- 8-12 Min Read
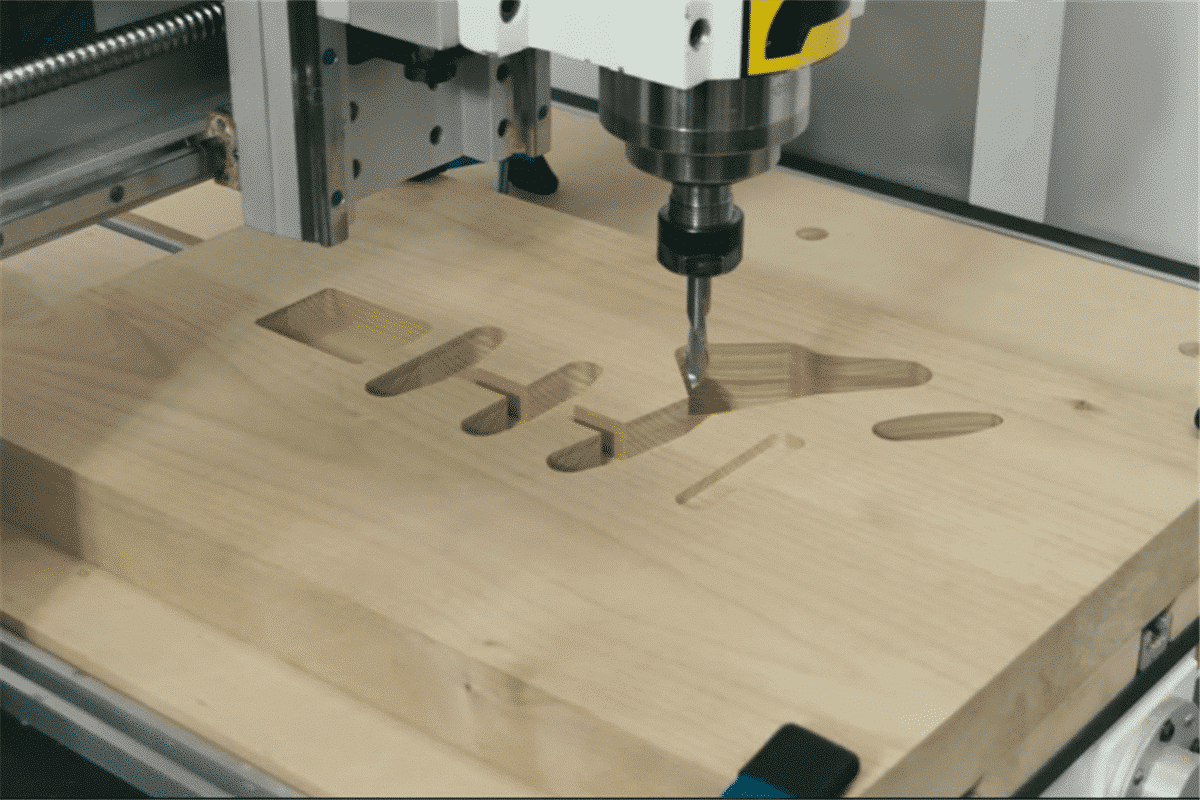
The art of building musical instruments has traditionally been associated with meticulous handcraftsmanship, where each detail is shaped by the artisan’s experience and skill. However, modern advancements in technology, particularly CNC (Computer Numerical Control) routers, have revolutionized the instrument-making process. With their ability to automate complex cuts and deliver repeatable precision, CNC routers offer new opportunities to streamline production while maintaining the high standards required for musical instruments.
This comprehensive guide explores the role of CNC routers in musical instrument manufacturing. We will delve into the fundamentals of CNC technology, the advantages it brings, and the challenges musical instrument manufacturers may face. Whether you’re a traditional instrument maker curious about integrating modern tools or a CNC router enthusiast looking to explore instrument production, this guide will equip you with the essential knowledge and guidance needed to create musical instruments using a CNC router.
Understanding musical instrument manufacturing
The art of manufacturing musical instruments has evolved over centuries, blending traditional craftsmanship with modern technological advancements. Understanding both these aspects provides insight into how the industry continues to innovate while preserving its rich heritage. However, this shift has also brought challenges, particularly for traditional craftsmanship, which faces new pressures in an increasingly mechanized world.
Traditional Methods of Musical Instrument Manufacturing
Traditional instrument making relies on skilled artisans who meticulously craft each piece by hand. Whether it’s the creation of a violin, guitar, or piano, these artisans use time-honored techniques passed down through generations. Key aspects of traditional methods include:
- Craftsmanship and Precision: Traditional instrument makers work manually, shaping, sanding, and assembling instruments with painstaking attention to detail. The resonance, tone, and longevity of the instrument depend largely on the mastery of the artisan.
- Customization: Many traditional instruments are tailored to the individual preferences of musicians, offering a unique sound or feel that mass-produced instruments cannot replicate. For example, a luthier making a custom guitar for a professional musician might adjust the shape of the neck or the placement of frets for personalized comfort and performance.
Modern Technology in Musical Instrument Manufacturing
With technological advancements, musical instrument manufacturing has incorporated automated processes and digital precision, resulting in several benefits:
- CNC routers and 3D Printing: CNC router machines are widely used to carve wood with exceptional accuracy, reducing human error. 3D printing also allows manufacturers to prototype and produce intricate parts faster and more efficiently.
- Mass Production: Modern technology has enabled large-scale production of instruments at a lower cost, making music more accessible to the masses. CNC routers can produce consistent quality, allowing beginners and hobbyists to own instruments without the high price tag of handmade models.
Challenges Faced by Traditional Craftsmanship
While modern technology has enhanced efficiency, traditional craftsmanship faces several challenges in today’s market:
- Loss of Skilled Artisans: With the rise of automation, fewer individuals are learning the traditional craft of instrument making. As older generations retire, there is a risk of losing the nuanced skills that create the world’sfinest instruments.
- Economic Pressure: Handcrafted instruments are expensive due to the time and expertise required to make them. As mass-produced instruments become more affordable, traditional makers struggle to compete in a market driven by price.
- Balancing Tradition and Innovation: Many traditional instrument makers face the dilemma of how much modern technology to incorporate into their work. While some embrace CNC router machines for certain processes, others worry that it diminishes the authenticity of hand-made instruments.
Musical instrument manufacturing exists at the intersection of tradition and modernity. While CNC technology enhances efficiency and accessibility, traditional craftsmanship retains a timeless appeal for its artistry and individuality. However, sustaining these artisanal methods amidst modern pressures presents ongoing challenges. Finding a balance between the two approaches will be key to preserving the cultural legacy of instrument making while embracing future innovations.
Understanding CNC Router
The CNC router represents a major advancement in manufacturing technology, and its use has revolutionized the world of musical instrument manufacturing. To better understand the role of CNC routers in modern musical instrument manufacturing, we can explore two critical aspects: CNC router analysis and programming, and automation.
CNC Router Analysis
A CNC router is a powerful tool that automates the cutting, shaping, and engraving processes by following precise computer instructions. In the context of musical instrument manufacturing, CNC routers can handle complex tasks that require high precision, such as cutting intricate designs, carving out specific contours, and drilling accurate holes. These CNC routers operate in multiple axes (typically three to five), allowing them to perform detailed work on various materials such as wood, metal, or composites, which are commonly used in instrument production.
Programming and Automation in CNC Routers
CNC routers rely heavily on programming and automation to operate efficiently. The use of computer programs ensures that the machine follows precise instructions, while automation streamlines the manufacturing process. Here’s how these elements contribute to the functionality of CNC routers:
- CAD and CAM Software: CNC routers are programmed using CAD (Computer-Aided Design) and CAM (Computer-Aided Manufacturing) software. The design process starts with CAD, where a digital model is created. This model is then transferred to CAM software, which converts the design into a toolpath, guiding the CNC router to execute the cuts. This process allows for great customization and precision in programming. Musical instrument makers can create intricate patterns and shapes in the software, which are then automatically executed by the machine.
- Automation: Automation plays a central role in CNC router operations. Once the program is set, the machine can execute repetitive tasks with precision, significantly speeding up the manufacturing process. In contrast to manual methods, where each part of the musical instrument might take hours or days to complete, CNC routers can produce components in a fraction of the time. This not only enhances efficiency but also reduces labor costs, making it a valuable asset for manufacturers looking to scale their operations while maintaining high quality. However, operators need to have a solid understanding of CNC programming and machine operation to ensure that the CNC router produces the desired results.
CNC routers combine precision, speed, and versatility with programming and automation. The ability to analyze materials and produce intricate designs with minimal error makes CNC routers essential in a variety of industries. As programming and automation technologies continue to evolve, CNC routers will become even more efficient, allowing musical instrument manufacturers to increase output while maintaining high-quality standards.
Advantages of Using a CNC Router for Musical Instrument Manufacturing
CNC routers have transformed the manufacturing processes in many industries, including musical instrument production. These machines offer several distinct advantages that enhance the precision, efficiency, and consistency required for creating high-quality instruments. Here are the key advantages of using CNC routers in musical instrument manufacturing:
- Precision and Consistency: One of the most significant advantages of using a CNC router in musical instrument manufacturing is its ability to deliver high precision and consistency. CNC routers are programmed to follow exact design specifications, allowing for the precise cutting and shaping of instrument components. This ensures that every instrument produced maintains consistent dimensions and quality, which is beneficial for achieving optimal sound properties.
- Improved Efficiency and Speed: Traditional methods of instrument making are labor-intensive and time-consuming, especially when producing multiple units. CNC routers automate many of these processes, dramatically reducing production time while maintaining high quality. CNC routers can operate at high speeds and produce multiple identical parts in a fraction of the time compared to manual craftsmanship. With automated setups and auto tool changers, CNC routers allow continuous operation, minimizing downtime and improving throughput.
- Complex Designs and Customization: CNC routers can handle intricate and complex designs with ease. Instrument makers can create highly detailed and custom components, such as fretboards, necks, or inlays, using CAD software. This opens up new possibilities for creativity and customization that would be challenging to achieve with traditional methods. With CNC technology, manufacturers can produce unique, personalized instruments for clients or experiment with innovative designs that push the boundaries of instrument construction.
- Material Versatility: CNC routers can work with a wide range of materials, including wood, metal, plastics, and composites, which are often used in the manufacturing of musical instruments. This flexibility allows manufacturers to experiment with different materials for various parts of an instrument, offering more options in terms of design and functionality. Additionally, CNC routers can handle materials of varying hardness, making them suitable for both delicate and heavy-duty applications.
- Scalability: CNC routers enable manufacturers to scale their production without compromising quality. Whether producing a few custom instruments or mass-producing parts for large batches, CNC routers provide the flexibility to adjust production levels while maintaining consistent standards. This scalability is a significant advantage for instrument makers looking to grow their business and meet increasing demand.
- Reduced Human Error: Human error in traditional instrument-making can lead to imperfections that affect the instrument’ssound quality or structural integrity. CNC routers minimize this risk by following precise computer-generated instructions, ensuring that each part is produced to the exact specifications. This reduction in human error results in fewer defects, improved quality control, and less material waste.
CNC routers provide several advantages for musical instrument manufacturing, from enhancing precision and efficiency to enabling customization and reducing human error. These machines not only improve production speed and consistency but also allow manufacturers to explore innovative designs while maintaining high-quality standards. By integrating CNC routers, instrument makers can balance the demands of modern manufacturing with the artistic legacy of traditional craftsmanship.
Challenges of using CNC router for musical instrument manufacturing
While CNC routers offer significant benefits in musical instrument manufacturing, their adoption also presents certain challenges. These challenges can impact the precision, efficiency, and artistry traditionally associated with instrument making. Here are some of the key challenges faced when using CNC routers in musical instrument manufacturing:
- Initial Investment Costs: Setting up a CNC router for instrument manufacturing involves significant upfront investment. High-quality CNC machines can be expensive, as are the necessary software, tools, and materials needed for operation. Additionally, ongoing costs for maintenance, repairs, and software upgrades can add to the financial burden. For small-scale manufacturers or individual luthiers, this cost may be prohibitive compared to traditional handcrafting methods, which require fewer expensive tools.
- Learning Curve and Skill Requirements: While CNC routers offer many advantages, they also require specialized knowledge in programming and operation. Learning to operate a CNC router and mastering the associated software can be time-consuming. Instrument makers accustomed to manual methods may struggle with this transition, requiring extensive training or the hiring of skilled CNC operators. Without proper training, mistakes in programming or design setup can result in costly errors, such as material waste or flawed components.
- Limitations in Artistic Customization: While CNC routers offer high precision, they may not always capture the artistic flair and uniqueness that can be achieved through handcrafting. CNC routers are excellent at producing identical, high-precision parts, but this can lead to a level of standardization that limits creative flexibility. Custom details or non-standard shapes can be harder to achieve with a CNC router, and the personal and artistic expression of handcrafting an instrument can be lost.
- Material Constraints: Although CNC routers can work with a variety of materials, not all materials behave predictably when machined. For example, wood, a common material for musical instruments, can be inconsistent in its grain and density, which may lead to issues such as splintering, tearing, or uneven cuts. This makes it challenging to achieve the exact precision required for high-quality instruments. CNC router operators must carefully select materials and optimize settings to avoid damaging sensitive or inconsistent materials.
- Maintenance and Technical Downtime: CNC routers are complex machines that require regular maintenance to keep them operating smoothly. Technical issues, such as software glitches, hardware malfunctions, or tool wear, can lead to costly downtime, delaying production schedules. Additionally, maintenance and repairs often require professional expertise, further increasing costs. Instrument makers relying on CNC routers must be prepared for these potential interruptions and have contingency plans in place to ensure smooth operation.
- Balancing Automation and Craftsmanship: One of the key challenges in using a CNC router for musical instrument manufacturing is maintaining the delicate balance between automation and traditional craftsmanship. Handcrafted instruments often carry a unique character, texture, and individuality that many musicians value. CNC routers, by their nature, create uniform and repeatable results, which can diminish the sense of craftsmanship. Manufacturers must find ways to preserve the artistic elements of instrument making, blending technology with the human touch to meet customer expectations for both quality and aesthetic appeal.
- Limited Flexibility During Production: Once a CNC program is set, the machine follows the exact instructions given, leaving little room for adjustments during the manufacturing process. In traditional craftsmanship, instrument makers can adapt and modify their approach as they work, responding to the natural characteristics of the material or making creative changes in real-time. With CNC technology, such flexibility is limited. Any modifications require reprogramming the design, which can slow down production and increase costs.
While CNC routers offer numerous advantages in terms of precision, efficiency, and reproducibility, they also present challenges in musical instrument manufacturing. These include the potential loss of traditional craftsmanship, the high cost of investment, and the need for technical expertise. Balancing automation with the artistry and acoustic requirements of handcrafted instruments remains a delicate challenge for instrument makers seeking to integrate CNC technology into their processes.
Summarize
Building musical instruments with a CNC router offers a unique combination of precision, efficiency, and creative freedom. By integrating modern technology into the traditional craft of instrument making, manufacturers and artisans can produce high-quality instruments with consistent results. As technology continues to evolve, CNC routers will remain a crucial component in the future of instrument making, driving new possibilities for sound and design. With the right knowledge, programming skills, and a thoughtful approach to blending modern and traditional techniques, CNC routers can open new doors for innovation in musical instrument design and production.
AccTek CNC is a leading Chinese CNC router manufacturer, known for producing high-quality, reliable machines that are perfect for precision-driven tasks like musical instrument manufacturing. Our CNC routers offer exceptional accuracy, efficiency, and customization capabilities, making them an excellent choice for instrument makers looking to streamline production without sacrificing quality. With AccTek CNC’s cutting-edge technology, manufacturers can easily tackle the challenges of CNC routing while achieving consistent, professional results.