- 10-15 Min Read
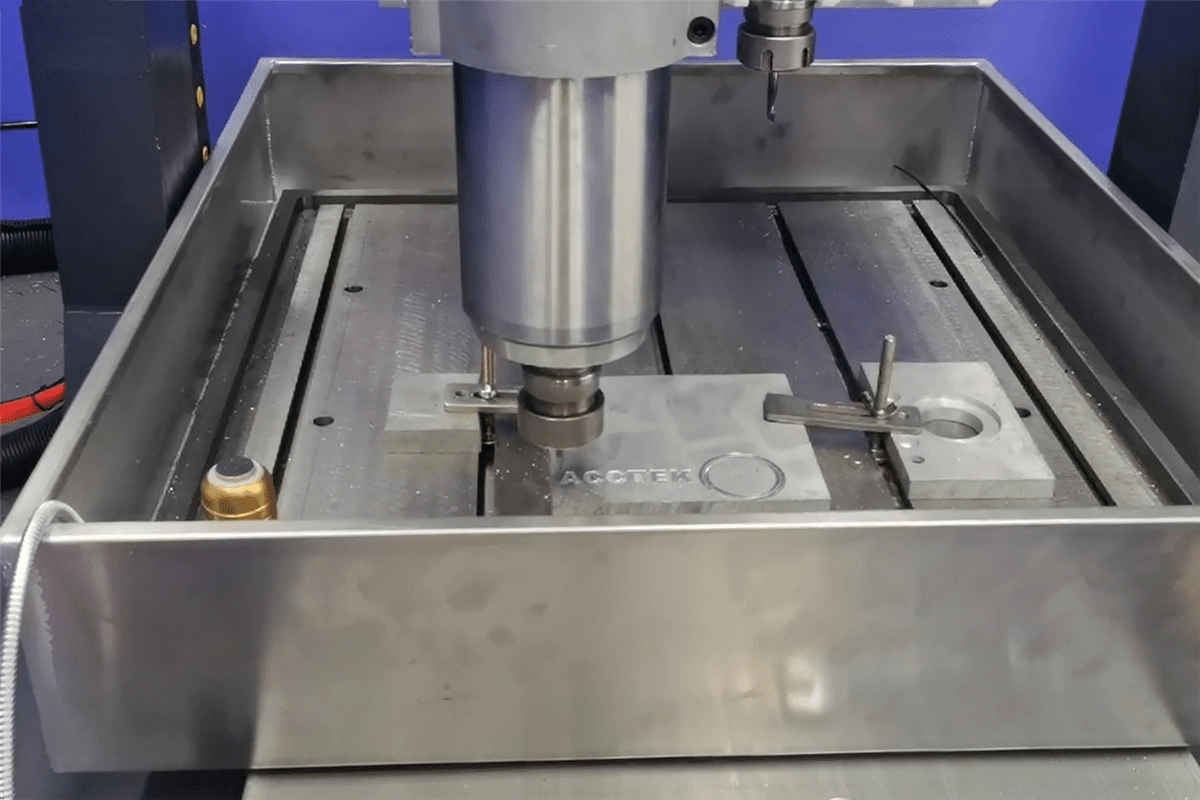
A CNC router is a versatile tool commonly associated with woodworking, but its capabilities extend far beyond that. While traditionally used for carving, cutting, and engraving wood, many people wonder if a CNC router can be used on metal materials. The short answer is yes, but with the right setup, tools, and adjustments. CNC routers can process a range of metals, including aluminum, brass, and soft steels, provided the machine is equipped with the correct tooling and settings.
In this article, we’ll explore the possibilities, limitations, and necessary considerations when using a CNC router on metal. Whether you’re a hobbyist looking to take your projects to the next level or a professional considering more material options for your CNC router, understanding how metal interacts with these machines will help you make an informed decision.
Understanding CNC Router
A CNC router is a powerful tool used in manufacturing and woodworking that automates the process of cutting, shaping, and engraving materials based on digital designs. In this section, we first understand the basic information about CNC routers, including their working principle and traditional applications.
Basic Principles of CNC Router
CNC routers are highly efficient machines that integrate precision, automation, and versatility to process materials based on computer-aided instructions. The basic principles of CNC routers revolve around the use of computer-controlled movements to guide a cutting tool along precise paths.
- Computer Control: The CNC router operates based on a program or set of instructions generated from CAD (Computer-Aided Design) or CAM (Computer-Aided Manufacturing) software. This program controls the movements of the router along various axes.
- Toolpath: The cutting or engraving tool follows a specific toolpath, a path defined by the program to cut the material. The toolpath is determined by the geometry of the workpiece and the desired finished design.
- Motorized Movement: Motors control the movement of the CNC router’tool along the axes. These motors receive commands from the CNC program to move the tool with high precision.
Traditional applications of CNC routers
With the ability to work with a variety of materials and offer high precision, CNC routers have become the backbone of many production processes. Here are some traditional application areas:
- Woodworking: CNC routers are most commonly used in woodworking, where they cut, carve, and shape wood for furniture, cabinetry, decorative items, and more. The precision of CNC technology allows for intricate designs, consistent results, and the ability to automate mass production processes. Whether crafting custom furniture or mass-producing wooden panels, CNC routers provide accuracy and efficiency.
- Sign Making: In the signage industry, CNC routers are extensively used to cut and engrave signs from a variety of materials, including wood, acrylic, foam, and metal. CNC routers enable sign makers to create detailed logos, lettering, and custom graphics with high precision and speed, ensuring that the final product meets both aesthetic and functional requirements.
- Furniture Manufacturing: CNC routers have revolutionized the furniture industry by enabling the mass production of furniture parts with intricate designs and uniform quality. They are used to cut and carve materials such as wood, MDF, plywood, and even plastic laminates to create everything from cabinet doors to tabletops.
- Model Making: CNC router machines can accurately cut, carve, and shape materials such as foam, plastic, and wood to create scale models of buildings, landscapes, and other structures. In the entertainment industry, CNC routers are used for creating props, sets, and special effects models.
- Mold Making: In mold making, CNC routers are used to carve and cut complex molds from materials such as aluminum, steel, or resin. CNC routers offer the precision necessary to create intricate mold cavities with tight tolerances, reducing the time and costs associated with traditional mold-making techniques.
These traditional applications of CNC routers demonstrate their versatility and value across multiple sectors, providing businesses with the ability to increase productivity, improve precision, and reduce production times.
Challenges of machining metal using a CNC router
Machining metal using a CNC router presents several challenges that operators must address to ensure precision and optimal results. Here are some key challenges:
Material Hardness
The hardness of the material can result in increased wear on tools, longer machining times, and the need for specialized cutting techniques. Harder metals, such as stainless steel, titanium, or hardened alloys, are more difficult to machine than softer materials like aluminum or copper. Harder materials resist cutting forces more, requiring more powerful machines, stronger tooling, and slower machining speeds.
Tool Selection
CNC routers typically come equipped with tools designed for non-metallic materials, such as wood and plastic. When machining metal, operators must invest in specialized tooling, such as carbide or diamond-coated bits, which can handle the demands of cutting harder materials. Choosing the wrong tool for the material or application can lead to tool wear, poor surface finish, or even tool breakage.
Heat Generation
Machining metal generates heat due to friction between the tool and the material. In softer metals, the heat is generally not a significant problem, but in harder metals, excessive heat can cause tool wear, thermal distortion of the workpiece, and even material changes such as hardening or warping. Additionally, without proper cooling or lubrication (like through coolant systems), excessive heat can cause tool failure and necessitate more frequent tool replacements.
Machine Rigidity
CNC routers designed for wood or plastic may lack the rigidity required to machine metals with the precision necessary for certain tasks. Metalworking typically requires higher machine rigidity to handle the forces involved during cutting without compromising accuracy. Insufficient machine rigidity can result in vibration or deflection during the cutting process, which compromises precision and surface finish.
Machining metal using a CNC router is certainly feasible, but it requires specialized tooling, adjustments to machine settings, and additional features to overcome the inherent challenges posed by the material’s hardness, heat generation, and rigidity requirements.
Enhancing a CNC Router Technology for Metal Cutting
The metal cutting capabilities of CNC routers have been significantly enhanced through various technological advancements. Here’ how improvements in five key areas contribute to superior cutting performance:
Tool Upgrades
Advanced cutting tools are beneficial for achieving high-quality metal cuts. Modern metal CNC routers often incorporate specialized tools such as:
- Carbide or PCD (Polycrystalline Diamond) Tools: These materials offer superior wear resistance, allowing for extended tool life and precision in cutting hard metals.
- Tool Coatings (e.g., TiN, TiAlN): Coatings reduce friction and enhance tool durability, providing better performance at higher cutting speeds and temperatures.
- Auto Tool Changers: Automatic tool changers(ATC) allow CNC routers to use different tools without manual intervention, improving efficiency and versatility when cutting various metals.
Spindle Power and Speed
The spindle is the heart of a CNC router, responsible for driving the cutting tool. Advances in spindle power and speed have drastically improved the cutting of metals:
- High Torque Spindles: Increased torque allows CNC routers to cut through thicker, harder metals with precision.
- High-Speed Spindles: Faster spindle speeds enable quicker material removal, improving productivity and surface finish on metal parts.
- Variable Speed Control: Modern routers come with the ability to adjust spindle speed based on the material and cutting conditions, allowing for optimized performance across a range of metals.
Rigid Structure
A CNC router’s structural rigidity is key to maintaining precision and reducing vibrations during metal cutting:
- Reinforced Frame Materials: Using materials such as steel or cast iron helps to create a solid foundation that absorbs vibrations and maintains cutting accuracy.
- Enhanced Gantry Systems: The gantry is designed for minimal flex, ensuring that the cutting tool stays precisely aligned with the workpiece even during heavy cuts.
- Vibration Dampening Technology: Anti-vibration systems are integrated to reduce chatter and improve surface finish during high-speed, high-load metal cutting operations.
Coolant System
Effective cooling during metal cutting reduces heat buildup, which can cause tool wear, material deformation, and poor surface quality. Modern CNC routers often feature advanced coolant systems:
- High-Pressure Coolant Systems: These systems direct coolant directly at the cutting tool and material, helping to reduce temperature, improve cutting performance, and extend tool life.
- Misting Systems: Some CNC routers use misting instead of flood coolant for more precise cooling, especially when cutting delicate or hard metals.
- Closed-Loop Coolant Recycling: This feature filters and recycles coolant, ensuring a consistent supply while reducing waste and lowering operating costs.
Advanced Control System
The control system is responsible for managing the CNC router’s operations, ensuring that cutting processes are efficient and precise:
- Adaptive Control Systems: These systems adjust cutting parameters such as feed rate, spindle speed, and depth of cut in real time based on material properties, ensuring optimal performance and quality.
- 3D Simulation Software: Advanced software can simulate the entire cutting process, allowing operators to optimize tool paths, avoid collisions, and minimize waste before cutting begins.
- Remote Monitoring and Diagnostics: Modern CNC routers are equipped with IoT capabilities that enable real-time performance monitoring, diagnostics, and maintenance scheduling, enhancing uptime and reliability.
Together, these advanced technologies ensure that CNC routers can handle a wider range of metals with greater efficiency, precision, and reliability, leading to higher-quality finished products and reduced operational costs.
Tips and best practices for using a CNC router on metal
When using a CNC router on metal, it’ essential to consider various factors. Here are some tips and best practices to ensure smooth operation and optimal results:
Material Selection
Not all metals are suitable for CNC routing. The hardness, thickness, and composition of the material must be considered to avoid excessive wear on tools or underperformance. Common materials for CNC routers include:
- Aluminum: Lightweight, easy to machine, and offers excellent corrosion resistance, making it a popular choice.
- Mild Steel: More challenging to cut, but suitable for many industrial applications.
- Stainless Steel: Tougher and more resistant to corrosion, requiring special attention in tool choice and cutting parameters.
- Brass and Copper: Softer metals that are easier to machine but can require special considerations due to heat buildup.
Ensure your CNC router is capable of handling the thickness of the material. Some machines might struggle with thicker metals and require slower feed rates or special cutting tools to ensure smooth cutting and precision.
Machine Calibration
Ensure that the machine is calibrated regularly to avoid misalignments and inaccuracies. This includes checking the:
- Tool Height: Adjust the Z-axis tool height frequently to ensure accurate depth cutting and avoid damaging the material.
- Workpiece Positioning: Ensure the workpiece is properly aligned to the machine’reference points to prevent shifting during machining.
- Tool Condition: Dull or damaged tools can cause poor finishes, inaccuracies, and increased wear on the machine. Regularly inspect and replace cutting tools when necessary.
- Check for Backlash and Worn Parts: Regularly inspect components like ball screws, guides, and bearings for wear. Backlash or loose parts can significantly impact precision, particularly when cutting metals.
- Spindle Speed and Feed Rates: Adjust spindle speeds and feed rates according to the type of metal you’re cutting. A slower feed rate and higher spindle speed work best for harder materials, while softer metals can be machined faster. Keep in mind that different tools will also have different optimal speed settings.
Programming Techniques
Effective programming is beneficial for optimizing cutting performance and ensuring accuracy when routing metal.
- Use Proper Toolpaths: The toolpath determines the cutting strategy. When working with metal, use adaptive or optimized toolpaths to maximize cutting efficiency and reduce the load on the machine. Avoid tight corners and unnecessary sharp turns, as they can cause tool deflection and poor finishes. Radial or helical toolpaths work better for metal cutting. For metal, climb milling (where the cutting tool moves in the same direction as the feed) is usually preferred over conventional milling. This reduces the risk of tool wear and provides a better surface finish.
- Optimize Cutting Depth: Set appropriate cutting depths for each pass. For tougher materials like stainless steel, avoid deep cuts in a single pass. Break the cut into multiple shallow passes to prevent tool stress and improve finish quality.
- Minimize Overlapping Tool Movements: In CNC programming, minimizing unnecessary tool movements between cuts helps to reduce cycle time and extend tool life. Use strategies such as ramping, pecking, or pocketing to handle material removal efficiently.
- Simulation and Verification: Before starting the actual machining process, always simulate the toolpath in the CNC software to check for potential collisions or errors. This helps prevent machine downtime and reduces the risk of damage to both the workpiece and the machine.
By following these best practices, you can achieve more efficient, accurate, and safe results when using a CNC router on metal. Always test your settings with scrap material first to avoid wasting valuable stock and to fine-tune your process.
Precautions for using CNC router for metal processing
When using a CNC router for metal processing, it’ essential to follow proper safety and operational precautions to ensure both effective machining and the safety of operators and equipment. Below are key precautions to consider:
Proper Tool Selection
- Choose the Right Tools: Always select cutting tools designed for metal processing, such as carbide tools. The wrong tools can cause damage to both the machine and the material.
- Tool Wear: Metal processing can cause tool wear more quickly than wood processing. Regularly inspect and replace tools as necessary to maintain cutting efficiency and prevent accidents.
Cooling and Lubrication
- Use Coolant Fluids: Metal cutting generates a lot of heat, which can damage both the material and the tool. Use appropriate coolant or lubricant to maintain temperatures during processing.
- Coolant System Maintenance: Regularly clean and maintain the coolant system to ensure efficient cooling and to prevent the coolant from clogging or becoming contaminated.
Proper Material Handling
- Secure the Material: Ensure that the metal workpiece is properly clamped or fixtured to prevent it from moving during cutting, which could result in poor cuts or machine damage.
- Weight Considerations: Some metals can be heavy and difficult to handle. Use appropriate lifting equipment to avoid injury and to ensure the workpiece is aligned correctly.
Safety Precautions
- Wear Protective Gear: Operators should wear appropriate personal protective equipment (PPE), such as safety glasses, ear protection, gloves, and long sleeves to protect against flying debris, sparks, and sharp metal edges.
- Machine Guarding: Ensure that the CNC router has proper guarding to protect the operator from moving parts and sparks. Always ensure that all safety covers are in place during operation.
- Emergency Stops: Familiarize yourself with the emergency stop function and always ensure it is working properly in case of an emergency.
Debris Management
- Clean Regularly: Metalworking generates significant amounts of metal chips and debris. Clean the machine regularly to ensure smooth operation and to prevent buildup around the tools or in cooling systems.
- Use Proper Chip Removal Systems: Install chip conveyors or vacuum systems to remove metal debris and keep the work area clean.
Regular Maintenance
- Routine Inspections: Regularly check the CNC router’mechanical components, such as the linear guides, spindle, and motors, for wear or damage. Also, monitor the performance of the cooling system.
- Lubrication and Calibration: Ensure that the machine’components are properly lubricated and calibrated to maintain optimal performance and accuracy. Check and adjust the machine as necessary to avoid accuracy issues.
By following these precautions, CNC routers can efficiently process metal materials while ensuring safety, accuracy, and longevity of both the machine and the workpiece.
Application of CNC router in metal processing
Equipped with the right tools and setup, a CNC router can perform a number of metalworking tasks. Here are the key applications of CNC routers in metal processing:
Metal Cutting
- Sheet Metal Cutting: CNC routers can cut sheet metal of varying thicknesses with high precision. Using the appropriate cutting tools, such as end mills and carbide tools, these machines can create intricate patterns, shapes, and designs on metal sheets, including mild steel, aluminum, and stainless steel.
- Profile Cutting: CNC routers are widely used for profile cutting, where they cut metals along a set path or profile, which can be used for structural components, machine parts, or custom metal components.
Engraving and Marking
- Surface Engraving: CNC routers are equipped with engraving tools that allow them to engrave letters, logos, and intricate designs onto the surface of metals. This is commonly used for industrial marking, branding, and part identification.
- Deep Engraving: For more detailed engravings, especially in tougher metals, CNC routers with specialized tools and settings can provide deep and precise engravings, useful in applications like trophies, plaques, and serial numbers on metal parts.
Drilling and Tapping
- Hole Drilling: CNC routers can drill precise holes of various diameters and depths in metal sheets or components. The flexibility of the CNC allows operators to create hole patterns for fastening, joining, or ventilation purposes.
- Tapping: In addition to drilling, CNC routers can also perform tapping operations to create threads in holes. This is especially useful for creating threaded holes for bolts, screws, and other fasteners in metal parts.
Milling and Slotting
- Milling: CNC routers can be used for milling operations where they remove material from metal surfaces to create slots, pockets, or cavities. This is commonly used in parts like housings, frames, and complex components that require precise geometric features.
- Slotting: A similar process to milling, CNC routers can create long, narrow cuts or slots in metal materials. This is useful for applications such as gear manufacturing, keyways, or custom tooling.
Custom Prototyping
- CNC routers are often used for rapid prototyping in metal processing. With the ability to quickly create and modify designs, these machines are ideal for creating prototypes for new products or for testing out new designs before mass production.
Tool and Die Manufacturing
- CNC routers are used in the creation of tools and dies that are used for stamping, molding, and other manufacturing processes. By using precision milling and cutting, CNC routers can produce high-quality dies and molds from metal.
CNC routers have found valuable applications in metal processing, ranging from cutting and milling to engraving and prototyping. Their precision, automation, and flexibility make them an essential tool in many industries.
Summarize
A CNC router can be a good choice for working with metal under specific conditions. It is ideal for lighter-duty metal cutting, engraving, and shaping on softer metals like aluminum, brass, and copper, especially when precision and versatility are needed. However, for heavy-duty metal cutting or working with harder materials like steel or titanium, other machinery such as a CNC milling machine or a fiber laser cutting machine would be more appropriate. Read “What Metals Can CNC Routers Cut?” for more information.
AccTek CNC is a reputable CNC router manufacturer in China, offering a wide range of high-quality CNC routers designed to meet the needs of various industries. Whether you’re working with wood, metal, plastic, or composite materials, AccTek CNC’s products provide precision, efficiency, and versatility for all your manufacturing needs. Tell me what project you are planning to start and I will provide you with the right CNC router selection solution.