- 10-15 Min Read
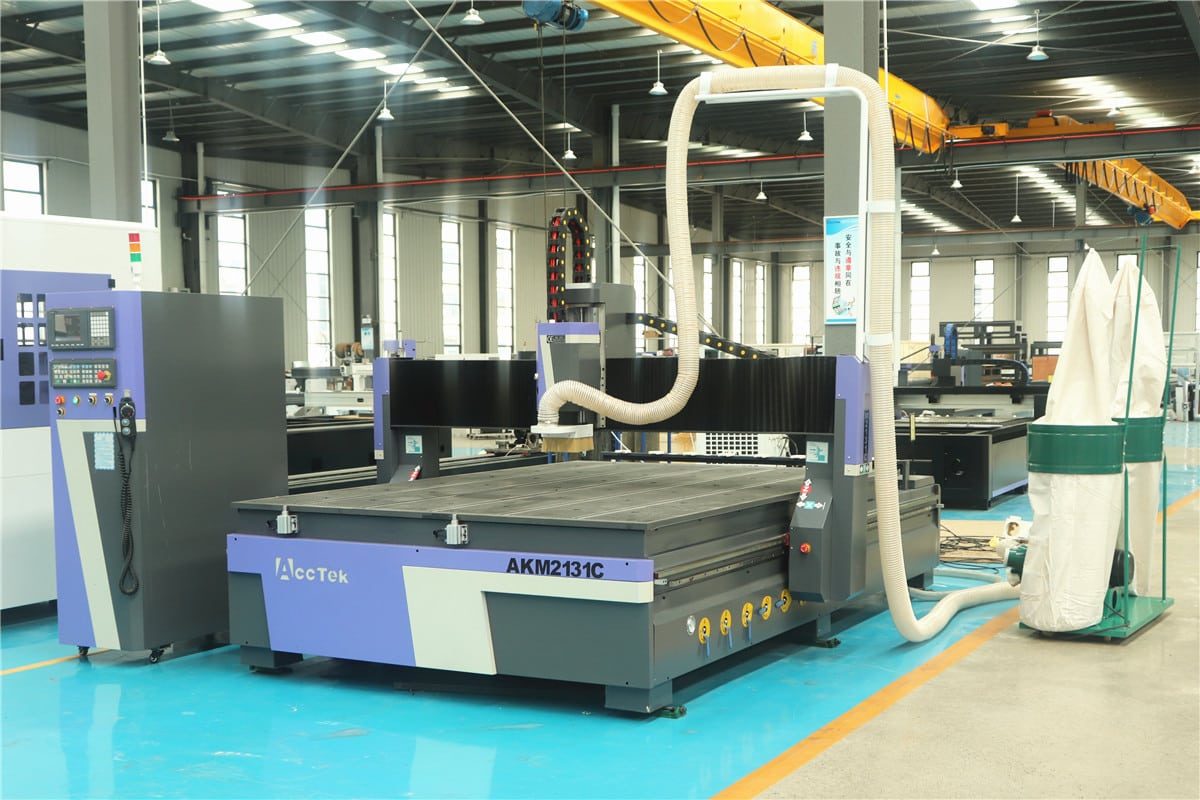
In today’s industrial landscape, the proliferation of Computer Numerical Control (CNC) routers has revolutionized manufacturing processes, offering precision and efficiency like never before. However, amidst the productivity gains lies a pressing concern: the responsible management of waste generated during CNC router operations. As industries increasingly embrace CNC technology, the disposal of waste materials demands meticulous attention. From wood shavings to metal filings, the byproducts of CNC machining can pose significant environmental challenges if not handled properly. Therefore, understanding the factors that influence waste disposal and implementing sustainable solutions is beneficial for mitigating environmental impact.
In this article, we delve into the multifaceted considerations essential for the correct disposal of waste materials from CNC router operations. We explore the environmental implications of improper waste management practices and provide actionable insights into responsibly addressing these challenges. From regulatory compliance to innovative recycling techniques, we examine the diverse strategies available to industries striving for environmental stewardship in the realm of CNC machining. Through informed actions and responsible management, we can tackle the environmental challenges posed by CNC waste, ensuring a balance between technological advancement and ecological preservation.
Understand the waste generated by CNC router operations
Like any industrial process, CNC routing generates various types of waste. Understanding the nature of these wastes is the first step toward developing effective disposal and recycling strategies. In this part, we conduct a specific analysis from the two aspects of waste types generated by CNC router operations and quantify waste generation. By understanding these, manufacturers can identify opportunities for waste reduction, recycling, and improved operational efficiency.
Types of Waste Generated by CNC Router Operations
- Material Offcuts and Scrap: CNC routers often produce large quantities of wood offcuts and sawdust. These byproducts can range from fine dust to larger wood chunks. Metal machining generates metal shavings, turnings, and scraps. These can include ferrous metals like steel and non-ferrous metals such as aluminum, brass, and copper. CNC machining of plastics and composite materials results in chips and dust. These materials can be more challenging to recycle due to their chemical compositions.
- Coolants and Lubricants: CNC operations often use coolants and lubricants to reduce heat and friction. These fluids can become contaminated with metal particles, oils, and other residues, making them hazardous if not disposed of properly.
- Dust and Particulate Matter: Fine dust generated during CNC routing can pose respiratory hazards and contribute to air pollution if not adequately controlled. This is particularly noticeable in woodworking and plastic machining.
- Used Tools and Components: Over time, CNC tools such as drill bits, end mills, and router bits wear out and need replacement. Disposing of these tools, often made of specialized metals, requires careful consideration.
Quantification of Waste Generation
- Material Type and Volume: Different materials (wood, metal, plastics) have varying densities and machining characteristics, leading to differences in waste generation. The volume and size of the workpieces being machined influence the amount of waste produced.
- Cutting Parameters: Factors such as cutting speed, feed rate, and tool selection affect material removal rates and, consequently, waste generation.
- Production Volume and Frequency: The scale and frequency of CNC machining operations directly impact the overall quantity of waste generated. High-volume production runs result in larger quantities of waste over time.
- Efficiency of Material Utilization: Optimization of cutting layouts and nesting strategies can minimize material waste by maximizing the use of raw materials.
- Tool Wear and Maintenance: The condition of cutting tools and machinery maintenance practices influence material waste through their impact on machining efficiency.
Impact of CNC router waste on the environment
The waste generated from CNC operations can have significant environmental impacts, particularly through harmful substances, energy consumption, and greenhouse gas emissions. This section explores these three critical aspects in detail, highlighting the need for responsible waste management and sustainable practices.
Harmful Substances
- Material Contaminants: CNC machining of metals produces shavings and scrap that can contain toxic elements such as lead, cadmium, and mercury. If not properly managed, these contaminants can leach into soil and water, posing risks to ecosystems and human health. Waste from plastics and composite materials can release harmful chemicals as they degrade. These substances can include volatile organic compounds (VOCs) and additives like phthalates and bisphenol A (BPA), which are known to be hazardous.
- Coolants and Lubricants: Used coolants and lubricants often contain heavy metals, oils, and other pollutants. Improper disposal can lead to contamination of water sources and soil, adversely affecting aquatic life and human populations reliant on these resources.
- Airborne Particulates: CNC operations generate fine dust and particulate matter, especially when machining wood and plastics. Inhalation of these particles can cause respiratory problems in workers and contribute to air pollution, impacting surrounding communities and natural habitats.
Energy Consumption
- Operational Energy Use: CNC routers require significant amounts of energy to operate. This includes powering the machinery, computer systems, and peripheral devices. High energy consumption not only leads to increased operational costs but also places a strain on energy resources, particularly if the energy is sourced from non-renewable sources.
- Waste Management Processes: Recycling and disposal processes for CNC waste also consume energy. Transporting waste materials to recycling facilities, processing them for reuse, and safely disposing of hazardous waste all require energy, further contributing to the environmental footprint of CNC operations.
- Resource Extraction: The production of raw materials used in CNC machining (e.g., metals, and plastics) involves energy-intensive extraction and processing methods. The more waste generated and discarded, the greater the demand for new raw materials, leading to increased energy consumption and environmental degradation from mining and extraction activities.
Greenhouse Gas Emissions
- Direct Emissions: The operation of CNC routers and associated machinery often relies on electricity generated from fossil fuels, which contributes to greenhouse gas emissions. This includes carbon dioxide (CO2) and methane (CH4), which are significant contributors to climate change.
- Indirect Emissions: The entire lifecycle of CNC materials, from extraction and production to disposal, generates greenhouse gas emissions. Manufacturing raw materials, transporting them to facilities, and processing waste all contribute to the carbon footprint of CNC operations.
- Waste Decomposition: Organic waste, such as wood shavings and sawdust, can decompose anaerobically in landfills, producing methane, a potent greenhouse gas. Proper management and recycling of such waste can mitigate these emissions, reducing the overall environmental impact.
Factors affecting correct disposal
Proper disposal of waste generated during CNC router operations is beneficial for minimizing environmental impact and ensuring regulatory compliance. Several critical factors influence the effectiveness of waste disposal, including material classification and segregation, regulatory compliance, disposal methods, and waste minimization technology. This article explores these four aspects in detail.
Material Classification and Segregation
- Accurate Identification: Classifying waste by material type is fundamental. CNC operations generate a variety of wastes, including wood, metal, plastic, and composite materials, each requiring specific handling and disposal methods. Distinguishing between hazardous and non-hazardous waste is crucial for compliance and environmental protection. For instance, used coolants and lubricants often contain hazardous substances that need special disposal.
- Effective Segregation: Use separate, clearly labeled containers for different types of waste to prevent cross-contamination. For example, separate bins for wood shavings, metal scraps, and plastic chips.
Regulatory Compliance
- Understanding and Adherence: Compliance with regulations at all levels is mandatory. These regulations define how different types of waste should be managed, transported, and disposed of. Following industry-specific standards and best practices helps ensure compliance and promotes sustainability.
- Documentation and Reporting: Maintain comprehensive records of waste types, quantities, and disposal methods. Submit necessary reports to regulatory bodies as required. This might include waste generation data, disposal practices, and proof of compliance with environmental regulations.
- Permits and Certifications: Acquire the necessary permits for waste disposal, particularly for hazardous materials. Partner with certified waste disposal services that comply with regulatory standards to handle and process waste correctly.
Disposal Methods
- Recycling and Reuse: Implement recycling programs tailored to different materials. For example, metal scraps can be sent to metal recycling facilities, while wood waste can be repurposed into particleboard or used as biomass fuel. Use filtration and purification systems to recycle coolants and lubricants, reducing the need for fresh supplies and minimizing hazardous waste.
- Safe Disposal of Hazardous Waste: Ensure hazardous waste, such as contaminated coolants and lubricants, is handled by specialized facilities that can treat and dispose of them safely. Use appropriate containment measures to prevent leaks and spills during the storage and transportation of hazardous materials.
- Landfill and Incineration: For waste that cannot be recycled or reused, ensure it is disposed of in an environmentally responsible manner. Use sanitary landfills designed to minimize environmental impact or incineration facilities that meet emission standards.
Waste Minimization Technology
- Advanced Technologies: Employ precision machining techniques to reduce material waste during CNC operations. Advanced CNC software can optimize cutting paths and material usage.
- Process Improvements: Implement lean manufacturing principles to streamline operations, reduce waste, and improve efficiency. This includes optimizing workflows and reducing unnecessary material use.
- Regular Maintenance: Maintain CNC equipment to ensure it operates at peak efficiency, minimizing the likelihood of generating excess waste due to machine errors or inefficiencies.
- Employee Training and Awareness: Train employees on the latest waste reduction techniques and the importance of sustainability. Encourage practices that minimize waste generation at every stage of the production process.
Disposal practices for different waste types
Effective disposal practices help manage the diverse waste streams generated by CNC router operations. Each type of waste requires specific handling and disposal methods to minimize environmental impact and promote sustainability. This article explores the recommended disposal practices for these key waste types.
Metal Scrap
- Collection and Segregation: Collect and segregate metal scraps by type (e.g., ferrous metals like steel and non-ferrous metals like aluminum, brass, and copper) to facilitate recycling.
- Recycling Facilities: Send segregated metal scraps to specialized metal recycling facilities where they are melted down and repurposed for new products. This reduces the need for virgin metal extraction and conserves natural resources.
- Proper Storage: Store metal scrap in designated containers to prevent contamination and facilitate easy transport to recycling centers.
- Safe Handling: Ensure proper handling to avoid injuries and environmental contamination.
Plastic Waste
- Identification and Segregation: Identify and segregate plastic waste by type (e.g., polyethylene, polypropylene, PVC) to streamline the recycling process.
- Recycling Methods: Use mechanical recycling (shredding, melting, and re-extruding plastics) or chemical recycling (breaking down plastics into their monomers for reuse) depending on the type of plastic.
- Specialized Programs: Participate in programs that focus on recycling specific types of plastics, such as industrial plastics recycling initiatives.
- Repurposing: Explore opportunities to repurpose plastic waste within the facility or for other industrial applications, reducing the need for new materials.
- Energy Recovery: For plastics that cannot be recycled, consider waste-to-energy options where plastic waste is incinerated to generate energy, thereby reducing landfill use.
Composite Waste
- Material Recovery: Some composite materials can be processed to recover valuable components, such as fibers and resins, for reuse in manufacturing new composite products.
- Mechanical Recycling: Shred composite waste to produce materials that can be used in lower-grade applications, such as construction materials or filler for other products.
- Disposal Challenges: Due to the heterogeneous nature of composites, recycling can be challenging. Specialized recycling technologies may be required to handle different composites effectively.
- Innovative Solutions: Invest in R&D to develop new recycling technologies and methods that can handle composite waste more efficiently. Collaborate with specialized recycling firms that can process composite materials.
Wood Waste
- Chipping and Mulching: Convert wood waste into chips or mulch, which can be used for landscaping, gardening, and biomass fuel.
- Particleboard Production: Use wood waste as raw material for manufacturing particleboard and other engineered wood products.
- Composting: Compost wood shavings and sawdust to produce nutrient-rich compost for agricultural use.
- Biomass Fuel: Utilize wood waste as biomass fuel for energy generation, which can be a sustainable alternative to fossil fuels.
- Proper Storage and Handling: Store wood waste in dry conditions to prevent mold growth and deterioration, making it easier to recycle or reuse.
- Dust Control: Implement dust control measures to minimize airborne particles that can pose health risks and environmental pollution.
Waste Management Technology and Innovation
Advancements in technology and innovative practices are transforming waste management in CNC router operations. These advancements drive efficiency, sustainability, and cost-effectiveness in waste handling and disposal. Here are some key technologies and innovations shaping waste management in CNC machining:
Advanced Recycling Systems
- Automated Sorting Technologies: High-tech sorting systems equipped with sensors and artificial intelligence can accurately segregate different types of waste materials, such as metals, plastics, and composites, for efficient recycling.
- Chemical Recycling: Innovative chemical processes break down complex waste materials into their constituent components, allowing for the recovery of valuable resources that would otherwise be difficult to recycle.
- Material Recovery Facilities (MRFs): State-of-the-art MRFs employ advanced equipment and robotics to sort, clean, and process recyclable materials, maximizing recovery rates and minimizing contamination.
Waste-to-Energy Technologies
- Anaerobic Digestion: Organic waste, such as wood shavings and food scraps, can be converted into biogas through anaerobic digestion, providing renewable energy and reducing greenhouse gas emissions.
- Incineration with Energy Recovery: Advanced incineration technologies not only dispose of waste but also generate heat or electricity through energy recovery systems, contributing to sustainable energy production.
Innovative Recycling Processes
- Closed-Loop Recycling: Closed-loop systems promote circular economy principles by recycling materials back into the same production process, reducing the need for virgin resources and minimizing waste generation.
- Upcycling and Repurposing: Innovative upcycling techniques transform waste materials into higher-value products, extending their lifecycle and reducing environmental impact.
Smart Waste Management Solutions
- IoT-enabled Waste Monitoring: Internet of Things (IoT) devices equipped with sensors monitor waste bins in real-time, optimizing collection routes, reducing overflow incidents, and minimizing resource wastage.
- Data Analytics and Predictive Modeling: Advanced data analytics and predictive modeling tools analyze historical waste data to forecast future waste generation trends, enabling proactive waste management strategies and resource allocation.
Sustainable Materials and Design
- Biodegradable and Renewable Materials: The development of biodegradable and renewable materials reduces the environmental impact of CNC waste, offering sustainable alternatives to traditional materials.
- Design for Disassembly: Incorporating design principles that facilitate easy disassembly and recycling of products promotes a circular economy approach, where materials are reused or recycled at the end of their lifecycle.
Collaborative Partnerships and Initiatives
- Industry Collaboration: Collaborative efforts between manufacturers, waste management companies, research institutions, and government agencies drive innovation and knowledge-sharing in waste management practices.
- Public-Private Partnerships: Public-private partnerships foster cooperation between government entities and private organizations to invest in and implement sustainable waste management solutions at a larger scale.
Future trends and challenges
As industries continue to evolve and prioritize sustainability, the management of CNC router waste will face both promising advancements and significant challenges. By staying informed of these trends and proactively addressing the associated challenges, industries can foster more sustainable practices and contribute to a healthier environment.
Sustainability and Circular Economy
- Trend: Increasing emphasis on sustainability and circular economy principles, driving the adoption of waste reduction, recycling, and reuse practices to minimize environmental impact and resource consumption.
- Challenge: Balancing sustainability goals with operational efficiency and economic viability, as implementing advanced recycling and circular economy initiatives may require significant investment and operational changes.
Technological Advancements
- Trend: Continued development of innovative technologies, such as AI-powered waste sorting systems, advanced recycling processes, and smart waste management solutions, to enhance efficiency, accuracy, and sustainability in waste management practices.
- Challenge: Overcoming barriers to technology adoption, including high initial costs, compatibility with existing infrastructure, and the need for specialized expertise for implementation and maintenance.
Regulatory Compliance
- Trend: Increasingly stringent waste management regulations and environmental standards, require industries to comply with waste disposal guidelines, report waste generation data, and implement sustainable waste management practices.
- Challenge: Navigating complex and evolving regulatory landscapes, ensuring compliance across multiple jurisdictions, and managing the administrative burden associated with regulatory reporting and documentation.
Waste Minimization and Optimization
- Trend: Growing focus on waste minimization and process optimization through lean manufacturing principles, advanced machining techniques, and material efficiency strategies to reduce waste generation and improve resource utilization.
- Challenge: Overcoming technical and logistical barriers to waste minimization, such as optimizing cutting layouts, minimizing tool wear, and optimizing coolant usage, while maintaining productivity and product quality.
Circular Supply Chains
- Trend: Emergence of circular supply chain models, where materials and components are sourced, produced, used, and recycled in closed-loop systems, promoting resource efficiency, waste reduction, and sustainable production practices.
- Challenge: Establishing collaborative partnerships across supply chains, overcoming logistical challenges related to material recovery and reverse logistics, and ensuring transparency and traceability throughout the recycling process.
Education and Awareness
- Trend: Increasing awareness and education initiatives to promote sustainable waste management practices among industry stakeholders, employees, consumers, and the broader community, fostering a culture of environmental responsibility and stewardship.
- Challenge: Overcoming resistance to change and cultural barriers to adopting sustainable practices, providing training and resources to equip stakeholders with the knowledge and skills needed to implement effective waste management strategies.
Summarize
Addressing environmental concerns in CNC router waste disposal is not just a necessity but a responsibility for individuals and industries alike. Navigating the complex landscape of waste disposal in CNC router operations requires a multifaceted approach that prioritizes environmental sustainability without compromising efficiency. By implementing the strategies outlined in this comprehensive guide, we can minimize the negative impact of CNC router waste on our environment and work towards a more sustainable future.
AccTek CNC, a well-known CNC router manufacturer in China, demonstrates a strong commitment to sustainability by focusing on improving the cutting accuracy of their machines to reduce material waste. We offer a versatile range of CNC routers to meet diverse cutting needs, including 3-axis, 4-axis, 5-axis, and rotary axis CNC routers. This variety allows customers to select the ideal machine for their specific projects, enhancing production efficiency and precision. We look forward to partnering with you on your journey to success and innovation in CNC machining.