- 8-12 Min Read
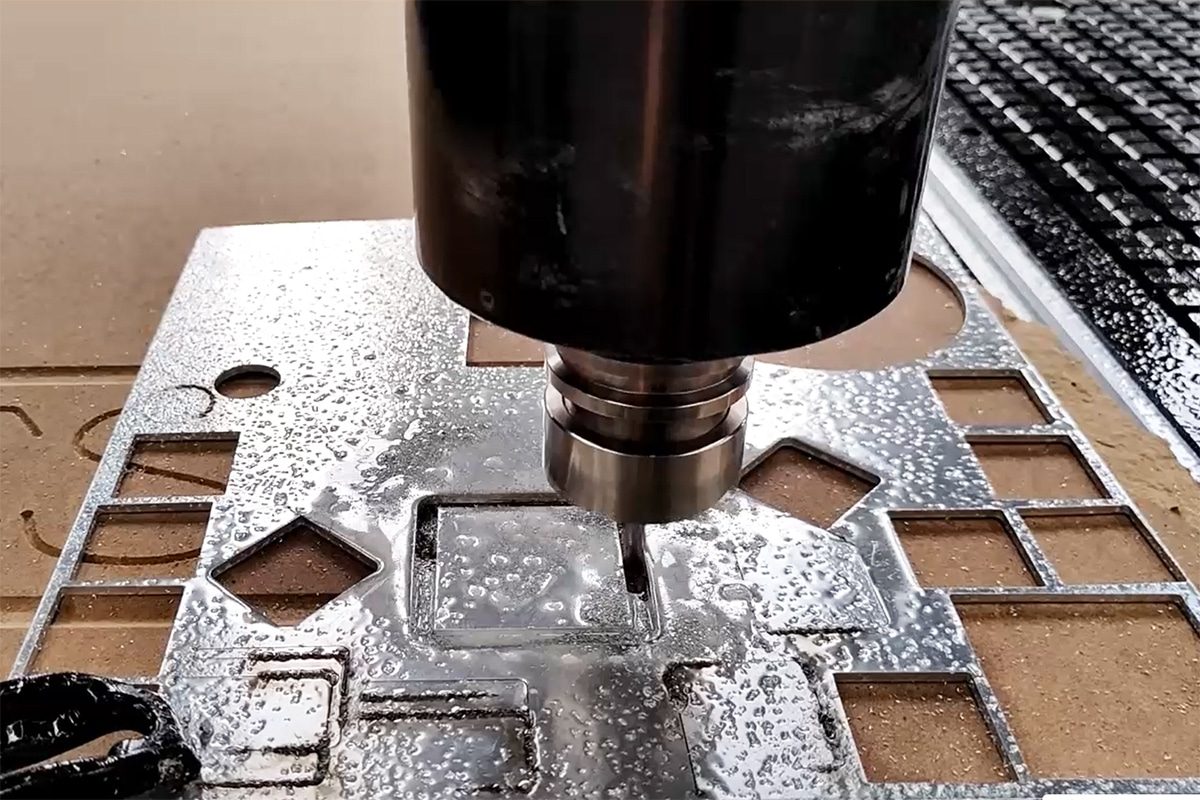
CNC routers are widely used for cutting and shaping materials like wood, plastic, and composites, but can they handle aluminum? The answer is yes, but with the right setup and considerations. While aluminum is softer than steel, it presents unique challenges due to its tendency to generate heat and create built-up edge (BUE) on cutting tools. To achieve precise and efficient aluminum cutting, factors like spindle power, cutting speeds, tool selection, and cooling methods must be optimized.
In this article, we’ll explore whether CNC routers can effectively cut aluminum, what factors influence performance, and how to get the best results. Whether you’re a hobbyist or a professional looking to expand your machining capabilities, understanding the right techniques and equipment will help you achieve clean, accurate cuts in aluminum.
Understanding CNC Routers
A CNC (Computer Numerical Control) router is an automated cutting machine that follows programmed tool paths to carve, engrave, and cut various materials. Unlike traditional manual cutting tools, CNC routers use computer-controlled movements to ensure precision, repeatability, and efficiency in machining operations.
How does CNC Router work?
A CNC router operates on three primary axes (X, Y, and Z) to move the cutting tool along a workpiece. Some advanced models also feature rotary or multi-axis capabilities for more complex cuts. The process of operating a CNC router involves several key steps:
- Design Creation: The first step is creating a digital design using CAD (Computer-Aided Design) software like AutoCAD, Fusion 360, or SolidWorks.
- Generating Toolpaths: The CAD model is converted into CAM (Computer-Aided Manufacturing) software, and the CAM software then generates G-code.
- Loading and Securing the Material: The workpiece is securely fixed onto the worktable using clamps, vacuum beds, or fixtures.
- Executing the Cutting Operation: The CNC router’s control system interprets the G-code and moves the spindle along the X, Y, and Z axes to perform the programmed cuts.
Key Components of a CNC Router
A CNC router consists of several essential components that work together to ensure precise and efficient cutting.
- Spindle: The motor-driven tool that performs the cutting. Spindle speed and power determine the machine’s capability to cut different materials.
- Cutting Tools: Various end mills and bits are used to shape and carve materials. For aluminum, carbide end mills with special coatings are preferred.
- Worktable: The surface where the material is placed and secured using clamps, vacuum beds, or fixtures.
- Motion System: Stepper or servo motors control the movement along different axes, ensuring precise cutting.
- Control System: The interface where operators input commands, adjust settings, and monitor the machining process.
Understanding how a CNC router works and its key components helps us explore its ability to cut aluminum. In the next section, we will analyze the specific challenges of cutting aluminum with a CNC router and how to overcome them.
Challenges of Cutting Aluminum with a CNC Router
Cutting aluminum with a CNC router presents several challenges due to the material’s unique properties, the way it forms chips, and the difficulty in evacuating those chips efficiently. Understanding these factors is beneficial to optimizing the cutting process and achieving high-quality results.
Material Properties
Aluminum differs significantly from wood, plastics, and even other metals due to its physical and mechanical properties.
- Soft and Ductile Nature: Unlike steel or other hard metals, aluminum is relatively soft and ductile, which can cause a built-up edge (BUE) on the cutting tool.
- High Thermal Conductivity but Poor Heat Dissipation in Cutting Zone: Aluminum retains heat in localized areas, especially in the cutting zone, which can cause thermal expansion and tool failure.
- Work Hardening Tendency: Some aluminum alloys can harden when cut, making subsequent passes more difficult. This results in inconsistent cutting performance and rough edges.
- Low Density and High Malleability: Aluminum deforms under high pressure, so proper work-holding and vibration control are required.
Chip Formation
The way aluminum forms chips during machining greatly affects the efficiency and quality of the cut.
- Gummy Chips That Stick to the Tool: Aluminum produces long, continuous, and often sticky chips that can cling to the cutting tool instead of breaking away. This results in built-up edge (BUE), where aluminum accumulates on the tool’s edge, leading to rough cuts and premature tool failure.
- Insufficient Chip Breaking: Unlike brittle materials that create small, easily removable chips, aluminum’s ductile nature means it forms long, curled chips that can wrap around the tool or clog the cutting area. This increases friction, generates more heat, and can lead to poor surface finishes and tool breakage.
Chip Evacuation
Proper chip evacuation is beneficial for maintaining tool life and achieving a smooth cut. However, aluminum’s chip behavior makes this difficult.
- Chip Packing and Tool Clogging: Because aluminum chips don’t break easily, they tend to accumulate in the cutting area, reducing efficiency and causing recutting of chips. This can lead to scratched surfaces, tool wear, and excessive heat buildup.
- Poor Airflow for Chip Removal: Unlike materials such as wood, where vacuum systems easily remove sawdust, aluminum chips require air blasts, high-speed vacuum systems, or mist coolant to be properly evacuated.
- Increased Heat Retention: When chips are not removed quickly, they retain heat in the cutting zone, accelerating tool wear and causing thermal expansion of the workpiece. This can result in inaccurate dimensions and deformations in the final product.
Cutting aluminum on a CNC router requires overcoming challenges related to material properties, chip formation, and chip evacuation. Aluminum’s soft, ductile nature and tendency to retain heat make it prone to tool wear, poor surface finishes, and excessive chip buildup. To mitigate these issues, it is essential to use the right cutting tools, cooling methods, and chip evacuation strategies to ensure efficient, high-quality machining. The next section will cover best practices for CNC routing aluminum, including optimal feed rates, tool selection, and cooling techniques.
Best Practices for CNC Routing Aluminum
To successfully cut aluminum with a CNC router, you need to optimize various factors such as tool selection, feed rates, cooling methods, and work-holding techniques. Here are the best practices to achieve precise, clean cuts while prolonging tool life and improving overall efficiency.
Choose the Right Cutting Tools
Choosing the right cutting tool is beneficial for chip evacuation and preventing aluminum buildup on the tool. Here are the best tool types for aluminum:
- Carbide End Mills: Use solid carbide end mills, which offer durability and wear resistance.
- Single or Double-Flute End Mills: Allow for better chip evacuation, reducing heat buildup.
- Coated Tools (TiAlN, ZrN, DLC): Titanium Aluminum Nitride (TiAlN) and Zirconium Nitride (ZrN) coatings reduce aluminum adhesion to the tool.
- Avoid Multi-Flute Tools: More flutes mean less space for chip removal, increasing the risk of chip packing and tool clogging.
Optimize Feeds and Speeds
Proper feeds and speeds prevent tool wear, overheating, and poor surface finishes. Here are the general guidelines:
- Spindle Speed (RPM): 18,000 – 24,000 RPM for CNC routers.
- Feed Rate: 50 – 300 inches per minute (IPM), depending on tool size and material thickness.
- Depth of Cut: 0.01″ – 0.05″ per pass for light cuts, avoid deep cuts to reduce tool deflection.
- Chip Load: Maintain an optimal chip load to prevent rubbing (not cutting).
- Avoid Improper Settings: Running too fast causes tool chatter and deflection. Running too slow leads to heat buildup and work-hardening.
Use Proper Cooling and Lubrication
Aluminum tends to generate excessive heat, requiring effective cooling. Here are the best cooling methods:
- Mist Coolant System: Sprays lubricant and coolant in fine droplets.
- Air Blast System: Blows chips away, reducing heat buildup.
- Lubricants (WD-40, Coolants): Prevent aluminum from sticking to the tool.
- Avoid Dry Cutting: This increases heat buildup, poor surface finish, and tool wear.
Prevent Chip Buildup with Proper Chip Evacuation
Aluminum chips are sticky and can clog the cutting area, leading to poor performance. Here are the best practices for chip evacuation:
- Use an Air Blast: Clears chips from the cutting zone.
- Choose Single/Double-Flute End Mills: Provides more space for chip removal.
- Adjust Feed Rates: Too slow and chips build up, too fast and tools wear out quickly.
Ensure Proper Workholding and Fixturing
Aluminum’s lightweight and malleable nature means it can vibrate or move during cutting. Here are the best workholding methods:
- T-slot Clamps: Secure the aluminum firmly to the table.
- Vacuum Table: Works well for thin sheets to prevent warping.
- Double-Sided Tape: This can be used for light aluminum work but is not ideal for heavy cuts.
- Avoid Loose Clamping: Poor fixation leads to vibrations, inaccurate cuts, and surface imperfections.
Reduce Vibration and Tool Deflection
Aluminum machining requires high rigidity to prevent vibrations (chatter). How to minimize vibration:
- Use a rigid metal CNC router with a steel or cast-iron frame.
- Reduce depth of cut instead of increasing feed rate.
- Choose a high-quality spindle with low runout and maintain constant torque.
Cutting aluminum on a CNC router is challenging but achievable with the right approach. By choosing carbide tools, optimizing feeds and speeds, using cooling and chip evacuation methods, and securing the material properly, you can achieve clean, precise cuts with minimal tool wear. Following these best practices ensures high-quality aluminum machining, making your CNC router a valuable tool for metalworking applications.
Maintenance of an Aluminum CNC Router
Regular maintenance of a CNC router used for cutting aluminum is beneficial to ensure optimal performance, precision, and longevity. Aluminum cutting generates more heat, wear, and chip accumulation compared to softer materials, making preventative maintenance even more important. Below are key maintenance practices for keeping your CNC router in excellent condition.
Spindle and Tool Holder Maintenance
The spindle is the most critical component of a CNC router. Any misalignment or wear can lead to poor-quality cuts. Here are the best maintenance practices:
- Inspect spindle bearings for wear and replace them if noise or vibration occurs.
- Clean the tool holder and collet after every job to prevent aluminum dust buildup.
- Ensure proper tool tightening to prevent runout and tool slippage.
- Lubricate spindle components as recommended by the manufacturer.
Cutting Tool and Bit Maintenance
Dull or worn-out tools lead to poor cuts and increased heat buildup. Here are the best maintenance practices:
- Regularly check end mills and router bits for wear or chipping.
- Replace dull or damaged tools to avoid chatter and rough edges.
- Use coated tools (TiAlN, ZrN) to extend tool life when cutting aluminum.
Chip Evacuation and Dust Collection
Aluminum chips can clog the cutting area and cause overheating. Here are the best maintenance practices:
- Use an air blast or vacuum system to clear chips after every job.
- Regularly inspect and clean chip collection filters to prevent airflow restrictions.
- Ensure coolant or lubrication systems function properly to reduce chip adhesion.
Guide Rails and Linear Bearings Maintenance
CNC routers rely on smooth, precise motion systems for accurate cutting. Here are its maintenance best practices:
- Clean linear rails, ball screws, and guideways regularly to remove aluminum dust.
- Apply light lubrication to prevent rust and wear.
- Check for signs of misalignment or wear and adjust if needed.
Worktable and Fixturing System Maintenance
A stable work surface ensures accurate and vibration-free cutting. Here are its maintenance best practices:
- Inspect and clean the T-slot table, vacuum table, or clamps after every use.
- Ensure firm fixturing to prevent aluminum sheets from shifting.
- Check for scratches or deformations on the worktable that could affect part accuracy.
Cooling and Lubrication System Maintenance
Heat buildup is a major issue when cutting aluminum, making cooling and lubrication systems essential. Here are its maintenance best practices:
- Regularly check coolant levels and refill with approved cutting fluids.
- Inspect mist cooling nozzles for clogging and ensure even coolant distribution.
- Clean air filters and coolant lines to prevent blockages.
Electrical and Software System Maintenance
A well-functioning control system ensures precision and reliability. Here are its maintenance best practices:
- Check electrical connections and tighten any loose wiring.
- Keep the CNC controller and software updated for performance improvements.
- Regularly inspect motor drivers, limit switches, and power supplies for signs of wear.
Safety Checks and General Housekeeping
Regular inspections prevent accidents and machine failures. Here are its maintenance best practices:
- Keep the work area clean and free of aluminum dust buildup.
- Ensure safety shields and emergency stop buttons function properly.
- Train operators on routine machine checks and maintenance schedules.
Regular maintenance of your aluminum CNC router ensures precision, longevity, and efficiency. By maintaining the spindle, cutting tools, motion system, chip evacuation, cooling, and software, you can prevent costly repairs and maintain high-quality cutting performance. A well-maintained CNC router results in cleaner cuts, extended tool life, and reduced downtime, making it a critical practice for any aluminum machining operation.
Summarize
The answer is yes, a CNC router can cut aluminum, but success depends on using the right setup, tools, and cutting parameters. Unlike softer materials like wood or plastic, aluminum presents unique challenges. However, by following best practices, CNC routers can achieve clean, precise aluminum cuts. If you want to know about the wider application of CNC routers, you can continue reading “What Industries Are CNC Routers Used In”.
For those who are looking for a high-performance CNC router for aluminum cutting, the AccTek CNC is an ideal choice. As a professional CNC router manufacturer, AccTek provides powerful high-speed spindles, precision motion systems, and advanced cooling solutions to handle the challenges of aluminum machining. Whether for metal fabrication, prototyping, signage, or industrial applications, we provide reliable, high-quality metal CNC routers. Contact AccTek today for expert guidance and tailored CNC solutions!