- 10-15 Min Read
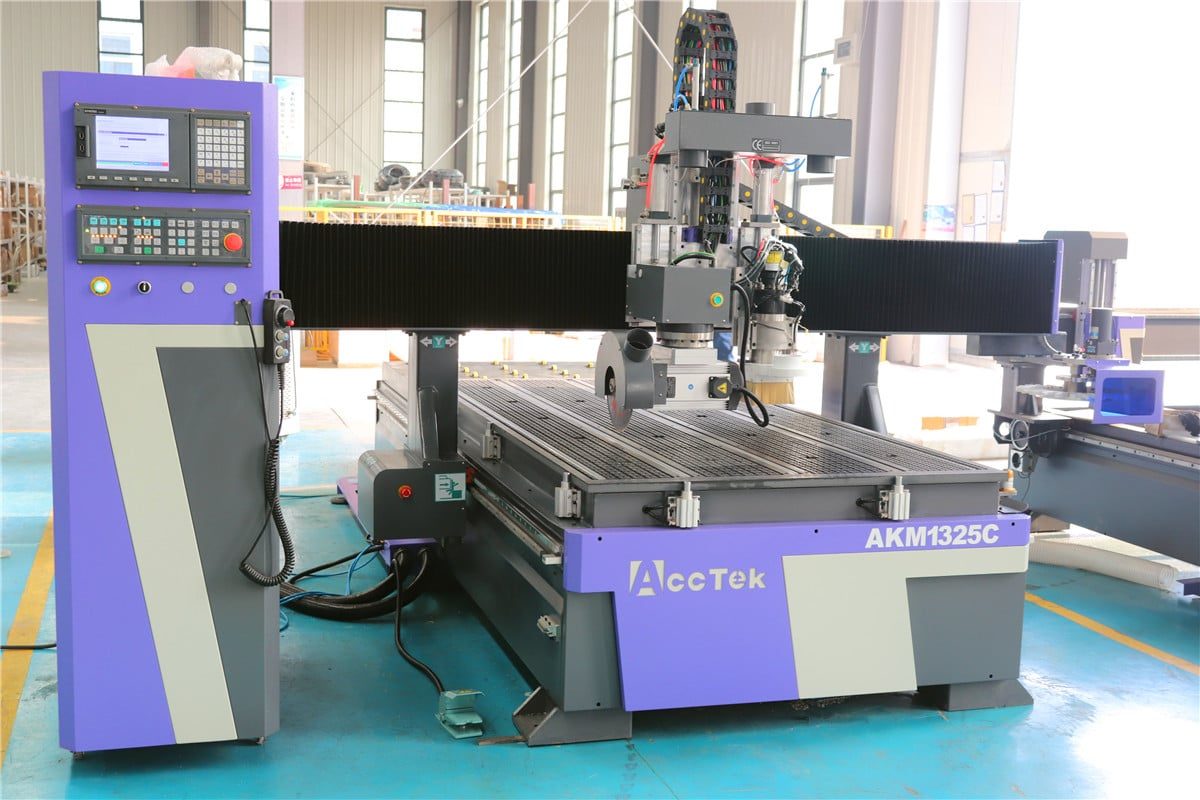
CNC routers and table saws are both essential tools in the woodworking industry, but they serve different purposes and operate in distinct ways. While table saws are known for their simplicity and ability to cut through wood with high precision, CNC routers offer a more advanced solution with automation, versatility, and the ability to handle complex designs. However, as technology advances, many wonder if a CNC router can truly replace the traditional table saw.
In this article, we’ll explore the strengths and limitations of both tools, compare their functions, and discuss whether a CNC router can be a viable alternative to the table saw. Whether you’re a professional woodworker or a hobbyist, understanding the potential of these machines can help you make more informed decisions about which tool best suits your needs.
Understanding CNC Router
A CNC router is a versatile, automated machine used for cutting, carving, milling, and engraving a wide variety of materials, including wood, metal, plastic, and composites. Unlike traditional routers, which are manually controlled, CNC routers are controlled by a computer, allowing for highly precise and repeatable cutting operations. The machine works by interpreting digital designs and converting them into specific movements that are executed by the CNC router spindle, which holds various tools for cutting, milling, or engraving.
Advantages of CNC Router
- Precision and Accuracy: CNC routers can achieve high precision and tight tolerances, making them ideal for detailed designs and high-quality production.
- Automation and Efficiency: Since CNC routers are computer-controlled, they can run continuously with minimal human intervention, improving productivity and reducing labor costs.
- Versatility: CNC routers can handle a wide range of materials (wood, metal, acrylic, composites, etc.) and are adaptable to a variety of applications, from cutting to engraving and 3D milling.
- Complex Designs: With CNC programming, even highly intricate and complex designs can be easily achieved, which would be difficult or impossible with manual methods.
- Consistency: CNC routers ensure uniformity in production, as each piece is cut exactly the same, eliminating human error.
Limitations of CNC Router
- Initial Cost: The upfront investment for a CNC router can be quite high, especially for models with advanced features and capabilities.
- Size and Space Requirements: Large CNC routers require significant floor space, which may not be feasible for small workshops or limited workspaces.
- Training and Setup: While the machine itself is automated, operators need to be trained to program and maintain the system. This can lead to a learning curve for new users.
- Maintenance Costs: CNC routers have moving parts that can wear out over time, and regular maintenance is required to ensure their longevity and optimal performance. Parts such as spindles, tool heads, and linear guides may need to be replaced periodically.
Applications of CNC Router
- Woodworking and Furniture Making: CNC routers are commonly used in furniture production, cabinetry, and custom woodworking projects, allowing for detailed designs and efficient mass production.
- Signage and Advertising: The ability to carve and cut intricate designs makes CNC routers ideal for creating signs, logos, and custom promotional products.
- Prototyping and Product Development: CNC routers are frequently used in the prototyping phase of product design to quickly produce detailed models or parts for testing and refinement.
- Decorative Items and Trophies: CNC routers can engrave and shape intricate patterns on metals, acrylics, and other materials, making them suitable for creating decorative items, trophies, and awards.
- Model Making and Sculpting: CNC routers are used in creating detailed models and sculptures, whether for architecture, education, or artistic purposes.
CNC routers are integral in modern manufacturing due to their adaptability, precision, and ability to automate complex processes.
Understanding Table Saw
A table saw is a powerful woodworking tool designed for making precise straight cuts in wood and other materials. The saw blade is mounted on an arbor, and it protrudes through a flat table surface, allowing the user to feed material through the blade for accurate cuts. It is commonly used in both professional workshops and DIY environments due to its versatility and cutting precision.
Advantages of Table Saw
- Precision and Accuracy: Table saws provide highly accurate cuts, especially when using a fence system to guide the material. They offer consistent and repeatable cuts, which is beneficial for professional and DIY woodworkers.
- Versatility: They can perform a wide range of cuts, including rip cuts (cutting along the grain), crosscuts (cutting against the grain), bevel cuts, and dados (grooves). With the right accessories, they can also handle more complex tasks.
- Speed and Efficiency: Table saws allow for faster and more efficient cutting than many handheld saws, especially for larger pieces of wood or when making long, straight cuts.
- Safety Features: Modern table saws come with safety features such as blade guards, riving knives, and anti-kickback pawls to reduce the risk of accidents.
Limitations of CNC Router
- Size and Portability: Table saws can be bulky and heavy, particularly the cabinet models. They often require a dedicated space in the workshop and may not be easily portable, limiting their use in smaller or temporary workspaces.
- Cost: High-quality table saws, especially cabinet models, can be expensive. In addition to the cost of the saw, accessories and maintenance can add to the overall expense.
- Risk of Injury: Despite safety features, table saws are still one of the most dangerous woodworking tools due to the high-speed spinning blade. Accidents can occur if the saw is not used correctly or if safety precautions are not followed.
- Limited Cutting Depth for Thicker Materials: While table saws are capable of cutting through a variety of materials, they may struggle to cut through very thick wood or dense materials, depending on the blade size and motor power.
Applications of Table Saw
- Woodworking: Table saws are a staple in woodworking shops, used for making precise cuts in wood, plywood, MDF, and other materials.
- Cabinet Making: The precision of a table saw makes it ideal for cabinet makers who need to create accurate cuts for cabinet faces, drawers, and shelves.
- Furniture Making: Furniture makers use table saws to cut components for tables, chairs, and other pieces, especially for straight and beveled cuts.
- Flooring and Trim Work: Table saws are commonly used in flooring installations and trim work, where consistent and clean cuts are beneficial for a professional finish.
- DIY and Home Projects: Home hobbyists and DIY enthusiasts use table saws for a wide variety of projects, from building furniture to creating decorative wooden items.
The table saw is a versatile and essential tool in woodworking, offering precision and efficiency but requiring space, safety considerations, and proper handling to ensure effective use.
Comparing CNC Routers and Table Saws
Comparing CNC routers and table saws involves evaluating various dimensions that impact their capabilities, performance, and application in woodworking and other industries. Here’s a comparison across several key factors:
Cutting Precision and Accuracy
- CNC Routers: CNC routers offer exceptional precision and accuracy, driven by computer-controlled motors. They can produce intricate and highly detailed cuts with minimal error. They are ideal for complex designs, including curves, slots, and 3D shapes.
- Table Saws: While table saws can provide relatively accurate cuts, they depend on manual adjustment and the skill of the operator. Precision can vary based on the operator’s experience, the saw’s calibration, and the type of fence used. They are less suited for intricate designs or curves.
Flexibility
- CNC Routers: CNC routers are extremely flexible. With the right software and tool changes, they can handle an array of cuts, materials, and designs. They are highly adaptable for both prototyping and mass production.
- Table Saws: Table saws are less flexible. While they are excellent for making straight cuts and bevels, additional tools (such as miter saws or band saws) are needed for more complex cuts.
Ease of Use
- CNC Routers: CNC routers are more complicated to operate, requiring knowledge of CAD (Computer-Aided Design) software and CNC programming. Operators need to load designs into the software, set parameters, and monitor the machine during operation.
- Table Saws: Table saws are much simpler to use. They involve adjusting the fence, blade height, and angle manually, making them more accessible to novice users. However, this simplicity also limits the range of cuts they can make without additional equipment.
Material Compatibility
- CNC Routers: CNC routers are versatile and can cut a wide range of materials, including wood, plastic, metal, foam, and composites. They are used for intricate patterns in materials that would be difficult to handle with a table saw.
- Table Saws: Table saws are primarily designed for cutting wood and wood-based products (plywood, MDF, etc.). Some models can also handle plastics and certain soft metals, but they are generally not used for cutting harder metals or composites.
Automation and Repeatability
- CNC Routers: CNC routers offer high levels of automation. Once the design and settings are programmed, the machine can automatically execute multiple cuts with precise repeatability, which is ideal for mass production.
- Table Saws: Table saws are not automated. Repeatability is dependent on the operator’s ability to set up and position the material consistently. While jigs and fixtures can improve repeatability, the process remains largely manual.
Cutting Speed
- CNC Routers: CNC routers tend to have slower cutting speeds compared to table saws due to the precision required for detailed cuts. However, they can cut multiple pieces in a single pass once properly set up, making them efficient for batch production.
- Table Saws: Table saws are faster for straight cuts. They can rapidly slice through wood and basic materials, especially when performing simple cuts without the need for intricate designs or setups.
Setup Time
- CNC Routers: CNC routers require significant setup time. This includes programming the machine, setting the material, and configuring the toolpath. Once set up, they can work autonomously for long periods, reducing the need for constant operator input.
- Table Saws: Table saws have a much quicker setup process. You only need to adjust the fence, blade, and height before starting, making them more suitable for quick tasks and small-scale projects.
Size and Space Requirements
- CNC Routers: CNC routers are generally larger and require more space. Industrial models can take up significant floor space, while smaller desktop models are more compact but still require a stable, dedicated workspace.
- Table Saws: Table saws are smaller and more portable, though some industrial versions can be quite large. They fit more easily into smaller workshops, making them suitable for home garages or small businesses.
Cost
- CNC Routers: CNC routers tend to be significantly more expensive due to their advanced technology, precision, and versatility. Industrial-grade models can cost tens of thousands of dollars, while desktop models may still be pricey but more affordable for hobbyists.
- Table Saws: Table saws are far more affordable. Entry-level models can be purchased for a few hundred dollars, and even high-end versions are still more budget-friendly compared to CNC routers.
CNC Routers are ideal for precise, intricate, and automated cutting of various materials and complex designs. They are best suited for industries or operations requiring high accuracy, large-scale production, and versatility. Table Saws are simpler, faster, and more cost-effective, making them perfect for woodworking projects with basic needs. They are more suitable for small to medium-scale operations and less complex tasks. Choosing between these two tools depends on the specific needs of the user.
The relationship between CNC router and table saw
While CNC router and table saw are typically used independently, there is a complementary relationship between the two. Here’s how these machines can work together:
Collaborative Use Cases
The CNC router and table saw complement each other through different stages of the manufacturing process, combining their strengths to achieve precision and efficiency.
- Precision Cutting with CNC Router: The CNC router excels at creating intricate and complex cuts, such as curved shapes, engravings, or detailed carvings. It is particularly useful for tasks that require high precision and flexibility, like cutting intricate patterns or custom designs on flat materials like wood, plastic, or composites.
- Rough Cutting with Table Saw: The table saw, on the other hand, is ideal for rough cutting large panels, boards, and timber quickly and accurately in straight lines. It is commonly used for cutting down materials into rough dimensions before they undergo further processing with a CNC router.
- Collaborative Use Case Example: In a woodworking shop, a table saw could be used first to cut large panels into manageable pieces. Once these pieces are at the correct size, a CNC router can take over to perform detailed tasks, such as cutting custom designs, engravings, or even making slots for joining the pieces together.
Hybrid Methods
The hybrid method refers to combining the capabilities of both machines in a single workflow, maximizing their individual strengths while minimizing their weaknesses.
- Hybrid Workflow Example: Start with the table saw to quickly cut down raw materials into rough dimensions (e.g., cutting down plywood sheets into rectangular sections). Then, move these pieces to the CNC router for finishing work, such as cutting complex shapes or adding precise slots for joining or assembly.
- Hybrid Design: Some hybrid designs incorporate both machines in a single, integrated system. For example, some CNC machines are equipped with a rotary table, or a hybrid machine may have a table saw integrated with a CNC router. This allows for quick rough cuts followed by precise routing or detailing, reducing the need for multiple setups and the overall production time.
- Multi-step Production Process: In more advanced applications, a CNC router could handle intricate tasks like engraving or cutting out holes, while the table saw might be used for cutting larger components, panels, or basic shapes. This allows for a seamless workflow where both machines are used in succession, improving productivity and reducing material wastage.
The complementary relationship between CNC routers and table saws is a result of their ability to handle different types of cutting tasks. The table saw excels in quick, straight cuts and rough dimensioning, while the CNC router provides precision and versatility for detailed, intricate designs. By using them collaboratively or through hybrid methods, manufacturers can achieve more efficient and effective workflows, leveraging the unique strengths of both machines.
When Should a CNC Router Replace a Table Saw?
A CNC router should be used instead of a table saw when the project demands complex, intricate cuts, precision, and automation. The following are scenarios where a CNC router can replace a table saw:
- Complex and Intricate Cuts: CNC routers are ideal for complex shapes, detailed patterns, and 3D carving. They can handle intricate designs like curves, joints, and patterns that a table saw is not capable of performing. If your project requires cuts like engraving, detailed lettering, or contouring, the CNC router can handle these with ease.
- Precision: CNC routers operate with precise, programmed control. They can execute highly detailed cuts within tolerances of a fraction of a millimeter, making them perfect for fine joinery, cabinetry, or intricate designs where a high degree of accuracy is required. For example, when working with thin materials like plywood, MDF, or plastic that require tight fitments, CNC routers offer consistent, repeatable precision.
- Automation: CNC routers are automated, reducing the need for manual labor. Once the design is programmed into the CNC software, the machinewill complete the cuts automatically with minimal operator intervention. Ideal for high-volume production or when multiple identical parts are needed, as CNC routers can consistently repeat the same cut.
- Material Versatility: CNC routers can handle a variety of materials such as wood, plastics, composites, and some metals. The versatility of a CNC router makes it useful for projects that involve diverse materials with varying thicknesses.
- Customization and Upgrades: CNC routers offer the flexibility to change tools and customize settings for different types of cuts or materials. They can be equipped with different tooling options (like drills, spindles, or cutting bits) for specific tasks such as drilling, shaping, or slicing.
A CNC router should replace a table saw when your work requires greater precision, the ability to cut a variety of materials, complex or custom cuts, or higher automation. If your tasks are simple, primarily involve wood, and you need a lower upfront cost, a table saw might still be the right tool. However, for more versatility, automation, and precision, a CNC router is a solid replacement.
Summarize
Both CNC router and table saw have their advantages, and in many modern workshops, it’s not about one replacing the other, but about choosing the right tool for the task at hand. As technology continues to advance, it’s likely that CNC routers will increasingly complement or even take over tasks that once required a table saw, offering more precision and flexibility. The key lies in understanding your workflow, the materials you work with, and the kind of projects you aim to complete. With the right balance of tools, your production capabilities can be maximized for efficiency, quality, and creativity.
AccTek CNC manufactures high-quality CNC routers, known for their precision, customizability, and reliability. We focus on providing excellent customer service, from pre-sales consultation to after-sales support, helping clients optimize their production processes and achieve high-quality results. Whether you’re a novice or an experienced professional, AccTek CNC routers are engineered to enhance productivity, streamline operations, and deliver exceptional precision in every cut.