- 10-15 Min Read
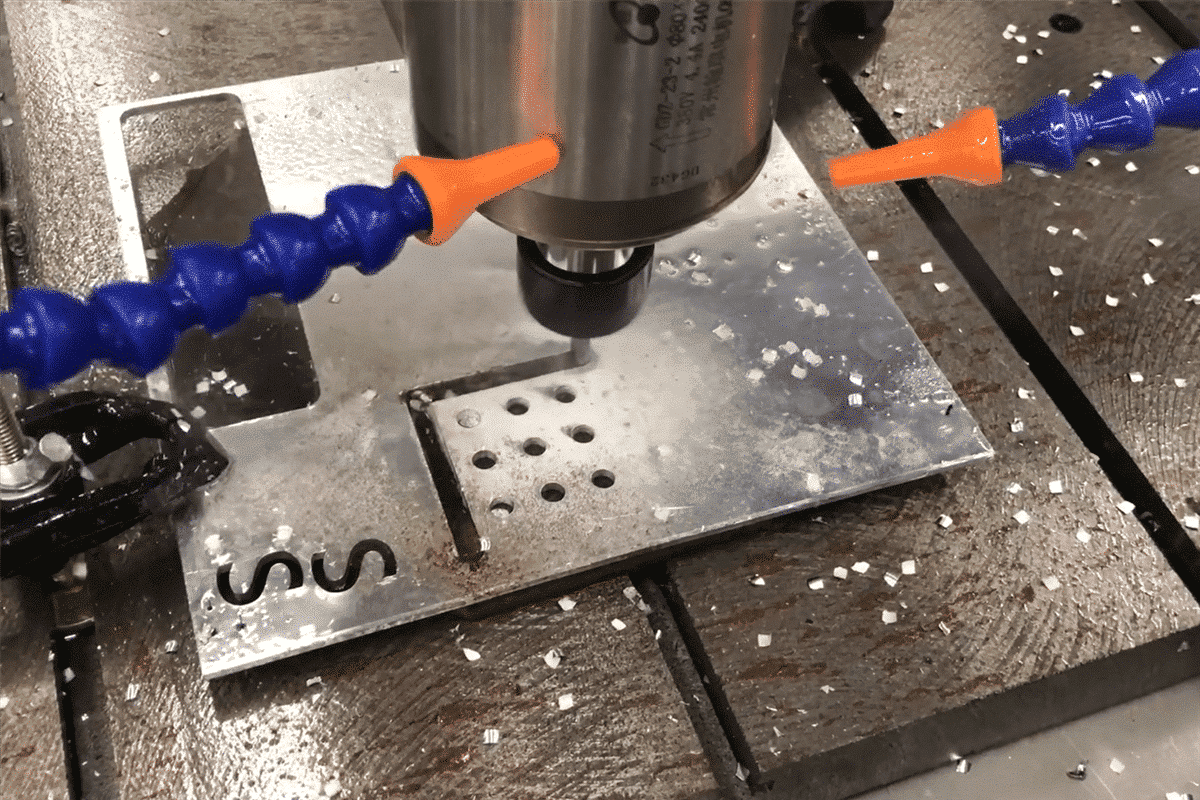
CNC routers are renowned for their precision and versatility in working with a wide range of materials, from wood and plastic to composites. However, a common question arises when considering more demanding projects: can a CNC router effectively cut metal? The idea of using a CNC router for metal cutting may seem unconventional, especially since these machines are traditionally associated with softer materials. Yet, with the right setup and understanding, CNC routers can indeed be used to cut metal, opening up new possibilities for both hobbyists and professionals.
In this article, we will delve into the role of CNC router key components in metal cutting, exploring the types of metals it can process, the challenges it faces, and safety considerations when cutting metal. Whether you’re considering this for your next project or simply curious about the capabilities of CNC routers, this guide will provide you with valuable insights into the potential and limitations of metal cutting with CNC technology.
Understanding CNC router
A CNC router is a powerful and versatile machine tool that is widely used in various industries for cutting, shaping, and carving materials with precision and efficiency. Unlike traditional manual tools, CNC routers are operated by a computer program that controls the movement of the cutting tool along multiple axes, enabling it to create complex shapes and designs with high accuracy. The automation of the process allows for consistent production, making CNC routers ideal for both mass production and custom manufacturing.
Main Configuration
The main components of a CNC router include a frame that provides structural support, a spindle that holds and drives the cutting tool, a control system that interprets the computer-generated codes and translates them into movements, and a worktable that holds the material to be cut. Other key elements include drive motors, which control the movement along the machine’s axes (X, Y, and Z), and the cutting tool itself, which can be customized based on the material and desired outcome. Some CNC routers also come with additional features like vacuum beds for material hold-down, automatic tool changers, and dust collection systems.
Working Principle
The working principle of a CNC router involves the use of a computer to control the movement of the cutting tool along multiple axes. The process begins with the creation of a digital design, typically using CAD (Computer-Aided Design) software. This design is then converted into a series of instructions or G-codes, which the CNC router interprets. The machine’s control system directs the spindle and cutting tool to move along the X, Y, and Z axes according to these instructions, cutting or shaping the material as specified. The precision of the movements ensures that the final product matches the digital design with high accuracy.
Application
CNC routers are widely used across various industries due to their versatility and precision. In woodworking, they are employed to cut and engrave furniture components, cabinetry, and decorative panels. In the signage industry, CNC routers are used to create detailed signs, logos, and lettering from materials like plastic, wood, and metal. In metalworking, with the appropriate setup, CNC routers can cut and engrave metals such as aluminum and brass. The ability to handle a wide range of materials and perform multiple tasks makes CNC routers indispensable in modern manufacturing and fabrication processes.
Key Components and Their Role in Metal Cutting
When it comes to metal cutting with a CNC router, key components can impact the efficiency, precision, and effectiveness of the cutting and engraving process. Each of these components must be optimized to handle the demands of metal cutting, as the process is significantly more challenging than working with softer materials like wood or plastic. Below is an introduction to these critical aspects:
Spindle Power and Speed
The spindle is the heart of the CNC router, responsible for holding and rotating the cutting tool. A high-power spindle is necessary to generate the torque required to cut through metal efficiently. Metals are harder and denser than other materials, so the spindle needs sufficient power to maintain consistent cutting forces without stalling or losing accuracy. Speed is equally important, as the spindle must operate at higher RPMs (Revolutions Per Minute) to achieve a clean, smooth cut in metal. The correct balance between power and speed allows the spindle to handle tougher metals like aluminum or brass, reducing the risk of tool breakage and ensuring a high-quality finish.
Tool Considerations
The cutting tool, or bit, is the component that directly interacts with the metal and its selection affects the success of the cutting operation. For metal cutting, tools made from hard, durable materials such as carbide or diamond-coated tools are preferred. These materials can withstand the high temperatures and forces generated during metal cutting. Additionally, the tool’s geometry, including the number of flutes, helix angle, and coating, must be suited to the specific type of metal being cut. Proper tool selection minimizes wear, prevents overheating, and ensures that the tool can cut through the metal efficiently, producing precise and accurate results.
Machine Rigidity and Stability
The frame and gantry of the CNC router provide the structural support needed to maintain accuracy during metal cutting. when cutting metal. Metal cutting requires the machine to absorb significant forces without flexing or vibrating, as any movement can lead to inaccuracies, poor surface finishes, or even tool breakage. A rigid machine frame ensures that the cutting tool follows the programmed path precisely, even under the heavy loads associated with metal cutting. Stability also minimizes vibrations, which can degrade the quality of the cut and reduce tool life. Therefore, a CNC router designed for metal cutting must have a strong, well-constructed frame and gantry to maintain precision throughout the cutting process.
Cooling/Lubrication System
Metal cutting generates substantial heat due to the friction between the cutting tool and the metal workpiece. An effective cooling or lubrication system is beneficial to manage this heat, prevent tool wear, and avoid damaging the workpiece. Coolant systems, which may involve liquid coolant, misting systems, or air cooling, help to dissipate heat and lubricate the cutting area. This not only extends the life of the cutting tool but also ensures that the metal retains its structural integrity and surface quality. Without proper cooling and lubrication, the metal can warp, the tool can dull quickly, and the overall cutting performance can degrade.
Understanding the roles of these key components in metal cutting helps in optimizing the CNC router for metalworking tasks, ensuring precision, efficiency, and quality in the final product.
Materials suitable for metal CNC router cutting
When using a CNC router for metal cutting, you should choose a material that is compatible with the machine’s capabilities and the cutting tools used. Not all metals are suitable for CNC router cutting, but several common metals can be effectively processed, especially when the machine is appropriately configured. The suitability of materials can be categorized into non-ferrous metals, composite materials, thin-gauge steel and stainless steel. Each of these categories has specific characteristics that make them appropriate for CNC router applications.
Non-Ferrous Metals
Non-ferrous metals, which do not contain iron, are often ideal for CNC router cutting due to their generally softer and more machinable nature compared to ferrous metals. Common non-ferrous metals suitable for CNC router cutting include:
- Aluminum: Aluminum is one of the most popular metals for CNC router cutting due to its relatively soft and lightweight nature compared to other metals. It is easy to machine, has excellent thermal conductivity, and provides a smooth finish. CNC routers can efficiently cut aluminum sheets, plates, and profiles, making them ideal for a variety of applications.
- Brass: Brass is another metal that is well-suited for CNC router cutting. It is an alloy of copper and zinc, known for its machinability, corrosion resistance, and attractive appearance. Brass is commonly used for decorative items, fittings, and precision components. CNC routers can cut brass effectively, producing clean and detailed edges, especially in intricate designs.
- Copper: Copper is valued for its exceptional electrical and thermal conductivity. It is softer than many other metals, which makes it suitable for CNC router cutting. However, copper can be prone to tool gumming, so the right cutting tools and cooling strategies are important to ensure clean cuts.
Composite Materials
Composite materials, which combine two or more distinct materials to create a new material with enhanced properties, are also suitable for CNC router cutting. These materials often include metal components, making them ideal for specific applications. Examples include:
- Aluminum Composites: Aluminum composite panels (ACP) are widely used in construction and signage industries. These panels consist of thin layers of aluminum bonded to a non-metallic core. CNC routers can efficiently cut through the aluminum layers and shape the panels.
- Metal Matrix Composites (MMCs): These composites combine metals with ceramics or other reinforcing materials to create stronger, lighter components. CNC routers equipped with appropriate tooling can machine MMCs, though they require more advanced setups due to their hardness.
Thin-Gauge Steel and Stainless Steel
While steel and stainless steel are generally more challenging to cut due to their hardness, CNC routers can still effectively machine thinner gauges of these materials.
- Mild Steel (Thin-Gauge): Mild steel, particularly in thin gauges, can be machined with a CNC router. It requires a robust machine setup with sufficient spindle power and appropriate cutting tools. Coolant may also be necessary to manage heat generation during cutting.
- Stainless Steel (Thin-Gauge): While stainless steel is tougher than non-ferrous metals, CNC routers can cut thin-gauge stainless steel sheets (typically up to 2mm thick). To cut stainless steel effectively, the CNC router must have a high-power spindle, robust tooling, and, often, a coolant system to manage heat and prevent tool wear.
By understanding the characteristics and requirements of these material categories, operators can effectively utilize CNC routers to cut a wide range of metals, from soft non-ferrous metals to more challenging materials like thin-gauge steel and stainless steel. Proper machine setup, tool selection, and cooling strategies are key to achieving optimal results when cutting metal with a CNC router.
Challenges of Metal Cutting Using a CNC Router
Cutting metal with a CNC router presents several challenges due to the material’s hardness, density, and specific properties. These challenges must be carefully managed to achieve high-quality results and prevent damage to the machine or cutting tools. Here are some of the primary challenges associated with metal cutting using a CNC router:
Tool Wear and Maintenance
Tool wear is a significant challenge when cutting metal with a CNC router. Metals are much harder and more abrasive than materials like wood or plastic, leading to rapid wear of cutting tools. This wear not only reduces the cutting efficiency but also affects the accuracy and quality of the cut. Frequent tool changes may be required, increasing downtime and operational costs.
To mitigate tool wear, it’s essential to use high-quality, durable tools such as carbide or diamond-coated bits. However, even with these advanced tools, regular maintenance and inspection are necessary to ensure they remain sharp and functional. Additionally, managing tool wear involves monitoring the cutting parameters closely to avoid excessive stress on the tool, which can lead to premature failure.
Dust and Chip Management
Metal cutting generates chips or swarf rather than dust, which presents a different set of challenges compared to softer materials. These metal chips can accumulate around the cutting area, clogging the tool path and potentially damaging the cutting tool. Inadequate chip evacuation can also cause heat buildup, leading to further challenges. Proper chip management is beneficial to maintain cutting efficiency and prevent tool breakage.
Using compressed air or coolant systems to remove chips from the cutting area is often necessary in metal cutting operations. Additionally, metal chips can be sharp and pose a safety hazard, so ensuring that they are effectively contained and disposed of is important. Unlike wood or plastic dust, metal chips also contribute to machine wear, so maintaining a clean work environment is beneficial for prolonging the machine’s life.
Feed and Speed Optimization
Optimizing feed rate and cutting speed is particularly challenging when cutting metal with a CNC router. Unlike softer materials, metal cutting requires a precise balance between feed rate and spindle speed to avoid problems like tool breakage, overheating, and poor surface finish. If the feed rate is too slow, the cutting tool may rub against the metal rather than cut it cleanly, leading to material hardening and increased tool wear. Conversely, if the feed rate is too fast or the spindle speed too high, the tool can overheat, which can cause thermal damage to both the tool and the workpiece.
Finding the right combination of feed and speed requires careful experimentation and often depends on the specific type of metal being cut, the thickness of the material, and the type of cutting tool used. Proper optimization is beneficial for achieving a clean, precise cut while maximizing tool life and overall efficiency.
Heat Generation
Cutting metal generates substantial heat due to the friction between the tool and the workpiece. This heat can cause several issues, such as warping of the material, reduced tool life, and poor surface finishes. In extreme cases, excessive heat can cause the cutting tool to lose its temper, leading to premature failure. Managing heat generation typically requires the use of coolant or lubrication systems to dissipate heat and protect both the tool and the workpiece.
Addressing these challenges requires careful planning, the right tool, and a deep understanding of both the CNC router and the metal being cut. By optimizing the machine setup, cutting parameters, and tool selection, it is possible to successfully cut metal with a CNC router, but it demands a higher level of attention and expertise compared to other materials.
Safety precautions for CNC router metal cutting
When performing metal cutting operations with a CNC router, it is important to follow specific safety precautions to ensure a safe working environment. The following strategies can help you create a safe work environment to protect operators and maintain equipment.
Metal Cutting Safety Measures
Metal cutting with a CNC router presents specific risks due to the hardness of the material, the high speeds involved, and the generation of heat and sharp debris. Key safety measures include:
- Personal Protective Equipment (PPE): Operators must wear appropriate PPE, including safety glasses or goggles to protect eyes from flying metal chips, hearing protection to mitigate noise levels, and cut-resistant gloves for handling metal parts. Respiratory protection may also be necessary if fumes or fine particles are generated.
- Secure Workholding: Ensuring the metal workpiece is firmly secured to the worktable. Loose material can shift during cutting, leading to inaccuracies, damage, or accidents. Proper clamping or fixturing is beneficial to prevent movement.
- Tool Inspection and Maintenance: Regularly inspect cutting tools for wear or damage before use. Worn or damaged tools can break under the stress of metal cutting, creating safety hazards. Maintaining sharp, high-quality tools is necessary for safe and efficient operations.
- Machine Guarding and Emergency Stops: All machine guards should be in place and functioning properly to protect operators from moving parts and flying debris. Operators should also be familiar with the location and operation of emergency stop buttons to quickly halt the machine in case of an issue.
Environmental Considerations
Beyond direct safety measures, environmental factors play a role in maintaining a safe and productive workspace when cutting metal with a CNC router:
- Dust and Chip Management: Metal cutting produces chips or swarf rather than fine dust, which can accumulate and create hazards. Effective chip evacuation, using systems like compressed air, coolant, or extraction units, is necessary to keep the cutting area clear. Proper disposal of metal chips is also important to prevent slips, trips, and potential damage to machinery.
- Ventilation and Air Quality: Metal cutting may produce fumes, especially if coolant is used or if certain metals are cut. Ensuring good ventilation or using localized extraction systems helps maintain air quality, protecting operators from inhaling harmful substances.
- Noise Control: CNC routers, particularly when cutting metal, can generate high noise levels. Ensuring that operators wear hearing protection and implementing sound-dampening measures in the work environment can help reduce the risk of hearing damage and create a more comfortable workspace.
- Fire Safety: The heat generated during metal cutting, combined with the presence of flammable materials, can create fire risks. Keeping the workspace free of flammable items, using coolant systems to manage heat, and having a Class D fire extinguisher (suitable for metal fires) readily available are critical fire safety practices.
By focusing on these metal cutting safety measures and environmental considerations, operators can create a safer, more efficient, and more productive environment for CNC router metal cutting operations. This comprehensive approach to safety not only protects individuals but also ensures the longevity and reliability of the equipment.
Summarize
CNC routers can indeed cut metal, but doing so requires careful consideration of several factors. By adopting the correct settings and addressing the key challenges of cutting metal, a CNC router can effectively cut metal materials such as aluminum, brass, and thin-gauge steel. This opens up new possibilities for innovation and productivity, making the CNC router a versatile tool for your metalworking projects. If you want to know about the wider application of CNC routers, you can continue reading “What Industries Are CNC Routers Used In“.
If you’re looking for a reliable and efficient solution for metal cutting, AccTek CNC’s professional metal CNC routers are an excellent choice. Designed with enhanced rigidity and stability, these machines are built to handle the demands of metal processing with precision. Equipped with a mist cooling system, they effectively manage heat, ensuring a higher quality finish and longer tool life. Whether you’re working with aluminum, brass, or thin-gauge steel, AccTek CNC routers offer the advanced features you need for superior metalworking performance.