease has excellent adhesion and does not easily break down, providing consistent lubrication over extended periods. However, its higher cost and potential incompatibility with other grease types require careful consideration when used in mixed lubrication systems.
Dry Lubricants
Dry lubricants are used in applications where oil or grease might attract dust or contaminants. They form a thin, solid film on the surface.
- PTFE-Based Dry Lubricants: They often referred to as Teflon lubricants, are ideal for CNC routers operating in dusty environments. PTFE-based dry lubricants form a thin, non-stick film on surfaces, reducing friction and preventing the accumulation of dust or debris. These lubricants are clean, non-greasy, and suitable for light-duty applications. However, they may not provide the load-bearing capacity required for heavy-duty operations and may need frequent reapplication for consistent performance.
- Graphite Lubricants: Graphite is inherently stable and can handle heavy loads without breaking down, making it suitable for demanding applications. They form a protective layer on guide rails and moving parts, reducing friction and wear. However, because it is a dry lubricant, it may not flow or distribute as easily as liquid or grease-based lubricants, limiting its use in some dynamic systems.
Solid Lubricant
Solid lubricants are materials that reduce friction and wear between surfaces without the need for a liquid or grease medium.
- Molybdenum Disulfide (MoS₂): It is a high-performance solid lubricant that excels in reducing friction under heavy loads and extreme pressure. Its unique layered structure allows for smooth sliding, even under severe operating conditions. MoS₂ is often used in CNC routers where components experience high stress or need enhanced wear resistance. While highly effective in demanding environments, it may not be ideal for applications requiring lightweight or clean lubricants due to its solid, powder-like nature.
- Tungsten Disulfide (WS₂): WS₂ is chemically stable, resists oxidation, and adheres well to surfaces, offering long-lasting protection for CNC router components. With a lower coefficient of friction than MoS₂, it provides even greater efficiency in high-load and high-temperature applications. However, its higher cost and specialized nature make it a choice primarily for high-performance or critical applications where other lubricants may fall short.
Each type of lubricant offers distinct advantages based on the specific needs of the machine and the operating conditions. Regular maintenance and proper selection of lubricants tailored to the machine’s specifications can significantly enhance the precision, efficiency, and reliability of CNC routers, ultimately contributing to a more productive and cost-effective manufacturing process.
Best Practices for Lubricating CNC Routers
To achieve the best lubrication effect for CNC routers, correct application and practice are the key steps. Here we introduce the techniques and safety measures that need to be followed throughout the lubrication process:
Cleaning and Preparing the Rails
- Removal of Old Lubricant and Contaminants: Before applying new lubricant, it is essential to remove old lubricant and any contaminants to ensure effective lubrication and prevent buildup. Use a lint-free cloth, soft brush, or air compressor to remove visible dust, debris, and old lubricant from the guide rails, ball screws, and other moving parts. For stubborn residue, apply a degreaser or cleaning solvent approved for CNC machines.
- Surface Preparation for New Lubricant Application: After cleaning, ensure all surfaces are free of residue or solvent. Wipe the parts dry using a clean, lint-free cloth to avoid moisture buildup. Check for visible damage, such as scratches or pitting, on the guide rails or ball screws. Damaged areas may require repair or replacement before applying lubricant.
Apply lubricant
- Appropriate Quantity and Distribution: Follow the manufacturer’s recommendations to ensure the right amount is applied to key areas such as guide rails, ball screws, and spindle bearings. Over-lubrication can attract dust and debris, creating buildup that hinders movement, while under-lubrication can lead to increased friction and wear. Distribute the lubricant evenly across all moving parts to provide consistent coverage, which ensures smooth operation and reduces the risk of uneven wear.
- Application Methods: The method of applying lubricant depends on the CNC router’s design. Manual lubrication can be done using tools like grease guns, brushes, or oil cans for precise application. For machines with automated lubrication systems, check that the system is functioning properly to dispense lubricant at the correct intervals and quantity. Ensure the lubricant reaches all critical points and work it into the moving parts by manually moving the axes after application.
Regular Inspection and Re-Coating
- Monitoring Lubricant Levels and Condition: Regularly monitor lubricant levels and assess its condition to maintain effective lubrication. If signs of deterioration are found, the deteriorated lubricant should be cleaned and replaced immediately to prevent damage to machine components. Use visual inspections and, where applicable, built-in monitoring systems to track lubricant performance and ensure timely reapplication.
- Scheduled Maintenance Intervals: Establish a routine maintenance schedule to ensure consistent lubrication. Frequency depends on machine usage, operating conditions, and manufacturer recommendations. For high-usage CNC routers, inspect and lubricate daily or weekly, while low-usage machines may only need monthly checks. Sticking to a schedule prevents unexpected failures and extends the life of critical components like guide rails and ball screws.
Safety Precautions
- Personal Protective Equipment (PPE): When lubricating CNC routers, always wear appropriate PPE to ensure safety. Use gloves to protect your hands from contact with oils, greases, or cleaning solvents that could irritate the skin. Wear safety goggles to shield your eyes from splashes during cleaning or lubrication. In poorly ventilated spaces, consider wearing a mask to avoid inhaling fumes, especially when using aerosol lubricants or solvents.
- Handling and Storage Guidelines: Handle lubricants carefully to avoid spills or contamination. Follow manufacturer guidelines for proper handling and application techniques. Store lubricants in a cool, dry location, away from direct sunlight and extreme temperatures. Keep containers tightly sealed to prevent contamination from dust, moisture, or air exposure. Label and organize lubricants clearly to avoid confusion between types, and always check expiration dates before use to ensure optimal performance.
By adhering to these best practices, CNC routers will remain well-lubricated, ensuring long-term reliability, precision, and efficiency while reducing maintenance costs and downtime.
Troubleshooting CNC Router Lubrication Problems
When lubrication issues arise in CNC routers, they can lead to a range of performance problems, such as decreased accuracy, overheating, and even machine failure. Identifying and addressing lubrication problems quickly is beneficial for maintaining a smooth operation. Here are common lubrication issues and how to troubleshoot them:
Over-lubrication and Under-lubrication
- Signs and Symptoms: Over-lubrication in machines can manifest through visible grease or oil accumulation on machine surfaces. Other indicators include frequent leakage around seals or excessive residue on components. Insufficient lubrication in machinery often manifests through increased friction, excessive heat generation, abnormal noise, and vibration. Reduced operational efficiency and frequent breakdowns are common indicators that lubrication is inadequate.
- Impact on Machine Performance and Maintenance: When lubrication is insufficient, friction between machine parts increases, causing heat buildup that can lead to premature wear or failure. However, over-lubrication complicates maintenance, requiring frequent cleaning and replacement of seals, and can cause clogging or damage to the lubrication system itself.
- Troubleshooting: Both conditions can be mitigated by training operators, following proper maintenance schedules, and using the right tools, such as oil flow meters or lubrication sensors, to maintain the optimal lubrication levels. For under-lubrication, ensure that the right amount and type of lubricant are applied based on manufacturer recommendations, operating conditions, and equipment specifications. For over-lubrication, reduce the amount of lubricant used. Implementing automated lubrication systems can help deliver precise amounts of lubricant, reducing human error.
Lubricant Contamination
- Identify the Source of Pollution: Dust, dirt, and debris from the work environment are common contaminants that can infiltrate lubrication systems. Additionally, poor maintenance practices, such as using unclean tools, can introduce contaminants. Another source is the accumulation of particles from cutting processes, which can easily be mixed with lubricant if not properly filtered. Lastly, moisture or water ingress from humid environments or washing procedures can compromise lubrication.
- Impact of Contaminants on Guiderail Performance: Dirt and debris can cause the rails to become abrasive, resulting in rough movement, noise, and accelerated degradation of the components. Particles may lead to scoring or pitting on the rails and bearings, reducing precision and causing parts to seize. Moisture contamination can lead to rust and corrosion, further impairing the smooth operation of the system. Overall, contaminants compromise the efficiency, accuracy, and lifespan of the CNC router’s rail system, increasing downtime and maintenance costs.
- Troubleshooting: Replace any contaminated lubricants with fresh, high-quality oil or grease, ensuring that the system is properly flushed to remove debris. Check and clean or replace the filtration system to prevent future contamination. Regularly inspect the work environment to minimize exposure to dust and dirt, and consider sealing systems to prevent external contaminants from entering. Finally, ensure that all components are correctly assembled and that moisture control measures are in place to avoid rust or corrosion.
Lubricant Compatibility
- Mixing incompatible lubricants: This can cause several problems, mainly affecting the performance and life of the CNC router. These include the breakdown of lubricating properties, leading to insufficient lubrication, which may cause excessive wear on components such as bearings, spindles, and motors. Mixing lubricants with differing chemical compositions can lead to gelling, thickening, or the formation of deposits, which may clog filters and passages, restricting fluid flow. The overall consequence is increased maintenance needs, potential machine downtime, and a reduced lifespan of critical components.
- Solving Compatibility Challenges: Before switching or mixing lubricants, consult the machine’s manual and verify the recommended lubricant specifications from the manufacturer. This includes checking for compatibility in terms of viscosity, base oil type, and additive package. If switching lubricants is necessary, thoroughly flush the system to remove any residual old lubricant. Lastly, regularly monitor the performance of the CNC router after lubrication changes, including checking for unusual sounds, increased friction, or other signs of abnormal operation.
During the operation of the CNC router, it is necessary to monitor and maintain a balanced lubrication system and proactively resolve various problems that arise during lubrication. Regular inspection, use of high-quality lubricants, and adherence to manufacturer guidelines can help prevent lubrication problems and extend the machine’s operational life.
Summarize
The appropriate lubricant helps reduce friction, prevent wear, and safeguard components against contaminants, ultimately improving the overall efficiency and reliability of the CNC router. By considering the factors we have mentioned in this article and using lubricants correctly according to the instructions in this article, you can achieve the best lubrication effect during the operation of CNC routers. Ultimately, investing time in choosing the right lubricant and adhering to a consistent lubrication schedule will help you achieve the best possible performance and longevity from your CNC router.
AccTek CNC stands out as a professional CNC router manufacturer in China, offering high-quality machines designed to meet the needs of various industries. With a strong reputation for precision, reliability, and technology, AccTek provides a wide range of CNC routers that are suitable for wood, metal, plastic, and composite materials. With customizable options and advanced features like powerful spindles, user-friendly control systems, and robust construction, our CNC routers are ideal for businesses looking to enhance production efficiency and maintain long-term operational success.